The Automotive Die-Stamping Equipment Market size was estimated at USD 1.31 billion in 2024 and expected to reach USD 1.40 billion in 2025, at a CAGR 7.00% to reach USD 1.97 billion by 2030.

Pioneering the Next Era of Automotive Die-Stamping Equipment by Embracing Agility, Precision Manufacturing, and the Imperative of Sustainable Innovation
The automotive die-stamping equipment sector stands at a pivotal intersection of precision engineering and transformative demand created by evolving vehicle architectures. As manufacturers strive for tighter tolerances, enhanced part consistency, and accelerated production cycles, die-stamping machinery has emerged as a critical enabler of competitive differentiation. Advanced press systems now confront the dual challenge of meeting stringent quality requirements while accommodating the shift toward lighter, multi-material constructions in both electrified and traditional powertrains.
Against this backdrop, the introduction of digital capabilities-including real-time monitoring, predictive maintenance, and closed-loop process control-has accelerated the modernization of stamping operations. The convergence of mechanical robustness and software intelligence is rewriting the rules for uptime, throughput, and operational efficiency. Moreover, tighter sustainability mandates are prompting equipment suppliers to innovate around energy consumption and waste reduction, further redefining the value proposition of next-generation stamping platforms.
In this executive summary, readers will discover how these dynamics are converging to shape strategic priorities for equipment manufacturers, stamping shops, and OEMs. By examining the catalysts of change and the responses across the value chain, this analysis lays the foundation for an actionable market perspective that guides decision-makers through a rapidly evolving industrial landscape.
Transformational Forces Reshaping the Automotive Die-Stamping Equipment Landscape through Electrification Digitalization Lightweighting and Agile Manufacturing
Across the die-stamping equipment landscape, several transformative forces are converging to redefine how parts are produced and how suppliers position themselves. Rapid electrification has intensified the need for robust lightweighting solutions, propelling a shift toward high-strength aluminum alloys that demand presses capable of higher tonnage and precise force control. At the same time, the drive for higher production flexibility has led to the integration of servo-electric press technology, which delivers faster response times, optimized energy utilization, and programmability that traditional hydraulic systems struggle to match.
Concurrently, Industry 4.0 principles have gained traction as manufacturers deploy smart sensors, edge analytics, and cloud-based frameworks to achieve end-to-end visibility. These digital threads not only enhance predictive maintenance capabilities but also unlock the potential for process simulation and digital twins that accelerate die development cycles. As a result, time-to-market is compressed while the cost of scrap and rework declines, enabling a leaner production footprint.
Moreover, global supply chain fragility has underscored the importance of regional diversification and collaborative ecosystems. Partnerships between press OEMs, tooling specialists, and material suppliers are forming consortia that co-innovate around specialized die-set design, modular automation, and lifecycle services. Ultimately, these transformative shifts are forging a new competitive paradigm, one in which agility, connectivity, and sustainability are the hallmarks of industry leadership.
Assessing the Cumulative Impact of 2025 United States Tariff Measures on Cost Structures and Competitive Dynamics in Automotive Die-Stamping
In 2025, the implementation of enhanced United States tariff measures aimed at imported steel inputs and finished stamping presses has significantly altered cost structures and supply chain dynamics. The imposition of duties under Section 232 and subsequent trade policy adjustments have prompted equipment manufacturers to reevaluate sourcing strategies. Imported press systems now carry elevated landed costs, leading many end users to consider localized partnerships and domestic assembly solutions to mitigate the financial impact.
These tariffs have also accelerated the expansion of regional manufacturing hubs within North America. Suppliers that previously concentrated production in lower-cost jurisdictions have started to establish assembly lines closer to key automotive OEM clusters, thereby reducing cross-border friction. This realignment supports greater production agility, enabling faster lead times and more responsive maintenance services for stamping operations.
At the same time, domestic steel producers have responded with capacity investments to meet rising demand for high-quality rolled steel and aluminum alloys, ensuring that automotive press builders have a stable local supply. While duty-induced cost pressures have been an initial challenge, they have also catalyzed a more resilient and transparent supply chain that reinforces long-term competitiveness. Consequently, tariff measures have yielded a net positive effect on the value proposition of domestically supported die-stamping equipment.
Unveiling Strategic Insights into Equipment Types Stamping Processes Material Choices Vehicle Classes Application Areas and End-User Industry Dynamics
Segmentation analysis reveals that servo presses are gaining prominence as the preferred choice for high-precision applications, driven by their energy efficiency and programmability compared to hydraulic, mechanical, and pneumatic counterparts. Within stamping methodologies, cold stamping continues to dominate routine sheet metal forming, while hot stamping is carving out a niche for advanced high-strength steels used in structural safety components. Die-stamping processes have also evolved: progressive die stamping offers rapid cycle times for high-volume runs, tandem die stamping aligns sequential operations in a single line for optimized material flow, and transfer die stamping supports complex multi-station forming for large panels.
Material selection plays a vital role as well, with steel remaining the foundational substrate for most structural parts even as aluminum alloys secure growth in lightweight body panels. The bifurcation of vehicle markets into commercial and passenger segments further informs equipment deployment, since commercial vehicles demand heavy-duty presses for chassis elements whereas passenger cars emphasize throughput and dielife for body in white manufacturing. Core applications, including body panels, chassis components, engine parts, and transmission modules, each impose distinct force, stroke, and automation requirements. Finally, the end-user landscape is characterized by a mix of large automotive OEMs that integrate stamping operations in-house and independent stamping presses that offer specialized contract manufacturing services across multiple customer tiers.
This comprehensive research report categorizes the Automotive Die-Stamping Equipment market into clearly defined segments, providing a detailed analysis of emerging trends and precise revenue forecasts to support strategic decision-making.
- Equipment Type
- Stamping
- Process Type
- Material Type
- Vehicle Type
- Application
- End-User Industry
Mapping Regional Dynamics and Growth Drivers across the Americas Europe Middle East and Africa and Asia-Pacific for Automotive Die-Stamping Equipment
Regional market dynamics are distinctly shaped by local automotive production trends and policy environments. In the Americas, nearshoring initiatives and free trade agreements underpin growth in die-stamping capacity, with North American OEMs prioritizing domestic supply chains to reduce logistical complexity. As sustainability targets tighten, stamping facilities in the region are upgrading to servo-electric presses and adopting carbon reduction measures to align with corporate environmental commitments.
Within Europe, the Middle East, and Africa, stringent emissions regulations and lightweighting mandates have prompted OEMs and tier suppliers to invest heavily in hot stamping lines that can form ultra-high-strength steels. The European Union’s emphasis on circular economy principles is also leading to the retrofitting of older mechanical presses with digital sensor packages and energy recovery systems, extending asset lifecycles while improving resource efficiency.
Meanwhile, the Asia-Pacific region remains a powerhouse for both equipment production and consumption. Japan and South Korea maintain leadership in press design innovation, whereas China has rapidly scaled manufacturing capacity to serve a growing domestic automotive market and export demand. Emerging economies across Southeast Asia are investing in foundational stamping infrastructures, often through joint ventures that transfer advanced press technologies from global OEMs to local toolrooms.
This comprehensive research report examines key regions that drive the evolution of the Automotive Die-Stamping Equipment market, offering deep insights into regional trends, growth factors, and industry developments that are influencing market performance.
- Americas
- Europe, Middle East & Africa
- Asia-Pacific
Highlighting Competitive Leadership and Collaborative Innovations among Key Manufacturers Shaping the Future of Automotive Die-Stamping Solutions
Key equipment manufacturers are intensifying their focus on collaborative innovation, forging partnerships with software providers and material specialists to deliver turnkey stamping solutions. Leading press builders differentiate themselves through modular automation packages that integrate robotics, die handling systems, and in-line quality inspection, positioning them as strategic partners rather than mere machine vendors. Several prominent players have expanded their aftermarket services, offering predictive maintenance subscriptions that harness real-time data streams to minimize unplanned downtime and extend die life.
Strategic acquisitions have further consolidated capability portfolios, enabling some companies to provide end-to-end offerings that span press manufacturing, tool design, and on-site engineering support. Others compete on technological leadership, unveiling next-generation servo-electrical presses and adaptive force control systems that cater to the rising complexity of lightweight multi-material assemblies. This competitive landscape underscores the importance of customer-centric innovation, as equipment suppliers align with OEMs and tier-one manufacturers to co-develop specialized forming processes that satisfy unique production requirements.
This comprehensive research report delivers an in-depth overview of the principal market players in the Automotive Die-Stamping Equipment market, evaluating their market share, strategic initiatives, and competitive positioning to illuminate the factors shaping the competitive landscape.
- AIDA Engineering Ltd.
- AMADA CO., LTD.
- American Industrial Company
- Andritz AG
- Bliss-Bret
- BRUDERER AG
- Clow Stamping Company
- D&H Industries, Inc.
- Dai-ichi Kiden Co.,Ltd.
- Eaton Corporation plc
- Emerson Electric Co.
- G&M Mfg. Corp.
- Galdabini SPA
- JR Automation by Jitachi Ltd
- Komatsu Ltd.
- Macrodyne Technologies Inc.
- Manor Tool & Manufacturing Company
- Manroland Sheetfed GmbH
- Mitsubishi Heavy Industries, Ltd.
- Pridgeon & Clay
- Schuler Group GmbH
- SHIEH YIH MACHINERY INDUSTRY CO., LTD.
- SIMPAC America Co. Ltd.
- Stamtec Inc by Chin Fong Machine Industrial Co., Ltd.
- Sumitomo (SHI) Demag Plastics Machinery GmbH
- Yangli Group
Formulating Actionable Strategies to Capitalize on Emerging Technologies and Operational Excellence in Die-Stamping for Automotive Leadership
Leaders in stamping equipment should prioritize investments in servo-electric press technology to achieve precise force modulation and substantial energy savings over hydraulic alternatives. At the same time, establishing local assembly or partnership agreements near major OEM facilities can insulate operations from cross-border tariff volatility and supply chain disruptions. To remain at the forefront of digital transformation, industry stakeholders must integrate advanced analytics platforms and real-time monitoring capabilities to shift maintenance strategies from reactive to predictive.
Additionally, cultivating closer collaboration with material suppliers will enable die-press OEMs to co-engineer forming processes for next-generation aluminum and high-strength steel grades. Workforce development is another critical lever, with training programs designed to upskill operators in areas such as automation control, data interpretation, and die-set optimization. By combining these strategic moves with lifecycle service offerings and flexible financing models, stamping equipment leaders can strengthen customer relationships, differentiate their value proposition, and secure long-term revenue streams.
Detailing Research Methodology Integrating Primary Interviews Secondary Data Analysis and Expert Validation Illuminating Automotive Die-Stamping Trends
This research is grounded in a comprehensive methodology that blends primary and secondary data to ensure depth and accuracy. The primary research phase included structured interviews and workshops with C-level executives, plant managers, and process engineers at leading automotive OEMs and tier-one suppliers. These engagements provided insights into strategic priorities, technology adoption roadmaps, and emerging pain points across global stamping operations.
Secondary research encompassed the review of industry publications, trade association reports, technical whitepapers, and regulatory filings. Data from equipment registries and production databases was triangulated with company disclosures and press announcements to track press deployments, capacity expansions, and service innovations. Expert validation sessions were conducted to refine assumptions, challenge preliminary findings, and confirm market trends prior to publication.
Explore AI-driven insights for the Automotive Die-Stamping Equipment market with ResearchAI on our online platform, providing deeper, data-backed market analysis.
Ask ResearchAI anything
World's First Innovative Al for Market Research
Concluding Reflections on How Innovation Policy Shifts and Strategic Adaptation Are Defining the Future Trajectory of Automotive Die-Stamping Operations
The convergence of advanced materials, digitalization, and shifting trade policies is redefining the competitive landscape for automotive die-stamping equipment. As manufacturers navigate cost pressures and sustainability targets, the emphasis on energy-efficient, programmable press platforms has never been higher. Regional tariff measures have catalyzed a realignment of supply chains, spurring local assembly initiatives and reinforcing North American manufacturing resilience.
Segmentation insights demonstrate that strategic differentiation is increasingly achieved through tailored solutions-whether it be high-precision servo presses for complex body structures or specialized hot stamping lines for UHSS safety components. Regional variances underscore the importance of a nuanced market approach, as each geography balances regulatory imperatives, production volumes, and localization strategies differently.
In summary, stakeholders that embrace these transformative shifts, align with key material and digital ecosystem partners, and adopt flexible service models will be best positioned to capture emerging opportunities. This research equips decision-makers with a detailed understanding of the forces at play and actionable recommendations to capitalise on evolving market dynamics.
This section provides a structured overview of the report, outlining key chapters and topics covered for easy reference in our Automotive Die-Stamping Equipment market comprehensive research report.
- Preface
- Research Methodology
- Executive Summary
- Market Overview
- Market Dynamics
- Market Insights
- Cumulative Impact of United States Tariffs 2025
- Automotive Die-Stamping Equipment Market, by Equipment Type
- Automotive Die-Stamping Equipment Market, by Stamping
- Automotive Die-Stamping Equipment Market, by Process Type
- Automotive Die-Stamping Equipment Market, by Material Type
- Automotive Die-Stamping Equipment Market, by Vehicle Type
- Automotive Die-Stamping Equipment Market, by Application
- Automotive Die-Stamping Equipment Market, by End-User Industry
- Americas Automotive Die-Stamping Equipment Market
- Europe, Middle East & Africa Automotive Die-Stamping Equipment Market
- Asia-Pacific Automotive Die-Stamping Equipment Market
- Competitive Landscape
- ResearchAI
- ResearchStatistics
- ResearchContacts
- ResearchArticles
- Appendix
- List of Figures [Total: 32]
- List of Tables [Total: 644 ]
Connect with Associate Director Sales and Marketing to Unlock Exclusive Insights and Gain Competitive Advantage with Die-Stamping Equipment Market Insights
To gain immediate access to granular data, comprehensive strategic analysis, and proprietary insights on the automotive die-stamping equipment market, reach out directly to Ketan Rohom, Associate Director, Sales and Marketing at 360iResearch. His deep understanding of client requirements and the current market pulse ensures you secure the exact intelligence needed to outpace competitors and make informed investment decisions. Engage now to receive a tailored briefing, accelerate your strategic planning, and capitalize on emerging opportunities in die-stamping technology by obtaining the full market research report today
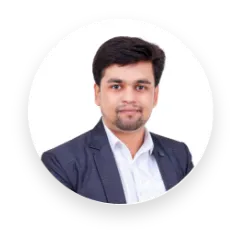
- How big is the Automotive Die-Stamping Equipment Market?
- What is the Automotive Die-Stamping Equipment Market growth?
- When do I get the report?
- In what format does this report get delivered to me?
- How long has 360iResearch been around?
- What if I have a question about your reports?
- Can I share this report with my team?
- Can I use your research in my presentation?