Introduction to the Drive Motor Core Landscape
In an era defined by rapid electrification and heightened efficiency standards, drive motor cores have become foundational elements across automotive, industrial and aerospace platforms. The core architecture, material selection and manufacturing precision of these components directly influence key performance indicators such as torque density, thermal stability and energy efficiency. Advances in electrical steel metallurgy, precision lamination stamping and hybrid core composites have accelerated the development of lighter, more compact motors capable of meeting stringent regulatory targets for emissions and operational reliability. Concurrently, end-user industries-including heavy commercial vehicles, high-performance electric mobility solutions and critical industrial applications-are demanding tailored core designs that balance cost pressures with long-term durability. This executive summary distills the essential trends, regulatory impacts and strategic segmentation insights that industry leaders must navigate. By examining the cumulative effect of forthcoming U.S. tariffs, profiling regional dynamics and leading competitors, and offering actionable recommendations, this analysis equips decision-makers with a clear framework to unlock growth opportunities and safeguard competitive advantage within the evolving drive motor core landscape.
Transformative Shifts Reshaping the Drive Motor Core Industry
The drive motor core industry is undergoing transformative shifts driven by several converging forces. Accelerated adoption of electric vehicles (EVs) is fueling demand for cores optimized for high voltage operation, while advanced manufacturing techniques such as additive layering and laser welding are enabling unprecedented precision. At the same time, digital twin technologies and AI-enhanced design tools are reducing development cycles and improving material utilization. Sustainability imperatives are promoting the use of low-loss electrical steels and recyclable composites, setting new benchmarks for core lifecycle impact. Additionally, the convergence of drive electronics and mechanical systems has given rise to integrated stator assemblies that streamline supply chains and enhance thermal management. These rapid changes require manufacturers to embrace agile process reconfiguration, invest in next-generation materials research, and forge strategic partnerships across the value chain. As the landscape evolves, the winners will be those organizations that can seamlessly integrate emerging technologies with robust core architectures to deliver both performance and cost-effectiveness.
Cumulative Impact of U.S. Tariffs Effective in 2025
With the implementation of U.S. tariffs on selected automotive and electrical steel imports scheduled for early 2025, manufacturers must anticipate a cumulative impact on raw material costs and global supply chains. The levies impose higher entry costs for alloy and electrical steel cores sourced from regions subject to trade restrictions, prompting OEMs and suppliers to evaluate near-shoring and regional sourcing strategies. As a direct consequence, production footprints are likely to shift toward free-trade partners and domestic steel mills, potentially accelerating joint ventures and capacity expansions within North America. Furthermore, the cost pressures created by tariff escalations could be passed through to electric vehicle manufacturers, influencing pricing strategies and margin structures. Mitigation approaches such as dual-sourcing agreements, longer-term supply contracts and investments in alternative core alloys will be critical. Navigating this tariff landscape demands proactive scenario planning and sustained engagement with policy stakeholders to minimize disruption and preserve competitiveness.
Key Segmentation Insights for the Drive Motor Core Market
Insight into market segmentation illuminates the nuanced demands that drive motor cores must satisfy. Based on motor type, asynchronous configurations-comprising both single- and three-phase designs-continue to lead due to their robustness and cost efficiency, while synchronous machines are gaining traction where precise speed regulation and peak efficiency are paramount. Material choices span from copper cores prized for conductivity to steel cores, differentiated into carbon and high-permeability electrical steel, with alloy cores emerging where weight savings justify higher costs. Manufacturing processes such as die casting, lamination stamping and pressing each offer unique trade-offs between volume throughput and dimensional accuracy. Application segments reflect the evolution of transport platforms: heavy and light commercial vehicles, alongside the rapid expansion of battery, hybrid and plug-in hybrid electric vehicles, and traditional passenger cars including hatchbacks, sedans and SUVs. End-user industries range from aerospace, with its rigorous certification requirements, to marine and industrial sectors that prioritize endurance in harsh environments. Power output bands-from sub-one kilowatt units to systems exceeding 100 kilowatts-drive modular design approaches. Drive type selection between all-wheel, front-wheel and rear-wheel configurations influences mechanical integration. Cooling methods span air-cooled systems to liquid solutions, subdivided into oil- and water-based circuits. Voltage range requirements-low, medium and high-shape insulation and winding strategies. Installation modalities vary between integral and stand-alone setups, while drive systems leverage belt, direct or gear transmissions. Finally, motor size classification into large, medium and small categories captures the end-use scale and mounting constraints that guide product development.
This comprehensive research report categorizes the Automotive Drive Motor Core market into clearly defined segments, providing a detailed analysis of emerging trends and precise revenue forecasts to support strategic decision-making.
- Motor Type
- Material Type
- Manufacturing Process
- Application
- End-User Industry
- Power Output
- Drive Type
- Cooling Method
- Voltage Range
- Installation Type
- Drive System
- Motor Size
Regional Dynamics Influencing the Drive Motor Core Market
Regional dynamics play a pivotal role in shaping competitiveness and supply resilience. In the Americas, robust incentives for electrification and a trend toward on-shoring have spurred investments in domestic core production facilities, especially for high-strength electrical steels. Meanwhile, regulatory alignment across U.S., Canadian and Mexican markets fosters integrated supply networks in North America. Europe, the Middle East and Africa exhibit a dual focus on stringent efficiency regulations and strategic raw material sourcing. Major steel producers in the EMEA region are collaborating with motor manufacturers to co-develop specialty electrical steels, and free trade arrangements within the EU facilitate seamless cross-border logistics. In the Asia-Pacific, high-volume manufacturing centers in China, Japan and South Korea maintain leadership through economies of scale and deep expertise in rare earth magnet integration. Governments across the region continue to incentivize EV adoption, driving localized demand for high-voltage cores and advanced cooling solutions. Together, these regional ecosystems define strategic corridors for capital allocation and partnership formation.
This comprehensive research report examines key regions that drive the evolution of the Automotive Drive Motor Core market, offering deep insights into regional trends, growth factors, and industry developments that are influencing market performance.
- Americas
- Asia-Pacific
- Europe, Middle East & Africa
Competitive Landscape and Leading Industry Players
The competitive landscape is characterized by a blend of traditional component specialists and vertically integrated conglomerates. Aisin Corporation leverages automotive heritage to optimize core-to-axle integration, while BorgWarner Inc. focuses on high-efficiency synchronous machines and power electronics synergy. Continental AG and Denso Corporation pursue collaborative R&D for next-gen materials and manufacturing automation. GKN Automotive Limited and Hitachi Astemo Ltd. differentiate themselves through modular core platforms targeted at commercial and industrial segments. Meanwhile, Johnson Electric Holdings Limited and MABUCHI MOTOR CO., LTD. excel in high-speed, small-frame cores for precision applications. Magna International Inc. and Mitsubishi Electric Corporation extend their portfolios into integrated e-drive systems, blending motor cores with inverters and control units. Nidec Corporation and Robert Bosch GmbH continue to scale global production capacities with investments in electrical steel partnerships. Siemens AG and Valeo SA are notable for cross-industry collaborations that marry core expertise with digital services. Tesla Inc. and ZF Friedrichshafen AG push the envelope in performance-oriented core designs, often leveraging in-house material science capabilities to enhance power density and thermal management.
This comprehensive research report delivers an in-depth overview of the principal market players in the Automotive Drive Motor Core market, evaluating their market share, strategic initiatives, and competitive positioning to illuminate the factors shaping the competitive landscape.
- Aisin Corporation
- BorgWarner Inc.
- Continental AG
- Denso Corporation
- GKN Automotive Limited
- Hitachi Astemo Ltd.
- Johnson Electric Holdings Limited
- MABUCHI MOTOR CO., LTD.
- Magna International Inc.
- Mitsubishi Electric Corporation
- Nidec Corporation
- Robert Bosch GmbH
- Siemens AG
- Tesla Inc.
- Valeo SA
- ZF Friedrichshafen AG
Actionable Recommendations for Industry Leaders
Industry leaders should adopt a multifaceted strategy to stay ahead. First, prioritizing investment in advanced electrical steels and low-loss core alloys will deliver measurable efficiency gains and sustainability benefits. Second, diversifying the supplier base through strategic alliances with regional steel mills and non-traditional material providers can mitigate tariff risks and raw material volatility. Third, integrating AI-driven design optimization and digital twin simulations will accelerate time-to-market and reduce scrap rates. Fourth, expanding localized manufacturing footprints in key regions will enhance responsiveness to OEM requirements and reduce logistical complexity. Fifth, deepening collaboration with vehicle and equipment manufacturers to co-develop application-specific core geometries will strengthen value propositions. Sixth, adopting modular core production platforms that accommodate variable power outputs, drive types and cooling methods will improve scalability. Lastly, embedding environmental, social and governance (ESG) criteria into core design and process workflows will become a differentiator as end users increasingly demand traceable, low-carbon solutions.
Explore AI-driven insights for the Automotive Drive Motor Core market with ResearchAI on our online platform, providing deeper, data-backed market analysis.
Ask ResearchAI anything
World's First Innovative Al for Market Research
Conclusion: Positioning for Success in the Drive Motor Core Market
The drive motor core sector stands at the intersection of electrification, material innovation and global trade realignment. Organizations that successfully navigate the shifting tariff environment, harness cutting-edge manufacturing technologies and align product portfolios with emerging vehicle architectures will secure competitive advantage. By leveraging detailed segmentation and regional insights, companies can pinpoint high-value opportunities and allocate resources effectively. Collaboration across the value chain-from steel suppliers to OEM integrators-remains essential to accelerate innovation cycles and optimize total cost of ownership. Ultimately, a balanced approach that marries strategic foresight with operational agility will define market leaders and shape the next generation of drive motor core solutions.
This section provides a structured overview of the report, outlining key chapters and topics covered for easy reference in our Automotive Drive Motor Core market comprehensive research report.
- Preface
- Research Methodology
- Executive Summary
- Market Overview
- Market Dynamics
- Market Insights
- Cumulative Impact of United States Tariffs 2025
- Automotive Drive Motor Core Market, by Motor Type
- Automotive Drive Motor Core Market, by Material Type
- Automotive Drive Motor Core Market, by Manufacturing Process
- Automotive Drive Motor Core Market, by Application
- Automotive Drive Motor Core Market, by End-User Industry
- Automotive Drive Motor Core Market, by Power Output
- Automotive Drive Motor Core Market, by Drive Type
- Automotive Drive Motor Core Market, by Cooling Method
- Automotive Drive Motor Core Market, by Voltage Range
- Automotive Drive Motor Core Market, by Installation Type
- Automotive Drive Motor Core Market, by Drive System
- Automotive Drive Motor Core Market, by Motor Size
- Americas Automotive Drive Motor Core Market
- Asia-Pacific Automotive Drive Motor Core Market
- Europe, Middle East & Africa Automotive Drive Motor Core Market
- Competitive Landscape
- ResearchAI
- ResearchStatistics
- ResearchContacts
- ResearchArticles
- Appendix
- List of Figures [Total: 40]
- List of Tables [Total: 820 ]
Next Steps: Secure Detailed Market Intelligence
For deeper analysis and bespoke consulting on drive motor core trends, regulatory impacts and competitive strategies, contact Ketan Rohom, Associate Director, Sales & Marketing, to secure comprehensive market research and support your strategic planning initiatives.
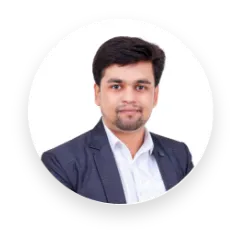
- When do I get the report?
- In what format does this report get delivered to me?
- How long has 360iResearch been around?
- What if I have a question about your reports?
- Can I share this report with my team?
- Can I use your research in my presentation?