The Automotive Lightweight Materials Market size was estimated at USD 104.35 billion in 2024 and expected to reach USD 112.81 billion in 2025, at a CAGR 7.88% to reach USD 164.52 billion by 2030.

Pioneering the Future of Vehicle Performance with Lightweight Materials
The automotive sector stands at a pivotal crossroads, driven by an unrelenting push for enhanced performance, reduced emissions, and stringent regulatory compliance. At the heart of this transformation lies the adoption of advanced lightweight materials, which are redefining vehicle design and manufacturing paradigms. As automakers and suppliers race to satisfy evolving consumer expectations and policy directives, the role of composites, metals, and polymers has moved from peripheral consideration to central strategy.
Regulatory mandates on fuel economy and carbon emissions have amplified the urgency for weight reduction, while electrification trends place even greater emphasis on optimizing every gram. Lightweight materials not only improve power-to-weight ratios and driving range, but they also contribute to lifecycle sustainability by lowering energy consumption across production and use phases. This intersection of performance and environmental responsibility is reshaping supply chain priorities, fostering deeper collaboration between OEMs, material innovators, and process specialists.
Yet, the path to widespread implementation is not without challenges. Cost differentials, technical complexities in joining dissimilar materials, and the need for robust supply networks demand strategic foresight. This executive summary unpacks the most consequential trends shaping this landscape, examines the ripple effects of recent trade measures, and delivers granular segmentation and regional insights. Through in-depth company analysis and rigorous methodology, this report equips decision-makers with the clarity required to harness lightweight materials as engines of competitive advantage.
Revolutionary Dynamics Reshaping Lightweight Material Innovation
A confluence of technological breakthroughs and market forces is catalyzing a profound shift in how the automotive industry approaches material selection. Electrification, in particular, has triggered an imperative for lighter chassis and components to maximize battery efficiency and range. This evolution has spotlighted carbon fiber and other composites that once faced barriers of cost and scalability but now benefit from innovative manufacturing techniques and volume-driven economies.
Simultaneously, advanced metal alloys are experiencing a renaissance as high-strength aluminum, magnesium, and titanium formulations deliver exceptional rigidity-to-weight ratios. Metallurgical refinements and process enhancements such as precision extrusion and forging have broadened the design envelope, enabling structural components to meet rigorous safety standards without adding mass. Within the polymer domain, specialties like polyamide and high-density polyethylene are emerging as viable alternatives for interior trim, under-the-hood applications, and nonstructural elements where impact resistance and thermal stability are paramount.
Moreover, digitalization and Industry 4.0 principles are empowering manufacturers to accelerate prototyping and validation. Virtual material characterization and digital twin platforms streamline the integration of novel substrates into existing assembly lines, while predictive maintenance systems ensure consistent quality in high-throughput molding and casting operations. In parallel, circular economy frameworks are prompting stakeholders to embed recyclability and end-of-life considerations into early design stages, thereby closing the loop on resource efficiency.
Tariff-Driven Transformations Reshaping US Supply Chains
In 2025, the cumulative effect of U.S. tariffs on critical raw materials and component imports has recalibrated procurement strategies across the automotive supply chain. Initial duties imposed on steel and aluminum under national security provisions created a ripple of cost inflation that extended to secondary alloys and specialty composites. Subsequent measures targeting carbon fiber and resin imports have further underscored the vulnerability of global sourcing models reliant on concentrated production hubs.
Faced with escalating landed costs, leading OEMs and tier-one suppliers are accelerating efforts to localize material processing capabilities. Investments in domestic extrusion and composite molding facilities have gained momentum, supported by incentive schemes aimed at enhancing manufacturing sovereignty. These reshoring initiatives are redefining supplier relationships, as regional partnerships replace long-haul logistics and buffer inventories mitigate exposure to potential policy shifts.
Meanwhile, the interplay between tariffs and emerging green subsidies has introduced complex trade-off scenarios. Incentivized domestic production of aluminum and magnesium aligns with environmental objectives under clean energy legislation, but the limited scale of local carbon fiber capacity creates tension between sustainability goals and supply resilience. To navigate this landscape, industry stakeholders are forging strategic alliances that blend financial support with joint R&D programs, ensuring that cost discipline and technological advancement progress in tandem.
Unveiling Deep-Dive Insights Across Critical Market Segments
A nuanced view of the market emerges when dissecting behavior across distinct material categories. Composites harness the superior strength-to-weight advantages of carbon fiber and glass fiber, positioning them at the forefront of next-generation body structures and chassis optimizations. Metals, spanning aluminum, magnesium, and titanium, continue to underpin load-bearing frameworks and high-temperature powertrain applications due to their proven mechanical properties and recyclability. Polymers such as polyamide, polyethylene, and polypropylene are carving out roles in interior assemblies and nonstructural components where durability and cost efficiency converge.
Manufacturing processes add another layer of granularity. Traditional casting remains prevalent for complex geometries in metal parts, while composite molding technologies address the growing demand for integrated panels and crash-resistant assemblies. Extrusion processes deliver consistent cross-sectional profiles for lightweight body reinforcements, forging techniques enhance the mechanical integrity of critical joints, and injection molding leverages rapid cycles for polymer-based fixtures and trims.
When applications are mapped, a clear hierarchy takes shape. Body structures and chassis elements dominate material consumption, reflecting the need for robust yet lightweight frameworks. Interior components capitalize on polymer versatility to meet ergonomics and aesthetic requirements, whereas powertrain segments increasingly integrate metallic alloys that balance thermal management with mass reduction.
Vehicle classifications further refine these patterns. Commercial vehicles, segmented into heavy and light variants, demand materials that combine longevity with cost containment, driving interest in durable metal alloys and glass fiber composites. Passenger vehicles prioritize performance and comfort, elevating the adoption of high-modulus carbon fiber and advanced polymers for premium segments.
Lastly, distribution channels shape market access and procurement lead times. Established offline networks remain the backbone of material supply for high-volume OEMs, but digital platforms are emerging as conduits for specialized suppliers to showcase turnkey solutions and rapid-response capabilities.
This comprehensive research report categorizes the Automotive Lightweight Materials market into clearly defined segments, providing a detailed analysis of emerging trends and precise revenue forecasts to support strategic decision-making.
- Material Type
- Process
- Application
- Vehicle Type
- Distribution Channel
Regional Dynamics Shaping Lightweight Material Adoption
A regional lens reveals divergent trajectories driven by regulatory frameworks, infrastructure maturity, and consumer preferences. In the Americas, stringent fuel economy standards and ambitious emissions targets have accelerated the adoption of lightweight strategies, with U.S. manufacturers and Mexican assembly plants enhancing local aluminum smelting and composite molding investments. Canada’s growing emphasis on sustainable materials further underscores North America’s leadership in circular production models.
Across Europe, Middle East & Africa, evolving safety regulations and carbon neutrality commitments are reshaping material portfolios. European OEMs leverage robust aluminum recycling infrastructures and polymer recovery schemes, while Gulf states and North African hubs explore joint ventures that bring advanced composites manufacturing capacity closer to emerging markets. Vehicle electrification initiatives in this region spur demand for weight-saving substrates that maximize range within densely regulated urban environments.
In the Asia-Pacific zone, relentless vehicle production growth collides with ambitious decarbonization roadmaps. China’s push for domestic carbon fiber facilities and India’s focus on affordable polymer materials illustrate a dual approach to balancing supply security with cost competitiveness. Japan and South Korea continue to advance proprietary high-strength alloys and automated process solutions, ensuring that this region remains a crucible for next-generation lightweight technologies.
This comprehensive research report examines key regions that drive the evolution of the Automotive Lightweight Materials market, offering deep insights into regional trends, growth factors, and industry developments that are influencing market performance.
- Americas
- Europe, Middle East & Africa
- Asia-Pacific
Strategic Moves by Industry Leaders Driving Material Evolution
Global OEMs are intensifying their commitment to material innovation through targeted partnerships and in-house R&D. Leading automotive brands have entered alliances with composite specialists to secure long-term access to high-modulus carbon fiber, while others are forging co-development agreements with metallurgical firms to refine extrusion and forging processes. Tier-one suppliers are similarly expanding their portfolios, establishing dedicated lightweight materials divisions and investing in pilot lines that accelerate the maturation of novel substrates.
Material producers occupy a strategic vantage point, leveraging economies of scale and technical know-how to serve a broad spectrum of vehicle programs. Aluminum specialists have scaled up low-carbon smelting operations, integrating digital quality controls that optimize alloy composition in real time. Carbon fiber manufacturers have diversified feedstock sources to reduce exposure to single-origin risks, while polymer innovators are tailoring resin formulations for enhanced thermal and impact performance.
Joint ventures between OEMs and raw material suppliers are creating vertically integrated ecosystems, where insights from end-use applications inform upstream process improvements. This synergy is manifest in co-located research centers and shared pilot facilities that de-risk technology transitions and shorten product development cycles. As a result, strategic collaborations are eclipsing traditional supplier relationships, establishing new benchmarks for agility and product differentiation.
This comprehensive research report delivers an in-depth overview of the principal market players in the Automotive Lightweight Materials market, evaluating their market share, strategic initiatives, and competitive positioning to illuminate the factors shaping the competitive landscape.
- Alcoa Corporation
- Novelis Inc.
- Constellium N.V.
- SGL Carbon
- Toray Industries, Inc.
- Hexcel Corporation
- Solvay S.A.
- Teijin Limited
- Mitsubishi Chemical Holdings Corporation
- Evonik Industries AG
Blueprint for Leadership in the Lightweight Materials Era
To thrive in this era of material complexity, industry leaders must adopt a proactive approach that blends technical rigor with strategic foresight. First, fostering deep partnerships across the value chain will ensure early visibility into emerging substrates and process advances. Collaborative innovation hubs and joint testing programs can bridge the gap between concept and production, equipping teams to validate performance under real-world conditions.
Second, investing in digital engineering platforms such as virtual material databases and simulation-driven design tools will streamline integration of lightweight elements into existing vehicle architectures. These systems accelerate iteration cycles, reduce physical prototyping costs, and enable rapid scenario analysis to balance trade-offs between weight, cost, and safety.
Third, supply chain resilience demands diversification of raw material sources and the development of regional production nodes. By aligning manufacturing footprints with tariff landscapes and logistical considerations, organizations can mitigate risk while capturing local incentives for sustainable operations.
Finally, embedding circular economy principles at the outset of product design will unlock long-term value. Strategies such as modular component design, end-of-life recyclability standards, and material traceability frameworks reinforce brand commitments to environmental stewardship and resonate with increasingly eco-conscious consumers.
Rigorous Research Framework Underpinning Market Intelligence
This study draws on a dual methodology combining extensive primary research with rigorous secondary analysis. Primary insights were gathered through in-depth interviews with senior executives across OEMs, tier-one suppliers, and material manufacturers, enabling a firsthand understanding of strategic priorities and technical challenges. Supplementing these discussions, field visits to advanced production facilities provided empirical validation of process capabilities and scalability.
Secondary research encompassed a comprehensive review of industry publications, regulatory filings, patent databases, and technical papers. Data triangulation techniques ensured consistency across divergent sources, while a structured framework assessed each material category against performance, cost, sustainability, and supply security criteria. The research team employed scenario planning to stress-test the implications of policy shifts, tariff changes, and technological breakthroughs.
Quality assurance protocols included peer reviews by subject matter experts and cross-validation with third-party analysts. The resulting insights reflect a holistic perspective on market dynamics, offering robust guidance for strategic planning and investment decision-making.
Explore AI-driven insights for the Automotive Lightweight Materials market with ResearchAI on our online platform, providing deeper, data-backed market analysis.
Ask ResearchAI anything
World's First Innovative Al for Market Research
Consolidating Key Themes for Material-Driven Success
As the automotive industry accelerates toward a low-carbon future, lightweight materials have emerged as a cornerstone of competitive advantage. From the granular shifts in material composition to the far-reaching effects of trade policy, the landscape is characterized by dynamic interplay between regulation, technology, and strategic collaboration. By dissecting segmentation nuances and regional disparities, this analysis highlights clear pathways for organizations to optimize performance, cost, and sustainability objectives.
Industry leaders that embrace digital-driven design tools, foster integrated partnerships, and build resilient supply networks will be best positioned to navigate tariff volatility and regulatory complexity. As manufacturers refine their approaches, the integration of circular economy principles and advanced process technologies will define the next generation of vehicle platforms. The insights presented herein offer a foundational blueprint for driving material-centric innovation and securing long-term value in an increasingly demanding marketplace.
This section provides a structured overview of the report, outlining key chapters and topics covered for easy reference in our Automotive Lightweight Materials market comprehensive research report.
- Preface
- Research Methodology
- Executive Summary
- Market Overview
- Market Dynamics
- Market Insights
- Cumulative Impact of United States Tariffs 2025
- Automotive Lightweight Materials Market, by Material Type
- Automotive Lightweight Materials Market, by Process
- Automotive Lightweight Materials Market, by Application
- Automotive Lightweight Materials Market, by Vehicle Type
- Automotive Lightweight Materials Market, by Distribution Channel
- Americas Automotive Lightweight Materials Market
- Europe, Middle East & Africa Automotive Lightweight Materials Market
- Asia-Pacific Automotive Lightweight Materials Market
- Competitive Landscape
- ResearchAI
- ResearchStatistics
- ResearchContacts
- ResearchArticles
- Appendix
- List of Figures [Total: 26]
- List of Tables [Total: 415 ]
Secure Your Competitive Edge with Exclusive Expert Analysis
For executives seeking a decisive advantage in the competitive automotive arena, securing access to comprehensive intelligence is paramount. Reach out to Ketan Rohom, Associate Director, Sales & Marketing at 360iResearch, to obtain the full market research report on automotive lightweight materials. His expertise will guide you through tailored solutions, enabling you to harness detailed analysis, strategic insights, and hands-on recommendations that drive innovation and profitability. Don’t miss this opportunity to elevate your strategic roadmap with authoritative data and actionable guidance designed for immediate implementation. Contact Ketan today to transform insights into impact and ensure your organization leads the lightweight materials revolution.
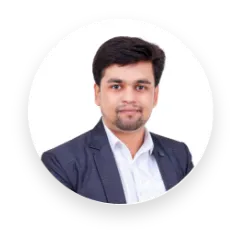
- How big is the Automotive Lightweight Materials Market?
- What is the Automotive Lightweight Materials Market growth?
- When do I get the report?
- In what format does this report get delivered to me?
- How long has 360iResearch been around?
- What if I have a question about your reports?
- Can I share this report with my team?
- Can I use your research in my presentation?