The Automotive Magnesium Die Casting Market size was estimated at USD 4.20 billion in 2024 and expected to reach USD 4.46 billion in 2025, at a CAGR 6.02% to reach USD 5.97 billion by 2030.
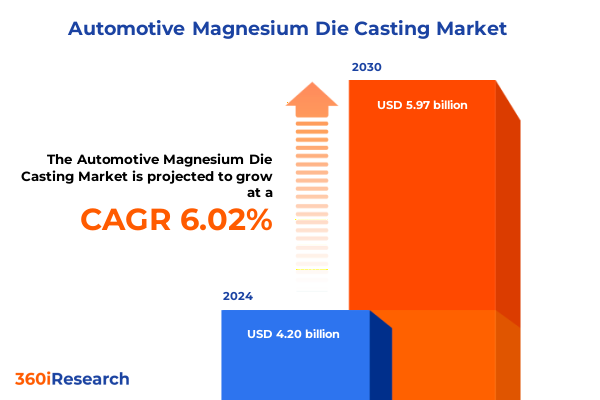
Introduction to the Automotive Magnesium Die Casting Market
The automotive industry is undergoing a fundamental shift toward lighter, more efficient materials, and magnesium die casting stands at the forefront of this transformation. Magnesium’s exceptional strength-to-weight ratio makes it an ideal choice for reducing vehicle mass, improving fuel economy in internal combustion engine vehicles, and extending range in battery electric vehicles. As OEMs and suppliers seek innovative solutions to meet stringent emissions regulations and rising consumer demand for performance and sustainability, die-cast magnesium components have emerged as key enablers of next-generation vehicle platforms.
Recent advances in casting technologies-ranging from high-pressure and low-pressure methods to squeeze, thixomolding, and vacuum systems-have expanded design freedom and optimized production efficiency. Complemented by developments in alloy chemistry, such as AM60B, AZ91D, and ZK60 grades, and process innovation in cold and hot chamber die casting, the market is poised for rapid growth. At the same time, global trade dynamics, including new tariffs and shifting supply chains, introduce both challenges and opportunities for manufacturers and end-users alike.
This executive summary provides a concise yet comprehensive overview of the pivotal trends, policy impacts, segmentation insights, regional dynamics, competitive landscape, and strategic actions that will shape the automotive magnesium die casting market over the coming years.
Transformative Shifts Reshaping Automotive Magnesium Die Casting
Automotive magnesium die casting is experiencing transformative shifts driven by the confluence of electrification, sustainability mandates, and digital innovation. Electrified powertrains demand lightweight structural elements, steering adoption of magnesium alloys for components ranging from crossmembers and subframes in chassis assemblies to body side outrigger structures and roof panels. Regulatory pressures to meet stringent CO₂ targets have accelerated material substitution, with magnesium rapidly replacing steel and aluminum in both structural and non-structural functions.
Simultaneously, advanced casting techniques are redefining production capabilities. High-pressure systems now boast precision tolerances for intricate geometries, while low-pressure and squeeze processes enhance mechanical properties for critical powertrain applications such as cylinder heads, engine blocks, and transmission cases. Thixomolding and vacuum die casting are unlocking complex electronic enclosures and connector housings, responding to rising integration of sensors and electronic control units. Industry 4.0 integration-through real-time monitoring, predictive maintenance, and digital twins-is further improving yield and reducing scrap rates, enabling just-in-time delivery and flexible manufacturing. These converging trends are reshaping the industry landscape, compelling stakeholders to innovate across design, process, and supply chain dimensions.
Cumulative Impact of United States Tariffs in 2025
The implementation of new U.S. tariffs in early 2025 has had a cumulative effect on the automotive magnesium die casting supply chain. With levies targeting certain magnesium ingots and cast parts, import costs from major producing regions have risen sharply, compelling manufacturers to reevaluate sourcing strategies. North American die casters have responded by accelerating near-shoring efforts, qualifying domestic suppliers, and investing in integrated recycling streams to secure lower-cost secondary ingots.
As a result, lead times for imported raw material have extended, driving a premium on just-in-stock inventory and creating upward pressure on component pricing. OEMs face heightened cost volatility, prompting collaborative negotiations with suppliers to mitigate cost pass-through while preserving profitability. At the same time, tariff-induced supply constraints have spurred strategic alliances between U.S. and European die casters to share best practices, co-develop new AM60B and AZ91D alloy formulations, and optimize production footprints across high-pressure, cold chamber, and hot chamber die casting operations. In this environment, agility and supply chain resilience will be critical to maintaining competitive advantage.
Key Segmentation Insights Driving Market Dynamics
A granular view of the market reveals distinct performance drivers across multiple segmentation dimensions. When analyzed by casting type-spanning high pressure, low pressure, squeeze, thixomolding, and vacuum processes-high-pressure systems continue to dominate in high-volume chassis and body structure components due to cycle efficiency and dimensional accuracy. Low-pressure and squeeze techniques are gaining traction for powertrain parts such as cylinder heads, engine blocks, and transmission cases, where enhanced microstructure and fatigue resistance are paramount. Thixomolding and vacuum die casting carve out specialized niches in electronics components, including connector bodies and sensor housings, where material integrity and surface finish directly influence system reliability.
Application segmentation highlights the criticality of body structures-comprising body side outriggers and roof panels-in achieving lightweight targets, while chassis sub-segments like crossmembers and subframes leverage magnesium’s damping properties for improved ride comfort. Electronics components yield rapid growth as automakers integrate sophisticated control modules, requiring magnesium enclosures with precise thermal management. Interior component adoption in console substrates and seat frames accelerates ergonomic design without compromising safety. In powertrain applications, the shift toward electrified architectures places premium emphasis on lightweight transmission cases and motor housings.
Examining end-use industries-commercial vehicles, electric vehicles, and passenger cars-reveals that electric vehicles, both battery electric and plug-in hybrid models, spearhead demand for ultra-light structural castings to offset battery weight. Among passenger car segments, SUVs demonstrate outsized consumption given their size and performance targets, while sedans and hatchbacks follow closely. In commercial vehicles, both heavy duty trucks and light commercial platforms are exploring magnesium integrations to comply with evolving emissions standards and payload requirements.
Material selection exerts a decisive influence, with AM60B alloy prized for its ductility in structural applications, AZ91D alloy favored for general casting due to balanced strength and castability, and ZK60 alloy chosen for high-performance powertrain elements requiring elevated tensile properties. Technology choice-cold chamber versus hot chamber die casting-depends on component complexity and cycle time demands, with cold chamber dominating heavy-section parts. Component-level analysis underscores growth in gear housings, instrument panels, and transmission covers as electrification drives new packaging configurations. Manufacturing process trends in coremaking, particularly core blowing, and degating operations are optimizing internal cavity formation and post-cast finishing, reducing secondary machining costs. Finally, functional differentiation between structural and non-structural applications highlights the trajectory of high-load bearing castings in vehicle monocoques and critical support structures versus cosmetic or ancillary parts.
This comprehensive research report categorizes the Automotive Magnesium Die Casting market into clearly defined segments, providing a detailed analysis of emerging trends and precise revenue forecasts to support strategic decision-making.
- Casting Type
- Application
- End-Use Industry
- Material
- Technology
- Component
- Manufacturing Process
- Function
Geographic Landscape: Regional Insights
Regional dynamics in the automotive magnesium die casting market demonstrate varied growth drivers and strategic imperatives across the Americas, Europe, Middle East & Africa, and Asia-Pacific. In the Americas, strong incentives for reshoring and domestic content requirements have made the U.S. and Mexico increasingly attractive for die cast part production, with OEMs investing in local high-pressure and cold chamber capacity to hedge against tariff exposure. Canada’s focus on sustainable supply chains further catalyzes partnerships in recycled magnesium streams.
Across Europe, Middle East & Africa, the push for carbon neutrality and circular economy initiatives fuels demand for high-integrity magnesium alloys. German and French OEMs are collaborating with regional casters to pioneer advanced AZ91D and ZK60 components for next-generation EV platforms. In the Middle East, infrastructure investments and diversification strategies are encouraging localized casting hubs, while Africa’s emerging automotive clusters in South Africa and Morocco explore entry-level applications.
Asia-Pacific remains the largest global production base, led by China, Japan, and South Korea. Chinese suppliers, despite export tariffs, continue to leverage scale for cost-competitive supply, while Japanese and Korean die casters emphasize high-precision technologies for premium passenger cars and luxury EVs. India’s automotive market expansion and government support for lightweight materials mark it as a rising player, particularly in cold chamber and hot chamber investments for both domestic OEMs and export markets.
This comprehensive research report examines key regions that drive the evolution of the Automotive Magnesium Die Casting market, offering deep insights into regional trends, growth factors, and industry developments that are influencing market performance.
- Americas
- Asia-Pacific
- Europe, Middle East & Africa
Competitive Landscape: Key Companies Insights
The competitive landscape is populated by established global players and emerging specialists. A&B Die Casting and Aludyne, Inc. are recognized for high-volume structural castings, leveraging integrated foundry networks to serve major OEMs. Chicago White Metal Casting, Inc. and Dynacast by Form Technologies excel in micro-precision electronic components, supporting advanced driver-assistance systems. Dongguan Minghe Die Casting Company and Magic Precision Inc. harness advanced vacuum processes to deliver critical connectors and enclosures for growing EV applications.
Georg Fischer AG and Pace Industries maintain diversified portfolios spanning chassis, body, and interior applications, benefitting from scale and cross-continental production flexibility. Gibbs Die Casting and Meridian Lightweight Technologies have focused on aluminum-magnesium hybrid structures, exploring proprietary alloy blends and process refinements. Ibex Engineering Pvt. Ltd. and Sundaram Clayton Limited underscore the rise of Indian capability in powertrain and gearbox housings, driven by cost-efficient manufacturing and rising domestic OEM integration.
Kinetic Die Casting Company and Mira Engineers have differentiated through rapid prototyping and coremaking innovations, including core blowing, enabling faster time-to-market. Morimura Bros., Inc. and Ortal Ltd. deploy specialized thixomolding lines, targeting high-complexity interior and exterior trim pieces. Ryobi Limited, Sandhar Technologies Limited, and Twin City Die Castings Co. round out the field with balanced portfolios across casting types and components, addressing both legacy engine platforms and emerging electric powertrain architectures.
This comprehensive research report delivers an in-depth overview of the principal market players in the Automotive Magnesium Die Casting market, evaluating their market share, strategic initiatives, and competitive positioning to illuminate the factors shaping the competitive landscape.
- A&B Die Casting
- Aludyne, Inc.
- Chicago White Metal Casting, Inc.
- Dongguan Minghe Die Casting Company
- Dynacast by Form Technologies
- Georg Fischer AG
- Gibbs Die Casting
- Ibex Engineering Pvt. Ltd.
- Kinetic Die Casting Company
- Magic Precision Inc.
- Meridian Lightweight Technologies
- Mira Engineers
- Morimura Bros., Inc.
- Ortal Ltd.
- Pace Industries
- Ryobi Limited
- Sandhar Technologies Limited
- Sundaram Clayton Limited
- Twin City Die Castings Co.
Actionable Recommendations for Industry Leaders
To capitalize on the evolving landscape, industry leaders should pursue several strategic imperatives. First, expand regional production footprints to mitigate tariff risk and align with OEM localization policies; this includes evaluating joint ventures or greenfield facilities in key markets. Second, diversify alloy and process capabilities by investing in R&D for next-generation magnesium formulations and integrating both cold and hot chamber die casting to serve a broader application spectrum.
Third, strengthen supply chain resilience through long-term contracts with recycled magnesium suppliers and digital traceability systems, ensuring consistent quality and compliance with sustainability mandates. Fourth, accelerate adoption of Industry 4.0 solutions-such as predictive analytics, digital twins, and advanced automation-to optimize throughput, reduce scrap, and enable flexible batch production. Fifth, foster collaborative partnerships across the value chain, including material scientists, OEM design teams, and aftermarket specialists, to co-develop lightweight structures and multifunctional components. Finally, embed regulatory intelligence into product roadmaps, proactively addressing emissions, recyclability, and safety standards to maintain market access and reputational advantage.
Explore AI-driven insights for the Automotive Magnesium Die Casting market with ResearchAI on our online platform, providing deeper, data-backed market analysis.
Ask ResearchAI anything
World's First Innovative Al for Market Research
Conclusion: Navigating Future Opportunities
Automotive magnesium die casting is at a pivotal juncture, driven by the dual imperatives of lightweighting and electrification. Stakeholders who embrace advanced casting methodologies, invest in alloy innovation, and proactively navigate geopolitical and regulatory headwinds will secure leadership positions. The interplay of market segmentation insights-from casting type and application to end-use industry and material selection-provides a roadmap for prioritizing investments and tailoring capabilities to high-growth areas such as EV powertrains and structural body components.
Regional diversification and competitive differentiation, underpinned by digital transformation and supply chain resilience, will define winners in the next wave of industry consolidation. By aligning strategic actions with emerging customer requirements and policy trends, manufacturers can turn the challenges of new tariffs and evolving standards into opportunities for value creation and sustained profitability.
This section provides a structured overview of the report, outlining key chapters and topics covered for easy reference in our Automotive Magnesium Die Casting market comprehensive research report.
- Preface
- Research Methodology
- Executive Summary
- Market Overview
- Market Dynamics
- Market Insights
- Cumulative Impact of United States Tariffs 2025
- Automotive Magnesium Die Casting Market, by Casting Type
- Automotive Magnesium Die Casting Market, by Application
- Automotive Magnesium Die Casting Market, by End-Use Industry
- Automotive Magnesium Die Casting Market, by Material
- Automotive Magnesium Die Casting Market, by Technology
- Automotive Magnesium Die Casting Market, by Component
- Automotive Magnesium Die Casting Market, by Manufacturing Process
- Automotive Magnesium Die Casting Market, by Function
- Americas Automotive Magnesium Die Casting Market
- Asia-Pacific Automotive Magnesium Die Casting Market
- Europe, Middle East & Africa Automotive Magnesium Die Casting Market
- Competitive Landscape
- ResearchAI
- ResearchStatistics
- ResearchContacts
- ResearchArticles
- Appendix
- List of Figures [Total: 32]
- List of Tables [Total: 769 ]
Next Steps: Connect with Ketan Rohom to Secure the Full Report
To gain comprehensive visibility into market dynamics, emerging technologies, competitive positioning, and strategic outlooks, schedule a direct discussion with Ketan Rohom, Associate Director, Sales & Marketing. Engage today to secure detailed intelligence, tailored insights, and actionable guidance that will empower your organization to lead the automotive magnesium die casting sector. Reach out now and unlock the full market research report for informed decision-making and competitive advantage.
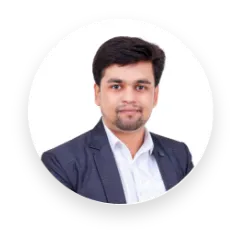
- How big is the Automotive Magnesium Die Casting Market?
- What is the Automotive Magnesium Die Casting Market growth?
- When do I get the report?
- In what format does this report get delivered to me?
- How long has 360iResearch been around?
- What if I have a question about your reports?
- Can I share this report with my team?
- Can I use your research in my presentation?