The Automotive Metal Market size was estimated at USD 114.98 billion in 2024 and expected to reach USD 123.88 billion in 2025, at a CAGR 7.38% to reach USD 176.32 billion by 2030.

Unveiling the Current Dynamics of Automotive Metal Industry
The automotive metal industry stands at a pivotal crossroads, where escalating demand for lightweight structures, stringent emissions regulations, and rapid technological breakthroughs drive unprecedented change. As conventional combustion engines share the stage with electric drivetrains and hybrid power units, manufacturers are compelled to reassess material choices and processing methods to achieve optimal performance and sustainability. Simultaneously, raw material cost volatility and growing pressure to localize supply chains have intensified strategic deliberations across boardrooms worldwide.
In this dynamic environment, a nuanced understanding of evolving market forces becomes indispensable for stakeholders seeking to maintain a competitive edge. This executive summary distills the core developments shaping the landscape, examines regulatory interventions and tariff regimes, and highlights segmentation and regional patterns that illuminate growth pockets. With expert perspectives woven throughout, decision makers will gain clarity on strategic imperatives and emerging opportunities that will define the next era of automotive manufacturing.
Redefining the Industry Through Technological and Regulatory Disruptions
Technological innovation and sustainability mandates have sparked a series of transformative shifts across the automotive metal sector. Electric vehicle proliferation has elevated the importance of high-strength aluminum alloys and advanced composites, compelling producers to expand capacities for die-cast and wrought aluminum while optimizing magnesium casting processes. Concurrently, digital twin modeling and additive manufacturing are redefining design cycles, enabling intricate part geometries and rapid prototyping that were previously unattainable with traditional stamping and forging.
Regulatory landscapes have also evolved in tandem, with tighter fuel efficiency standards and carbon emission targets prompting mass reduction initiatives. Manufacturers now leverage closed-die and open-die forging techniques to bolster component integrity while minimizing weight. In parallel, sustainability considerations have spurred investments in recyclable and low-embodied-energy materials, signaling a shift towards circular economy principles. These converging forces are driving a holistic reinvention of material selection, production methodologies, and value chain partnerships.
Assessing the Far-Reaching Effects of 2025 United States Tariffs
The introduction of new United States tariffs in 2025 has reverberated across global automotive metal supply chains, altering trade flows and cost structures. Steel imports now attract heightened duties, prompting manufacturers to pivot towards domestically sourced carbon steel and stainless grades. Aluminum extrusions and castings have faced additional levies, compelling many OEMs to reassess sourcing strategies and accelerate investments in local production sites.
As a consequence, regional suppliers within North America have expanded capacity, while multinational corporations have relocated certain processing lines to mitigate tariff exposure. Upstream raw material costs have risen, putting pressure on profit margins and heightening the impetus for operational efficiency. Meanwhile, importers of magnesium and titanium have encountered analogous burdens, incentivizing the development of alternative alloys and material substitutions where feasible. Collectively, these measures have reconfigured competitiveness dynamics, with long-term ramifications for both established and emerging participants.
Decoding Market Potential Across Product, Vehicle, Application and Material Dimensions
When analyzing market segmentation through the lens of product typology, castings emerge as a cornerstone category subdivided into aluminum castings, iron castings, and magnesium castings. Each subsegment presents unique performance attributes, from the corrosion resistance and weight optimization of aluminum to the cost efficiency and durability of iron alloys. Forgings follow closely, differentiated by closed-die, open-die, and ring forging processes that yield components with superior grain structure and mechanical strength. Sheet metal remains critical, encompassing cold rolled steel, hot rolled steel, and stainless steel, each offering a distinct balance of formability, tensile strength, and finish quality. Stamped components complete the picture, ranging from exterior panels to interior reinforcements and structural members that underpin vehicle integrity.
In parallel, segmentation by vehicle type reveals divergent material demands. Commercial vehicles, spanning heavy and light payload platforms, prioritize high-strength steel and cast iron in drivetrain and chassis elements. Passenger vehicles, including hatchbacks, MPVs, sedans, and SUVs, increasingly adopt aluminum and magnesium solutions to meet fuel economy targets without compromising safety. Two wheelers, from motorcycles to scooters, rely on lightweight cast aluminum and press-formed sheet metal to balance agility with cost-effectiveness.
Evaluating application-based divisions highlights the strategic importance of body structure, encompassing inner frameworks and outer panels that dictate crashworthiness and weight distribution. Chassis components, such as axles and subframes, demand precision forging and robust stamping to withstand mechanical loads. Interior elements, including decorative trim and functional parts, integrate advanced alloys for aesthetic appeal and durability. Powertrain applications leverage engine and transmission components that must endure thermal stress and cyclic fatigue, driving innovation in material composition and surface treatments.
Finally, material-type segmentation underscores the varied role of aluminum, magnesium, steel, and titanium. Aluminum branches into cast and wrought forms tailored for structural and sheet applications, while magnesium divides into die-cast and wrought grades prized for extreme weight reduction. Steel bifurcates into carbon steel and stainless varieties that deliver strength and corrosion control, and titanium, available as pure metal or alloys, serves niche high-performance scenarios where cost can be justified by critical benefits.
This comprehensive research report categorizes the Automotive Metal market into clearly defined segments, providing a detailed analysis of emerging trends and precise revenue forecasts to support strategic decision-making.
- Product Type
- Vehicle Type
- Application
- Material Type
Navigating Growth Trajectories Across Key Global Regions
Regional dynamics reveal distinct growth trajectories across the Americas, Europe Middle East and Africa, and Asia-Pacific. In the Americas, a resurgence of localized manufacturing is underway, spurred by reshored capacities and robust infrastructure investment. North American producers are capitalizing on tariff-driven incentives to expand steel and aluminum processing plants, while Latin American markets demonstrate potential in light commercial vehicle segments.
Across Europe Middle East and Africa, tightening emissions regulations and ambitious carbon neutrality targets are accelerating adoption of lightweight alloys and advanced forging techniques. OEMs headquartered in Western Europe continue to lead in high-value applications, whereas emerging markets in Eastern Europe and the Middle East offer cost-competitive hubs for sheet metal stamping and component assembly.
Meanwhile, Asia-Pacific remains the largest volume center, driven by strong passenger vehicle production in China and India and expanding two-wheeler demand across Southeast Asia. Domestic metal producers are intensifying capacity expansions for cold rolled steel and magnesium castings to serve fast-growing electrified vehicle platforms. Regulatory alignment with global safety standards is also fostering new partnerships and joint ventures that will further consolidate the regional supply base.
This comprehensive research report examines key regions that drive the evolution of the Automotive Metal market, offering deep insights into regional trends, growth factors, and industry developments that are influencing market performance.
- Americas
- Europe, Middle East & Africa
- Asia-Pacific
Profiling Leading Players Shaping Industry Trends
Leading companies are deploying strategic initiatives to cement their positions in an increasingly competitive environment. Multinational corporations have diversified upstream raw material sourcing and invested in next-generation alloy development through dedicated R&D centers. Strategic alliances between forging specialists and OEMs are facilitating co-development of bespoke components for electric drivetrains and high-efficiency powertrains.
At the same time, sheet metal and stamping leaders are upgrading production lines with digital quality monitoring and predictive maintenance systems to boost throughput and yield. In the realm of advanced castings, a handful of innovators have pioneered proprietary technologies that enhance grain refinement and reduce porosity, capturing premium applications in lightweight vehicle segments. Meanwhile, vertically integrated groups are leveraging integrated supply chains-from raw metal mills to finished component assembly-to optimize lead times and cost structures. Collectively, these competitive moves underscore the emphasis on agility, technological leadership, and end-to-end value chain integration.
This comprehensive research report delivers an in-depth overview of the principal market players in the Automotive Metal market, evaluating their market share, strategic initiatives, and competitive positioning to illuminate the factors shaping the competitive landscape.
- Ulbrich Stainless Steels & Special Metals, Inc.
- thyssenkrupp Materials NA, Inc.
- H & S Manufacturing Co.
- Steel Warehouse Company LLC
- Gestamp Automoción, S.A.
- Versa-Bar, Inc.
- Worthington Industries, Inc.
- Arbor/Metals Inc.
- Mills Products, Inc.
- Drawn Metal Tube Company
Strategic Actions to Secure Competitive Advantage
Industry leaders should prioritize a balanced approach that harmonizes material innovation with supply chain resilience. Establishing collaborative ventures with alloy developers will accelerate the adoption of next-gen aluminum and magnesium blends, while securing long-term raw material agreements can shield operations from price fluctuations. Concurrently, investing in digital manufacturing platforms and in-line inspection systems will drive productivity gains and enhance quality consistency.
Adapting to tariff-driven market realignments requires diversification of production footprints and exploration of nearshore alternatives. By cultivating relationships with regional mini-mills and forging suppliers, stakeholders can reduce logistical complexities and respond swiftly to policy shifts. Integration of circular economy practices-such as closed-loop recycling for high-value steels and alloys-will further strengthen sustainability credentials and unlock cost savings. In parallel, executive teams should embed scenario planning into strategic roadmaps to anticipate regulatory changes and technology disruptions, thereby safeguarding competitive advantage in a rapidly evolving landscape.
Robust Methodological Framework Underpinning the Analysis
The analysis underpinning this report integrates comprehensive desk research, primary stakeholder interviews, and multi-tier data validation. A systematic literature review of industry publications and regulatory filings established foundational context, while conversations with materials scientists, procurement executives, and manufacturing engineers provided ground-level intelligence on emerging trends.
Quantitative insights were derived from customs data, trade association statistics, and proprietary supplier performance metrics. These figures underwent rigorous cross-referencing against company disclosures and expert estimates to ensure accuracy and credibility. Market segmentation was constructed by aligning product, vehicle, application, and material classifications with real-world supply chain practices. Geographical analysis accounted for production volumes, capacity expansions, and policy environments.
Throughout the methodology, an iterative approach to data triangulation reinforced the robustness of findings. Insights were further validated through workshops with technical advisors and client feedback sessions, ensuring that the conclusions reflect both strategic relevance and operational practicability.
Explore AI-driven insights for the Automotive Metal market with ResearchAI on our online platform, providing deeper, data-backed market analysis.
Ask ResearchAI anything
World's First Innovative Al for Market Research
Synthesis of Critical Findings and Future Outlook
In synthesizing the critical findings, it becomes clear that the automotive metal industry is being reshaped by the confluence of electrification, sustainability imperatives, and protective trade measures. Product diversification strategies across castings, forgings, sheet metal, and stamped components highlight the growing need for custom alloys and advanced manufacturing techniques. Vehicle segmentation underscores how passenger vehicles and two-wheelers are spearheading lightweight material adoption, while commercial platforms continue to rely on traditional steel and iron formulations.
Regional insights reveal a realignment of manufacturing epicenters, as policy incentives and tariff structures redirect investments and capacity expansions. Leading companies that combine technological prowess with agile supply chain configurations are best positioned to thrive. Actionable recommendations emphasize collaboration across the value chain, integration of circular practices, and rigorous scenario planning to navigate policy uncertainties.
Ultimately, stakeholders who embrace a strategic blend of innovation, resilience, and sustainability will unlock new avenues for growth and maintain a competitive edge in a market defined by relentless transformation.
This section provides a structured overview of the report, outlining key chapters and topics covered for easy reference in our Automotive Metal market comprehensive research report.
- Preface
- Research Methodology
- Executive Summary
- Market Overview
- Market Dynamics
- Market Insights
- Cumulative Impact of United States Tariffs 2025
- Automotive Metal Market, by Product Type
- Automotive Metal Market, by Vehicle Type
- Automotive Metal Market, by Application
- Automotive Metal Market, by Material Type
- Americas Automotive Metal Market
- Europe, Middle East & Africa Automotive Metal Market
- Asia-Pacific Automotive Metal Market
- Competitive Landscape
- ResearchAI
- ResearchStatistics
- ResearchContacts
- ResearchArticles
- Appendix
- List of Figures [Total: 24]
- List of Tables [Total: 860 ]
Partner with Our Expert to Unlock In-Depth Market Insights
Elevate your strategic decision making with tailored insights by reaching out to Ketan Rohom, Associate Director of Sales & Marketing at 360i. Discover how in-depth analysis of product types, vehicle categories, applications, and materials can guide your next investment. Engage directly to explore customizable packages, explore sample chapters, and secure competitive advantage with authoritative intelligence. Take the next step toward unlocking your full market potential by scheduling a consultation today.
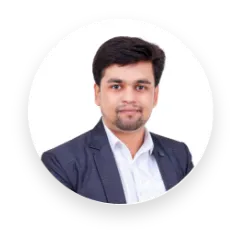
- How big is the Automotive Metal Market?
- What is the Automotive Metal Market growth?
- When do I get the report?
- In what format does this report get delivered to me?
- How long has 360iResearch been around?
- What if I have a question about your reports?
- Can I share this report with my team?
- Can I use your research in my presentation?