The Automotive Mold Market size was estimated at USD 43.76 billion in 2024 and expected to reach USD 46.64 billion in 2025, at a CAGR 6.52% to reach USD 63.94 billion by 2030.

Setting the Stage for Automotive Mold Market Innovation
The automotive mold sector is undergoing an era of profound transformation driven by rapid technological advancements, evolving automotive architectures, and mounting regulatory demands. As vehicles embrace electrification, lightweight composites, and complex geometries, mold manufacturers are compelled to innovate in design, materials, and process automation. This convergence of trends heralds unprecedented opportunities for those able to adapt swiftly, as well as significant challenges for traditional production methods.
In recent years, injection molding has emerged as a cornerstone technology for high-volume, precision components, particularly within interior and exterior assemblies. Simultaneously, compression and blow molding continue to serve specialty applications, demanding an agile approach to tooling design and material selection. Market players are now navigating a dynamic environment where digital thread integration, additive manufacturing for rapid prototyping, and real-time process monitoring are becoming table stakes for competitiveness.
This report delves into the critical drivers steering the automotive mold landscape, offering a comprehensive overview of market dynamics, emerging innovations, and key stakeholders. By establishing this foundational context, readers will gain a clear understanding of the factors shaping demand, the evolving value chain, and the imperatives for strategic investment and partnerships going forward.
Driving Forces Reshaping the Automotive Mold Landscape
Electrification of powertrain systems has rapidly elevated demand for intricate polymer and elastomer components, propelling injection molders to refine multi-cavity tooling while optimizing cycle times. As OEMs pivot toward electric vehicles, mold designers are tasked with accommodating novel battery housings, coolant channels, and lightweight structural elements that must balance mechanical integrity with thermal performance.
Sustainability and circular economy imperatives have further accelerated interest in thermoplastic polymers capable of efficient recycling. Engineering plastics such as ABS, PA, PBT, and PC are now scrutinized not only for their mechanical and chemical properties but also for their end-of-life recyclability. At the same time, polyolefins including polyethylene and polypropylene are gaining traction as cost-effective alternatives for select non-critical applications, prompting material scientists and molders to collaborate more closely than ever.
Automation and Industry 4.0 frameworks are increasingly integrated into mold production lines, enabling fully automatic, semi-automatic, and manual cell configurations that enhance throughput and quality consistency. Real-time process data, predictive maintenance, and adaptive control systems are driving continuous improvement, allowing manufacturers to meet stringent OEM specifications while mitigating downtime and scrap rates.
As regulatory bodies worldwide tighten emissions and safety standards, mold developers must also account for fire retardancy, UV resistance, and chemical stability in targeted end-use environments. This regulatory overlay intensifies the complexity of tooling design and material selection, reinforcing the need for robust testing protocols and strategic alliances across the supply chain.
Evaluating the 2025 United States Tariff Impacts on Molding Operations
The implementation of targeted United States tariffs in early 2025 has introduced new cost pressures across the automotive mold supply chain. Imported tooling and associated raw materials face elevated duties, compelling domestic and international suppliers to reassess sourcing strategies. In response, several manufacturers have accelerated local production investments to mitigate the impact of higher import costs and potential supply chain disruptions.
Tariffs on compression and blow mold equipment have disproportionately affected smaller molders reliant on specialized European and Asian machinery. These increased duties have prompted a critical evaluation of capital expenditure plans, with some firms postponing modernization projects while others are exploring alternative vendors in countries outside the tariff scope. Conversely, injection molders with local facilities have gained a competitive edge as OEMs seek to shorten lead times and stabilize component costs.
Material tariffs, particularly on select thermoset polymers and elastomers, have further complicated cost structures. Manufacturers are now negotiating long-term supply contracts to lock in pricing and ensure continuity. At the same time, the broader market has witnessed a shift toward domestically produced thermoplastic polymers, partially offsetting tariff-induced inflation.
Ultimately, the tariff landscape is driving heightened collaboration between molders, material suppliers, and OEMs to navigate cost volatility. Strategic alliances, joint ventures, and co-investment in regional manufacturing hubs are emerging as pragmatic solutions to counteract the financial implications of the tariffs while maintaining agility in a rapidly evolving market.
Unveiling Critical Segmentation Trends in Automotive Mold Demand
An in-depth look at mold type segmentation reveals that injection molding continues to dominate volume production, with single cavity and multi cavity tooling addressing applications ranging from dashboard components to underbody fittings. Compression mold and blow mold technologies remain essential for specialized parts such as sealants, gaskets, and fluid reservoirs, with transfer mold serving niche powertrain and sensor housings. This diversity in mold type reflects a market that demands both precision and versatility.
Material segmentation underscores the importance of thermoplastic polymers in modern vehicle architectures. Elastomers are leveraged for their flexibility and sealing properties, while thermoset polymers secure applications requiring thermal stability and chemical resistance. Within thermoplastic polymers, engineering plastics such as ABS, PA, PBT, and PC are favored for high-performance interior and exterior components, whereas polyolefins including polyethylene and polypropylene offer cost-effective solutions for non-structural parts.
Vehicle type segmentation highlights the distinct requirements of passenger vehicles, commercial trucks, and off highway machinery. Cars, SUVs, and vans each drive different volume dynamics and component specifications, reflecting consumer preferences for comfort, safety, and design aesthetics. Commercial vehicles emphasize durability and load-bearing capabilities, while off highway applications prioritize resistance to extreme conditions and mechanical stress.
End-use segmentation illuminates how electrical components for advanced driver assistance systems and infotainment require ultra-precise molds, exterior components demand aesthetic finishes and tight tolerances, interior parts must balance tactile quality with durability, powertrain components necessitate robust thermal performance, and underbody sections call for complex geometries to integrate structural reinforcements and skid plates.
Sales channel segmentation differentiates the aftermarket, where replacement and upgrade molds demand rapid turnaround, from original equipment manufacturing, which prioritizes long-term partnerships and engineering support for large-scale production. Finally, automation type segmentation captures the spectrum from fully automatic systems that deliver high throughput to semi-automatic and manual solutions that serve specialized, lower-volume runs, demonstrating the industry’s commitment to flexible manufacturing strategies.
This comprehensive research report categorizes the Automotive Mold market into clearly defined segments, providing a detailed analysis of emerging trends and precise revenue forecasts to support strategic decision-making.
- Mold Type
- Material Type
- Vehicle Type
- End Use
- Sales Channel
- Automation Type
Regional Dynamics Shaping the Automotive Mold Industry
The Americas region is characterized by a strong focus on local content and supply chain resilience. Manufacturers are increasingly investing in domestic tooling capacity to align with OEM localization objectives and to mitigate exposure to geopolitical uncertainties. The United States and Brazil serve as pivotal hubs, with technological collaborations and government incentives bolstering mold innovation and advanced materials research.
In Europe, Middle East & Africa, stringent regulatory standards on emissions and recycling drive continuous enhancement of molding processes. Germany, France, and Italy maintain leadership in high-precision toolmaking, leveraging Industry 4.0 capabilities and additive manufacturing for rapid prototyping. Emerging markets within the region are beginning to adopt these best practices, supported by trade agreements that facilitate the movement of specialized equipment and expertise.
Asia-Pacific stands out for its blend of cost-competitive manufacturing and rapid capacity expansion. China, India, South Korea, and Japan play substantial roles, catering to both domestic automotive growth and global export demand. Investments in automation and digitalization are accelerating, while collaborations between molders and OEM research centers are fostering region-specific material innovations that address local climate and operational requirements.
These distinct regional dynamics underscore the importance of tailored market strategies. Companies seeking to optimize their global footprint must navigate varying regulatory regimes, labor market conditions, and technological adoption rates to capitalize on regional strengths and mitigate potential barriers.
This comprehensive research report examines key regions that drive the evolution of the Automotive Mold market, offering deep insights into regional trends, growth factors, and industry developments that are influencing market performance.
- Americas
- Europe, Middle East & Africa
- Asia-Pacific
Spotlight on Leading Automotive Mold Manufacturers and Innovators
Market leaders are harnessing advanced simulation software and digital twin technology to optimize mold design, reduce cycle times, and preemptively address potential defects. By integrating real-time monitoring sensors within tooling cavities, these companies provide OEMs with actionable data that drive continuous process improvement and quality assurance.
Strategic acquisitions and joint ventures are also reshaping competitive positioning. Several top-tier mold suppliers have partnered with material technology firms to co-develop custom polymer blends that enhance component performance while simplifying mold maintenance requirements. Others have expanded their footprints through cross-border investments in automated production facilities, enabling rapid scale-up of multi-cavity injection molds for electric vehicle components.
In parallel, smaller specialists are carving out niches in high-value applications. By focusing on complex compression and transfer molds for powertrain and sensor housings, these innovators capitalize on deep technical expertise and collaborative engineering models. Their agility and customer-centric approach often complement the broader capabilities of larger firms, fostering an ecosystem of cooperative innovation.
Across the board, leading companies are prioritizing sustainable practices, from the adoption of closed-loop cooling systems to the integration of recycled resins. This dual emphasis on performance and environmental stewardship reflects the evolving expectations of OEMs and end consumers alike, setting a new benchmark for operational excellence in the automotive mold sector.
This comprehensive research report delivers an in-depth overview of the principal market players in the Automotive Mold market, evaluating their market share, strategic initiatives, and competitive positioning to illuminate the factors shaping the competitive landscape.
- Haitian International Holdings Limited
- Milacron Holdings Corp.
- Sumitomo Heavy Industries, Ltd.
- ENGEL Holding GmbH
- KraussMaffei Group GmbH
- OMG Auto Mould Pvt. Ltd.
Strategic Recommendations to Elevate Market Positioning
To navigate the evolving automotive mold landscape, manufacturers should prioritize the integration of digital process controls and predictive analytics within their production environments. By leveraging data-driven insights, companies can optimize cycle efficiency, reduce scrap rates, and deliver consistent quality that meets the stringent specifications of OEMs.
Investment in modular tooling platforms offers another avenue to accelerate time-to-market. Designing standardized core and cavity elements that can be rapidly configured for different applications enables molders to respond to shifting demand patterns and emerging vehicle architectures without incurring extensive engineering lead times.
Collaborating closely with material suppliers to co-develop specialized polymer formulations will help ensure that mold designs align with performance requirements and regulatory standards. Early-stage partnerships facilitate joint testing protocols and reduce the risk of material-induced defects during high-volume production.
Geographic expansion strategies should focus on establishing regional centers of excellence that combine local market knowledge with centralized engineering capabilities. This hybrid model enables manufacturers to serve global OEM programs efficiently while adapting rapidly to region-specific regulations and customer preferences.
Finally, embedding sustainability at the core of operational strategy-through the adoption of recycled materials, energy-efficient machinery, and waste reduction initiatives-will not only satisfy regulatory mandates but also enhance brand reputation and open new revenue streams in eco-focused market segments.
Rigorous Research Methodology Underpinning Market Analysis
The insights presented in this report are based on a multi-method research approach, combining primary interviews with key executives across mold manufacturing, material science, and vehicle OEM sectors with secondary data drawn from industry publications, regulatory filings, and patent databases. This triangulation ensures a comprehensive view of technology trends, competitive activities, and regulatory developments.
Quantitative analysis of capacity deployment, trade flows, and machinery investments was conducted using proprietary databases and validated against publicly available trade statistics. Material consumption patterns and product application breakdowns were examined to delineate segmentation trends, while tariff schedules and policy announcements were systematically analyzed to assess financial impacts.
A series of case studies illustrate real-world responses to technological shifts and regulatory pressures, highlighting best practices in automation integration, sustainability initiatives, and collaborative R&D frameworks. Peer review by in-house industry experts and third-party advisors further strengthened the findings, ensuring objectivity and rigor.
By adhering to these stringent research protocols, the report offers a reliable foundation for strategic decision-making, enabling stakeholders to anticipate market movements and craft informed investment and partnership strategies.
Explore AI-driven insights for the Automotive Mold market with ResearchAI on our online platform, providing deeper, data-backed market analysis.
Ask ResearchAI anything
World's First Innovative Al for Market Research
Consolidating Insights to Drive Future Automotive Mold Strategies
As the automotive industry accelerates toward electrification, connectivity, and sustainability, the mold sector must evolve in tandem. The convergence of high-precision tooling, advanced polymer science, and digital manufacturing platforms will dictate competitive advantage, requiring molders to balance innovation with operational discipline.
Tariff-induced cost pressures underscore the value of localized production and flexible sourcing models. At the same time, the expanding array of materials-from recycled thermoplastics to high-performance elastomers-necessitates a robust material qualification framework and agile prototype-to-production capabilities.
Regional variations in regulatory landscapes and market maturity present both challenges and opportunities. Leading mold manufacturers will be those that strategically align regional assets with centralized R&D, enabling them to deliver consistent quality at scale while adapting to local customer needs.
In summary, the future of automotive molding hinges on a holistic approach that integrates technology, material innovation, process automation, and sustainability. Companies that embrace this integrated strategy will be poised to capture growth, drive operational excellence, and shape the next generation of mobility solutions.
This section provides a structured overview of the report, outlining key chapters and topics covered for easy reference in our Automotive Mold market comprehensive research report.
- Preface
- Research Methodology
- Executive Summary
- Market Overview
- Market Dynamics
- Market Insights
- Cumulative Impact of United States Tariffs 2025
- Automotive Mold Market, by Mold Type
- Automotive Mold Market, by Material Type
- Automotive Mold Market, by Vehicle Type
- Automotive Mold Market, by End Use
- Automotive Mold Market, by Sales Channel
- Automotive Mold Market, by Automation Type
- Americas Automotive Mold Market
- Europe, Middle East & Africa Automotive Mold Market
- Asia-Pacific Automotive Mold Market
- Competitive Landscape
- ResearchAI
- ResearchStatistics
- ResearchContacts
- ResearchArticles
- Appendix
- List of Figures [Total: 28]
- List of Tables [Total: 506 ]
Take Action Now to Secure Comprehensive Market Intelligence
For a deeper exploration of automotive mold market dynamics, strategic imperatives, and competitive positioning, reach out to Ketan Rohom, Associate Director of Sales & Marketing, to access the full market research report. Leverage these insights to inform your investment decisions, optimize your product portfolio, and strengthen your market presence in an increasingly complex global landscape.
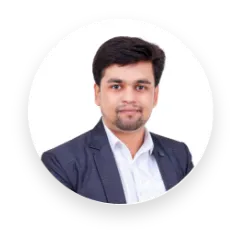
- How big is the Automotive Mold Market?
- What is the Automotive Mold Market growth?
- When do I get the report?
- In what format does this report get delivered to me?
- How long has 360iResearch been around?
- What if I have a question about your reports?
- Can I share this report with my team?
- Can I use your research in my presentation?