Introduction to the Automotive Plain Carbon Electric Resistance Welding Tubes Market
The automotive plain carbon electric resistance welding tubes market occupies a critical role in the manufacturing of modern vehicles, delivering precision, strength, and reliability in key structural and functional assemblies. These tubes, crafted from plain carbon steel and joined through electric resistance welding, serve as integral elements within chassis frames, hydraulic and pneumatic systems, and electrical conduits. As automakers pursue greater durability, enhanced energy efficiency, and reduced total cost of ownership, the demand for consistent weld quality and material performance has never been more pronounced. This executive summary provides a comprehensive overview of the latest developments shaping this niche segment, examines the transformative shifts influencing production methods and material specifications, and explores how evolving trade policies and regulatory requirements are altering the supply landscape. By integrating in-depth segmentation insights, regional dynamics, and competitive positioning, this summary equips industry decision-makers with the actionable intelligence they need to navigate complexity, anticipate challenges, and pinpoint growth opportunities within this specialized tubing sector.
Transformative Shifts Redefining the Welding Tubes Landscape
The automotive tubing landscape is undergoing transformative shifts driven by technological innovation, sustainability mandates, and new market imperatives. Automation Integration has accelerated the adoption of advanced process controls and inline nondestructive testing systems, enabling manufacturers to achieve tighter tolerances and higher throughput without compromising quality. Simultaneously, growing emphasis on corrosion resistance and temperature performance is prompting material-grade refinements that balance alloy composition and base-metal properties for optimal fatigue life. In parallel, the migration toward electrified vehicles demands tubing solutions that support both direct current welding techniques for battery enclosures and alternating current processes for high-stress structural reinforcements. Environmental regulations and safety requirements have raised the bar on quality certifications, leading to standardized compliance frameworks that streamline cross-border production. Together, these shifts underscore a market that prizes agility, precision, and sustainability. As competitive dynamics intensify, stakeholders must adopt holistic strategies that blend manufacturing excellence with rigorous safety protocols and energy-efficient designs to stay ahead in this evolving ecosystem.
Cumulative Impact of United States Tariffs in 2025 on Tubing Trade
The introduction of new United States tariffs in 2025 has produced a cumulative impact across the entire value chain of plain carbon electric resistance welding tubes. Supply costs have risen as raw material suppliers adjust pricing to reflect elevated import duties, pressuring margins for downstream tube fabricators. This environment is spurring regional reconfigurations, with many manufacturers evaluating nearshore opportunities to mitigate cross-border expenses and streamline logistics. In response, original equipment manufacturers are renegotiating long-term supply contracts, shifting toward local sourcing and tighter inventory management to preserve production continuity. Meanwhile, aftermarket suppliers and replacement markets are recalibrating price models to remain competitive while adhering to safety standards and industry certifications. The tariff ripple effect also underscores the strategic importance of process optimization, as companies leverage automation and material-efficiency initiatives to offset incremental duty burdens. This landscape demands both operational resilience and strategic foresight as industry players adapt to a higher-cost environment without sacrificing quality or compliance.
Key Segmentation Insights Across Product, Process, End Use and More
A detailed segmentation analysis reveals essential insights across seven dimensions. Based on product features, the market divides into diameter range, length variation, material grade, and wall thickness, while material grade analysis further distinguishes between specific alloy compositions and core base materials. Examining manufacturing processes highlights the role of automation integration, nuances of electric resistance welding techniques-spanning alternating current welding and direct current welding-and the deployment of quality control systems that include advanced nondestructive testing protocols. End use application segmentation spans chassis and frame components, electrical systems, hydraulic and pneumatic assemblies, and structural reinforcement elements critical to vehicle integrity. Performance characteristics segmentation emphasizes corrosion resistance, overall durability, energy efficiency-distinguishing between operational efficiency and thermal efficiency-and temperature resistance capabilities under harsh conditions. Industry adoption lenses highlight sourcing patterns among aftermarket suppliers, original equipment manufacturers, and replacement markets. Finally, investment and cost structure considerations explore capital expenditure commitments, cost efficiency improvements driven by material efficiency and process optimization, and ongoing operational costs. Regulatory compliance and safety criteria encapsulate automotive industry standards, ISO certifications, material handling safety, and welding-specific safety requirements.
This comprehensive research report categorizes the Automotive Plain Carbon Electric Resistance Welding Tubes market into clearly defined segments, providing a detailed analysis of emerging trends and precise revenue forecasts to support strategic decision-making.
- Product Features
- Manufacturing Process
- End Use Application
- Performance Characteristics
- Industry Adoption
- Investment And Cost Structure
- Regulatory Compliance And Safety
Critical Regional Insights Driving Growth across Global Markets
Regional dynamics in the plain carbon electric resistance welding tubes sector reveal divergent drivers and opportunities across the Americas, Europe, Middle East & Africa, and Asia-Pacific. In the Americas, emphasis on lightweighting and structural optimization is prompting increased demand for high-precision tube configurations, supported by robust OEM networks and aftermarket channels. Europe, the Middle East & Africa stand out for stringent environmental regulations that elevate demand for corrosion-resistant and energy-efficient solutions, while regulatory certifications drive harmonization across national markets. In Asia-Pacific, surging production volumes and an expanding electric vehicle segment are fueling investments in automated welding processes and quality control systems to meet both domestic and export requirements. Each region’s unique policy landscape, infrastructure maturity, and industrial ecosystem shape strategic priorities-from material-grade innovation in one geography to cost-driven process enhancements in another. Harmonizing these regional insights allows market participants to tailor product portfolios, partnership models, and capital deployments to local needs while maintaining global operational agility.
This comprehensive research report examines key regions that drive the evolution of the Automotive Plain Carbon Electric Resistance Welding Tubes market, offering deep insights into regional trends, growth factors, and industry developments that are influencing market performance.
- Americas
- Asia-Pacific
- Europe, Middle East & Africa
Prominent Company Strategies Shaping Competitive Dynamics
Competitive dynamics in this specialized tubing market are defined by an array of established leaders and agile challengers. Accord Carbon Technologies Inc., Alpha Auto Tubing Inc., Beta Weldings Ltd., Brisk Welding Tubes Corporation and Carbotech Enterprises LLC continue to invest in process automation and material innovation to maintain technical leadership. Crest Auto Solutions LLC, Delta Resistance Weld Systems Incorporated and Dynamo Resistance Tubing Ltd. differentiate through customized engineering services and rapid prototyping capabilities. Elite Weld Tube Solutions Inc., Epsilon Weld Tubes Corporation, Fusion Automotive Products Inc. and Giga Resistance Welding Tubes Ltd. emphasize lean manufacturing and localized supply agreements to optimize cost structure and lead times. Helix Welding Tube Systems LLC, Innovative Carbon Solutions Inc., Jolt Resistance Welding Inc. and Kinetic Tubing Technologies LLC excel at integrating upstream alloy refinement with downstream forming processes. Lumina Automation Supply Co., Magnus Resistance Innovations Inc., Meridian Carbon Fab Corp. and NexGen Welding Solutions LLC leverage digital quality control platforms to deliver certified compliance records. Omega Tubing Industries Ltd., Pinnacle Carbon Weld Inc., Precise Weld Components LLC and Quantum Resistance Tubing Co. focus on strategic partnerships with OEMs, while Razor Welding Technologies Corporation, SteelCore Tubing Solutions Inc., Synergy Auto Weld Systems Inc. and Titan Tube & Resistance Manufacturing LLC drive volume through aftermarket and replacement channels. Ultra Weld Tubes Ltd., Universal Automotive Tubes Ltd., Vanguard Carbon Tubing Corporation and Visage Tubing Technologies Inc. invest heavily in research collaborations, and Wave Resistance Weld Co., WeldMaster Carbon Technologies LLC, Xenon Automotive Tubing Enterprises LLC, Xpert Weld Tube Solutions Inc., Yield Resistance Welding Systems Inc., Zenith Tube Solutions Ltd. and Zeno Carbon Weld Components Ltd. round out a competitive field defined by innovation, customization and supply-chain resilience.
This comprehensive research report delivers an in-depth overview of the principal market players in the Automotive Plain Carbon Electric Resistance Welding Tubes market, evaluating their market share, strategic initiatives, and competitive positioning to illuminate the factors shaping the competitive landscape.
- Accord Carbon Technologies Inc.
- Alpha Auto Tubing Inc.
- Beta Weldings Ltd.
- Brisk Welding Tubes Corporation
- Carbotech Enterprises LLC
- Crest Auto Solutions LLC
- Delta Resistance Weld Systems Incorporated
- Dynamo Resistance Tubing Ltd.
- Elite Weld Tube Solutions Inc.
- Epsilon Weld Tubes Corporation
- Fusion Automotive Products Inc.
- Giga Resistance Welding Tubes Ltd.
- Helix Welding Tube Systems LLC
- Innovative Carbon Solutions Inc.
- Jolt Resistance Welding Inc.
- Kinetic Tubing Technologies LLC
- Lumina Automation Supply Co.
- Magnus Resistance Innovations Inc.
- Meridian Carbon Fab Corp.
- NexGen Welding Solutions LLC
- Omega Tubing Industries Ltd.
- Pinnacle Carbon Weld Inc.
- Precise Weld Components LLC
- Quantum Resistance Tubing Co.
- Razor Welding Technologies Corporation
- SteelCore Tubing Solutions Inc.
- Synergy Auto Weld Systems Inc.
- Titan Tube & Resistance Manufacturing LLC
- Ultra Weld Tubes Ltd.
- Universal Automotive Tubes Ltd.
- Vanguard Carbon Tubing Corporation
- Visage Tubing Technologies Inc.
- Wave Resistance Weld Co.
- WeldMaster Carbon Technologies LLC
- Xenon Automotive Tubing Enterprises LLC
- Xpert Weld Tube Solutions Inc.
- Yield Resistance Welding Systems Inc.
- Zenith Tube Solutions Ltd.
- Zeno Carbon Weld Components Ltd.
Actionable Recommendations for Industry Leaders to Navigate Change
To thrive amid these shifts, industry leaders should prioritize targeted investments and strategic initiatives. First, enhancing automation integration and nondestructive testing capabilities will ensure consistent weld integrity and reduce scrap rates. Second, developing advanced corrosion-resistant and temperature-resistant formulations can address emerging performance requirements in electric and hybrid powertrain modules. Third, fostering flexible manufacturing cells that accommodate both alternating current and direct current welding processes will enable rapid adaptation to diverse end-use applications. Fourth, engaging with regulatory bodies to influence safety standards and streamline certification workflows can accelerate product introductions. Fifth, optimizing material utilization through process refinements and alloy selection can mitigate cost pressures, especially in high-tariff environments. Sixth, building collaborative partnerships with original equipment manufacturers and aftermarket suppliers will secure long-term supply agreements and enable co-development of next-generation tubing solutions. Collectively, these recommendations offer a roadmap for sustaining profitability, driving innovation and reinforcing competitive differentiation.
Explore AI-driven insights for the Automotive Plain Carbon Electric Resistance Welding Tubes market with ResearchAI on our online platform, providing deeper, data-backed market analysis.
Ask ResearchAI anything
World's First Innovative Al for Market Research
Conclusion and Outlook on the Welding Tubes Sector
In summary, the plain carbon electric resistance welding tubes market stands at a pivotal juncture, shaped by technological breakthroughs, evolving regulatory landscapes and shifting trade policies. Manufacturers who embrace segmentation-driven strategies-applying precise control over diameter, wall thickness, material grade and performance attributes-will unlock efficiency gains and deliver tailored solutions across diverse automotive applications. At the same time, regional insights underscore the importance of aligning development roadmaps with local regulatory regimes and end-use demands. Competitive success will hinge on the ability to integrate end-to-end quality control, sustain cost-efficient operations in light of tariff pressures and cultivate strategic partnerships across the supply chain. By synthesizing these factors into a coherent business approach, companies can position themselves for sustained growth and resilience against market volatility.
This section provides a structured overview of the report, outlining key chapters and topics covered for easy reference in our Automotive Plain Carbon Electric Resistance Welding Tubes market comprehensive research report.
- Preface
- Research Methodology
- Executive Summary
- Market Overview
- Market Dynamics
- Market Insights
- Cumulative Impact of United States Tariffs 2025
- Automotive Plain Carbon Electric Resistance Welding Tubes Market, by Product Features
- Automotive Plain Carbon Electric Resistance Welding Tubes Market, by Manufacturing Process
- Automotive Plain Carbon Electric Resistance Welding Tubes Market, by End Use Application
- Automotive Plain Carbon Electric Resistance Welding Tubes Market, by Performance Characteristics
- Automotive Plain Carbon Electric Resistance Welding Tubes Market, by Industry Adoption
- Automotive Plain Carbon Electric Resistance Welding Tubes Market, by Investment And Cost Structure
- Automotive Plain Carbon Electric Resistance Welding Tubes Market, by Regulatory Compliance And Safety
- Americas Automotive Plain Carbon Electric Resistance Welding Tubes Market
- Asia-Pacific Automotive Plain Carbon Electric Resistance Welding Tubes Market
- Europe, Middle East & Africa Automotive Plain Carbon Electric Resistance Welding Tubes Market
- Competitive Landscape
- ResearchAI
- ResearchStatistics
- ResearchContacts
- ResearchArticles
- Appendix
- List of Figures [Total: 30]
- List of Tables [Total: 635 ]
Call to Action: Engage with Our Expert, Ketan Rohom, for In-Depth Analysis
To gain deeper insights and actionable guidance, reach out to Ketan Rohom, Associate Director, Sales & Marketing, for tailored consulting on this market research report. Ketan can help you leverage the findings, refine your strategic roadmap and secure a competitive edge in the automotive tubing arena. Contact Ketan today to explore how these insights can drive your next phase of growth and innovation.
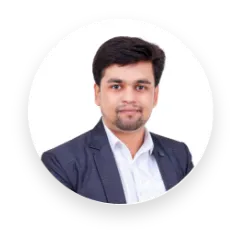
- When do I get the report?
- In what format does this report get delivered to me?
- How long has 360iResearch been around?
- What if I have a question about your reports?
- Can I share this report with my team?
- Can I use your research in my presentation?