The Automotive Plastic Compounding Market size was estimated at USD 17.82 billion in 2024 and expected to reach USD 19.13 billion in 2025, at a CAGR 7.24% to reach USD 27.11 billion by 2030.
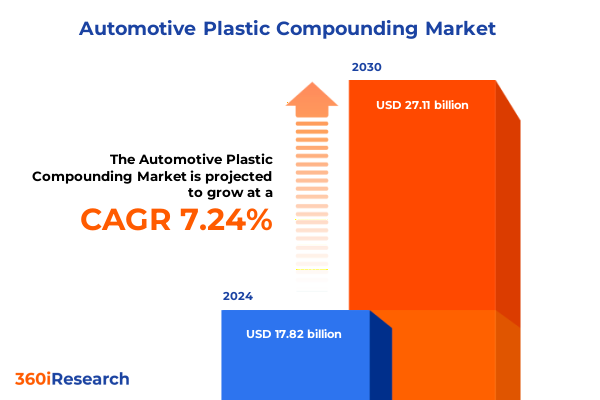
Defining the Role of Plastic Compounding in Automotive Innovation
The automotive plastic compounding industry sits at the intersection of advanced materials engineering and relentless innovation, playing a pivotal role in the evolution of modern vehicles. As manufacturers strive to reduce weight, improve fuel efficiency, and meet increasingly stringent regulatory requirements, compounders have emerged as vital partners in delivering tailored polymer blends that balance performance, cost, and sustainability.
Over the past decade, the adoption of engineered plastics has shifted from niche applications to mainstream vehicle architectures. Exterior body panels and bumpers benefit from high-impact resistance compounds, while interior dashboards and door panels demand materials with superior aesthetics and durability. Under-the-hood components such as air intake boxes and engine covers require thermal stability and chemical resistance that only specialized compounding formulations can provide.
This introduction frames the strategic importance of plastic compounding within broader automotive trends. Rapid advancements in electric powertrains, the push toward lightweighting, and the rise of autonomous vehicle platforms have elevated material selection to a critical competitive differentiator. Industry stakeholders must navigate a complex landscape of application requirements, material innovations, and geopolitical headwinds to capitalize on growth opportunities. By understanding these dynamics, decision-makers can align their product roadmaps, sourcing strategies, and investment priorities with the trajectory of the market.
Navigating Emerging Forces Reshaping Plastic Compounding in Vehicles
The automotive landscape is undergoing transformative shifts driven by the electrification of powertrains, heightened environmental regulations, and evolving consumer expectations. Electrified vehicles demand lighter constructions to offset the weight of battery systems, compelling OEMs and tier-one suppliers to explore advanced polymer blends with high strength-to-weight ratios. The integration of polyamide or polypropylene compounds reinforced with glass fibers has become a cornerstone of lightweighting strategies, replacing steel and aluminum in non-structural applications.
Sustainability has also emerged as a defining force reshaping material selection. Circular economy principles push compounding partners to scale up recycled resin content without compromising performance. Innovations in compatibilizers and additive packages enable the use of post-industrial and post-consumer polyethylene and polyvinyl chloride streams within demanding automotive interiors. At the same time, regulatory bodies around the globe are tightening emission standards and mandating bio-based content in polymers, accelerating research into next-generation biopolymers and eco-friendly processing aids.
Technological breakthroughs in digital twin modeling, simulation, and in-line quality monitoring are optimizing the design and production of compounded resins. Manufacturers leverage predictive analytics to fine-tune rheological properties based on application requirements, reducing trial-and-error cycles and time-to-market. Partnerships between material formulators, OEMs, and equipment suppliers are becoming more collaborative, fostering co-development of customized solutions that address noise, vibration, and harshness targets while upholding crashworthiness criteria.
Taken together, these transformative shifts underscore a new era where materials engineering, environmental stewardship, and digital innovation converge to define competitive advantage in automotive plastic compounding.
Assessing the Ripple Effects of US Tariffs on Plastic Compounds in 2025
The introduction of heightened US tariffs slated for 2025 will send ripple effects across the global plastic compounding supply chain. Import levies on key polymer feedstocks such as acrylonitrile butadiene styrene and polypropylene are poised to elevate production costs for domestic compounders, compelling many to reassess their sourcing strategies. Those dependent on cost-effective resin supplies from Asia or Europe may face immediate margin compression unless cost pass-through is accepted by automotive customers.
In response, select compounders are evaluating onshore polymerization capacities or diversifying raw material portfolios to include more domestically produced resins. At the same time, forward-thinking players are negotiating long-term supply agreements and investing in backward integration to shield themselves from tariff volatility. These moves not only offer cost stability but also enhance supply security, a factor increasingly prized by OEMs under pressure to maintain uninterrupted production.
On the demand side, tier-one suppliers and automakers are recalibrating their cost models to account for potential material surcharges. Contract negotiations now feature more rigorous price escalation clauses, tying resin costs to benchmark indices. In certain high-volume programs, stakeholders are exploring material substitutions, shifting from higher-cost engineered resins to more economical alternatives in less critical segments.
Ultimately, the cumulative impact of US tariffs will favor compounders that proactively manage feedstock risks, leverage strategic partnerships, and maintain operational agility. Those who fail to adapt may struggle to compete on both price and performance, underscoring the imperative for dynamic supply chain models in the face of evolving trade policies.
Unveiling Market Dynamics Through Application, Material, Vehicle and Process Lenses
Analyzing the market through the prism of automotive application reveals distinct growth trajectories for exterior components, interior modules, and under-the-hood parts. Body panels, bumpers, and grilles drive demand for high-impact resins capable of withstanding regulatory crash tests while maintaining surface quality. Dashboard and instrument panel compounds prioritize flame retardancy and low volatile organic compound emissions, whereas door panels and seats require materials that balance tactile comfort with wear resistance. In the engine bay, air intake boxes and engine covers depend on thermally stable blends that resist chemical degradation throughout the vehicle’s service life.
Material segmentation uncovers a steady gravitation toward polypropylene and acrylonitrile butadiene styrene, valued for their versatility across multiple applications. Polyethylene remains a cost-effective choice for certain under-the-hood parts but faces gradual displacement in high-performance segments by engineered polyamides. Polyvinyl chloride maintains a niche in interior trim due to its superior weatherability and dyeability, though regulatory scrutiny of additive packages drives ongoing reformulation efforts.
Vehicle type serves as another lens into demand patterns. Passenger vehicles account for the lion’s share of compound consumption, reflecting the broad proliferation of comfort and safety features in mass-market sedans and SUVs. Light commercial vehicles exhibit growing appetite for reinforced polypropylene blends that support payload requirements without sacrificing corrosion resistance. Heavy commercial vehicles adopt polyamide-based compounds in critical systems where mechanical robustness under heavy loads and extreme temperatures is non-negotiable.
When viewed by compounding type, the recycled resin segment is gaining traction through mandated recycled content targets and sustainability commitments among OEMs. Virgin resin compounding remains dominant in safety-critical and performance-sensitive applications, but hybrid formulations that merge recycled and virgin polymers are emerging as a compromise. Process segmentation casts light on production methods: blow molding furthers the manufacture of hollow structures such as fluid reservoirs, extrusion covers cable sheathing, and injection molding continues to reign supreme for complex geometries in both interior and exterior components.
This multifaceted segmentation narrative underscores the nuanced interplay of application requirements, material science, vehicle characteristics, recyclability goals, and processing technologies that shape the competitive arena of automotive plastic compounding.
This comprehensive research report categorizes the Automotive Plastic Compounding market into clearly defined segments, providing a detailed analysis of emerging trends and precise revenue forecasts to support strategic decision-making.
- Application
- Material
- Vehicle Type
- Compounding Type
- Process
Regional Performance Drivers Across Americas EMEA and Asia-Pacific
Examining regional dynamics highlights divergent growth drivers and strategic considerations across global markets. In the Americas, rising consumer demand for SUVs and pickup trucks amplifies the need for lightweight exterior body panels and high-strength under-the-hood components. Local environmental mandates also catalyze the incorporation of recycled polymer content, prompting suppliers to expand closed-loop recycling initiatives and bolster domestic compounding capacities.
Across Europe, Middle East & Africa, stringent CO2 emission targets and a rapid transition to electric mobility underpin sustained demand for advanced polymer blends in battery enclosures, thermal management systems, and structural reinforcements. The European Union’s emerging directives on polymer recyclability and chemical safety have spurred innovation in bio-based compatibilizers and solvent-free processing aids, setting new benchmarks for sustainable material performance.
In Asia-Pacific, burgeoning vehicle production in emerging economies coexists with mature automotive hubs in Japan and South Korea. This duality fosters both volume-driven demand for cost-effective polypropylene and ABS compounds, as well as premium requirements for high-temperature polyamide and engineered blends in luxury segments. Regional trade agreements and local content regulations also influence supply chain design, prompting key compounders to establish joint ventures and greenfield plants to meet domestic sourcing rules and expedite delivery timelines.
This comprehensive research report examines key regions that drive the evolution of the Automotive Plastic Compounding market, offering deep insights into regional trends, growth factors, and industry developments that are influencing market performance.
- Americas
- Europe, Middle East & Africa
- Asia-Pacific
Profiling Leading Innovators and Strategic Collaborators in Plastic Compounding
Leading the charge in the automotive plastic compounding sector, a cadre of global material specialists and regional innovators has forged competitive advantage through technology, scale, and strategic alliances. Major polysynthetic producers have leveraged integrated polymerization-to-compounding platforms to secure feedstock supply while exerting granular control over resin properties. Strategic acquisitions of sustainable technology startups have further bolstered their portfolios with next-generation compatibilizers and bio-based additives.
At the same time, midsized compounders have carved niches by offering rapid prototyping, bespoke color matching, and localized technical support tailored to complex vehicle programs. Partnerships with OEM engineering teams accelerate co-development cycles, ensuring that compound formulations seamlessly integrate with vehicle assembly processes and compliance protocols. Several regional players in Asia-Pacific have capitalized on cost arbitrage and government incentives, emerging as key suppliers to both domestic and export markets.
Innovation remains a defining hallmark of competitive differentiation. Collaborations focused on additive manufacturing, in-die foaming, and reactive extrusion have unlocked novel material architectures. These advances not only improve crash performance and acoustic damping but also streamline downstream processes by reducing part count and assembly complexity.
As consolidation continues and R&D investments intensify, companies that couple deep application expertise with agile process innovation are best positioned to capture the next wave of growth in automotive plastic compounding.
This comprehensive research report delivers an in-depth overview of the principal market players in the Automotive Plastic Compounding market, evaluating their market share, strategic initiatives, and competitive positioning to illuminate the factors shaping the competitive landscape.
- Saudi Basic Industries Corporation
- BASF SE
- Celanese Corporation
- LyondellBasell Industries N.V.
- LANXESS AG
- Covestro AG
- Solvay S.A.
- Evonik Industries AG
- DuPont de Nemours, Inc.
- Avient Corporation
Strategic Imperatives for Manufacturers to Thrive in a Changing Market
Manufacturers must prioritize vertical integration to mitigate raw material volatility. Securing long-term feedstock agreements and investing in on-site polymerization facilities will provide cost stability and supply agility in the face of tariff fluctuations and geopolitical uncertainty. Embracing modular compounding lines equipped with in-line rheometry and spectral analysis will accelerate product validation and reduce time-to-market for new resin formulations.
Sustainability targets should extend beyond recycled content percentages to encompass cradle-to-grave lifecycle assessments. Incorporating bio-based monomers, solvent-free process aids, and closed-loop material recovery programs will not only meet regulatory demands but also resonate with environmentally conscious consumers. Transparent reporting of carbon footprints and recyclability metrics can form the basis for value-added partnerships with OEMs pursuing circular economy objectives.
Cultivating deeper collaboration with vehicle manufacturers is another imperative. Embedding compounders within early-stage vehicle and platform design teams ensures that material solutions align with structural, thermal, and aesthetic requirements from inception. Co-innovation agreements coupled with shared simulation platforms will streamline design iterations and enable rapid adaptations to changing program specifications.
Geographical diversification of production assets will also prove critical. Establishing compounding facilities in emerging markets under favorable trade agreements and cost structures will serve local content mandates and hedge against regional disruptions. By balancing central R&D hubs with decentralized manufacturing footprints, industry leaders can deliver globally consistent quality while remaining responsive to regional market nuances.
Rigorous Multi-Source Approach Underpinning Market Insights
This report is built upon a rigorous methodology combining primary expert interviews, exhaustive secondary research, and quantitative data analysis. Primary engagements encompass in-depth discussions with material scientists, supply chain executives, and OEM procurement leaders to validate market drivers, technical trends, and strategic imperatives. Secondary sources include industry journals, regulatory filings, patent databases, and corporate disclosures.
Data points are triangulated across multiple sources to ensure accuracy and mitigate bias. Market intelligence is further enriched by on-site facility visits and process audits at key compounding plants. Analytical frameworks leverage scenario modeling and sensitivity analyses to capture the impact of trade policies, raw material price volatility, and regional regulatory shifts.
Quality assurance protocols involve peer review by cross-functional experts, including chemical engineers, automotive designers, and sustainability specialists. All findings are subjected to consistency checks against historical trends and benchmark comparisons. The final report synthesizes these insights into a coherent narrative, providing stakeholders with validated, actionable intelligence.
Explore AI-driven insights for the Automotive Plastic Compounding market with ResearchAI on our online platform, providing deeper, data-backed market analysis.
Ask ResearchAI anything
World's First Innovative Al for Market Research
Synthesizing Key Takeaways to Chart Future Growth Pathways
The automotive plastic compounding sector stands at a pivotal juncture defined by material innovation, regulatory pressure, and supply chain realignment. Advanced polymer blends are no longer mere cost-saving substitutes but integral enablers of vehicle performance, safety, and sustainability. Navigating emerging tariff regimes, meeting stringent recycled content targets, and responding to divergent regional dynamics will distinguish market leaders from laggards.
Segmentation analysis reinforces that tailored strategies across application areas-from crash-worthy exterior panels to thermally stable under-the-hood components-are essential. Material selection must balance the competing imperatives of performance, cost, and environmental impact, while process technologies must deliver both precision and scale. Companies that embed themselves early in vehicle design processes and invest in circular economy solutions will capture disproportionate value as the industry transitions.
Looking ahead, the confluence of electrification, digitalization, and sustainability will continue to raise the bar for polymer performance and supply chain resilience. Stakeholders who act decisively-integrating forward-looking R&D, strategic partnerships, and dynamic sourcing models-will be best equipped to capitalize on the next wave of automotive transformation.
This section provides a structured overview of the report, outlining key chapters and topics covered for easy reference in our Automotive Plastic Compounding market comprehensive research report.
- Preface
- Research Methodology
- Executive Summary
- Market Overview
- Market Dynamics
- Market Insights
- Cumulative Impact of United States Tariffs 2025
- Automotive Plastic Compounding Market, by Application
- Automotive Plastic Compounding Market, by Material
- Automotive Plastic Compounding Market, by Vehicle Type
- Automotive Plastic Compounding Market, by Compounding Type
- Automotive Plastic Compounding Market, by Process
- Americas Automotive Plastic Compounding Market
- Europe, Middle East & Africa Automotive Plastic Compounding Market
- Asia-Pacific Automotive Plastic Compounding Market
- Competitive Landscape
- ResearchAI
- ResearchStatistics
- ResearchContacts
- ResearchArticles
- Appendix
- List of Figures [Total: 26]
- List of Tables [Total: 370 ]
Engage with Ketan Rohom to Secure the Comprehensive Market Report
For a tailored walkthrough of these insights and to secure the full market research report, reach out directly to Ketan Rohom, Associate Director, Sales & Marketing. Gain exclusive access to granular data, in-depth analyses, and strategic frameworks designed to empower your decision-making and drive growth in the automotive plastic compounding arena.
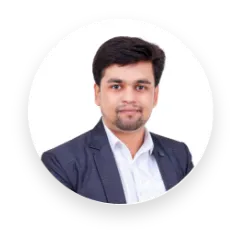
- How big is the Automotive Plastic Compounding Market?
- What is the Automotive Plastic Compounding Market growth?
- When do I get the report?
- In what format does this report get delivered to me?
- How long has 360iResearch been around?
- What if I have a question about your reports?
- Can I share this report with my team?
- Can I use your research in my presentation?