The Automotive Stamping Dies & Parts Market size was estimated at USD 18.43 billion in 2024 and expected to reach USD 19.41 billion in 2025, at a CAGR 5.40% to reach USD 25.28 billion by 2030.

A concise orientation to the complex and evolving world of automotive stamping dies and parts that frames supply chain, technology, and strategic sourcing considerations
The automotive stamping dies and parts sector sits at the intersection of materials science, precision engineering, and global supply chain optimization, and this report offers an authoritative orientation for executives navigating rapid change. The industry supports vehicle manufacture across powertrain, body, chassis, interior, and emerging electrified subsystems, with processes spanning cold, warm, and hot stamping and a range of press types that determine cycle times and part complexity. As automakers prioritize lightweighting, emission reduction, and manufacturability, the role of stamping specialists has expanded beyond single-die suppliers toward integrated partners that deliver design for manufacture, tool maintenance strategies, and just-in-time capacity scaling.
Consequently, decision-makers must view stamping as both a cost center and a strategic enabler. Advances in material blending, high-strength steels and multi-material joining, and the growing requirements for EV enclosures and busbars have shifted engineering priorities and supplier relationships. This introduction frames the subsequent sections by highlighting how technological evolution, trade policy, and segmentation dynamics converge to reshape sourcing, investment, and risk management across the stamping value chain.
How electrification, lightweighting, and advanced press technologies are reshaping supplier capabilities, investment priorities, and production economics
The landscape for stamping dies and parts has undergone transformative shifts driven by electrification, materials innovation, and manufacturing automation, and these forces are now accelerating supplier consolidation and capability specialization. Electrified powertrains and battery systems have created new demand pathways for components such as battery enclosures, busbars, and motor laminations, prompting existing stamping houses to add precision forming and higher-tolerance dies to their portfolios. At the same time, lightweighting imperatives push engineers to substitute traditional steel with aluminum alloys from the 5xxx, 6xxx, and 7xxx series, or to adopt coated blanks that meet corrosion and joining requirements while enabling complex stamping geometries.
Process-level change is equally significant: hot stamping and advanced warm forming are being deployed to produce structural components with tailored properties, while servo and transfer presses enable higher throughput for progressive and tandem dies with lower scrap rates. Maintenance paradigms are shifting toward predictive and condition-based regimes to protect capital-intensive dies and presses, and service providers are monetizing retrofit and repair cycles. Taken together, these shifts are realigning customer-supplier contracts, redefining capital allocation for press lines across 201–600 tons and above, and elevating the strategic value of stamping capabilities as OEMs and tier suppliers reconfigure platforms for mixed-material architectures.
Assessment of how the 2025 expansion and enforcement of steel and aluminum tariff measures have altered sourcing economics, compliance obligations, and strategic investment decisions
Changes to U.S. trade policy in 2025 have imposed material and pricing shocks across the stamping ecosystem and are now a central factor in sourcing and make-or-buy calculus. Executive-level trade actions enacted in 2025 expanded the scope of Section 232 measures and related proclamations to cover a broader set of steel and aluminum articles and their derivative products, and the effective rates and dates of those measures are explicitly laid out in presidential proclamations and accompanying fact sheets. These policy steps altered the underlying cost base for imported sheet and downstream stampings, necessitating rapid reassessment of supplier footprints, inventory strategies, and domestic sourcing options.
The practical effects for stamping suppliers include immediate pressure on margins where imported coated blanks or specialty aluminum were previously used, and increased incentives to qualify domestic material sources or vertically integrate rolling and blanking capabilities. The proclamations that became effective in March and June 2025 also introduced stricter “melted and poured” rules, expanded the tariffable product lists to include derivative articles, and set effective dates for higher ad valorem duties that impact both raw sheet and assemblies containing steel or aluminum inputs. For procurement and commercial teams, this has translated into renewed urgency to negotiate long-term supply contracts, to redesign parts for domestically available alloys or coated blanks, and to accelerate tool and die localization to mitigate duty exposure.
Strategically, these trade changes are producing both constriction and opportunity. Short-term, buyers face cost inflation and potential delivery disruptions as suppliers respond to reclassification risk and increased customs scrutiny. Mid-term, however, there is a material incentive to redeploy capital into domestic blanking, roll forming, and higher-capacity press lines, which can secure lower landed costs over multiyear sourcing cycles and reduce exposure to tariff volatility. Suppliers and OEM sourcing teams that invest in compliance, tariff engineering, and alternative material qualification programs will better protect earnings while capturing share where competitors are slower to adapt.
How a multi-dimensional segmentation framework linking product, material, process, press class, application and end-user channels reveals where engineering constraints align with commercial opportunity
Segmentation provides the analytical scaffolding necessary to translate market complexity into targeted product, material, and service strategies, and a careful reading of product categories, materials, processes, and customer applications reveals where margins, risk and growth converge. The product-category framework differentiates worked metal from the tooling that produces it by separating stamped parts-spanning body panels, EV and e-mobility components such as battery enclosures, busbars and motor laminations, exhaust components including converter shells and muffler shells, fasteners and small brackets, interior and safety parts like airbag housings and seat structures, powertrain and thermal stampings such as engine brackets and heat shields, and structural and chassis pieces like crossmembers and suspension stampings-from the full taxonomy of stamping dies which ranges from progressive, compound, and tandem line dies to fine blanking, hot stamping, prototype soft dies and trim and pierce tooling. This distinction matters because capital intensity, lifecycle, and aftermarket service models differ dramatically across part classes.
Material-type segmentation isolates aluminum in both cast and wrought forms, coated blanks including Al-Si, galvanized and galvannealed variants, copper for electrical and thermal pathways, and steel varieties split across carbon and stainless categories. Sheet-material granularity further divides aluminum into 5xxx, 6xxx and 7xxx series and steel into AHSS, HSLA, mild, stainless and UHSS grades, each presenting unique formability, springback and joining challenges that drive die design and press selection. Process and press-level segmentation clarifies capability requirements: cold, warm and hot stamping govern achievable microstructure and mechanical properties, while press-type segmentation-covering high-speed, mechanical, hydraulic, servo and transfer presses-determines cycle time, accuracy and permissible tonnage classes from sub-200-ton platforms up to presses exceeding 1,200 tons. Service and aftermarket segmentation recognizes the importance of maintenance, repair, and retrofit offerings, with predictive and preventive maintenance regimes emerging as commercial levers to extend die life and reduce unplanned downtime. Application and vehicle-type segmentation tie all of these dimensions to end markets; chassis, engine, exterior body panels such as doors and hoods, and interior components have distinct tolerances and volume profiles, while vehicle-type end users span passenger cars and SUVs, light and heavy commercial vehicles, and off-highway specialty segments in agriculture, construction and military applications. Finally, end-user distinction between OEM and aftermarket channels highlights divergent contracting, warranty exposures and customization demands. Together, the segmentation schema guides product development roadmaps, capital planning and go-to-market choices by linking engineering constraints to commercial outcomes.
This comprehensive research report categorizes the Automotive Stamping Dies & Parts market into clearly defined segments, providing a detailed analysis of emerging trends and precise revenue forecasts to support strategic decision-making.
- Product Category
- Material Type
- Service Type
- Process Type
- Sheet Material
- Tonnage Class
- Press Type
- Application
- Vehicle Type
- End User
Regional competitive dynamics and capability concentrations across the Americas, EMEA, and Asia-Pacific that dictate sourcing footprints, aftermarket strategies and localization priorities
Regional dynamics remain a critical determinant of investment decisions for suppliers and OEMs, and the Americas, Europe-Middle East-Africa, and Asia-Pacific each present distinct advantages and structural challenges that shape strategy. In the Americas, proximity to major North American OEMs, established blanking and rolling capacity, and a resurgence in reshoring driven by tariff exposure and prioritization of domestic content create favorable conditions for nearshoring and capacity expansion, particularly for structural stampings and high-tonnage presses. Supply chains in this region are adapting to stricter trade enforcement by prioritizing “melted and poured” traceability and by investing in tooling and blanking assets that shorten lead times and reduce duty risk.
Europe, the Middle East and Africa continue to emphasize advanced materials and high-precision manufacturing, and regulatory pressures around emissions and recyclability push suppliers toward coated blanks and advanced steels that meet lifecycle and crashworthiness requirements. Investments in automation and advanced process control are prevalent in high-cost labor jurisdictions to preserve competitiveness. Asia-Pacific remains the dominant volume center for blanking, progressive dies and medium-tonnage press capacity, and it is also the fastest adopter of specialized EV component production such as busbars and battery casings. For global players, the regional mix implies a hybrid footprint: maintain agile, high-precision centers close to OEM engineering hubs while leveraging scale manufacturing in Asia-Pacific for standardized, high-volume components.
This comprehensive research report examines key regions that drive the evolution of the Automotive Stamping Dies & Parts market, offering deep insights into regional trends, growth factors, and industry developments that are influencing market performance.
- Americas
- Europe, Middle East & Africa
- Asia-Pacific
Competitive moves and capability investments among die makers and stampers that reveal which suppliers are positioning for scale, material expertise, or differentiated service offerings
Company-level activity in the stamping and dies domain is characterized by three overlapping trends: capability consolidation, targeted investments in high-value EV and structural components, and service differentiation through maintenance and retrofit offerings. Leading suppliers are expanding into adjacent capabilities such as blanking, roll forming, and assembly to capture more of the bill of materials and to offer just-in-time supply to OEM lines. Concurrently, several suppliers are selectively investing in hot-stamping and fine-blanking capacity to serve chassis and safety-critical parts that require tailored mechanical properties and tight dimensional control.
Strategic partnerships between die makers and material producers, as well as joint ventures with regional fabricators, are increasingly common as a way to accelerate qualification cycles for coated blanks and specialty aluminum alloys. Firms that offer predictive maintenance, in-house tool refurbishment, and retrofit engineering are capturing aftermarket revenue while differentiating on uptime guarantees and warranty transferability. For buyers, the consequence is a clearer segmentation of potential partners: those that compete primarily on cost and scale, those that compete on technological capability and material expertise, and those that compete on integrated services and lifecycle support.
This comprehensive research report delivers an in-depth overview of the principal market players in the Automotive Stamping Dies & Parts market, evaluating their market share, strategic initiatives, and competitive positioning to illuminate the factors shaping the competitive landscape.
- Bharat Forge Limited
- Boker’s, Inc.
- Toyota Motor Corporation
- Reich Tool & Design, Inc.
- Aisin Seiki Co., Ltd.
- Auto Component Manufacturers Association of India
- Altair Engineering Inc.
- Autokiniton US Holdings, Inc.
- D&H Industries, Inc.
- DENSO Corporation
- F-tech Inc.
- GESTAMP SERVICIOS, S.A.
- Interplex Holdings Pte. Ltd.
- JBM Group
- KIRCHHOFF Automotive SE
- KTH Parts Industries Inc.
- LISI Automotive SAS
- Magna International Inc.
- Nippon Steel Corporation
- Proterial, Ltd.
- Thyssenkrupp AG
- Schuler Group GmbH
- Keats Manufacturing Co., Inc.
- WALKER TOOL & DIE, Inc.
- Tooling Systems Group, Inc.
Practical recommendations for executives to harden supply chains, accelerate material qualification, and convert maintenance capabilities into recurring revenue streams
Actionable recommendations for leaders in stamping and parts should prioritize interventions that reduce exposure to trade volatility, accelerate qualification of emerging materials, and monetize die maintenance and retrofit services. Operationally, companies should adopt tariff engineering and product redesign as part of commercial negotiations to preserve margin while materials and logistics costs fluctuate. Concurrently, accelerating qualification programs for aluminum 5xxx–7xxx alloys, galvannealed and Al-Si coated blanks, and electrical-grade copper stampings will shorten the path to supply chain resiliency and broaden options for sourcing components closer to assembly lines.
On the capital side, owners should re-evaluate press portfolios across tonnage classes and consider adding servo and transfer press capacity for flexible high-mix low- to mid-volume production while preserving mechanical or hydraulic lines for high-volume body panels. Investment in predictive maintenance platforms tied to retrofit and repair service offerings will convert aftermarket uptime into recurring revenue and reduce total cost of ownership for key OEM clients. Finally, commercial leaders should pursue strategic partnerships with upstream material suppliers and logistics providers to secure priority allocations for critical coated blanks and specialty alloys, and to develop contractual mechanisms that share tariff risk across the value chain.
Methodological approach combining primary interviews, technical die-process mapping, and regulatory validation to ensure reproducible and actionable market insights
The research methodology underpinning this analysis combined primary interviews with senior procurement, engineering, and operations leaders across OEMs and tiered suppliers, focused technical reviews of die and press specifications, and secondary analysis of regulatory and trade documentation. Primary engagements included structured discussions on supplier selection criteria, qualification timelines for new alloys and coated blanks, and capital planning for press purchases across tonnage classes, which informed the assessment of capability gaps and investment priorities. Secondary sources were used to validate policy timelines, customs and tariff proclamations, and to triangulate observable shifts in regional manufacturing footprints.
Data synthesis relied on cross-referencing technical die types-such as progressive, compound, transfer and fine blanking dies-with press-type constraints and material-forming windows to map where certain combinations of material and process are feasible. The methodology emphasized reproducibility: assumptions, interview guides, and scoring rubrics for supplier capability were documented so that conclusions can be re-tested against new primary data or evolving policy environments. Where applicable, qualitative inputs were converted into comparative indices to help quantify relative readiness for EV components, structural parts and aftermarket services.
Explore AI-driven insights for the Automotive Stamping Dies & Parts market with ResearchAI on our online platform, providing deeper, data-backed market analysis.
Ask ResearchAI anything
World's First Innovative Al for Market Research
Synthesis and strategic implications summarizing how material transitions, process advances, and trade dynamics combine to reshape competitive positioning
In summary, the stamping dies and parts ecosystem faces a period of structural change driven by materials transition, evolving process technologies, and stronger trade policy enforcement that together reshape sourcing economics and capital allocation. The rise of EV-specific components and the continued demand for lightweight structural parts are changing the profile of profitable work, pushing suppliers to augment their dies and press portfolios and to deepen material expertise. Trade policy developments in 2025 have accelerated localization and vertical integration tendencies, and suppliers that act quickly to secure domestic material streams, or to implement tariff mitigation strategies, will be in a stronger position to capture next-generation OEM programs.
Leaders that combine targeted capital investment, disciplined product redesign for domestic-material compatibility, and commercial models that monetize maintenance and retrofit capabilities will find the most resilient paths to growth. The near-term environment rewards agility and technical depth: those who invest in process capability, predictive service models, and strategic supplier partnerships will convert policy and material disruptions into competitive advantage.
This section provides a structured overview of the report, outlining key chapters and topics covered for easy reference in our Automotive Stamping Dies & Parts market comprehensive research report.
- Preface
- Research Methodology
- Executive Summary
- Market Overview
- Market Dynamics
- Market Insights
- Cumulative Impact of United States Tariffs 2025
- Automotive Stamping Dies & Parts Market, by Product Category
- Automotive Stamping Dies & Parts Market, by Material Type
- Automotive Stamping Dies & Parts Market, by Service Type
- Automotive Stamping Dies & Parts Market, by Process Type
- Automotive Stamping Dies & Parts Market, by Sheet Material
- Automotive Stamping Dies & Parts Market, by Tonnage Class
- Automotive Stamping Dies & Parts Market, by Press Type
- Automotive Stamping Dies & Parts Market, by Application
- Automotive Stamping Dies & Parts Market, by Vehicle Type
- Automotive Stamping Dies & Parts Market, by End User
- Americas Automotive Stamping Dies & Parts Market
- Europe, Middle East & Africa Automotive Stamping Dies & Parts Market
- Asia-Pacific Automotive Stamping Dies & Parts Market
- Competitive Landscape
- ResearchAI
- ResearchStatistics
- ResearchContacts
- ResearchArticles
- Appendix
- List of Figures [Total: 38]
- List of Tables [Total: 2654 ]
Contact the study lead to purchase the full automotive stamping dies and parts market report and arrange tailored briefings and data licensing options
To obtain the full, proprietary market research report and unlock the detailed datasets, regional breakdowns, and supplier-level analysis that underpin this executive summary, please contact Ketan Rohom, Associate Director, Sales & Marketing. Ketan will coordinate access to the comprehensive report, arrange a tailored briefing to walk through the findings most relevant to your business priorities, and provide options for licensing the data and purchasing supplementary deliverables such as custom slides, extended regional appendices, or a deep-dive supplier landscape. Prospective buyers can request a demo of key report sections and clarify the permitted uses of the intellectual property before purchase. Engaging directly will also allow you to negotiate bundled advisory time or bespoke modeling to test scenarios specific to your product portfolio, material mix, or supply-base transformation plans. Reach out to schedule a consultative call and secure immediate access to the report and supporting datasets.
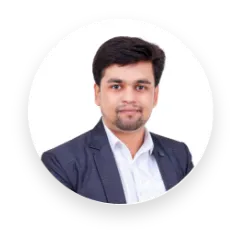
- How big is the Automotive Stamping Dies & Parts Market?
- What is the Automotive Stamping Dies & Parts Market growth?
- When do I get the report?
- In what format does this report get delivered to me?
- How long has 360iResearch been around?
- What if I have a question about your reports?
- Can I share this report with my team?
- Can I use your research in my presentation?