The Automotive Stampings Market size was estimated at USD 74.61 billion in 2024 and expected to reach USD 77.83 billion in 2025, at a CAGR 4.38% to reach USD 96.55 billion by 2030.

Shaping Tomorrow’s Vehicles with Advanced Stampings
Automotive stampings lie at the heart of modern vehicle production, delivering the structural components that define performance, safety and design. As consumers demand lighter, more efficient vehicles, the role of advanced stamping processes has never been more critical. By shaping steel and aluminum into precision parts at scale, stamping technologies enable manufacturers to meet stringent regulatory requirements while optimizing cost and assembly time.
Innovation in press design, material science and process control has transformed stamping capabilities over the past decade. High-strength steel alloys allow for thinner gauges without sacrificing rigidity, and heat-treatable aluminum alloys contribute to significant weight reduction. Concurrently, the integration of sensors and real-time feedback loops has ushered in a new era of quality assurance, reducing defects and material waste.
This executive summary will explore the disruptive dynamics influencing the automotive stampings market, from emerging manufacturing trends to policy shifts and global trade considerations. It provides a holistic view of segmentation frameworks and regional performance, uncovers competitive strategies among leading suppliers and offers actionable recommendations to navigate complexity. Designed for decision makers seeking strategic insights, this overview sets the stage for a deeper dive into the forces shaping the next generation of vehicle architectures.
Looking forward, the convergence of electrification, autonomous driving and sustainability targets is set to drive further evolution in stamping applications. As electric vehicle platforms proliferate, demand will shift toward parts that support battery enclosures, lightweight chassis components and thermal management systems. Industry players must therefore anticipate these changes with agile production strategies and targeted investments to capitalize on new growth corridors.
Revolutionary Forces Reshaping Automotive Stampings
As the automotive ecosystem transitions toward electrified powertrains, weight optimization has become a strategic imperative. Designers are increasingly relying on aluminum and advanced high-strength steel alloys to reduce mass while sustaining crash performance. These material preferences are reshaping stamping operations, prompting investments in presses capable of higher tonnage and robust die steels that withstand complex forming sequences and elevated cycle counts.
Concurrently, digitization and advanced automation are redefining process efficiency and quality assurance. The implementation of Industry 4.0 architectures, encompassing digital twins and real-time analytics, empowers engineers to simulate stamping outcomes and fine-tune parameters before physical trials. Robotic material handling and in-line inspection systems further minimize human error, accelerating throughput and ensuring consistent tolerances across high-volume production runs.
Beyond manufacturing technology, market participants face mounting pressure to demonstrate supply chain resilience and environmental stewardship. Strategic partnerships are emerging to secure raw material availability and mitigate volatility, while ongoing research into low-carbon steel and recycled aluminum signals a commitment to circular economy principles. Together, these transformative forces are forging a new landscape where agility, innovation and sustainability converge to shape the future of automotive stampings.
Unveiling the 2025 Tariff Impact on U.S. Stampings
In 2025, the continuation of Section 232 tariffs on steel and aluminum imports has introduced a renewed dynamic into the automotive stampings sector. Products derived from cold rolled and hot rolled steel, as well as heat treatable and non-heat treatable aluminum alloys, are subject to import duties that directly affect production costs. These levies, instituted on grounds of national security, have extended the timeline for stable raw material pricing, compelling manufacturers to reassess procurement strategies.
The tariff burden has reverberated through the supply chain, prompting some OEMs and tier-one suppliers to negotiate cost pass-through agreements or to absorb duties to maintain competitive pricing. This shift has intensified vendor consolidation trends, as buyers seek partners with established domestic footprint or diversified sourcing networks. In parallel, secondary sourcing has gained traction, with firms exploring regional suppliers across North America to hedge against import volatility.
Adaptation has taken multiple forms: reshoring and nearshoring initiatives have accelerated capacity expansions in domestic stamping facilities, while material engineers are advancing higher-strength alternatives that require thinner section gauges and, consequently, less raw material per component. These strategic adjustments underscore the industry’s resilience, as stakeholders navigate a tariff-inflated environment without compromising on delivery schedules or structural performance standards.
Decoding Market Segmentation for Precision Insights
A granular examination of material type reveals a bifurcated market divided between aluminum and steel stampings, each with distinct process requirements and performance attributes. Within the aluminum domain, producers differentiate between heat treatable alloys that deliver superior tensile strength post-forming and non-heat treatable variants prized for their high formability. Steel stampings, by contrast, span cold rolled grades that offer exceptional surface finish and dimensional accuracy and hot rolled steels valued for their cost effectiveness and robustness in heavy-duty applications.
Production technologies further delineate market opportunities, driven by method-specific efficiencies and part complexity. Bending remains a cornerstone process for achieving precise angular geometries, while blanking sets the stage for defining part outlines from coil stock. Coining techniques impart fine detail by compressive loading, and embossing introduces controlled surface contours for aesthetic or functional features. Flanging operations complete perimeter reinforcement, elevating assembly readiness.
Application areas underscore the functional diversity of stamped components across the vehicle architecture. Exterior panels such as doors and roof structures rely on large-format stampings, whereas the underbody network incorporates brake pedals and suspension mounts engineered to withstand dynamic loads. Inside the cabin, dashboard support structures and seating frames depend on precision-formed stampings to balance comfort, safety and assembly integration.
Finally, the end-use industry perspective distinguishes aftermarket channels focused on replacement parts and service components from original equipment manufacturers that integrate stampings into new-vehicle platforms. Each end-use avenue presents unique distribution dynamics, margin structures and quality standards that shape strategic positioning for producers seeking to capture value across the automotive lifecycle.
This comprehensive research report categorizes the Automotive Stampings market into clearly defined segments, providing a detailed analysis of emerging trends and precise revenue forecasts to support strategic decision-making.
- Material Type
- Technology
- Application
- End-Use Industry
Regional Dynamics Driving Global Stampings Trends
In the Americas, robust automotive production footprints in the United States, Mexico and Canada underpin a dynamic stamping market fueled by strong demand for light trucks and electric vehicle platforms. Proximity to key OEM assembly plants has incentivized domestic and nearshore investments in high-tonnage presses and specialized dies. The pursuit of shorter supply chains has driven regional collaborations, with mid-market suppliers expanding footprints across the North American Free Trade Agreement corridor to mitigate tariff exposure and accelerate just-in-time delivery models.
Within Europe, the Middle East and Africa, the stamping landscape is shaped by stringent regulatory requirements and diverse manufacturing cultures. European OEMs emphasize ultra-lightweight constructions, propelling the adoption of advanced aluminum stampings and dual-phase steel technologies. Meanwhile, emerging automotive hubs in North Africa and the Gulf region are cultivating localized capabilities to support aftermarket networks and lower-volume niche production. Trade agreements such as the EU’s Carbon Border Adjustment Mechanism are motivating suppliers to refine their carbon footprints, aligning material sourcing and process energy consumption with evolving sustainability mandates.
The Asia-Pacific region remains the largest by volume, driven by high-growth markets in China, India and Southeast Asia. Local stampings capacity has scaled rapidly in parallel with regional vehicle assembly, fostering a competitive environment where cost efficiency and process innovation converge. Domestic players are investing in automated forming lines and exploring high-speed forming techniques to meet the twin imperatives of affordability and quality. Simultaneously, government incentives for new energy vehicles are accelerating the development of battery enclosure stampings and thermally managed chassis components, distinguishing the region as a critical epicenter for future automotive architectures.
This comprehensive research report examines key regions that drive the evolution of the Automotive Stampings market, offering deep insights into regional trends, growth factors, and industry developments that are influencing market performance.
- Americas
- Europe, Middle East & Africa
- Asia-Pacific
Key Players Steering Innovation in Stampings
A portfolio of diversified multinationals anchors the global stamping market, combining extensive production capacity with integrated design services. Companies such as Magna International and Gestamp leverage their multinational footprints and R&D investments to deliver end-to-end solutions from blank production through complex multi-stage forming lines. Their scale enables competitive pricing while ensuring access to the latest process engineering practices and digital tooling capabilities.
Specialty tier-one suppliers also play a critical role, focusing on high-strength and lightweight components for premium and performance applications. Nemak, for instance, specializes in aluminum powertrain components and structural housings, utilizing squeeze casting techniques in conjunction with precision stamping to achieve demanding weight targets. Similarly, companies like Shiloh Industries deploy advanced metallurgy and roll-forming integrations to optimize cold rolled steel components for crash-management systems.
Regional players in Asia are scaling rapidly to capture growing domestic demand and to service export markets with cost-competitive offerings. Chinese and Indian firms have invested heavily in automated forming cells and coil processing lines, enabling them to produce high-volume parts for body-in-white assemblies. These companies are increasingly forming strategic partnerships with global automakers to co-develop localized stamping solutions tailored to region-specific vehicle platforms and regulatory landscapes.
Emerging technology providers are also making inroads, offering modular logic controls, real-time inspection systems and cloud-based analytics platforms that enhance process transparency and reduce rejection rates. These innovators often collaborate with press manufacturers to embed smart sensors and remote diagnostics, elevating traditional stamping operations toward predictive maintenance regimes and digital supply chain integration. Together, this competitive ecosystem ensures a dynamic balance between legacy expertise and frontier technologies.
This comprehensive research report delivers an in-depth overview of the principal market players in the Automotive Stampings market, evaluating their market share, strategic initiatives, and competitive positioning to illuminate the factors shaping the competitive landscape.
- AIDA Engineering, Ltd.
- AISIN CORPORATION
- American Industrial Company
- Autocomp Corporation Panse Pvt. Ltd.
- Bliss-Bret Industries
- CIE AUTOMOTIVE S.A.
- Clow Stamping Company
- D&H Industries, Inc.
- Eagle Press & Equipment Co., Ltd.
- Goshen Stamping Company
- Hyundai Rotem Company
- Industrial Quick Search, Inc.
- Interplex Holdings Pte. Ltd.
- JBM Group
- JTEKT India Limited
- KLT Group
- Macrodyne Technologies Inc.
- Manor Tool & Manufacturing Company
- Omax Autos Limited
- Ridgeview Industries, Inc.
- Schuler AG
- Teknic Motion Co., Ltd.
- Tempco Manufacturing
- Wisconsin Metal Parts, Inc.
Strategic Imperatives for Industry Leadership
To capitalize on evolving vehicle architectures, industry leaders should prioritize investments in advanced material capabilities. This entails establishing dedicated alloy development programs focused on heat treatable aluminum grades and third-generation high-strength steels. By collaborating with material suppliers and academic institutions, OEMs and stampers can co-innovate die designs that exploit these alloys’ unique properties, achieving both weight reduction and cost efficiencies in high-volume production.
Embracing digitalization will be critical to sustaining competitive advantage. Implementing integrated Industry 4.0 solutions-ranging from digital twin simulations of multi-stage stamping processes to AI-driven defect detection-enables real-time parameter optimization and predictive maintenance. Firms should adopt modular data architectures that aggregate machine performance and quality metrics across global facilities, unlocking insights to drive continuous process improvement and cross-site benchmarking.
Supply chain robustness must be enhanced through strategic diversification. Executives are advised to develop a balanced portfolio of domestic, nearshore and regional suppliers, mitigating exposure to import tariffs and logistical disruptions. Joint ventures or capacity sharing agreements with localized partners can secure raw material access, while inventory management strategies such as vendor-managed stock can ensure responsiveness to fluctuating demand.
Finally, sustainability and workforce excellence should underpin long-term strategies. Leaders need to set quantifiable carbon reduction targets within their stamping operations and invest in energy-efficient press technologies and closed-loop recycling systems. Concurrently, nurturing a skilled labor pool through apprenticeship programs and upskilling initiatives is essential to maintain the high level of precision and safety required in modern stamping environments. These comprehensive actions will position organizations to thrive amid shifting market forces and emergent vehicle platforms.
Robust Methodology Underpinning Market Intelligence
This research initiative commenced with an exhaustive review of secondary sources, including peer-reviewed journals, industry whitepapers and government publications on trade policies and material science developments. Publicly available data from regulatory bodies, patent repositories and corporate financial disclosures provided foundational insights into production capacities, tariff structures and technological advancements. This desk research established a comprehensive baseline for understanding current market dynamics and competitive positioning.
Primary research was conducted through structured interviews with senior executives at OEMs, tier-one suppliers and raw material producers. These discussions yielded qualitative perspectives on strategic priorities, investment trends and emerging challenges in stamping operations. The collected data underwent rigorous triangulation, cross-referencing quantitative indicators with expert insights to validate assumptions and refine segmentation approaches.
To ensure methodological robustness, the analysis incorporated a multi-layered data validation process, including peer review by industry specialists and cross-site consistency checks. A combination of statistical modeling and scenario analysis was applied to historical trends without engaging in forward-looking estimates. The result is a transparent, replicable methodology that prioritizes data integrity and offers reliable intelligence for strategic decision making.
Explore AI-driven insights for the Automotive Stampings market with ResearchAI on our online platform, providing deeper, data-backed market analysis.
Ask ResearchAI anything
World's First Innovative Al for Market Research
Concluding Insights: The Road Ahead for Stampings
In conclusion, the automotive stampings market stands at a strategic inflection point, driven by material innovation, digital transformation and evolving trade frameworks. Stakeholders must navigate the interplay of lightweight structural requirements, tariff-induced cost pressures and regional market dynamics to sustain growth and profitability. An informed understanding of segmentation layers-from material types and forming technologies to application domains and end-use sectors-enables precise targeting of value creation opportunities.
Looking ahead, success will hinge on the ability to integrate advanced materials, deploy smart manufacturing systems and cultivate resilient supply chains. By adopting the actionable recommendations outlined herein, industry players can align operational excellence with environmental goals, thereby securing a sustainable and competitive position in the future of vehicle manufacturing. The journey forward demands agility, collaboration and a steadfast commitment to technological advancement.
This section provides a structured overview of the report, outlining key chapters and topics covered for easy reference in our Automotive Stampings market comprehensive research report.
- Preface
- Research Methodology
- Executive Summary
- Market Overview
- Market Dynamics
- Market Insights
- Cumulative Impact of United States Tariffs 2025
- Automotive Stampings Market, by Material Type
- Automotive Stampings Market, by Technology
- Automotive Stampings Market, by Application
- Automotive Stampings Market, by End-Use Industry
- Americas Automotive Stampings Market
- Europe, Middle East & Africa Automotive Stampings Market
- Asia-Pacific Automotive Stampings Market
- Competitive Landscape
- ResearchAI
- ResearchStatistics
- ResearchContacts
- ResearchArticles
- Appendix
- List of Figures [Total: 24]
- List of Tables [Total: 412 ]
Unlock the Full Automotive Stampings Report Today
To access the full insights, detailed data and strategic recommendations contained in the complete market research report, please contact Ketan Rohom, Associate Director, Sales & Marketing. His expertise will guide you through tailored solutions and licensing options designed to empower your strategic planning in the automotive stampings sector. Reach out today to ensure your organization stays ahead in this dynamic market.
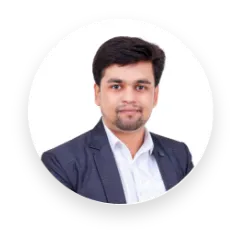
- How big is the Automotive Stampings Market?
- What is the Automotive Stampings Market growth?
- When do I get the report?
- In what format does this report get delivered to me?
- How long has 360iResearch been around?
- What if I have a question about your reports?
- Can I share this report with my team?
- Can I use your research in my presentation?