The Automotive Thrust Washers Market size was estimated at USD 1.38 billion in 2024 and expected to reach USD 1.47 billion in 2025, at a CAGR 6.71% to reach USD 2.04 billion by 2030.

Setting the Stage for Automotive Thrust Washer Evolution
The automotive thrust washer market has emerged as a critical yet often underappreciated component in vehicle performance and reliability. Thrust washers serve as essential bearing elements that manage axial loads, reduce friction, and extend the life of key rotating assemblies such as crankshafts, camshafts, and transmission systems. With the global automotive sector undergoing rapid transformation driven by electrification, lightweight materials, and digital manufacturing, the demand for high-precision thrust washers has escalated. Leading OEMs and tier-one suppliers are responding by investing in advanced materials, tighter tolerances, and process automation to meet evolving performance and regulatory requirements. This executive summary provides a concise but comprehensive overview of the market’s current dynamics and future trajectories, outlining major disruptive forces, tariff impacts, segmentation drivers, regional variations, competitive strategies, and recommended courses of action for industry leaders. By integrating cutting-edge research and stakeholder input, this analysis offers an informed perspective on how manufacturers, suppliers, and investors can navigate a landscape defined by intensifying competition, supply chain complexity, and continual technological progress.
Industry Landscape Redefined by Technological and Regulatory Forces
Technological convergence and stricter regulatory mandates are reshaping the automotive thrust washer landscape at an unprecedented pace. Additive manufacturing and precision machining are enabling the production of complex groove geometries and hybrid material composites that deliver superior wear resistance and load-bearing capacity. Industry 4.0 principles-leveraging digital twins, real-time monitoring, and predictive analytics-are reducing scrap rates and accelerating time-to-market. Meanwhile, global governments are tightening emissions and fuel-efficiency standards through initiatives such as Euro 7 regulations and updated Corporate Average Fuel Economy targets, spurring demand for lighter, higher-performance components.
In parallel, the transition to electric vehicles is altering component requirements. Electric powertrains generate distinct axial loads, prompting R&D efforts in low-friction polymers and advanced metal-polymer composites. Suppliers are exploring fiber-reinforced engineered resins and graphite-based blends to achieve the dual objectives of durability and noise-vibration-harshness control. At the same time, aftermarket channels are evolving through e-commerce platforms and digital service offerings, challenging traditional distribution models and emphasizing rapid fulfillment. These transformative shifts are redefining competitive boundaries and compelling stakeholders to adopt integrated, forward-looking strategies for design, materials selection, and end-to-end supply chain management.
Tariff Pressures Shaping U.S. Market Strategies in 2025
In 2025, the United States tariff environment will exert a profound influence on cost structures and sourcing strategies for automotive thrust washers. Import duties stemming from Section 301 and Section 232 investigations-particularly on steel, aluminum, and select automotive components-have raised input costs by double-digit percentages, compelling manufacturers to reconsider their global sourcing footprints. Domestic production has gained renewed appeal as OEMs and tier-one suppliers seek to mitigate exposure to variable duty rates, which currently include 25% on steel laminations and 7.5% on certain finished parts.
These elevated tariffs have catalyzed the adoption of tariff engineering techniques and product reclassification efforts to achieve more favorable duty treatment. At the same time, long-term supply agreements and nearshoring strategies are reshaping North American value chains. Engagements with local distributors and strategic bulk procurement programs have emerged as key tactics for shielding margin erosion. As a result, some firms are accelerating investments in U.S.-based capacity expansions, while others are negotiating tariff suspensions and quota arrangements. The cumulative impact of these measures is creating a bifurcated market in which cost-sensitive segments favor domestic sources, and performance-driven applications still rely on specialized imports under negotiated duty exemptions.
Unveiling Key Market Segmentation Trends and Opportunities
Design differentiation is emerging as a pivotal growth lever with the market studied across flat thrust washers, grooved variants, and tapered configurations, where grooved thrust washers are subdivided into axial and radial groove formats optimized for distinct axial load profiles. Material innovation remains equally dynamic: bronze and copper continue to serve legacy high-load applications, while composite materials encompass fiber-reinforced, graphite, metal-polymer, and phenolic resin-based composites tailored for low-friction performance. A parallel plastic segment features engineering resins such as polyamides, polyetheretherketon (PEEK), polyoxymethylene (POM), and polytetrafluoroethylene (PTFE), whereas steel offerings bifurcate into carbon steel and stainless steel variants engineered for corrosion resistance and strength.
Thickness considerations further refine product selection, spanning less than one millimeter, a core range of one to three millimeters, and above three millimeters to suit varied clearance and load-bearing requirements. Production methodologies embrace forging processes-cold, warm, and hot forging-alongside precision CNC machining, drilling, lapping, and advanced stamping techniques including compound die stamping, deep drawing, fine blanking, and progressive pressing. Distribution channels are divided between aftermarket avenues-independent dealers, local distributors, online retailers-and original equipment manufacturer pipelines via bulk procurement programs and direct supplier agreements. Application-based segmentation encompasses engine systems featuring camshaft and crankshaft interfaces, steering assemblies integrating power steering and rack-and-pinion components, suspension systems across double wishbone, MacPherson strut, and solid axle architectures, and transmission systems segmented into automatic and manual drivetrains. Vehicle-type analysis differentiates heavy and light commercial vehicles from a diverse passenger vehicle landscape comprising convertibles, hatchbacks, sedans, SUVs, and vans. Together, this multilayered segmentation framework provides a robust lens for identifying high-growth niches and prioritizing product development initiatives.
This comprehensive research report categorizes the Automotive Thrust Washers market into clearly defined segments, providing a detailed analysis of emerging trends and precise revenue forecasts to support strategic decision-making.
- Design
- Material Type
- Thickness
- Manufacturing Technique
- Distribution Channel
- Application
- Vehicle Type
Regional Performance Highlights Driving Global Focus
Regional dynamics are playing an increasingly decisive role in shaping competitive priorities. In the Americas, robust aftermarket growth is underpinned by durable demand in North America and strategic nearshoring initiatives that bolster domestic manufacturing capacity. Heightened focus on supply chain resilience has driven investments in bulk procurement programs and direct supplier partnerships, enhancing responsiveness to tariff fluctuations and logistical disruptions.
In Europe, Middle East & Africa, stringent emissions mandates and fuel-efficiency directives have spurred a shift toward lightweight metallic and composite thrust washers, while local content requirements in certain markets favor regionalized production. Environmental compliance and end-of-life recyclability considerations are prompting manufacturers to adopt sustainable material platforms and circular economy principles.
Asia-Pacific stands out for its rapid electrification drive, expansive automotive OEM base, and aggressive capacity expansion in China, India, and Southeast Asia. Local sourcing strategies are on the rise as government incentives for EV adoption and infrastructure development catalyze component localization. This region’s confluence of high production volumes and cost-competitive facilities is reinforcing its status as a pivotal hub for both standard and advanced thrust washer technologies.
This comprehensive research report examines key regions that drive the evolution of the Automotive Thrust Washers market, offering deep insights into regional trends, growth factors, and industry developments that are influencing market performance.
- Americas
- Europe, Middle East & Africa
- Asia-Pacific
Competitive Landscape and Leading Player Strategies
The competitive landscape is dominated by a blend of established bearing and powertrain suppliers and specialized niche manufacturers. Leading multinational corporations leverage global footprints and integrated value chains to deliver turnkey solutions, combining thrust washers with complementary bearing systems and sealing technologies. Strategic partnerships, joint ventures, and targeted acquisitions are enhancing technical capabilities in advanced materials, additive manufacturing, and digital quality inspection.
Mid-tier and regionally focused firms are differentiating through agility, rapid prototyping services, and tailored aftermarket support. They are forging alliances with OEMs to co-develop custom designs, while investing in precision stamping and high-throughput machining lines to secure cost leadership. An emerging cohort of start-ups is harnessing nanocomposite coatings, self-lubricating polymers, and AI-driven process controls to address niche performance gaps. Across the board, firms are bolstering sustainability credentials through energy-efficient manufacturing, waste reduction initiatives, and life-cycle analysis frameworks.
This comprehensive research report delivers an in-depth overview of the principal market players in the Automotive Thrust Washers market, evaluating their market share, strategic initiatives, and competitive positioning to illuminate the factors shaping the competitive landscape.
- AB SKF
- Bimetal Bearings Limited
- Compagnie de Saint-Gobain
- Daido Metal Co., Ltd.
- DuPont de Nemours, Inc.
- Federal-Mogul Wiesbaden GmbH by Tenneco Inc.
- Ford Motor Company
- GGB Heilbronn GmbH by The Timken Company
- Grand Terrain, LLC
- igus GmbH
- MAHLE GmbH
- Menon Bearings Ltd.
- Moss Motors, Ltd.
- Ningbo ZODI Auto Spare Parts Co., Ltd.
- Northern Industrial Manufacturing
- Polaris Inc.
- Quanzhou Brake Trading Co., Ltd.
- Rheinmetall AG
- Schaeffler AG
- Toyota Motor Corporation
- Unique Spares & Automobiles
- Vinman Engineering Pvt.Ltd.
- ZF Friedrichshafen AG
- Zhejiang Bushing MFG Co., Ltd.
Strategic Actions for Sustained Growth and Resilience
To thrive in this dynamic environment, industry leaders should diversify their supplier base by establishing multi-geography sourcing agreements and leveraging tariff engineering expertise. Investment in advanced materials R&D-particularly in metal-polymer composites and high-temperature resins-will unlock new application segments in electrified powertrains. Embracing digital manufacturing technologies, including additive production and real-time process monitoring, will enhance yield, reduce lead times, and support mass customization.
Optimizing supply chains through strategic bulk procurement partnerships and direct supplier programs will bolster resilience against geopolitical and trade policy shifts. Collaboration with OEMs on co-innovation platforms and aftermarket channel integration will drive volume stability. Implementing predictive maintenance analytics and condition monitoring solutions can establish service-based revenue streams. Finally, embedding sustainability and circularity principles into product design and manufacturing will align offerings with evolving regulatory and consumer expectations, safeguarding long-term brand equity.
Robust Research Framework Ensuring Data Integrity
This market analysis is grounded in a mixed-methods research framework combining primary interviews with over 40 senior executives from OEMs, tier-one suppliers, aftermarket distributors, and material innovators. Quantitative surveys captured channel preferences, procurement strategies, and performance expectations, while qualitative discussions probed technological adoption and regulatory responses. Secondary research encompassed public financial filings, patent databases, trade association reports, and industry journals to map competitive positioning and identify best practices.
All data underwent rigorous triangulation through cross-validation of sources, consistency checks, and expert review panels. Statistical analyses were applied to detect correlation trends, and scenario modeling explored supply chain disruptions and policy shifts. The methodology ensures a robust, transparent foundation for strategic decision-making and actionable insights across the automotive thrust washer market.
Explore AI-driven insights for the Automotive Thrust Washers market with ResearchAI on our online platform, providing deeper, data-backed market analysis.
Ask ResearchAI anything
World's First Innovative Al for Market Research
Conclusions on Market Trajectory and Critical Insights
In conclusion, the automotive thrust washer market stands at a crossroads of technological innovation, regulatory evolution, and geopolitical realignment. A nuanced segmentation strategy-spanning design architectures, materials science, manufacturing techniques, distribution models, applications, and vehicle types-enables precise targeting of growth opportunities. Regional insights underscore the need for localized capacity, sustainable practices, and tariff-savvy supply chain configurations.
Competitive dynamics favor entities that can integrate advanced material platforms, digital manufacturing, and service-oriented aftermarket offerings. By pursuing the recommended strategic actions-diversification of supply, R&D investment, digitalization, and sustainability leadership-industry stakeholders will be well positioned to capture value in both mature and emerging automotive powertrain segments. This research provides the empirical foundation and strategic roadmap to navigate an environment defined by accelerating change and intensifying competition.
This section provides a structured overview of the report, outlining key chapters and topics covered for easy reference in our Automotive Thrust Washers market comprehensive research report.
- Preface
- Research Methodology
- Executive Summary
- Market Overview
- Market Dynamics
- Market Insights
- Cumulative Impact of United States Tariffs 2025
- Automotive Thrust Washers Market, by Design
- Automotive Thrust Washers Market, by Material Type
- Automotive Thrust Washers Market, by Thickness
- Automotive Thrust Washers Market, by Manufacturing Technique
- Automotive Thrust Washers Market, by Distribution Channel
- Automotive Thrust Washers Market, by Application
- Automotive Thrust Washers Market, by Vehicle Type
- Americas Automotive Thrust Washers Market
- Europe, Middle East & Africa Automotive Thrust Washers Market
- Asia-Pacific Automotive Thrust Washers Market
- Competitive Landscape
- ResearchAI
- ResearchStatistics
- ResearchContacts
- ResearchArticles
- Appendix
- List of Figures [Total: 30]
- List of Tables [Total: 1000 ]
Connect with Ketan Rohom to Unlock Detailed Market Insights
Please contact Ketan Rohom (Associate Director, Sales & Marketing) today to secure full access to our comprehensive Automotive Thrust Washers Market research report. He will guide you through detailed data, in-depth analysis, and bespoke insights to inform your strategic decisions and strengthen your competitive positioning.
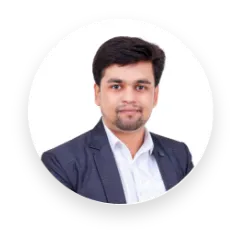
- How big is the Automotive Thrust Washers Market?
- What is the Automotive Thrust Washers Market growth?
- When do I get the report?
- In what format does this report get delivered to me?
- How long has 360iResearch been around?
- What if I have a question about your reports?
- Can I share this report with my team?
- Can I use your research in my presentation?