The Automotive Tire Molds Market size was estimated at USD 1.82 billion in 2024 and expected to reach USD 1.93 billion in 2025, at a CAGR 6.11% to reach USD 2.60 billion by 2030.

Setting the Stage for Innovation in Tire Mold Manufacturing
Since the advent of radial tire technology, the manufacturing process for molds has become increasingly sophisticated. The tire mold market is at the forefront of material science and precision engineering, underpinned by the demand for high-performance and environmentally sustainable tires. As automakers pursue lower rolling resistance and extended tread life, mold producers are challenged to innovate in design complexity, material resilience and manufacturing throughput.
Recent supply chain disruptions have underscored the importance of agile production strategies and local sourcing. Digital twins and predictive maintenance systems are now integral to modern mold shops, enabling real-time monitoring and reducing unplanned downtime. In tandem, the electrification of mobility and the rise of autonomous vehicles are driving demand for specialized tread patterns that balance energy efficiency with safety and comfort.
Moreover, the convergence of consumer personalization and lean manufacturing has prompted mold manufacturers to embrace rapid prototyping and flexible tooling. Collaborative partnerships between mold shops and tire designers are yielding bespoke solutions that accelerate time to market. This collaborative spirit is further fueled by investments in next-generation manufacturing methods such as additive processes.
This executive summary distills the most salient trends, policy developments and competitive dynamics shaping the tire mold industry today. By unpacking technological advancements, tariff impacts, segmentation patterns and regional opportunities, we aim to equip decision-makers with actionable intelligence to navigate an increasingly complex and opportunity-rich landscape.
Emerging Transformations Redefining the Tire Mold Arena
Digital transformation is redefining the contours of the tire mold industry, with data-driven workflows and automation enabling unprecedented levels of precision and efficiency. Smart factory initiatives are integrating sensors and analytics tools across the production floor, delivering insights that optimize cycle times, reduce scrap rates and enhance overall equipment effectiveness. Beyond process automation, digital platforms are facilitating remote collaboration between design teams, mold engineers and supply chain partners to streamline development cycles and accelerate innovation.
Parallel to the digital wave, additive manufacturing is emerging as a game changer for mold prototyping and small-batch production. By leveraging layer-by-layer fabrication, mold shops can rapidly iterate complex geometries and validate performance characteristics before committing to high-volume machining. The growing maturity of additive technologies is also lowering barriers for producing specialized inserts for tread patterns, enabling greater customization without incurring protracted lead times.
Sustainability imperatives are exerting a transformative influence on mold materials and energy consumption. Water-based release agents, low-emission coatings and energy-efficient furnaces are becoming standard considerations in plant upgrades. Regulatory pressures to curb greenhouse gas emissions are prompting manufacturers to track carbon footprints throughout the mold lifecycle, while end users increasingly demand molds produced under rigorous environmental stewardship.
Moreover, geopolitical realignments and trade policy shifts are motivating companies to reassess global sourcing strategies and invest in regional manufacturing hubs. This redistribution of capacity responds to both cost pressures and the need for supply chain resilience, ensuring that mold producers remain agile in the face of emerging market risks and opportunities.
Assessing the 2025 United States Tariff Ripple Effects
In early 2025, new United States tariffs targeting imported components and raw materials began to reshape the economics of tire mold production. Levies on certain steel and aluminum grades, as well as on molds sourced from designated countries, have introduced additional cost layers that resonate throughout the value chain. Mold manufacturers faced with higher input prices are evaluating strategies to offset these increases, ranging from material substitution and supplier renegotiation to partial pass-through costs to original equipment manufacturers.
These tariff measures have accelerated the push toward domestic capacity expansion. Investments in local machining centers and additive manufacturing facilities are being justified by the potential to mitigate import levies and shorten lead times. At the same time, tariff-related uncertainties have prompted some mold producers to secure long-term contracts with North American foundries, ensuring steady access to critical alloys at predictable pricing.
The ripple effects of the tariff regime extend into project planning and capital allocation. Engineering teams are revisiting material specifications to identify feasible alternatives such as aluminum alloys with comparable mechanical properties or composite inserts that reduce reliance on tariffed steel categories. Concurrently, procurement leaders are diversifying their supplier base, extending beyond traditional low-cost regions to cultivate partnerships in jurisdictions with favorable trade agreements or stable regulatory environments.
With the tariff landscape likely to evolve further, mold manufacturers are advised to maintain dynamic cost models and engage in proactive scenario planning. By continuously modeling tariff scenarios and their impact on gross margins, companies can devise adaptive pricing structures, hedge currency exposures and safeguard profitability in an increasingly volatile trade environment.
Unveiling Critical Segmentation Patterns Shaping Market Dynamics
Material selection remains a cornerstone of performance and durability in tire mold manufacturing. Aluminum molds are prized for their lightweight construction and superior thermal conductivity, facilitating faster cycle times and more consistent cooling. Rubber molds continue to be utilized for their inherent flexibility, particularly in applications requiring intricate tread features. However, steel dominates the market due to its exceptional wear resistance and structural integrity. Within the steel category, prehardened steel offers a cost-efficient balance of toughness and machinability, whereas stainless steel provides enhanced corrosion resistance and a finer surface finish, critical for premium tire lines.
Mold architecture significantly influences production flexibility and maintenance requirements. Segmented molds enable rapid reconfiguration of individual pattern blocks, granting manufacturers the ability to accommodate multiple tire designs within the same tooling investment. Conversely, two-piece molds deliver robust clamping force and are preferred for large-diameter or high-load applications such as heavy truck and off-the-road tires. The choice between these mold types is often informed by anticipated production volumes, changeover frequency and the technical specifications of the tire being manufactured.
Advances in additive manufacturing and CNC machining are reshaping the technology landscape for mold production. Computer numerical control (CNC) machining offers high precision and repeatability, making it the standard for high-volume runs. In parallel, additive manufacturing platforms are gaining traction for prototyping and low-volume series production. Fused deposition modeling accelerates proof-of-concept stages, selective laser sintering delivers robust part strength and stereolithography achieves ultra-fine surface detail for complex tread geometries, opening new possibilities for design creativity.
The diverse range of tire applications-from agricultural to passenger car-drives specialized mold requirements. Agricultural molds demand rugged patterns to withstand abrasive soil conditions, while heavy truck molds prioritize load distribution and thermal management. Light truck and passenger car molds balance ride comfort, noise reduction and fuel efficiency, and off-the-road molds focus on abrasion resistance for extreme terrains. These technical demands intersect with end-user segmentation, where original equipment manufacturers necessitate high-volume, consistency-driven tooling under stringent quality standards, and the aftermarket sector values cost-effective, easily maintainable molds to support repair and retread cycles.
This comprehensive research report categorizes the Automotive Tire Molds market into clearly defined segments, providing a detailed analysis of emerging trends and precise revenue forecasts to support strategic decision-making.
- Material
- Mold Type
- Technology
- Tire Type
- End User
Regional Nuances Driving Growth Trajectories Across Key Markets
Regional dynamics are critically shaping the trajectory of the tire mold market. In the Americas, the United States and Canada are witnessing a resurgence of domestic mold production as manufacturers respond to tariff-induced cost pressures and logistical challenges. Mexico remains an important foothold for nearshore operations, offering a strategic balance of labor cost advantages and proximity to major original equipment manufacturers. Investments in local machining centers and additive manufacturing cells are enabling North American mold producers to deliver rapid turnaround times and reinforce supply chain continuity.
Across Europe, Middle East & Africa, sustainability regulations and stringent emissions standards are accelerating the adoption of eco-friendly mold production practices. European mold makers are leading the way in water-based release agents and energy-efficient heat treatment systems, while research collaborations in the region are pioneering bio-based polymers for innovative mold liners. In the Middle East, growth in commercial vehicle production is fostering demand for high-durability molds, and Africa’s emerging tire manufacturing hubs are increasingly turning to modular segmented molds to capitalize on flexible tooling strategies.
The Asia-Pacific region represents the most dynamic growth frontier, underpinned by rapid industrialization in China and India. Chinese mold manufacturers are scaling up high-precision CNC operations and integrating additive technologies into pilot production, buoyed by government incentives for advanced manufacturing. In India, shifting automotive investments and infrastructure projects are driving demand for heavy truck and off-the-road mold solutions. Southeast Asian markets are also expanding as local tire producers pursue vertical integration, generating opportunities for specialized mold suppliers to establish footholds and joint ventures throughout the region.
This comprehensive research report examines key regions that drive the evolution of the Automotive Tire Molds market, offering deep insights into regional trends, growth factors, and industry developments that are influencing market performance.
- Americas
- Europe, Middle East & Africa
- Asia-Pacific
Profiling Leading Innovators in the Tire Mold Sector
Leading tire mold manufacturers are differentiating through strategic investments in research and development, digital integration and global production capacities. Trelleborg sets benchmarks in high-performance elastomer technologies, leveraging its end-to-end capabilities to deliver turnkey mold solutions for premium tire segments. Freudenberg Sealing Technologies has expanded its metallurgical expertise to include advanced mold liners and optimized surface treatments, addressing the dual demands of durability and rapid prototyping.
Sumitomo Precision Products has fortified its market position by integrating additive manufacturing platforms alongside its traditional CNC machining centers, enabling faster concept validation and reduced time to market. JTEKT’s focus on precision tooling and modular mold systems has catered to varying production scales, from high-volume passenger car applications to specialized agricultural patterns. Meanwhile, regional specialists such as Plastomatics and select Chinese producers have carved niches by offering cost-competitive solutions and agile customization services for local tire manufacturers.
Collaborative ventures are also reshaping the competitive landscape. Partnerships between mold shops and software providers are yielding digital twin environments that simulate thermal and mechanical performance before physical tooling is produced. In parallel, alliances with material suppliers are fostering the development of next-generation alloys and coating technologies that extend mold life and reduce maintenance cycles. These strategic moves underscore a broader industry shift toward integrated value chains and data-driven decision making.
This comprehensive research report delivers an in-depth overview of the principal market players in the Automotive Tire Molds market, evaluating their market share, strategic initiatives, and competitive positioning to illuminate the factors shaping the competitive landscape.
- King Machine
- Herbert Maschinen- und Anlagenbau GmbH & Co. KG
- Continental AG
- Shinko Mold Industrial Co., Ltd.
- The Yokohama Rubber Co., Ltd.
- Georg Fischer Ltd.
- NGK FINE MOLDS, Inc.
- Vulcan-Vulcap Industries Inc. by International Tire Repair Solutions Inc.
- Shandong Haomai Machinery Technology Co., Ltd.
- MESNAC Co., Ltd.
- Athens Mold and Machine
- Himile Mechanical Science & Technology (Shandong) Co, Ltd.
- PNEUFORM Hulín, Inc.
- Allied Industries
- Langer GmbH & Co. KG
- Hankook Precision Works Co., Ltd.
- Metalcraft Solutions
- Kohitech Tooling LLP
- SHANDONG YUNFENG CNC TECHNOLOGY CO., LTD.
- dynamic design Co., Ltd.
Strategic Imperatives to Gain Competitive Advantage
To secure a competitive edge, industry leaders should prioritize investments in additive manufacturing and digital twin technologies to shorten development lifecycles and enhance product innovation. By integrating real-time data analytics into production processes, companies can proactively identify performance bottlenecks and optimize mold designs for durability and cost efficiency. Embracing a modular tooling approach will further enable rapid reconfiguration for multiple tire lines, reducing capital expenditures and inventory risks.
Collaborating closely with tire manufacturers on co-development initiatives can yield bespoke mold solutions tailored to evolving performance requirements, particularly in electrified and autonomous vehicle applications. Establishing strategic alliances with material science partners will drive breakthroughs in alloy composition and surface coatings, supporting sustainability goals by minimizing energy consumption and extending tool life. Moreover, firms should diversify their supply chains by cultivating secondary manufacturing hubs in regions with favorable trade agreements, mitigating tariff exposure and ensuring resilience against geopolitical disruptions.
Finally, cultivating a skilled workforce through targeted training programs in advanced machining, additive fabrication and digital modeling is essential to operational excellence. By investing in talent development and cross-functional collaboration, mold producers can accelerate innovation, maintain rigorous quality standards and deliver superior value to both original equipment and aftermarket customers.
Robust Multi-Source Methodology Anchoring the Analysis
This analysis is founded on a robust, multi-source methodology, combining primary interviews with senior executives, engineering specialists and procurement leaders across the tire and mold industries. In total, more than 50 in-depth interviews were conducted to capture real-world perspectives on technological adoption, supply chain strategies and market challenges. These insights were supplemented by secondary research, including industry publications, regulatory filings and patent databases, to ensure comprehensive coverage of emerging trends and competitive dynamics.
Data triangulation techniques were employed to validate findings, aligning qualitative input with quantitative indicators such as trade statistics, production volumes and material pricing trends. Case studies of leading mold producers provided granular context for best practices in operational management and innovation roadmaps. An expert advisory panel reviewed draft conclusions to confirm technical accuracy and relevance, while iterative feedback loops refined the strategic recommendations.
The research framework emphasizes transparency and reproducibility, with documentation of data sources, interview protocols and analytical models. Rigorous quality checks, including cross-functional peer reviews and conflict-of-interest assessments, underpin the credibility of the analysis. This methodological rigor ensures that the resulting insights accurately reflect the complexities of the global tire mold market and inform sound strategic decision-making.
Explore AI-driven insights for the Automotive Tire Molds market with ResearchAI on our online platform, providing deeper, data-backed market analysis.
Ask ResearchAI anything
World's First Innovative Al for Market Research
Concluding Insights on the Evolving Tire Mold Landscape
The tire mold industry stands at a pivotal juncture, propelled by technological innovation, shifting trade policies and evolving consumer demands. As additive manufacturing and digital platforms reshape design and production paradigms, mold producers must adapt by embracing flexible tooling strategies and sustainable material choices. Concurrently, the 2025 tariff landscape has highlighted the importance of regional capacity, dynamic cost modeling and supply chain diversification.
Segmentation insights reveal that material preferences, mold architecture and technological approaches are becoming more specialized, driven by the performance requirements of distinct tire categories and the quality demands of OEM and aftermarket segments. Regional analyses underscore the opportunities in the Americas, Europe, Middle East & Africa and Asia-Pacific for companies that can align production footprints with local market drivers and regulatory environments. Leading players are forging partnerships and investing in R&D to deliver next-generation mold solutions, setting new standards in durability, precision and speed to market.
Looking ahead, success in the tire mold sector will hinge on collaborative innovation, data-driven operations and strategic agility. By leveraging insights from this report, industry stakeholders can navigate uncertainties, capitalize on growth pockets and chart a resilient course through an increasingly complex marketplace.
This section provides a structured overview of the report, outlining key chapters and topics covered for easy reference in our Automotive Tire Molds market comprehensive research report.
- Preface
- Research Methodology
- Executive Summary
- Market Overview
- Market Dynamics
- Market Insights
- Cumulative Impact of United States Tariffs 2025
- Automotive Tire Molds Market, by Material
- Automotive Tire Molds Market, by Mold Type
- Automotive Tire Molds Market, by Technology
- Automotive Tire Molds Market, by Tire Type
- Automotive Tire Molds Market, by End User
- Americas Automotive Tire Molds Market
- Europe, Middle East & Africa Automotive Tire Molds Market
- Asia-Pacific Automotive Tire Molds Market
- Competitive Landscape
- ResearchAI
- ResearchStatistics
- ResearchContacts
- ResearchArticles
- Appendix
- List of Figures [Total: 26]
- List of Tables [Total: 324 ]
Engage with Associate Director Ketan Rohom to Secure Your Comprehensive Report
To gain full access to the comprehensive tire mold market research report, please connect with Ketan Rohom, Associate Director of Sales & Marketing, who will guide you through tailored insights and purchasing options. Ketan’s expertise spans in-depth market analysis, customer engagement and strategic advisory services, ensuring that your organization receives the data-driven intelligence needed to inform critical decisions.
Whether you require a detailed segmentation deep dive, an assessment of tariff impacts or customized recommendations for operational excellence, reach out to schedule a personalized consultation. Secure your competitive advantage by partnering with Ketan to obtain the definitive resource on global tire mold market dynamics and emerging opportunities.
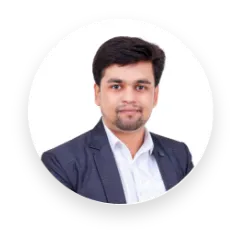
- How big is the Automotive Tire Molds Market?
- What is the Automotive Tire Molds Market growth?
- When do I get the report?
- In what format does this report get delivered to me?
- How long has 360iResearch been around?
- What if I have a question about your reports?
- Can I share this report with my team?
- Can I use your research in my presentation?