Revolution in Automotive Die Casting Presents Unprecedented Opportunities and Challenges for Efficient Transmission Case Manufacturing
The evolution of automotive transmission design has propelled aluminum die casting to the forefront of manufacturing innovation. As vehicle OEMs prioritize lighter, stronger, and more cost-effective solutions, aluminum die cast transmission cases have emerged as a critical enabler of performance and efficiency. These components play a pivotal role in ensuring precise gear alignment, thermal management, and structural integrity, particularly in the context of next-generation electrified drivetrains. Amid intensifying regulatory standards targeting fuel economy and emissions, the adoption of aluminum alloy die casting offers significant weight reduction benefits without compromising mechanical robustness. This shift underscores a broader industry trend toward advanced materials and streamlined production methods which respond to both environmental imperatives and customer demand for reliability.
Moreover, the competitive landscape for transmission case manufacturing is becoming increasingly dynamic. Traditional internal combustion vehicle platforms continue to rely on established die casting techniques, while hybrid and electric powertrains introduce novel design requirements that test the limits of current process capabilities. In turn, manufacturers are compelled to invest in high-precision tooling, refined metallurgical formulations, and automated quality inspection systems. Transitioning from legacy production frameworks to state-of-the-art die casting operations not only demands capital investment but also a strategic orientation toward collaborative R&D. Stakeholders across the supply chain-spanning foundries, tier-one suppliers, and academic research institutions-are forging partnerships to co-develop breakthrough solutions that will define the next era of transmission performance and sustainability.
Rapid Advancements in Materials Science and Process Innovations Redefining Future of Transmission Case Aluminum Die Casting Landscape
The automotive die casting sector is experiencing transformative shifts driven by advancements in materials science and manufacturing processes. High-strength aluminum alloys with improved fluidity and thermal conductivity are gaining traction, enabling thinner wall sections and more intricate cavity geometries in transmission cases. Coupled with precision high-pressure die casting machines equipped with real-time monitoring, these material innovations yield parts that meet increasingly stringent dimensional tolerances and mechanical specifications. As digital twins and simulation technologies become commonplace, production lines are optimized virtually before tooling development, reducing cycle times and preempting quality deviations.
In parallel, the integration of additive manufacturing for mold inserts and cores is redefining design freedom, allowing for internal channels and lattice structures that enhance cooling performance. This convergence of additive and subtractive techniques fosters a hybrid manufacturing ecosystem in which traditional die casting is augmented by rapid prototyping methods. Furthermore, Industry 4.0 connectivity is streamlining data collection across presses, furnaces, and inspection stations, enabling predictive maintenance and minimizing unplanned downtime. Overall, this wave of innovation is accelerating throughput, elevating part quality, and unlocking new design paradigms-reshaping the competitive dynamics of transmission case production for both conventional drivetrains and electrified architectures.
Assessing the Multifaceted Consequences of 2025 United States Tariffs on Aluminum Die Cast Transmission Case Production and Supply Chains
The imposition of new United States tariffs on imported aluminum in 2025 has introduced a complex set of considerations for transmission case manufacturers. Elevated duties on raw material imports from key supplier regions have increased input costs, prompting many producers to reassess their procurement strategies. Several foundries have responded by securing long-term contracts with domestic smelters or by sourcing recycled aluminum to mitigate cost fluctuations. At the same time, the ripple effects of these tariffs have altered global freight patterns and lead times, as logistical bottlenecks emerge and alternative supply corridors are activated.
Moreover, the tariff regime has accelerated nearshoring initiatives, with some companies establishing additional capacity within North America to sidestep import duties altogether. While this shift enhances supply chain resilience, it also introduces challenges related to capital expenditure, workforce training, and competitive pricing pressures. For multinational OEMs, the recalibration of sourcing footprints has triggered cross-regional negotiations to rebalance component allocations. Consequently, the cumulative impact of the 2025 tariffs extends beyond cost inflation, influencing strategic investment decisions and partnership frameworks across the transmission case die casting ecosystem.
Deep Dive into Transmission Case Aluminum Die Casting Market Segmentation Unveils Strategic Opportunities Across Key Product and Application Categories
Insight into the transmission case aluminum die casting market is enriched by exploring segmentation across multiple dimensions. When examining transmission type, it becomes evident that the rising adoption of automatic transmissions drives demand for more complex, high-precision die cast cases, while continuingly variable transmissions require optimized wall thicknesses to facilitate seamless power delivery. Dual clutch transmissions, with their rapid shift capabilities, necessitate casings that balance rigidity and thermal dissipation, whereas manual transmissions continue to favor cost-effective, simplified castings for broad applications.
Process technology further differentiates market dynamics: high-pressure die casting dominates in high-volume scenarios, delivering consistent part quality, while low-pressure and vacuum techniques are leveraged for specialized applications that demand superior mechanical properties and reduced porosity. This diversity in process selection reflects evolving OEM priorities around part reliability and production efficiency. Additionally, vehicle type segmentation illustrates how heavy commercial vehicles impose rigorous durability requirements for robust chassis integration, light commercial vehicles emphasize payload efficiency and lifecycle costs, and passenger cars prioritize weight savings and noise reduction for enhanced ride comfort. By synthesizing these segmentation insights, industry stakeholders can tailor their manufacturing strategies to address the distinct performance and cost imperatives of each application cohort.
This comprehensive research report categorizes the Automotive Transmission Case Aluminum Die Casting market into clearly defined segments, providing a detailed analysis of emerging trends and precise revenue forecasts to support strategic decision-making.
- Transmission Type
- Process Technology
- Vehicle Type
Comparative Evaluation of Americas, EMEA, and Asia-Pacific Markets Reveals Divergent Dynamics Influencing Transmission Case Aluminum Die Casting Growth
A regional lens reveals distinct growth trajectories and investment priorities shaping the transmission case aluminum die casting domain. In the Americas, strong OEM investment in light-weighting initiatives combined with growing electric vehicle production in North America has spurred local die casting capacity expansions. Supply chain consolidation and collaborative pilot projects with automotive clusters underscore the region’s emphasis on manufacturing agility and sustainability.
Across Europe, the Middle East, and Africa, stringent emissions regulations and the rapid electrification of fleets in Western Europe have driven demand for advanced die cast casings able to withstand higher thermal loads. Foundries in Germany and the United Kingdom are leading process automation efforts, integrating robotics and quality inspection systems to meet rigorous OEM specifications, while emerging markets in the Middle East and Africa explore partnerships to develop localized production hubs that reduce import dependency.
In Asia-Pacific, high production volumes in China, Japan, and India anchor a mature die casting ecosystem, yet the pivot toward electric and hybrid powertrains is reshaping equipment investments and alloy choices. Regional manufacturers are collaborating closely with global automakers to refine casting recipes and implement digital monitoring solutions. These distinct regional dynamics highlight the importance of tailored market entry and capacity planning strategies for stakeholders seeking to optimize their geographic footprint.
This comprehensive research report examines key regions that drive the evolution of the Automotive Transmission Case Aluminum Die Casting market, offering deep insights into regional trends, growth factors, and industry developments that are influencing market performance.
- Americas
- Europe, Middle East & Africa
- Asia-Pacific
Profiling Industry Leaders Driving Innovation in Transmission Case Aluminum Die Casting with Collaborative Strategies and Technological Prowess
Several leading players are redefining the competitive landscape through targeted investments and collaborative ventures. Major foundries have expanded their R&D centers to explore next-generation aluminum alloys and closed-loop recycling systems, aligning with OEM sustainability goals. Cross-industry partnerships between automotive suppliers and equipment manufacturers are resulting in turnkey die casting cells that integrate automated mold handling, molten metal delivery, and in-line non-destructive testing. Some organizations have initiated joint development agreements with universities and national laboratories to pioneer ultrafine grain microstructures that enhance mechanical performance while reducing cycle times.
Furthermore, forward-looking companies are leveraging digital platforms to offer predictive analytics services, allowing OEMs to anticipate maintenance needs and batch variability. Strategic acquisitions and capacity partnerships in key regions have enabled these firms to secure long-term contracts with global automakers. By combining metallurgical expertise with advanced process automation, these companies are establishing best-in-class benchmarks for part consistency, sustainability metrics, and total cost of ownership-ultimately shaping the direction of transmission case manufacturing for years to come.
This comprehensive research report delivers an in-depth overview of the principal market players in the Automotive Transmission Case Aluminum Die Casting market, evaluating their market share, strategic initiatives, and competitive positioning to illuminate the factors shaping the competitive landscape.
- Nemak, S.A.B. de C.V.
- Ryobi Limited
- Linamar Corporation
- Martinrea International Inc.
- Dynacast International LLC
- Magna International Inc.
- Shiloh Industries, Inc.
- Honsel GmbH
- Gibbs Die Casting Corporation
- Endurance Technologies Limited
Actionable Strategies for Industry Leaders to Navigate Tariffs, Technological Shifts, and Competitive Pressures in Die Casting Transmission Case Manufacturing
Industry leaders must take decisive action to thrive amidst evolving market dynamics. First, investing in advanced process technologies such as vacuum die casting and hybrid additive tooling will enable manufacturers to meet stringent performance requirements while minimizing scrap rates. Simultaneously, diversifying raw material sources-including ramping up recycled aluminum usage-can alleviate exposure to tariff volatility and supply disruptions. By forging strategic alliances with domestic smelters and recyclers, companies can secure a stable, cost-efficient input stream.
Moreover, embracing end-to-end digitalization-from virtual mold simulation to real-time machine health monitoring-will enhance operational agility and reduce downtime. Companies should develop a robust data-driven culture, providing upskilling programs for frontline engineers and operators. Collaborative ventures with OEMs and academic institutions will accelerate alloy innovation, while joint pilots on sustainable casting practices can position participants as preferred partners in zero-emission vehicle programs. Finally, executives are advised to evaluate their global footprint, balancing nearshore expansions in low-tariff zones with strategic presence in high-growth regions, ensuring resilience and responsiveness to shifting commercial vehicle and passenger car demands.
Transparent and Rigorous Research Methodology Ensures Credibility and Reliability of Transmission Case Aluminum Die Casting Market Insights
The insights presented in this report are underpinned by a rigorous research methodology designed to deliver reliable, objective findings. The process commenced with an exhaustive review of industry publications, technical papers, and patent filings to map emerging alloy developments and process innovations. Concurrently, detailed company profiles and financial disclosures were analyzed to gauge strategic initiatives and investment patterns. Primary research involved in-depth interviews with senior executives, metallurgical experts, and production engineers from OEMs, tier-one suppliers, and foundries across key global markets.
To ensure data integrity, triangulation techniques were applied by cross-verifying information from multiple independent sources. Quantitative metrics were compiled from customs databases, trade associations, and regulatory filings to assess tariff impacts and production volumes. Qualitative insights were enriched through roundtable discussions with academic researchers specializing in materials science and sustainable manufacturing. The cumulative research framework was reviewed by an external advisory panel, comprising industry veterans and policy analysts, ensuring that the report’s conclusions accurately reflect the complex realities of the transmission case aluminum die casting sector.
Explore AI-driven insights for the Automotive Transmission Case Aluminum Die Casting market with ResearchAI on our online platform, providing deeper, data-backed market analysis.
Ask ResearchAI anything
World's First Innovative Al for Market Research
Synthesis of Critical Findings Highlights Strategic Imperatives and Future Trajectories in Automotive Transmission Case Aluminum Die Casting Industry
The evolution of the transmission case aluminum die casting industry is defined by a confluence of technological, economic, and regulatory forces. The transition to electrified drivetrains is accelerating innovation in alloy design and process automation, with both high-pressure and specialized casting methods playing critical roles. At the same time, the implementation of 2025 United States tariffs has prompted strategic realignments in sourcing, manufacturing footprints, and partnership frameworks, underscoring the importance of supply chain agility.
Segment-level analysis reveals unique performance and cost drivers across transmission types, process technologies, and vehicle applications, enabling stakeholders to tailor their approaches to specific market demands. Regional disparities across the Americas, EMEA, and Asia-Pacific further highlight the necessity of localized strategies and collaborative ecosystem development. As industry leaders pursue advanced die casting capabilities and sustainable practices, proactive investments in digitalization, workforce development, and cross-sector partnerships will be paramount. Collectively, these insights lay the groundwork for informed decision-making and strategic planning, charting a clear path toward resilient growth and innovation in the evolving transmission case manufacturing landscape.
This section provides a structured overview of the report, outlining key chapters and topics covered for easy reference in our Automotive Transmission Case Aluminum Die Casting market comprehensive research report.
- Preface
- Research Methodology
- Executive Summary
- Market Overview
- Market Dynamics
- Market Insights
- Cumulative Impact of United States Tariffs 2025
- Automotive Transmission Case Aluminum Die Casting Market, by Transmission Type
- Automotive Transmission Case Aluminum Die Casting Market, by Process Technology
- Automotive Transmission Case Aluminum Die Casting Market, by Vehicle Type
- Americas Automotive Transmission Case Aluminum Die Casting Market
- Europe, Middle East & Africa Automotive Transmission Case Aluminum Die Casting Market
- Asia-Pacific Automotive Transmission Case Aluminum Die Casting Market
- Competitive Landscape
- ResearchAI
- ResearchStatistics
- ResearchContacts
- ResearchArticles
- Appendix
- List of Figures [Total: 24]
- List of Tables [Total: 290 ]
Unlock Comprehensive Insights and Drive Strategic Growth in Transmission Case Aluminum Die Casting with Direct Access to In-Depth Market Report
To secure the full report and gain an unparalleled competitive edge, reach out to Ketan Rohom, Associate Director, Sales & Marketing at 360iResearch. His expertise in guiding organizations through complex market landscapes will ensure you harness the insights needed to optimize your transmission case die casting strategies, mitigate emerging risks, and capitalize on evolving opportunities. Engage directly with Ketan Rohom to tailor a solutions package that aligns with your strategic objectives and unlocks the actionable intelligence required for sustained growth. Elevate your decision-making and stay ahead of the curve by investing in the comprehensive analysis and data-driven recommendations provided in the full market research report.
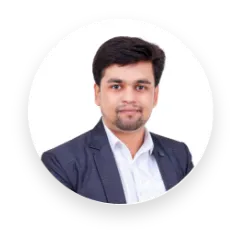
- When do I get the report?
- In what format does this report get delivered to me?
- How long has 360iResearch been around?
- What if I have a question about your reports?
- Can I share this report with my team?
- Can I use your research in my presentation?