Introduction to the Automotive Welding Production Line Market
The automotive welding production line stands at the heart of vehicle manufacturing, shaping the strength, safety, and performance of every car, truck, and commercial vehicle on the road. As demand for lightweight designs, increased fuel efficiency, and advanced safety features accelerates, welding technologies evolve to meet these stringent requirements. High-strength steels, aluminum alloys, and novel composite materials drive innovation in welding equipment, processes, and materials science. Meanwhile, global supply chain dynamics, regulatory frameworks, and shifting trade policies influence strategic priorities across automotive OEMs, suppliers, and equipment manufacturers.
In this dynamic environment, stakeholders must integrate cutting-edge technologies such as robotic automation, laser welding, and digital monitoring systems to enhance precision, reduce cycle times, and ensure repeatable quality. This executive summary provides an authoritative overview of market shifts, regulatory impacts, segmentation insights, regional dynamics, and competitive strategies that define the current landscape. By distilling critical trends and actionable recommendations, this analysis empowers decision-makers to optimize investments, streamline operations, and achieve sustainable growth in an increasingly complex automotive ecosystem.
Transformative Shifts Reshaping Welding Production Lines
The automotive welding sector has undergone transformative shifts driven by rapid technological advances and evolving market demands. First, robotic automation has redefined production efficiency: intelligent welding robots equipped with advanced vision systems now perform complex welds with consistent accuracy and minimal human intervention. This surge in automation not only reduces labor costs but also enhances worker safety by relocating personnel away from hazardous fumes and high-temperature environments.
Second, digitalization and Industry 4.0 principles are reshaping quality control and process optimization. Real-time data analytics enable predictive maintenance of welding fixtures and robots, minimizing downtime and maximizing throughput. Moreover, integrated software platforms facilitate seamless collaboration between design, engineering, and production teams, accelerating product development cycles.
Third, sustainability considerations are driving adoption of energy-efficient welding processes and eco-friendly consumables. Fiber laser welding, for example, offers lower energy consumption and minimal distortion compared to traditional CO2 lasers. Additionally, new shielding gas mixtures and filler materials reduce greenhouse gas emissions without compromising weld integrity.
Together, these transformative forces create a competitive landscape where agility, innovation, and digital mastery determine market leadership.
Assessing the 2025 U.S. Tariff Impact on Welding Operations
The implementation of new tariff measures on steel, aluminum, and related welding equipment in 2025 has introduced significant challenges across North American supply chains. Tariffs imposed on imported raw materials have elevated input costs for advanced high-strength steel, aluminum alloys, and specialty consumables used in arc, laser, seam, and spot welding processes. As a result, manufacturers face margin pressure and must explore alternative sourcing strategies.
Furthermore, equipment suppliers reliant on cross-border component flows experience lead-time disruptions, prompting a reevaluation of near-shoring and on-shore manufacturing options. Some OEMs have responded by establishing local coating, fabrication, and subassembly centers to mitigate tariff exposure and stabilize production schedules.
In addition, higher material costs have accelerated the shift toward process optimization and waste reduction. Welding lines are integrating automated sensing and closed-loop feedback systems to ensure first-pass yield, reduce rework, and conserve expensive materials. Collaborative efforts between suppliers and end users focus on redesigning joint geometries and welding parameters to maintain structural integrity while minimizing resource utilization.
Overall, these trade policy changes underscore the necessity for flexible production networks and strategic partnerships in navigating an increasingly protectionist environment.
Key Segmentation Insights Guiding Strategic Investments
Detailed segmentation analysis reveals the nuanced drivers of growth and adoption within the automotive welding landscape. Based on technology type, arc welding remains a mainstay-comprising metal inert gas welding for high-speed applications and tungsten inert gas welding for precision tasks-while laser welding gains traction through CO₂ systems and fiber laser variants that deliver superior energy efficiency. Seam welding predominantly leverages resistance seam machines for continuous, leak-proof joints, and spot welding employs both laser spot and resistance spot methods depending on joint complexity.
Material type further refines market dynamics: advanced high-strength steel, including complex phase and dual-phase grades, meets structural requirements for lightweight designs, while aluminum alloys-both heat-treatable and non-heat-treatable-address weight reduction targets. Traditional steels such as high-strength low-alloy and stainless grades continue to serve chassis and structural components where corrosion resistance and toughness are paramount.
Process segmentation distinguishes automated welding-which encompasses both machine-driven and robotic cells-from manual welding methods like gas tungsten arc welding and shielded metal arc welding used for specialized repairs and low-volume runs. This duality enables manufacturers to balance throughput with customization.
Application insights highlight the importance of automotive components-spanning body panels, chassis members, and engine parts-alongside fabrication tasks that cover non-structural assemblies and heavy structural subassemblies. End-user segmentation captures aftermarket activities such as performance modifications and maintenance repairs, as well as original equipment manufacturing for commercial vehicles and passenger cars.
Finally, welding equipment type segmentation underscores the roles of fixtures-both clamping and positioner-and robotics, including articulated arms for complex geometries and collaborative robots for flexible cell integration. Together, these six segmentation dimensions guide strategic planning by aligning technology investments with material, process, application, and end-user requirements.
This comprehensive research report categorizes the Automotive Welding Production Line market into clearly defined segments, providing a detailed analysis of emerging trends and precise revenue forecasts to support strategic decision-making.
- Technology Type
- Material Type
- Welding Process
- Application
- End User
- Welding Equipment Type
Key Regional Insights Influencing Market Trajectories
Regional dynamics shape competitive priorities and adoption rates across the globe. In the Americas, strong automotive production hubs in the United States and Mexico drive demand for high-precision welding solutions to support assembly plants and subassembly centers. Manufacturers increasingly invest in integrated robotic cells near OEM facilities to reduce logistics costs and comply with evolving trade regulations.
The Europe, Middle East & Africa region benefits from longstanding engineering expertise and advanced manufacturing infrastructure. Germany and other Western European nations lead in developing high-power laser welding systems and adaptive fixture technologies. Simultaneously, growth in the Middle East and North Africa is fueled by expanding commercial vehicle and aftersales markets, creating opportunities for modular welding lines and mobile repair units.
Across Asia-Pacific, rapid industrialization and electrification strategies in China, Japan, and India fuel investments in automated welding platforms. Domestic equipment suppliers collaborate with global technology firms to localize high-value laser and robotic welding solutions, meeting the region’s emphasis on cost-efficiency and scale. These regional trends underscore the importance of tailoring product portfolios and service models to diverse operational and regulatory environments.
This comprehensive research report examines key regions that drive the evolution of the Automotive Welding Production Line market, offering deep insights into regional trends, growth factors, and industry developments that are influencing market performance.
- Americas
- Asia-Pacific
- Europe, Middle East & Africa
Competitive Company Insights and Technology Leadership
Leading equipment manufacturers and material suppliers shape the competitive landscape through continuous innovation and global network expansion. ABB Group leverages cross-industry robotics expertise to deliver integrated welding solutions with advanced sensing and control. Air Liquide S.A. focuses on custom gas blends and process analytics to optimize weld quality and reduce emissions. Cloos Robotic Welding GmbH differentiates through modular cell designs and digital twin simulations that accelerate commissioning and scale-up.
Daihen Corporation and Yaskawa Electric Corporation integrate motion control and servo technologies to enhance arc stability in MIG, TIG, and resistance welding. ESAB Corporation and Lincoln Electric Holdings, Inc. maintain strong positions in consumables and power source development, driving productivity gains across manual and automated processes. FANUC Corporation and KUKA AG consistently expand their robotic portfolios, adding collaborative and high-payload options for heavy structural welding.
Fronius International GmbH and Kemppi Oy emphasize software-defined welding processes, enabling seamless data exchange and quality traceability. Hobart Brothers LLC and Miller Electric Mfg. LLC supply comprehensive arc solutions for aftermarket and low-volume applications. Panasonic Corporation’s laser systems deliver high-speed precision, while Voestalpine AG and Saarstahl AG supply advanced steel grades tailored for welding. Meanwhile, The Linde Group and Lokmart Products International provide specialty gases and welding fixtures, respectively, completing an ecosystem of end-to-end welding excellence.
This comprehensive research report delivers an in-depth overview of the principal market players in the Automotive Welding Production Line market, evaluating their market share, strategic initiatives, and competitive positioning to illuminate the factors shaping the competitive landscape.
- ABB Group
- Air Liquide S.A.
- Cloos Robotic Welding GmbH
- Daihen Corporation
- ESAB Corporation
- FANUC Corporation
- Fronius International GmbH
- Hobart Brothers LLC
- ITW Welding
- Kemppi Oy
- KUKA AG
- Lincoln Electric Holdings, Inc.
- Lokmart Products International
- Miller Electric Mfg. LLC (A subsidiary of Illinois Tool Works Inc.)
- Panasonic Corporation
- Saarstahl AG
- The Linde Group
- Voestalpine AG
- Yaskawa Electric Corporation
Actionable Recommendations for Future-Ready Production
To navigate this complex market, industry leaders should adopt a multi-pronged strategic approach:
- Prioritize modular automation by deploying flexible robotic welding cells that can be reconfigured for different vehicle platforms, reducing capital risk and supporting rapid product changeovers.
- Develop digital integration roadmaps that connect welding equipment, quality inspection systems, and enterprise resource planning platforms to enable predictive maintenance and real-time analytics.
- Establish regional production hubs through partnerships or joint ventures to mitigate trade policy risks and ensure just-in-time supply of critical welding consumables and equipment components.
- Drive collaborative innovation with material suppliers to co-develop consumables and joint designs that optimize weld quality while minimizing distortion and filler usage.
- Invest in workforce upskilling programs focused on advanced welding techniques, robotic programming, and digital diagnostics to ensure a talent pipeline capable of sustaining high-tech operations.
By executing these initiatives, manufacturers and OEMs can achieve a resilient, efficient, and future-ready welding production capability.
Explore AI-driven insights for the Automotive Welding Production Line market with ResearchAI on our online platform, providing deeper, data-backed market analysis.
Ask ResearchAI anything
World's First Innovative Al for Market Research
Concluding Perspectives on Welding Production Evolution
The evolution of automotive welding production lines underscores the interplay between technology, materials, and global trade dynamics. Stakeholders who embrace automation, digitalization, and collaborative innovation will bolster their competitive edge. Meanwhile, strategic responses to tariff environments and regional variations will define resilience and operational agility. As welding processes become more sophisticated, continuous alignment of segmentation insights with market demands remains essential for sustained growth and performance excellence.
This section provides a structured overview of the report, outlining key chapters and topics covered for easy reference in our Automotive Welding Production Line market comprehensive research report.
- Preface
- Research Methodology
- Executive Summary
- Market Overview
- Market Dynamics
- Market Insights
- Cumulative Impact of United States Tariffs 2025
- Automotive Welding Production Line Market, by Technology Type
- Automotive Welding Production Line Market, by Material Type
- Automotive Welding Production Line Market, by Welding Process
- Automotive Welding Production Line Market, by Application
- Automotive Welding Production Line Market, by End User
- Automotive Welding Production Line Market, by Welding Equipment Type
- Americas Automotive Welding Production Line Market
- Asia-Pacific Automotive Welding Production Line Market
- Europe, Middle East & Africa Automotive Welding Production Line Market
- Competitive Landscape
- ResearchAI
- ResearchStatistics
- ResearchContacts
- ResearchArticles
- Appendix
- List of Figures [Total: 28]
- List of Tables [Total: 938 ]
Connect with Ketan Rohom to Secure Your Comprehensive Report
For comprehensive insights and tailored guidance on optimizing your automotive welding operations, contact Ketan Rohom (Associate Director, Sales & Marketing) to acquire the full market research report. Gain the strategic intelligence needed to drive decision-making and secure a leadership position in the evolving welding landscape.
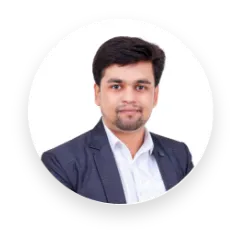
- When do I get the report?
- In what format does this report get delivered to me?
- How long has 360iResearch been around?
- What if I have a question about your reports?
- Can I share this report with my team?
- Can I use your research in my presentation?