The Battery Production Machine Market size was estimated at USD 16.38 billion in 2024 and expected to reach USD 19.30 billion in 2025, at a CAGR 18.18% to reach USD 44.63 billion by 2030.

Navigating the Next Frontier in Battery Production
As industries embrace electrification, the pressure to optimize every aspect of battery manufacturing intensifies. Sophisticated machines now form the backbone of production lines, enabling manufacturers to meet surging demand for energy storage solutions. In this landscape, innovation in assembly line automation, precision calendering, seamless coating processes, and advanced cutting and slitting equipment ensures that quality and throughput remain at the forefront of competitive advantage.
In parallel, cutting-edge drying systems and electrode stacking or winding machines have emerged as pivotal investments to enhance consistency and reduce cycle times. Electrolyte filling units, formation and testing platforms, rigorous quality inspection setups, and reliable sealing machines complete the ecosystem that drives operational excellence. This interconnected machinery network not only dictates production capacity but also influences unit economics, safety standards, and sustainability goals.
Against a backdrop of rising environmental scrutiny and shifting end-user demands, manufacturers must navigate a complex web of technology choices, regulatory compliance, and supply chain resilience. From advanced lithium-ion cell formats to the resurgence of legacy chemistries, machine tool builders are challenged to refine their portfolios constantly. This report delves into these imperatives, offering executives a comprehensive introduction to the critical factors shaping the future of battery production machinery.
Unfolding Transformations Driving Battery Manufacturing Forward
The battery production landscape has undergone profound shifts driven by technological breakthroughs and evolving market imperatives. Rapid advancements in materials science have propelled solid-state and high-nickel chemistries into the spotlight, demanding machine designs that can accommodate new thickness tolerances and thermal management requirements. At the same time, the push for sustainability has elevated the importance of recycling and disposal equipment, integrating closed-loop processes that reclaim valuable metals and reduce environmental footprints.
Supply chain disruptions have triggered a renaissance in modular and flexible manufacturing systems, enabling rapid reconfiguration of production lines to address fluctuating demand or raw material availability. Companies are investing in digital twins and real-time analytics to simulate production scenarios, optimize maintenance schedules, and improve yield rates. The integration of artificial intelligence and machine vision technologies within quality inspection systems has further advanced defect detection capabilities, ensuring higher throughput with minimal manual intervention.
As industry stakeholders collaborate to establish global standards for safety and performance, machine builders are forging partnerships across research institutions, component suppliers, and end users. These alliances are fostering co-development of next-generation coating chemistries, precision tooling, and smart robotics that can adapt to a broader range of cell formats. By aligning technological innovation with market needs, this transformative wave is reshaping how battery production capacity scales and how excellence is defined.
Assessing the Ripple Effects of US Tariffs in 2025
In 2025, newly applied tariffs on battery manufacturing equipment are expected to generate sweeping effects across the supply chain. Import duties on key production machines increase cost pressures for domestic assemblers who rely on advanced coating machines, calendering systems, and formation test rigs sourced from leading international manufacturers. The immediate result is a recalibration of capital budgets as companies evaluate whether to absorb higher costs, renegotiate vendor agreements, or postpone expansion plans.
The tariff landscape also incentivizes local production of critical machinery components, spurring investments in regional supply networks. Shops specializing in electrostatic coating guns or precision winding spindles are expanding capabilities to offset imported price hikes. Concurrently, some global equipment providers are altering their manufacturing footprints, shifting assembly or subcomponent fabrication to comply with tariff thresholds and preserve competitiveness.
For OEMs that navigate the tariff environment effectively, opportunities arise in offering retrofit programs and upgrade pathways for legacy equipment. By emphasizing modularity and software-driven enhancements, suppliers can position themselves as cost-effective partners in a more protectionist climate. Meanwhile, end users must reassess total cost of ownership models, accounting not only for upfront capital outlays but also for long-term service agreements and potential tariff escalations. Through strategic planning and agile sourcing, stakeholders can turn tariff challenges into catalysts for greater self-sufficiency and innovation.
Unearthing Comprehensive Segmentation Insights for Precise Strategies
Deep understanding of market segmentation enables companies to tailor their product development and go-to-market strategies with precision. Within machine type classifications, demand fluctuates between comprehensive assembly line automation platforms and specialized equipment such as calendering machinery that ensures electrode uniformity. Precision-oriented coating machines coexist with high-capacity drying systems, while niche devices like cutting and slitting tools, electrode stacking or winding apparatus, electrolyte filling systems, formation and testing equipment, quality inspection modules, and sealing machines each play distinct roles in optimizing efficiency and quality at every phase of production.
Technology segments demand differentiated approaches as manufacturers shift focus from traditional lead-acid and nickel-cadmium chemistries toward next-generation lithium-ion variants, nickel-metal hydride formulations, and the emergent solid-state battery platforms. Production process and stage considerations emphasize the need for seamless integration across cell assembly, electrode manufacturing, battery module and pack assembly, battery testing and inspection operations, and end-of-life recycling and disposal services. Adapting machinery to the unique throughput, precision and sustainability requirements of each stage enhances yield and minimizes waste.
End-user industries further refine strategic priorities. Aerospace and defense programs often require bespoke, high-reliability equipment, while the automotive sector demands high-volume, cost-effective solutions. Consumer goods applications prioritize compact, versatile machines, whereas healthcare systems lean on specialized tools for medical devices and wearable healthcare technologies. Industrial applications span material handling equipment and uninterrupted power systems, where equipment uptime and robustness are paramount. By aligning machine innovation with the nuanced needs of these segments, manufacturers can unlock targeted growth pathways and deepen customer partnerships.
This comprehensive research report categorizes the Battery Production Machine market into clearly defined segments, providing a detailed analysis of emerging trends and precise revenue forecasts to support strategic decision-making.
- Machine Type
- Technology
- Production Process/Stage
- End-User Industry
Decoding Regional Dynamics Shaping Battery Production Trends
Regional dynamics critically influence technology adoption, regulatory alignment, and investment priorities in battery production. In the Americas, a resurgence of domestic manufacturing has been propelled by government incentives and infrastructure initiatives that favor near-shore production. Producers in North America are investing heavily in assembly line automation and digital monitoring systems, seeking to safeguard supply chains and reduce lead times through localized equipment sourcing.
Across Europe, Middle East and Africa, stringent environmental standards and ambitious renewable energy targets are catalyzing demand for recycling and disposal machinery alongside conventional production assets. Manufacturers in this region emphasize modular and reconfigurable platforms that can pivot between different battery chemistries as regulatory frameworks evolve. Collaborative research networks spanning universities and private firms also drive co-development of advanced quality inspection and smart robotics solutions.
Asia-Pacific remains the epicenter of battery manufacturing, characterized by large-scale investments in coating, calendering and electrode processing equipment. Leading economies in the region prioritize high-throughput drying systems and electrolyte filling machines to meet the voracious demand from automotive and consumer electronics OEMs. Additionally, emerging markets in Southeast Asia are rapidly expanding capacity for formation and testing equipment, recognizing the value of early-stage process optimization in achieving global competitiveness.
This comprehensive research report examines key regions that drive the evolution of the Battery Production Machine market, offering deep insights into regional trends, growth factors, and industry developments that are influencing market performance.
- Americas
- Europe, Middle East & Africa
- Asia-Pacific
Spotlight on Leading Innovators and Market Trailblazers
A handful of global equipment providers continue to define benchmarks for innovation, reliability and service excellence. These market leaders are distinguished by their broad portfolios that span advanced assembly line automation systems through to precision calendering, coating, cutting, and slitting machines. Their investments in digitalization and predictive maintenance platforms have set new standards for equipment uptime and operational transparency.
Nimble specialized firms, meanwhile, are carving out niches in high-precision sectors such as electrode stacking and winding, as well as in the development of next-generation quality inspection technologies that leverage artificial intelligence and machine vision. By focusing R&D efforts on ultra-fine tolerances and defect analytics, these companies are enabling higher yields and tighter process control for high-performance battery segments.
Collaborative consortia and joint ventures are also reshaping the competitive landscape. Partnerships between machine builders and chemical innovators facilitate co-innovation of tailor-made coating modules and drying systems that align with emerging chemistries. Similarly, alliances with automation and robotics integrators accelerate the deployment of modular production cells that can adapt swiftly to changing cell formats and production scales. As market leaders and agile players converge around open standards and interoperability, customers benefit from an expanded ecosystem of interoperable solutions and service offerings.
This comprehensive research report delivers an in-depth overview of the principal market players in the Battery Production Machine market, evaluating their market share, strategic initiatives, and competitive positioning to illuminate the factors shaping the competitive landscape.
- Aero Incorpration
- ANDRITZ AG
- BREYER Maschinenfabrik GmbH
- Bühler AG
- Condair Group
- Dürr Aktiengesellschaft
- FISAIR S.L.U.
- Fluidomatic
- Foshan Golden Milky Way Intelligent Equipment Co., Ltd.
- Guangdong Lyric Robot Automation Co., Ltd.
- Hakusan Corporation
- Hitachi, Ltd.
- Hymson Laser Technology Group Co.,Ltd.
- Kampf GmbH
- Lead Intelligent Equipment Co., Ltd.
- Maestrotech Systems Private Limited
- Manz AG
- MS Fulodo
- Munters AB
- Nagano Automation Co.,Ltd.
- Nordson Corporation
- Pahwa Group
- Raunik Greentech Private Limited
- Rosendahl Nextrom GmbH
- Shenzhen Yinghe Technology Co.,Ltd.
- Super Components Engineering(Dongguan) Ltd.
- Toray Industries, Inc.
- UNIK Techno Systems Pvt. Ltd.
- Xiamen Acey New Energy Technology Co.,Ltd.
- Xiamen Tmax Battery Equipments Limited
- Xiamen TOB New Energy Technology Co., Ltd.
Strategic Imperatives to Shape Competitive Advantage
Industry leaders should prioritize modular equipment architectures that enable rapid reconfiguration of production lines in response to evolving chemistries and market demands. By investing in open-platform digital twins and analytics frameworks, companies can simulate process changes, predict maintenance needs, and optimize throughput before committing capital to physical deployments.
To mitigate geopolitical and tariff-related risks, organizations must cultivate diversified supply chains for both machinery and critical components. Engaging with local fabrication partners for subassemblies and establishing near-shore service centers will reduce lead times, limit exposure to import duties, and enhance customer responsiveness. Concurrently, providers can differentiate through retrofit and upgrade offerings that extend the service life of existing assets, creating new revenue streams and deepening customer relationships.
A relentless focus on sustainability will unlock competitive benefits. Incorporating energy-efficient motors, waste heat recovery systems, and recyclable material handling solutions not only reduces operational carbon footprints but also aligns with the rising expectations of regulators and end users. By embedding circular economy principles into machine design and partnering with specialized recycling service providers, equipment makers will fortify their value propositions and drive long-term customer loyalty.
Rigorous Methodological Framework Underpinning Our Analysis
Our analysis integrates a multi-pronged research approach, beginning with an extensive review of primary and secondary sources. In-depth interviews with C-level executives, equipment engineers, and procurement specialists provided firsthand perspectives on technology adoption, operational benchmarks, and emerging pain points. These qualitative insights were complemented by rigorous examination of technical journals, industry white papers, patent filings, and regulatory disclosures.
We mapped the competitive landscape through detailed profiling of leading machine vendors, niche innovators, and collaborative joint ventures. Each company’s product portfolio, strategic alliances, and service capabilities were assessed to gauge relative strengths and identify gaps in the market. Segmentation analyses were developed by cross-referencing machine type, technology chemistry, production stage, and end-user requirements to reveal nuanced demand patterns.
Regional assessments drew on trade data, government incentive programs, and environmental regulatory frameworks to capture the influence of policy on equipment investment. Tariff implications were examined through scenario modeling that considered duty structures, local content thresholds, and shifting trade agreements. Collectively, this methodological framework ensures that our findings are grounded in both empirical evidence and real-world practitioner experience.
Explore AI-driven insights for the Battery Production Machine market with ResearchAI on our online platform, providing deeper, data-backed market analysis.
Ask ResearchAI anything
World's First Innovative Al for Market Research
Synthesis of Core Findings and Industry Implications
The battery production machinery sector stands at a pivotal juncture, shaped by technological innovation, shifting trade policies, and escalating demands for sustainability. Advanced automation, precision tooling, and digital integration are no longer optional but essential components of competitive differentiation. Manufacturers that align their machine investments with targeted segmentation strategies-spanning machine types, battery chemistries, production stages, and end-user applications-stand to capture disproportionate value.
Regional nuances underscore the importance of tailored approaches, whether it is leveraging localized manufacturing incentives in the Americas, embracing modular reconfigurability amid European environmental mandates, or scaling up throughput in Asia-Pacific’s high-volume hubs. Meanwhile, the cumulative impact of tariffs and trade dynamics calls for resilient supply chains and proactive retrofit programs.
Ultimately, success will be determined by the ability to anticipate market shifts, forge collaborative ecosystems, and embed sustainability at every level of machine design and operation. This comprehensive synthesis of core findings equips decision makers with the insights necessary to navigate complexity, capitalize on emerging opportunities, and drive the next wave of growth in battery production machinery.
This section provides a structured overview of the report, outlining key chapters and topics covered for easy reference in our Battery Production Machine market comprehensive research report.
- Preface
- Research Methodology
- Executive Summary
- Market Overview
- Market Dynamics
- Market Insights
- Cumulative Impact of United States Tariffs 2025
- Battery Production Machine Market, by Machine Type
- Battery Production Machine Market, by Technology
- Battery Production Machine Market, by Production Process/Stage
- Battery Production Machine Market, by End-User Industry
- Americas Battery Production Machine Market
- Europe, Middle East & Africa Battery Production Machine Market
- Asia-Pacific Battery Production Machine Market
- Competitive Landscape
- ResearchAI
- ResearchStatistics
- ResearchContacts
- ResearchArticles
- Appendix
- List of Figures [Total: 24]
- List of Tables [Total: 292 ]
Secure Your Access to Critical Battery Market Intelligence
For organizations poised to secure a leading edge in the battery production sector, accessing the full market research report presents an unmissable opportunity. Reach out to Ketan Rohom (Associate Director, Sales & Marketing at 360iResearch) to explore tailored insights, in-depth analysis, and practical recommendations that will empower your strategic decision making. Engage today to unlock critical data on emerging trends, competitive dynamics, and regulatory developments, all crafted to elevate your business trajectory.
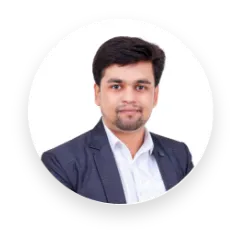
- How big is the Battery Production Machine Market?
- What is the Battery Production Machine Market growth?
- When do I get the report?
- In what format does this report get delivered to me?
- How long has 360iResearch been around?
- What if I have a question about your reports?
- Can I share this report with my team?
- Can I use your research in my presentation?