Introduction to the Beryllium Copper Master Alloy Market Landscape
Since its discovery in the early 19th century, beryllium copper master alloy has emerged as an indispensable material across high-performance sectors. Its unique combination of high electrical and thermal conductivity, superior tensile strength, outstanding fatigue resistance and excellent corrosion resilience positions it as a critical enabler for demanding applications. Moreover, the alloy’s ability to withstand extreme temperature variations while maintaining dimensional stability has driven its adoption in precision components.
In aerospace, its integration into electrical systems and landing gear ensures reliability in safety-critical environments. Within automotive manufacturing, electrical connectors, engine components and heat exchangers benefit from the alloy’s thermal efficiency and mechanical robustness. The electronics industry leverages its formability to produce connectors, terminals, shields and switches that support IoT and 5G infrastructures. Simultaneously, energy projects employ beryllium copper master alloy in oil and gas drilling assemblies and wind turbine components to optimize performance under harsh conditions. Industrial uses in plastic molds and welding components capitalize on its wear resistance, while telecommunication networks depend on connectors and fiber optic components for uninterrupted data transmission.
As global trends in electrification, miniaturization and sustainability accelerate, this master alloy remains a strategic material. Given the alloy’s critical role in advancing next-generation technologies and stringent regulatory landscapes governing beryllium usage, stakeholders require comprehensive insights to navigate supply chain complexities, optimize production processes and align with evolving industry standards. This executive summary provides a concise yet thorough foundation for informed decision-making and strategic planning in a rapidly evolving marketplace.
Transformative Shifts Reshaping the Beryllium Copper Master Alloy Sector
Recent years have witnessed transformative shifts reshaping the beryllium copper master alloy sector. Technological advancements in additive manufacturing and precision machining have unlocked complex geometries and tighter tolerances, enabling designers to exploit the alloy’s performance envelope. In addition, digital twins and process simulation tools enhance production efficiency by predicting material behavior under various conditions, reducing trial-and-error cycles.
Sustainability imperatives and more stringent environmental regulations have also catalyzed change. Manufacturers increasingly seek closed-loop recycling to recover beryllium copper scrap, thereby minimizing raw material consumption and mitigating exposure risks. Regulatory bodies in North America, Europe and Asia-Pacific continue to refine guidelines on workplace safety and alloy content, compelling producers to invest in cleaner processes and employee training programs.
Furthermore, global supply chain disruptions and geopolitical dynamics have driven firms to diversify sourcing strategies and bolster onshore capacities. Partnerships between alloy producers and key end users, especially in the automotive and aerospace verticals, foster collaborative research into next-generation formulations with reduced beryllium content. These transformative shifts set the stage for deeper analysis of tariff impacts, segmentation performance and regional opportunities presented in the following sections.
Cumulative Impact of United States Tariffs 2025 on Beryllium Copper Supply Chain
In 2025, the United States implemented revised tariffs on beryllium copper master alloy imports as part of broader trade measures aimed at securing critical mineral supply chains. These tariff adjustments, targeting key exporting nations, have elevated import duties, thereby increasing landed costs for downstream manufacturers. As a direct consequence, companies reliant on imported master alloy have experienced margin compression and cost overruns.
Domestic producers have seized this opportunity to enhance capacity, invest in advanced melting and alloying technologies and renegotiate long-term contracts with end users. However, while reshoring initiatives reduce exposure to import levies, they also introduce challenges related to scale-up timelines, capital expenditure requirements and workforce training. In parallel, some manufacturers have shifted procurement toward tariff-exempt countries or reclassified alloy grades to mitigate duty impacts, though these strategies often entail lead time extensions and quality validation cycles.
End-use industries such as aerospace and automotive have begun absorbing a portion of the increased material costs, passing them along value chains through revised pricing agreements. At the same time, aftermarket repair services are adapting pricing models to balance profitability against service continuity. As tariff regimes continue to evolve, stakeholders must maintain agile sourcing networks and engage in active dialogue with trade authorities to anticipate policy adjustments and safeguard supply reliability. As we examine the segmentation landscape in the next section, it becomes clear how tariff pressures intersect with specific market segments and influence strategic priorities.
Key Segmentation Insights Across Application, Industry, Form, Process, End Use and Purity
A detailed examination of market segments reveals distinct growth trajectories and strategic imperatives across application verticals, industry channels, product forms, manufacturing processes, end-use categories and purity tiers. Application analysis indicates strong momentum in aerospace electrical systems and landing gear spurred by fleet modernization, while automotive segments encompassing electrical connectors, engine components and heat exchangers gain traction from vehicle electrification and advanced thermal management. Electronic connectors, terminals, housing and shields, alongside switches, are scaling with IoT proliferation and 5G deployments. Energy uses in oil and gas drilling and wind turbine components leverage fatigue resistance and conductivity, whereas industrial plastic molds and welding components benefit from wear resistance. Telecommunication connectors and fiber optic components support expanding network infrastructure.
In channel dynamics, original equipment manufacturers-specifically automotive and electronic device producers-seek alloy customization and integrated supply partnerships, while aftermarket repair and replacement services concentrate on legacy equipment support and spare parts. Bars dominate in precision machining, ingots feed large-scale castings and wires serve high-density interconnect applications. Process-wise, die casting and sand casting enable complex shapes, cold forming and extrusion enhance mechanical performance and machining guarantees dimensional accuracy. End-use categories highlight commercial applications in automobile manufacturing and consumer electronics, construction demands for building materials and infrastructure components, defense requirements in aerospace components and military vehicles, and healthcare needs in medical devices and surgical instruments. Finally, purity level segmentation contrasts high-purity grades for critical applications against standard grades for broader industrial use. These insights guide resource prioritization, product development and market positioning strategies.
This comprehensive research report categorizes the Beryllium Copper Master Alloy market into clearly defined segments, providing a detailed analysis of emerging trends and precise revenue forecasts to support strategic decision-making.
- Application
- Industry Type
- Form
- Manufacturing Process
- End Use
- Purity Level
Regional Dynamics Driving the Global Beryllium Copper Master Alloy Market
Regional analysis underscores divergent growth patterns and strategic priorities across the Americas, Europe, Middle East & Africa and Asia-Pacific. In the Americas, strong aerospace and automotive sectors in the United States and Canada drive robust demand for beryllium copper master alloy, with reshoring initiatives and tariff policies encouraging domestic capacity expansion. Mexico’s manufacturing clusters also benefit from near-shore advantages, supporting supply chain resilience and just-in-time delivery models.
Across Europe, Middle East & Africa, traditional automotive hubs in Germany, France and the United Kingdom are integrating electrification and Industry 4.0 practices, elevating demand for high-performance alloys. Meanwhile, oil-rich economies in the Middle East invest in renewable energy infrastructure that leverages beryllium copper components for wind turbines and drilling operations. Emerging markets in Africa present untapped potential for telecommunication network build-outs and defense modernization programs.
Asia-Pacific remains the largest regional consumer, with China leading in production and consumption across electronics, renewable energy and automotive applications. Japan and South Korea continue to innovate in precision components and advanced manufacturing processes, while India’s rapid urbanization and healthcare sector growth fuel demand for construction materials, medical devices and surgical instruments manufactured from beryllium copper master alloy. Collectively, these regional dynamics shape global trade flows, investment patterns and competitive positioning.
This comprehensive research report examines key regions that drive the evolution of the Beryllium Copper Master Alloy market, offering deep insights into regional trends, growth factors, and industry developments that are influencing market performance.
- Americas
- Asia-Pacific
- Europe, Middle East & Africa
Competitive Landscape and Key Company Profiles in Beryllium Copper Master Alloy
The beryllium copper master alloy market features a competitive landscape marked by both global leaders and regional specialists. Aviva Metals distinguishes itself through a focus on sustainable recycling processes and a broad portfolio of alloy grades designed for high-volume manufacturing. Belmont Metals Inc. emphasizes custom alloy formulations and value-added services, catering to niche requirements in aerospace and electronics. China Beryllium Copper Ltd. commands significant production capacity, leveraging vertical integration to secure raw material inputs and cost efficiencies for large-scale applications. Eagle Alloys Corporation has expanded its service offerings with rapid prototyping and qualification support, meeting tight development timelines for automotive and defense clients.
HB Special Alloy Manufacturing Ltd. maintains rigorous quality certifications and advanced process controls to serve safety-critical markets, while IBC Advanced Alloys pioneers ultra-high performance grades for demanding thermal and electrical applications. Materion Brush Inc. and its parent, Materion Corporation, invest heavily in proprietary melting technologies and global service networks to deliver customized alloy solutions. NGK Berylco benefits from its expertise in ceramics partnerships, enhancing composite component capabilities. Xiamen Honglu Tungsten Molybdenum Co. Ltd. and Zhejiang Huacheng Nonferrous Metals Co. Ltd. have broadened their regional footprints, targeting rapidly growing Asia-Pacific demand centers. Collectively, these companies differentiate through technological innovation, capacity expansion, strategic partnerships and commitments to regulatory compliance and employee safety. Understanding their competitive positioning and strategic priorities informs alliance and investment decisions across the value chain.
This comprehensive research report delivers an in-depth overview of the principal market players in the Beryllium Copper Master Alloy market, evaluating their market share, strategic initiatives, and competitive positioning to illuminate the factors shaping the competitive landscape.
- Aviva Metals
- Belmont Metals Inc.
- China Beryllium Copper Ltd.
- Eagle Alloys Corporation
- HB Special Alloy Manufacturing Ltd.
- IBC Advanced Alloys
- Materion Brush Inc.
- Materion Corporation
- NGK Berylco
- Xiamen Honglu Tungsten Molybdenum Co. Ltd.
- Zhejiang Huacheng Nonferrous Metals Co. Ltd.
Actionable Recommendations for Industry Leaders in Beryllium Copper Alloy Sector
Industry leaders can adopt a series of actionable measures to capitalize on emerging opportunities and mitigate risks in the beryllium copper master alloy sector. First, investing in state-of-the-art purification and alloying technologies will enhance product quality, yield improvements and cost efficiency while ensuring compliance with evolving regulatory standards on beryllium exposure. Second, diversifying raw material sourcing across multiple geographic regions and qualifying alternative suppliers will strengthen supply chain resilience against tariff fluctuations and geopolitical disruptions. Third, forging strategic partnerships with automotive, aerospace and electronic original equipment manufacturers accelerates co-development of specialized alloy grades for next-generation applications.
In addition, strengthening closed-loop recycling programs and exploring secondary recovery of scrap material reduces dependency on primary feedstock and aligns with sustainability mandates. Proactively engaging with trade associations and government agencies to anticipate policy changes will enable timely adjustments to pricing structures and sourcing strategies. Embracing digitalization across procurement, production and logistics functions-through real-time tracking, predictive maintenance and process optimization tools-will drive operational efficiency. Finally, prioritizing workforce training on safe handling protocols, continuous improvement methodologies and emerging manufacturing techniques ensures both product integrity and employee safety across the value chain.
Explore AI-driven insights for the Beryllium Copper Master Alloy market with ResearchAI on our online platform, providing deeper, data-backed market analysis.
Ask ResearchAI anything
World's First Innovative Al for Market Research
Conclusion: Navigating Opportunities and Challenges in the Beryllium Copper Market
In summary, the beryllium copper master alloy market is poised at the crossroads of technological innovation, regulatory evolution and shifting trade dynamics. The alloy’s exceptional properties continue to unlock new applications in aerospace, automotive, electronics, energy, industrial and telecommunication segments. Yet, rising environmental and safety regulations, along with evolving tariff regimes, present both challenges and opportunities that require strategic foresight.
A nuanced understanding of application-based demand, industry channel preferences, form factor requirements, manufacturing process advantages, end-use sector drivers and purity considerations is essential for effective market positioning. Regional dynamics further underscore the need for tailored approaches, whether expanding domestic capacities in the Americas, capitalizing on renewable infrastructure investments in Europe, Middle East & Africa, or navigating high-volume production hubs in Asia-Pacific. The competitive landscape, characterized by a mix of recycling experts, custom alloyers and integrated producers, highlights the importance of differentiation through technology, service and sustainability.
By aligning strategic investments, collaborative partnerships and operational excellence initiatives with these insights, stakeholders can navigate uncertainty, drive growth and maintain a competitive edge in a demanding global environment.
This section provides a structured overview of the report, outlining key chapters and topics covered for easy reference in our Beryllium Copper Master Alloy market comprehensive research report.
- Preface
- Research Methodology
- Executive Summary
- Market Overview
- Market Dynamics
- Market Insights
- Cumulative Impact of United States Tariffs 2025
- Beryllium Copper Master Alloy Market, by Application
- Beryllium Copper Master Alloy Market, by Industry Type
- Beryllium Copper Master Alloy Market, by Form
- Beryllium Copper Master Alloy Market, by Manufacturing Process
- Beryllium Copper Master Alloy Market, by End Use
- Beryllium Copper Master Alloy Market, by Purity Level
- Americas Beryllium Copper Master Alloy Market
- Asia-Pacific Beryllium Copper Master Alloy Market
- Europe, Middle East & Africa Beryllium Copper Master Alloy Market
- Competitive Landscape
- ResearchAI
- ResearchStatistics
- ResearchContacts
- ResearchArticles
- Appendix
- List of Figures [Total: 28]
- List of Tables [Total: 857 ]
Call to Action: Engage with Ketan Rohom for a Comprehensive Market Research Report
To gain in-depth analysis, comprehensive data and strategic guidance tailored to the beryllium copper master alloy market, we invite you to engage with Ketan Rohom (Associate Director, Sales & Marketing at 360iResearch). Connect directly to discuss how the full market research report can inform your investment decisions, product development roadmap and supply chain strategy. Act now to secure the actionable insights needed to stay ahead of regulatory shifts, tariff challenges and evolving end-use requirements. Contact Ketan Rohom today to purchase the definitive market research report and position your organization for sustained success.
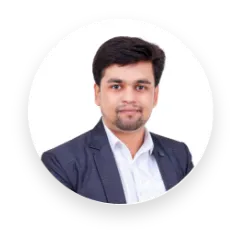
- When do I get the report?
- In what format does this report get delivered to me?
- How long has 360iResearch been around?
- What if I have a question about your reports?
- Can I share this report with my team?
- Can I use your research in my presentation?