The Blow Fill Seal Technology Market size was estimated at USD 484.13 million in 2024 and expected to reach USD 516.77 million in 2025, at a CAGR 6.43% to reach USD 703.69 million by 2030.

Setting the Stage for Evolution in Blow Fill Seal Technology
Blow Fill Seal Technology embodies an advanced manufacturing methodology that seamlessly integrates the formation, filling, and sealing of containers in a single automated operation. By injecting molten polymer into a mold to form a sterile container, immediately filling the container with the desired formulation, and then hermetically sealing it, this process minimizes human intervention and maintains high levels of sterility. Originally developed for pharmaceutical and specialty applications, the technology has expanded its relevance across food and beverage as well as personal care segments, driven by its efficiency, precision, and compliance with stringent regulatory standards.
As regulatory authorities worldwide intensify their focus on contamination risk reduction, manufacturers are increasingly adopting this aseptic packaging solution. The continuous, closed-loop nature of Blow Fill Seal lines enables high throughput while delivering consistent product quality and minimizing waste. Moreover, the flexibility inherent in various machine configurations caters to a broad range of container shapes and sizes, facilitating customization in line with evolving consumer and industrial requirements.
This executive summary offers a comprehensive perspective on the state of Blow Fill Seal technology, highlighting the transformative shifts currently reshaping the market landscape. It examines the implications of recent tariff adjustments, decodes key segmentation criteria such as machine type, packaging material, container geometry, and end-use applications, and distills regional dynamics across major geographic zones. Additionally, it profiles leading industry participants, outlines strategic recommendations for market leaders, and describes the research methodology underpinning the analysis.
Pivotal Transformations Redefining Industry Trajectories
Over the past several years, the Blow Fill Seal landscape has undergone a profound evolution driven by rapid technological advancements and shifting market expectations. Automation has reached new heights as integrated robotics and real-time monitoring systems permeate production lines, enabling manufacturers to achieve unprecedented speeds and precision. At the same time, digital twins and predictive maintenance algorithms have become standard tools for optimizing uptime and reducing operational risks, fostering an environment of continuous improvement.
Simultaneously, regulatory frameworks are tightening global standards for aseptic processing, compelling equipment suppliers to incorporate innovative sterilization protocols and advanced barrier systems. This has coincided with escalating demands for sustainable packaging solutions, prompting the exploration of bio-based polymers and lightweight container designs. Manufacturers are increasingly balancing environmental objectives with performance requirements, advancing research into recyclable and compostable materials that preserve product integrity while reducing carbon footprints.
Personalization trends have also begun to reshape equipment configurations, as end-users seek tailored container geometries for niche applications in cosmetics, specialty beverages, and biopharmaceuticals. The integration of modular machine architectures permits rapid tool changeovers, facilitating efficient transitions between small-batch and large-scale production runs. This agility is further enhanced by smart factory initiatives, where machine-to-machine communication and centralized data analytics drive strategic decision-making and resource allocation.
Taken together, these transformative shifts are redefining competitive parameters within the Blow Fill Seal market. Industry incumbents must navigate a complex matrix of regulatory compliance, sustainability mandates, and evolving consumer preferences, all while leveraging digitalization to maintain operational excellence and foster innovation.
Assessing the Ripple Effects of 2025 U.S. Tariff Adjustments
With the implementation of revised U.S. import tariffs slated for 2025, stakeholders across the Blow Fill Seal spectrum are bracing for material and equipment cost fluctuations that could reshape competitive dynamics. These tariff adjustments target a range of critical inputs, including specialized machinery components as well as primary packaging substrates such as Type I and Type II glass and high-grade polymers like PET, polyethylene, and polypropylene. As duty structures realign, manufacturers are evaluating the downstream implications for production budgets and pricing strategies.
The most immediate effect has been observed in the capital expenditure required for acquiring state-of-the-art inline and rotary filling systems. Duty increases on multi station and six station configurations have driven an uptick in landed costs, compelling engineering teams to reassess procurement timelines and total cost of ownership projections. Furthermore, higher levies on glass containers have introduced additional complexity in balancing material costs with performance characteristics, as suppliers of both Type I and Type II substrates adjust to a more constrained tariff environment.
In response, many producers are intensifying efforts to diversify their supply chain footprint. Strategies include establishing partnerships with regional polymer resin manufacturers, repatriating select packaging operations to tariff-free zones, and exploring vertical integration through in-house material compounding. Concurrently, some enterprises are accelerating negotiations with equipment vendors to explore favorable financing terms or alternative machine configurations that minimize exposure to high-duty categories.
Looking ahead, these tariff-induced cost pressures are likely to catalyze a broader reassessment of business models. Companies that proactively optimize their sourcing strategies, embrace design-for-cost principles, and leverage local manufacturing ecosystems will be positioned to maintain margin resilience and secure competitive advantage in the evolving Blow Fill Seal marketplace.
Decoding Market Segments to Uncover Hidden Opportunities
An in-depth understanding of key segmentation criteria reveals distinct opportunity landscapes within the Blow Fill Seal domain. When evaluating machine typologies, the market divides between inline systems, which include single station modules well-suited for specialized product formats and multi station assemblies engineered for moderate throughput, and rotary platforms that span four station, multi station, and six station architectures designed to deliver high-volume, continuous operation. This dichotomy underscores the importance of aligning equipment selection with production volume requirements and scale-up objectives.
Equally critical is the choice of packaging material, where glass and plastic substrates present divergent performance and cost considerations. Glass offerings bifurcate into Type I borosilicate variants prized for chemical resistance and thermal stability, and Type II soda lime compositions that offer cost efficiencies for less reactive formulations. Plastic alternatives encompass polyethylene terephthalate for clarity and barrier properties, alongside polyethylene and polypropylene, which offer flexibility, impact resistance, and lightweight logistics advantages.
Container typology further refines market targeting, as ampoules, bottles, tubes, and vials each impose unique form-fill-seal challenges. Ampoule configurations demand precise neck metallurgy and controlled thermal sealing, whereas bottles and vials require robust sealing integrity at higher fill volumes. Tube applications emphasize lamination compatibility and closure versatility, broadening the spectrum of design considerations.
The end-use application matrix extends across cosmetics, where product lines in hair care, personal hygiene, and skin care require differentiated dosing and aesthetic attributes; food and beverage, encompassing beverages, condiments, and dairy products that impose varying viscosities and sterility demands; and pharmaceuticals, covering irrigating solutions, lyophilized products, ophthalmic solutions, and parenteral solutions, each governed by stringent regulatory and sterility criteria.
By cross-analyzing these segmentation vectors, industry participants can pinpoint niches where technology adapts most effectively, ensuring that equipment investments, material sourcing, and product development initiatives are precisely aligned with evolving market requisites.
This comprehensive research report categorizes the Blow Fill Seal Technology market into clearly defined segments, providing a detailed analysis of emerging trends and precise revenue forecasts to support strategic decision-making.
- Machine Type
- Packaging Material
- Container Type
- Application
Regional Dynamics Shaping Global Blow Fill Seal Adoption
Within the Americas, the United States stands as a primary driver of Blow Fill Seal adoption, propelled by robust pharmaceutical R&D pipelines and stringent regulatory mandates for aseptic packaging. Canada complements this landscape with incremental gains in specialty cosmetics and nutraceutical lines. Meanwhile, Latin American markets are demonstrating emerging interest, particularly in the beverage sector, where brand differentiation and shelf-life extension underscore the value proposition of automated aseptic filling.
In Europe, Middle Eastern, and African markets, the regulatory environment varies widely but generally trends toward comprehensive directives aimed at contamination control and environmental stewardship. Western European nations leverage advanced infrastructure to integrate smart manufacturing concepts, whereas Eastern European enterprises are increasingly retrofit driven. The Middle East exhibits growing investment in biopharmaceutical production hubs, while African regions are at nascent stages of adoption, focusing primarily on condensed volumes for high-value pharmaceuticals and cosmetics.
Asia-Pacific remains the most dynamic growth frontier for Blow Fill Seal equipment, characterized by expansive food and beverage consumption, burgeoning cosmetic markets, and accelerating pharmaceutical production. China and India lead volume-driven demand, underpinned by domestic packaging material innovations and government incentives for local machinery manufacturing. Japan and South Korea continue to emphasize ultra-sterile parenteral solutions, driving incremental adoption of rotary machine platforms with six station throughput capabilities.
By tailoring market entry strategies to these regional idiosyncrasies-whether through local partnerships, compliance alignment, or technology transfer agreements-equipment suppliers and end-users can effectively capitalize on divergent growth trajectories and regulatory frameworks across global markets.
This comprehensive research report examines key regions that drive the evolution of the Blow Fill Seal Technology market, offering deep insights into regional trends, growth factors, and industry developments that are influencing market performance.
- Americas
- Europe, Middle East & Africa
- Asia-Pacific
Competitive Landscape of Leading Blow Fill Seal Technology Providers
Competition within the Blow Fill Seal sector is marked by a blend of established global original equipment manufacturers and agile regional specialists. The foremost suppliers maintain significant R&D budgets, channeling resources into sterilization advances, predictive maintenance capabilities, and next-generation control systems. Their extensive service networks ensure rapid installation and technical support, reinforcing customer loyalty and facilitating cross-selling of aftermarket parts and digital monitoring subscriptions.
The operational model adopted by these leading vendors emphasizes modularity, enabling customers to scale their operations and retrofit lines without major capital reinvestments. Through targeted acquisitions and joint ventures, they have broadened their geographic footprint, gaining access to emerging markets and bolstering their local manufacturing capacities. In parallel, strategic partnerships with polymer and glass producers have ensured preferential material pricing and co-development of novel container designs.
Conversely, a cohort of regional suppliers has carved out niches by delivering cost-effective machine configurations tailored to localized regulatory and production requirements. These providers often differentiate through rapid lead times and flexible financing structures, appealing to small and medium-sized enterprises seeking to enter the aseptic packaging arena with minimal upfront risk.
Additionally, contract manufacturing organizations and system integrators are playing a more pronounced role, offering turnkey Blow Fill Seal solutions that bundle installation, validation, and operational oversight under unified service agreements. This shift reflects end-user preferences for outsourcing complex aseptic processes in pursuit of operational focus and risk mitigation.
Looking ahead, competitive advantage will hinge on the ability to orchestrate seamless digital ecosystems, from real-time performance analytics to remote servicing capabilities, while expanding aftermarket revenue streams. Businesses that can harmonize technological innovation with customer-centric service models will secure prominent positions in this dynamic market landscape.
This comprehensive research report delivers an in-depth overview of the principal market players in the Blow Fill Seal Technology market, evaluating their market share, strategic initiatives, and competitive positioning to illuminate the factors shaping the competitive landscape.
- Syntegon Technology GmbH
- Rommelag GmbH
- IMA Life S.p.A
- Marchesini Group S.p.A
- MGS Machine Company, Inc.
- OPTIMA packaging group GmbH
- Serac S.A.S
- Harro Höfliger Verpackungsmaschinen GmbH
- Skan AG
- ProMach, Inc.
Strategic Imperatives for Accelerating Market Leadership
Incorporating advanced digital tools across Blow Fill Seal lines is no longer optional but imperative for sustaining competitive advantage. Industry leaders should deploy predictive maintenance systems that leverage sensor data and machine learning algorithms to anticipate component wear and schedule service interventions proactively. Concurrently, the adoption of real-time quality monitoring platforms will enhance process control, ensuring batch consistency and regulatory compliance.
Prioritizing sustainability within the packaging value chain can generate tangible benefits in cost reduction and brand reputation. Investing in research collaborations to develop bio-based polymers and recyclable container formats will align product portfolios with evolving environmental standards and consumer expectations. Equally, embracing lightweight container designs and optimized mold geometries can mitigate material usage without compromising barrier properties.
Diversifying supply chains and building regional sourcing hubs can shield operations from tariff volatility and logistical disruptions. Establishing strategic partnerships with local polymer compounders and glass manufacturers will secure preferential access to key substrates and facilitate rapid response to market fluctuations. Furthermore, nearshoring critical fabrication processes can reduce lead times while delivering cost efficiencies.
Modular and scalable machine architectures offer a pathway to agility in product changeovers and capacity expansions. By selecting platforms that provide seamless conversion between single station, multi station, and rotary configurations, manufacturers can effectively balance the needs of small-batch pilot runs and high-speed production campaigns.
Finally, enhancing after-sales support through value-added services such as remote diagnostics, operator training modules, and consumables management programs can unlock recurring revenue streams and foster deeper customer relationships. Strategic alliances with technology partners and service firms will further amplify these offerings, bolstering market leadership and long-term growth.
Methodological Approach Underpinning Our Market Analysis
This analysis is grounded in a structured research framework that integrates both qualitative insights and quantitative rigor to deliver a holistic view of the Blow Fill Seal technology market. The primary objective was to identify key industry drivers, assess market segmentation dynamics, evaluate regional trajectories, and benchmark leading participants against rigorous competitive criteria.
Primary research initiatives included in-depth interviews with equipment manufacturers, material suppliers, contract packagers, and end-user decision-makers across pharmaceutical, food and beverage, and cosmetics verticals. These discussions yielded firsthand perspectives on operational challenges, emerging demand patterns, regulatory hurdles, and technology adoption roadmaps, providing a nuanced understanding of market sentiment and strategic imperatives.
Secondary research comprised exhaustive reviews of public and proprietary databases, industry association reports, financial filings of major equipment vendors, and peer-reviewed technical publications. This phase also involved an analysis of tariff databases and government regulations to ascertain the impact of trade policy changes on raw material sourcing and capital equipment procurement.
Data triangulation procedures were applied throughout the study to reconcile discrepancies between disparate information sources and ensure reliability. Statistical models and comparative benchmarking techniques were employed to validate market segmentation frameworks and regional forecasts. While every effort has been made to maintain accuracy and objectivity, stakeholders should consider the intrinsic limitations of market research, including data latency and potential shifts in regulatory or macroeconomic conditions.
Explore AI-driven insights for the Blow Fill Seal Technology market with ResearchAI on our online platform, providing deeper, data-backed market analysis.
Ask ResearchAI anything
World's First Innovative Al for Market Research
Concluding Perspectives on the Future of Blow Fill Seal Tech
The Blow Fill Seal technology market stands at a critical juncture, marked by accelerating digitization, stringent aseptic processing mandates, and a growing emphasis on sustainable packaging solutions. Recent tariff adjustments have further underscored the need for supply chain resilience and strategic sourcing decisions. These converging forces are reshaping equipment investment strategies, driving manufacturers and end-users to reevaluate their operational frameworks.
A comprehensive segmentation lens reveals differentiated opportunities across machine typologies, container formats, material substrates, and end-use verticals. Regional landscapes offer varied growth trajectories, with each geographic zone presenting unique regulatory, logistical, and consumer demand factors. Meanwhile, the competitive arena is defined by the interplay between global original equipment manufacturers, specialized regional providers, and integrated service partners, all vying to deliver the most responsive, cost-effective solutions.
Moving forward, stakeholders who align their technology roadmaps with modular machine designs, invest in advanced data analytics, and cultivate collaborative partnerships across the value chain will be best positioned to capture emerging market share. The capacity to adapt to shifting regulatory requirements, material innovations, and consumer preferences will determine the sustainability of competitive advantage in this dynamic sector.
This section provides a structured overview of the report, outlining key chapters and topics covered for easy reference in our Blow Fill Seal Technology market comprehensive research report.
- Preface
- Research Methodology
- Executive Summary
- Market Overview
- Market Dynamics
- Market Insights
- Cumulative Impact of United States Tariffs 2025
- Blow Fill Seal Technology Market, by Machine Type
- Blow Fill Seal Technology Market, by Packaging Material
- Blow Fill Seal Technology Market, by Container Type
- Blow Fill Seal Technology Market, by Application
- Americas Blow Fill Seal Technology Market
- Europe, Middle East & Africa Blow Fill Seal Technology Market
- Asia-Pacific Blow Fill Seal Technology Market
- Competitive Landscape
- ResearchAI
- ResearchStatistics
- ResearchContacts
- ResearchArticles
- Appendix
- List of Figures [Total: 24]
- List of Tables [Total: 504 ]
Secure Your Competitive Edge with Targeted Market Intelligence
In order to leverage the insights and strategic direction provided in this executive summary, decision-makers are encouraged to connect with Ketan Rohom, Associate Director of Sales & Marketing. He will guide stakeholders through the report’s comprehensive analyses and facilitate tailored procurement arrangements that align with organizational objectives.
Reach out today to secure your copy of the full market research report and empower your team with the critical intelligence necessary to lead in the evolving Blow Fill Seal landscape
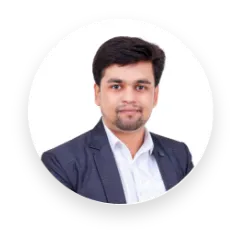
- How big is the Blow Fill Seal Technology Market?
- What is the Blow Fill Seal Technology Market growth?
- When do I get the report?
- In what format does this report get delivered to me?
- How long has 360iResearch been around?
- What if I have a question about your reports?
- Can I share this report with my team?
- Can I use your research in my presentation?