Introduction to the Brazing Wire Market
The brazing wire market is a critical enabler of high-integrity joints across industries ranging from aerospace to HVAC&R. As manufacturers seek stronger, lighter, and more durable assemblies, the choice of joining technology becomes pivotal. Brazing wires deliver precision, versatility, and minimal thermal distortion, making them an indispensable component in modern production processes. In recent years, advancements in material science have broadened the alloy options available, while digital process controls have elevated quality and repeatability. However, evolving trade policies, shifting end-user requirements, and sustainability mandates are introducing new complexities. Moreover, as global supply chains recalibrate, resilience and responsiveness become paramount. Companies that anticipate shifts in raw material availability and cost structures will outpace competitors. This executive summary synthesizes the latest transformative trends, tariff impacts, segmentation analyses, regional drivers, and competitive strategies to equip industry leaders with actionable insights. Whether planning investments in production capabilities or optimizing sourcing strategies, this overview offers the clarity needed to navigate an increasingly intricate global market and to bridge high-level strategic considerations with operational imperatives.
Transformative Shifts Reshaping the Brazing Wire Landscape
In recent years, the brazing wire sector has witnessed a profound leap in technological sophistication. Additive manufacturing integration, Internet of Things–enabled process monitoring, and AI-driven quality analytics have redefined production standards. Flux-cored formulations now incorporate nano-scale activators to optimize wetting and joint integrity, while low-silver and nickel alloys offer cost-efficient alternatives without compromising corrosion resistance. Sustainability imperatives have spurred the development of recyclable base metals and energy-efficient induction brazing systems, reducing carbon footprints and utility expenses. The convergence of advanced process controls with Industry 4.0 platforms ensures consistent heat distribution and real-time defect detection, minimizing rework. Simultaneously, the rise of electric vehicle powertrains and lightweight composite assemblies is expanding the palette of brazing wire applications. These transformative shifts challenge legacy supply models and demand agile adaptation. Companies that embrace digitalization, prioritize eco-friendly alloy design, and foster cross-disciplinary collaboration will redefine competitive benchmarks. The transition toward clean energy infrastructure and the acceleration of high-performance computing hardware further amplify the strategic importance of precision joining. This landscape of continuous innovation underscores the need for robust market intelligence to seize emerging opportunities and mitigate potential disruptions.
Cumulative Impact of United States Tariffs in 2025
Beginning in 2025, the United States will implement a series of import tariffs affecting key raw materials used in brazing wire production, including aluminum, copper, nickel, and silver. These duties increase landed costs for manufacturers reliant on offshore suppliers, prompting reevaluation of sourcing strategies. Many fabricators are exploring nearshoring options in Mexico and Latin America to offset tariff burdens, while others seek tariff-exempt duty drawback programs to reclaim duties on re-exported finished goods. Supply chain contracts are being renegotiated to transfer cost pressures or secure volume discounts, and some producers are accelerating vertical integration to control upstream feedstock. The tariffs also intensify competition among domestic alloy formulators capable of substituting high-cost precious metals. Product lines using flux-cored brazing wires and specialized nickel formulations feel the strain most acutely, as raw material intensity is highest. On the demand side, original equipment manufacturers may adjust design specifications to reduce dependency on tariff-impacted alloys, favoring lower-cost or alternative joining methods. In this context, transparency into supplier cost structures and contingency planning emerges as critical. Stakeholders must monitor tariff adjustments, engage in proactive price modeling, and maintain flexible production capabilities to navigate the evolving regulatory environment.
Key Segmentation Insights Across Product, Application, and Process
Breaking down the market by product type reveals unique growth drivers. Aluminum brazing wires gain traction where lightweight assemblies are paramount, while copper brazing wires dominate applications demanding superior thermal and electrical conductivity. Flux-cored brazing wires continue to expand their footprint in automated furnace systems, and nickel brazing alloys prove indispensable for high-temperature resistance. Silver brazing wires maintain niche status in precision electronics and medical devices. Application-based segmentation uncovers distinct end-use patterns: aerospace demand bifurcates across commercial and defense aviation as well as space exploration, automotive requirements split between OEM powertrain assemblies and aftermarket repairs, and construction projects range from commercial developments to infrastructure and residential retrofits. Electronics applications divide into consumer and industrial segments, while HVAC&R deployments encompass air conditioning, heating, refrigeration, and ventilation systems. Heavy machinery and industrial equipment represent another major segment. From a material composition standpoint, the interplay between base metals, coating materials, and flux constituents defines joint performance and process compatibility. End-user channels vary from distributors managing inventory and technical support to manufacturers specifying custom alloys, suppliers coordinating logistics, and end consumers leveraging brazing expertise in complex assemblies. Diameter ranges-from ultra-fine wires up to 0.5 mm to robust sections above 1 mm-dictate feeding and heat penetration characteristics. Finally, process segmentation across furnace brazing, induction brazing, and torch brazing highlights the coexistence of batch-level throughput and precision repairs, underscoring the necessity for tailored alloy-process pairings.
This comprehensive research report categorizes the Brazing Wire market into clearly defined segments, providing a detailed analysis of emerging trends and precise revenue forecasts to support strategic decision-making.
- Product Type
- Application
- Material Composition
- End-User
- Diameter
- Process
Regional Dynamics Driving Brazing Wire Demand
Regional dynamics play a pivotal role in shaping the brazing wire market’s trajectory. In the Americas, robust aerospace and automotive manufacturing hubs in the United States, Canada, and Mexico drive steady demand for high-performance aluminum and nickel brazing wires. Emerging production clusters in Brazil and Argentina also contribute to growth as local industries modernize infrastructure. Meanwhile, Europe, the Middle East, and Africa present a diverse landscape: Western Europe’s stringent regulatory standards and advanced industrial base fuel demand for premium silver and flux-cored alloys, while Eastern Europe and the Middle East emphasize cost-effective copper formulations to support construction and energy-sector expansion. African markets remain nascent but exhibit potential as mining and resource processing activities increase. Asia-Pacific commands the largest share, anchored by China, Japan, South Korea, and India’s electronics and automotive sectors. Rapid urbanization in Southeast Asia propels HVAC&R applications, and industrial equipment builders in the region adopt induction brazing technologies to maximize throughput. Cross-border supply networks in APAC also benefit from free-trade agreements, enhancing material flow. Understanding these regional nuances is essential for businesses aiming to align inventory strategies, prioritize R&D investments, and structure sales channels to capture localized opportunities and manage geopolitical risk.
This comprehensive research report examines key regions that drive the evolution of the Brazing Wire market, offering deep insights into regional trends, growth factors, and industry developments that are influencing market performance.
- Americas
- Asia-Pacific
- Europe, Middle East & Africa
Competitive Landscape and Leading Company Strategies
Leading companies are deploying distinct strategies to consolidate their positions in the brazing wire market. Aimtek Inc. excels at custom flux formulations, catering to specialized induction brazing applications. Bellman-Melcor LLC leverages its heritage in nickel-based alloys to serve high-temperature sectors, while Deutsche Nickel GmbH focuses on proprietary low-oxygen brazing wires for automotive and semiconductor production lines. Fusion Inc. has invested heavily in research collaborations, introducing nano-structured silver alloys that enhance joint strength and reduce cycle times. HAAN Industrial Group Co., Ltd. differentiates through integrated coating processes, delivering turnkey solutions for heat exchanger assembly. Harris Products Group, with its broad portfolio, targets both OEM and aftermarket channels, optimizing distribution networks to ensure rapid delivery. Indian Solder and Braze Alloys has scaled operations to meet surging domestic demand, expanding capacity for flux-cored and copper-based wires. Johnson Matthey Plc’s expertise in precious metal management supports high-purity silver offerings, while LINBRAZE S.r.l. focuses on exotic alloying elements for aerospace applications. Lucas-Milhaupt Inc. maintains a global footprint, balancing commodity copper wires with advanced nickel-chromium blends. Morgan Advanced Materials plc integrates its ceramic and refractory capabilities to address furnace brazing challenges. Oerlikon Metco (Switzerland) AG positions itself at the intersection of additive manufacturing and brazing, exploring hybrid process solutions. Meanwhile, Prince & Izant Company and Saru Silver Alloy Private Limited harness regional strengths in North America and Asia, respectively, to supply cost-competitive silver formulations. Solvay S.A. and Tokyo Braze Co., Ltd. drive innovation in flux compositions, enhancing process stability, and Umicore Brazil Ltd. has emerged as a key supplier in Latin America. Voestalpine Böhler Welding GmbH expands its welding and brazing systems integration, and Wall Colmonoy Corporation capitalizes on hardfacing and brazing synergies. Finally, Wieland Edelmetalle GmbH combines deep expertise in precious metals with sustainable alloy practices, rounding out a competitive landscape defined by technological prowess and strategic partnerships.
This comprehensive research report delivers an in-depth overview of the principal market players in the Brazing Wire market, evaluating their market share, strategic initiatives, and competitive positioning to illuminate the factors shaping the competitive landscape.
- Aimtek Inc.
- Bellman-Melcor LLC
- Deutsche Nickel GmbH
- Fusion Inc.
- HAAN Industrial Group Co., Ltd.
- Harris Products Group
- Indian Solder and Braze Alloys
- Johnson Matthey Plc
- LINBRAZE S.r.l.
- Lucas-Milhaupt Inc.
- Morgan Advanced Materials plc
- Oerlikon Metco (Switzerland) AG
- Prince & Izant Company
- Saru Silver Alloy Private Limited
- Solvay S.A.
- Tokyo Braze Co., Ltd.
- Umicore Brazil Ltd.
- Voestalpine Böhler Welding GmbH
- Wall Colmonoy Corporation
- Wieland Edelmetalle GmbH
Actionable Recommendations for Industry Leadership
To thrive amid accelerating change, industry leaders must implement targeted initiatives. First, diversify raw material sourcing by establishing dual-sourcing agreements in tariff-resilient regions and pursuing nearshoring collaborations to mitigate exposure to 2025 duty increases. Second, invest in R&D programs that explore low-silver and nickel-replacement alloys, balancing performance requirements with cost efficiency and sustainability goals. Third, adopt digital process monitoring across furnace and induction brazing lines, leveraging real-time analytics to reduce scrap rates by detecting joint defects before completion. Fourth, strengthen partnerships with distributors and end consumers through technical training, shared quality assurance protocols, and collaborative product development to deepen customer loyalty and expand market share. Fifth, optimize asset utilization by aligning process selection-whether torch, induction, or furnace brazing-with product complexity and throughput demands, ensuring capital expenditures deliver maximum ROI. Sixth, align corporate sustainability strategies with alloy lifecycle management, promoting recyclable materials and transparent supply chain traceability to meet emerging regulatory and end-customer expectations. Lastly, monitor competitor moves and patent filings to anticipate innovative alloy introductions, allowing proactive adjustments to product roadmaps and marketing strategies. These actions, taken synergistically, will position organizations to outpace rivals and navigate geopolitical and technological headwinds effectively.
Explore AI-driven insights for the Brazing Wire market with ResearchAI on our online platform, providing deeper, data-backed market analysis.
Ask ResearchAI anything
World's First Innovative Al for Market Research
Concluding Perspectives on Market Evolution
As the brazing wire industry navigates an era defined by innovation, regulatory shifts, and sharpened global competition, a nuanced understanding of market forces is indispensable. Technological advancements in alloy chemistry and digital control systems are unlocking new performance thresholds, while tariff-induced supply chain realignments introduce fresh operational imperatives. Detailed segmentation analysis underscores the importance of catering to diverse end-use requirements, and regional insights reveal shifting demand centers across the Americas, EMEA, and Asia-Pacific. The competitive landscape, populated by specialized alloy developers and integrated process solution providers, rewards agility and collaboration. By synthesizing these insights and translating them into focused strategy-whether through material diversification, process optimization, or sustainability integration-executives can secure a sustainable advantage. The path forward demands proactive engagement with emerging trends, disciplined risk management, and continuous innovation in both product and process domains. With these guiding principles, stakeholders will be well-positioned to harness growth opportunities and reinforce their leadership in the brazing wire market.
This section provides a structured overview of the report, outlining key chapters and topics covered for easy reference in our Brazing Wire market comprehensive research report.
- Preface
- Research Methodology
- Executive Summary
- Market Overview
- Market Dynamics
- Market Insights
- Cumulative Impact of United States Tariffs 2025
- Brazing Wire Market, by Product Type
- Brazing Wire Market, by Application
- Brazing Wire Market, by Material Composition
- Brazing Wire Market, by End-User
- Brazing Wire Market, by Diameter
- Brazing Wire Market, by Process
- Americas Brazing Wire Market
- Asia-Pacific Brazing Wire Market
- Europe, Middle East & Africa Brazing Wire Market
- Competitive Landscape
- ResearchAI
- ResearchStatistics
- ResearchContacts
- ResearchArticles
- Appendix
- List of Figures [Total: 28]
- List of Tables [Total: 555 ]
Next Steps and Expert Research Access
Unlock the full depth of these insights by acquiring the comprehensive market research report. For tailored guidance and exclusive access to detailed analyses on tariffs, segmentation trends, competitive strategies, and regional forecasts, contact Ketan Rohom, Associate Director, Sales & Marketing. Reach out directly to discuss your specific information needs, explore customized research packages, and secure the intelligence required to drive strategic decision-making. Act now to ensure your business remains at the forefront of the brazing wire market’s evolution.
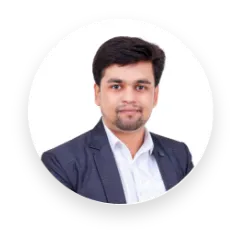
- When do I get the report?
- In what format does this report get delivered to me?
- How long has 360iResearch been around?
- What if I have a question about your reports?
- Can I share this report with my team?
- Can I use your research in my presentation?