Introduction: The Rise of Busbars in Electric Vehicles
As global automotive manufacturers accelerate electrification strategies, busbars have emerged as critical components for power distribution within electric vehicles. These conductive bars replace complex wiring harnesses, enabling reduced weight, enhanced thermal performance and improved reliability under high-current conditions. Innovations in materials science, such as advanced aluminum and copper alloys, together with breakthrough insulation and coating technologies, are unlocking new design possibilities. Moreover, the push for longer driving ranges and faster charging times places stringent requirements on energy efficiency and heat management, intensifying demand for optimized busbar solutions.
In this evolving context, system architects are balancing trade-offs between conductivity, mechanical integrity and cost. Solid aluminum busbars offer lightweight advantages while coated variants mitigate corrosion risks. At the same time, high conductivity copper grades deliver superior performance in compact footprints, albeit at higher material expense. Insulation options spanning epoxy, polyester, hybrid and PVC platforms further influence dielectric strength and thermal stability. Consequently, flexible and rigid configurations must align with vehicle architectures across passenger, commercial and heavy-duty segments.
This executive summary maps the transformative trends shaping the busbar market in electric vehicles. It highlights tariff impacts, segmentation insights, regional dynamics and leading innovators. The analysis culminates in actionable recommendations to help industry leaders seize emerging opportunities and navigate a complex regulatory and competitive landscape.
Transformative Shifts in the Busbar Landscape
As the automotive sector commits to net-zero emissions targets, busbars have undergone a series of transformational shifts. First, material innovation has moved beyond traditional solid copper toward coated and composite aluminum–copper configurations that balance conductivity with weight reduction. High conductivity copper alloys, for example, now coexist alongside coated aluminum solutions to achieve performance parity while curbing total mass.
Next, manufacturing techniques have evolved. Automated welding and laser welding processes deliver precise joints with minimal thermal distortion, and additive manufacturing is promising rapid prototyping of intricate busbar geometries. Digital twins and advanced simulation tools accelerate design cycles by predicting electrical and thermal behavior under varying load profiles.
Additionally, system integration is reaching new heights. Encapsulated busbar assemblies now feature integrated sensors and embedded temperature monitoring, enabling real-time feedback for battery management and predictive maintenance. Hybrid insulation systems, combining epoxy and high-performance polymers, extend service lives while reducing footprint.
Meanwhile, commercialization pathways broaden as busbars transition from niche components to standardized modules compatible with diverse vehicle platforms. Passenger cars, light commercial vehicles and heavy-duty trucks increasingly rely on modular busbar designs that simplify assembly and reduce time-to-market.
Digitalization and data analytics now play a pivotal role in busbar lifecycle management. Cloud-based simulation and predictive analytics pinpoint potential hotspots and inform preventive maintenance, while compliance with evolving safety standards such as ISO 26262 and UL approvals drives standardized testing protocols. Software integration extends into vehicle control units, enabling dynamic load balancing and optimized thermal distribution.
Cumulative Impact of United States Tariffs 2025
In 2025, cumulative adjustments in United States tariff policy are reshaping cost structures for busbar manufacturers and integrators. Heightened import duties on key raw materials, including copper and specialized aluminum alloys, have amplified input costs. These measures, combined with tariffs on insulating polymers and plating chemicals, increase the total landed cost of busbar assemblies destined for U.S. production lines.
Many components fall under HTS codes 7407 and 7604, triggering additional duties under Section 301. Firms are leveraging duty drawback programs and bonded warehousing to reclaim a portion of expenses. At the same time, certain companies have established dedicated R&D centers within the United States to design tariff-exempt variants and accelerate intellectual property development.
As a result, suppliers face pressure to localize sourcing strategies. Several global players are expanding domestic smelting and extrusion capacity or negotiating long-term contracts with U.S.-based metal producers to mitigate duty impacts. Advanced insulation providers are exploring regional polymer processing partnerships to avoid cross-border levies.
The tariffs also accelerate the formation of nearshore manufacturing hubs. By shifting production to Mexico, Canada and the U.S., industry stakeholders can minimize logistics expenses and maintain supply chain resilience. However, retooling plants for domestic fabrication demands significant capital investment and workforce training.
Consequently, strategic alliances between raw material suppliers, insulation specialists and system integrators are rising in prominence. Collaboration on shared manufacturing platforms and co-development agreements reduces duplication of effort and diffuses tariff-related risk. In this environment, firms that anticipate regulatory changes and proactively adjust their footprint will secure a competitive advantage.
Key Segmentation Insights Driving Market Dynamics
Material choices profoundly affect performance and cost. Aluminum busbars, available in coated and solid variants, deliver compelling weight savings, while brass options-ranging from basic brass to copper-alloyed grades-strike a balance between conductivity and formability. Copper configurations, whether in high-conductivity or standard grades, underpin applications demanding maximum current capacity in compact assemblies. Insulation systems span epoxy, polyester, hybrid and PVC platforms, each offering distinct dielectric and thermal attributes that influence busbar longevity under rigorous thermal cycling.
Application type further stratifies requirements. Passenger electric vehicles prioritize lightweight, flexible busbars to optimize cabin packaging and reduce energy consumption, whereas commercial platforms demand robust, rigid configurations to endure higher load profiles and duty cycles. Heavy-duty EVs, in particular, leverage solid copper solutions combined with advanced coatings such as nickel, silver or tin to resist corrosion and elevate current density.
Voltage rating introduces another layer of complexity. Low, medium and high-voltage assemblies cater to a spectrum of auxiliary, traction and charging systems; ultra-high voltage busbars emerge as performance imperatives for next-generation fast-charging infrastructures. Conductor architectures-from single layer to multi-layer and braided designs-balance electrical efficiency with mechanical flexibility.
Types of electric vehicles impose unique demands. Battery electric vehicles require high-voltage busbars with robust insulation; hybrids emphasize compact, multi-layer conductor arrangements; plug-in hybrids blend these requirements, demanding flexible busbar assemblies that accommodate dual power sources. System configurations-from fully encapsulated modules that provide enhanced leak protection to open busbars optimized for rapid assembly-further tailor solutions to operational priorities.
End-user industries span aerospace, automotive OEMs and aftermarket channels, as well as transportation and logistics segments. This segmentation mosaic guides targeted innovation and investment by aligning product attributes with specific performance and regulatory demands.
This comprehensive research report categorizes the Busbar for EV market into clearly defined segments, providing a detailed analysis of emerging trends and precise revenue forecasts to support strategic decision-making.
- Material Type
- Insulation Material
- Application Type
- Shape/Density Configuration
- Voltage Rating
- Conductor Plus Type
- Types of EVs
- Busbar Coatings
- End User Industry
- System Configuration
Key Regional Insights Shaping Global Adoption
Regional dynamics spotlight divergent trajectories. In the Americas, aggressive electrification incentives and robust infrastructure investments underpin a surge in demand for lightweight, high-performance busbars, prompting manufacturers to fortify domestic assembly lines and local material supply. In Canada and the U.S., federal and state-level subsidies accelerate battery production, reinforcing the need for advanced busbar architectures.
In Europe, Middle East & Africa, stringent emission regulations and landmark zero-emission targets accelerate adoption of high-voltage busbar architectures, fuelling innovation in coatings and insulation to satisfy rigorous safety standards. In the Middle East, nascent battery gigafactories and government-backed public-private partnerships drive demand for medium-voltage distribution systems, while African markets focus on retrofitting existing distribution networks to support electric public transportation.
Across Asia-Pacific, the confluence of large-scale EV production and cost-competitive manufacturing culminates in a thriving ecosystem for volume-based busbar production. Suppliers in the region leverage economies of scale, integrating advanced automation and end-to-end quality control to serve both domestic and export markets. Cross-regional grid harmonization efforts further streamline charging infrastructure and enable synergies in material sourcing and technology transfer that reinforce the global supply chain.
This comprehensive research report examines key regions that drive the evolution of the Busbar for EV market, offering deep insights into regional trends, growth factors, and industry developments that are influencing market performance.
- Americas
- Asia-Pacific
- Europe, Middle East & Africa
Key Companies Driving Innovation and Growth
Market leadership rests with a diverse array of innovators spanning material science, component engineering and system integration. Global materials giant 3M Company pushes the envelope with advanced insulation films, while Alstom SA applies its rail electrification expertise to next-generation busbar systems. AMADA WELD TECH and CTI Electronics Corporation deliver precision welding and assembly solutions that underpin high-reliability performance. Delphi Technologies PLC and TE Connectivity Ltd. boast deep automotive domain expertise, collaborating with OEMs to co-develop integrated busbar modules.
Electrical Components International Inc. and Rogers Corporation specialize in high-performance polymer insulators, while ElringKlinger AG advances sealed and encapsulated designs for heavy-duty applications. Fujipoly America Corporation focuses on flexible conductive interfaces, and Hella GmbH & Co. KGaA integrates sensor arrays for real-time thermal monitoring. Semiconductor leader Infineon Technologies AG contributes power electronics interfaces that streamline busbar integration with inverter and battery systems. Meanwhile, IWIS Motor Vehicles and Leoni AG optimize conductor architectures for dynamic load environments.
Recent joint ventures, such as those between Infineon Technologies AG and Leoni AG on integrated busbar–inverter modules, exemplify how strategic alliances accelerate time to market. M&A activity, like Mersen S.A.’s acquisition of Rena GmbH, expands material portfolios and geographic reach. Investment in greenfield capacity by Electrical Components International Inc. further underscores the race to secure annual throughput for EV programs. Vectra Corporation pioneers composite materials while Vishay Intertechnology, Inc. enhances busbar diagnostics through resistor-based sensing modalities. This constellation of players drives continuous improvement and competitive differentiation.
This comprehensive research report delivers an in-depth overview of the principal market players in the Busbar for EV market, evaluating their market share, strategic initiatives, and competitive positioning to illuminate the factors shaping the competitive landscape.
- 3M Company
- Alstom SA
- AMADA WELD TECH
- CTI Electronics Corporation
- Delphi Technologies PLC
- Electrical Components International Inc.
- ElringKlinger AG
- Fujipoly America Corporation
- Hella GmbH & Co. KGaA
- Infineon Technologies AG
- IWIS Motor Vehicles
- Leoni AG
- Mersen S.A.
- Rena GmbH
- Rogers Corporation
- Sumitomo Electric Industries, Ltd.
- TE Connectivity Ltd.
- Vectra Corporation
- Vishay Intertechnology, Inc.
Actionable Recommendations for Industry Leaders
First, industry leaders should accelerate investments in advanced material portfolios to strike the optimal balance between conductivity, weight and cost. By partnering with material science innovators, firms can co-create coated aluminum and high-conductivity copper alloys tailored to specific vehicle platforms. Second, establishing flexible manufacturing networks across multiple regions will mitigate tariff exposure and supply chain disruptions. Collaborative nearshore facilities and multilateral trade agreements should be leveraged to localize critical component production.
Third, integration of real-time monitoring sensors within busbar assemblies can unlock preventive maintenance windows and extend product lifecycles. Companies should adopt open communication protocols to ensure seamless interoperability with vehicle battery management systems. Fourth, standardization of modular busbar interfaces will reduce development cycle times and encourage economies of scale, especially across commercial and heavy-duty EV segments. Fifth, strategic implementation of digital twin platforms will enable virtual validation of busbar performance under extreme scenarios, reducing prototyping cycles and speeding product launches.
Sixth, embedding cybersecurity protocols within busbar control interfaces ensures data integrity and safety in connected vehicles. Pursuing sustainability certifications, such as ISO 14001 and UL 94V-0, demonstrates environmental stewardship and enhances customer confidence. Finally, cultivating specialized engineering talent through targeted training programs will sustain innovation and operational excellence. By executing on these strategic imperatives, stakeholders can capture emerging growth pockets and reinforce long-term profitability.
Explore AI-driven insights for the Busbar for EV market with ResearchAI on our online platform, providing deeper, data-backed market analysis.
Ask ResearchAI anything
World's First Innovative Al for Market Research
Conclusion: Steering Toward Electrified Mobility
As electric mobility becomes the cornerstone of sustainable transportation, busbars remain indispensable enablers of efficient power distribution and thermal management. The convergence of material innovation, advanced manufacturing techniques and strategic supply chain realignment is reshaping the competitive landscape. Navigating the cumulative effects of tariff adjustments demands agile sourcing strategies and collaborative partnerships, while nuanced segmentation-encompassing material types, insulation platforms, voltage tiers and end-user industries-guides targeted product development.
Regional variations underscore the importance of localized manufacturing footprints and regulatory compliance, whereas a diverse ecosystem of specialized and integrated players drives continuous improvement. Legislative drivers such as the Inflation Reduction Act, upcoming Euro 7 emissions standards and the EU Battery Directive heighten compliance requirements. Embracing circular economy principles by designing busbars for disassembly and recyclability can reduce end-of-life waste and support corporate sustainability mandates. By embedding regulatory foresight into product roadmaps, organizations minimize costly redesigns and reinforce market credibility.
By synthesizing these insights, decision-makers can chart a course that leverages both emerging technologies and consolidated industry relationships. The future belongs to organizations that proactively anticipate market shifts, invest in differentiated capabilities and deliver turnkey busbar solutions that meet the rigorous demands of next-generation electric vehicles.
This section provides a structured overview of the report, outlining key chapters and topics covered for easy reference in our Busbar for EV market comprehensive research report.
- Preface
- Research Methodology
- Executive Summary
- Market Overview
- Market Dynamics
- Market Insights
- Cumulative Impact of United States Tariffs 2025
- Busbar for EV Market, by Material Type
- Busbar for EV Market, by Insulation Material
- Busbar for EV Market, by Application Type
- Busbar for EV Market, by Shape/Density Configuration
- Busbar for EV Market, by Voltage Rating
- Busbar for EV Market, by Conductor Plus Type
- Busbar for EV Market, by Types of EVs
- Busbar for EV Market, by Busbar Coatings
- Busbar for EV Market, by End User Industry
- Busbar for EV Market, by System Configuration
- Americas Busbar for EV Market
- Asia-Pacific Busbar for EV Market
- Europe, Middle East & Africa Busbar for EV Market
- Competitive Landscape
- ResearchAI
- ResearchStatistics
- ResearchContacts
- ResearchArticles
- Appendix
- List of Figures [Total: 36]
- List of Tables [Total: 722 ]
Next Steps: Secure Your In-Depth Market Intelligence with Ketan Rohom
To gain deeper insights and actionable intelligence on the evolving busbar market, contact Ketan Rohom, Associate Director, Sales & Marketing at 360iResearch. His expertise will guide you through comprehensive data on material trends, tariff impacts, segmentation strategies and competitive landscapes. Secure your access to in-depth analysis, tailored recommendations and proprietary benchmarking that will empower your organization to outpace competitors and accelerate electric vehicle innovation. Reach out today to obtain the full market research report and position your business at the forefront of busbar technology.
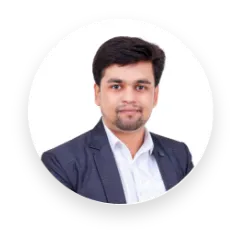
- When do I get the report?
- In what format does this report get delivered to me?
- How long has 360iResearch been around?
- What if I have a question about your reports?
- Can I share this report with my team?
- Can I use your research in my presentation?