Introduction to Car Traction Motor Core Market Dynamics
The rapid acceleration of electric vehicle adoption has elevated the traction motor core from a niche component to a pivotal driver of automotive innovation. As governments worldwide tighten emissions regulations and consumers demand the seamless performance of electric and hybrid powertrains, manufacturers are under immense pressure to optimize motor core design for efficiency, thermal stability, and torque density. This market summary explores the critical forces shaping the car traction motor core landscape, from material advancements and construction methodologies to evolving regulatory frameworks and supply chain dynamics. By examining the convergence of technological breakthroughs-such as soft magnetic composites, additive manufacturing techniques, and advanced insulation systems-this report illuminates how industry stakeholders are redefining performance benchmarks. In addition, it highlights the strategic implications of shifting trade policies and regional growth patterns. With global competition intensifying, decision-makers must navigate both the opportunities presented by next-generation materials and the challenges of tariff-induced cost fluctuations. This introduction sets the stage for an in-depth analysis of transformative market shifts, segmentation insights, regional drivers, and actionable recommendations. Ultimately, understanding these dynamics will enable OEMs, tier-one suppliers, and material specialists to align their strategies with emerging growth vectors and maintain a competitive edge in a rapidly evolving automotive ecosystem.
Transformative Shifts Redefining the Car Traction Motor Core Landscape
Over the past decade, the traction motor core sector has undergone transformative shifts driven by electrification imperatives, digitalization, and sustainability goals. Firstly, the surge in electric and hybrid vehicle deployments has prompted a re-evaluation of core geometries to minimize iron losses and enhance thermal management. Manufacturers are leveraging digital twin simulations to accelerate design iterations, enabling complex lamination patterns and optimized magnetic flux paths that were previously impractical. In parallel, the incorporation of soft magnetic composites and high-silicon electrical steels is reducing weight without sacrificing structural integrity, supporting extended driving ranges and improved power density.
Moreover, additive manufacturing is emerging as a game-changer, allowing for near-net-shape cores with tailored cooling channels and minimal material waste. This shift not only shortens development cycles but also aligns with circular economy principles by facilitating easier recycling and material recovery. Regulatory landscapes are evolving in tandem; stringent efficiency standards in key markets are incentivizing investments in advanced core technologies, while harmonized global safety requirements are streamlining certification processes.
Consequently, collaboration across the value chain is intensifying. Material suppliers, motor designers, and OEMs are forming strategic alliances to co-develop insulation systems, integrate smart sensors for real-time condition monitoring, and validate performance under extreme thermal and mechanical loads. This holistic approach to motor core innovation is setting new benchmarks for reliability and lifecycle performance. As these transformative forces continue to intersect, the industry is poised for sustained growth underpinned by continuous technological refinement and cross-sector partnerships.
Analyzing the Cumulative Impact of US Tariffs in 2025
The implementation of United States tariffs in 2025 has introduced a complex layer of cost considerations for stakeholders across the traction motor core supply chain. Tariffs imposed on key inputs such as high-grade silicon steel, cobalt and nickel-based alloys, and certain composite materials have driven procurement teams to reassess supplier portfolios and seek alternative sourcing strategies. In response, some manufacturers have accelerated efforts to localize production, investing in domestic rolling mills and coating facilities to mitigate the impact of import duties. This reshoring trend not only reduces exposure to cross-border freight disruptions but also aligns with incentives offered under regional infrastructure and sustainable manufacturing initiatives.
However, the tariff environment has also prompted strategic re-engineering of core designs to accommodate lower-cost materials without compromising performance. For example, motor designers are exploring hybrid constructions that blend grain-oriented steel laminations with targeted applications of soft magnetic composites, achieving a balance between efficiency and material cost. Meanwhile, indirect effects are surfacing as suppliers absorb portions of the tariff burden to maintain long-standing OEM partnerships, compressing margins throughout the value chain.
International trade routes have recalibrated as well; manufacturers previously reliant on Asian exports are forging new relationships with producers in regions exempt from certain duties, including select countries in Central America and Eastern Europe. At the same time, collaborative procurement consortia are forming to negotiate volume discounts and shared logistics solutions, thereby distributing risk and reducing unit costs.
Overall, while tariffs have introduced short-term pricing volatility, they are also catalyzing supply chain innovation and regional self-sufficiency. As the market adapts, companies that proactively diversify sourcing, optimize material utilization, and strengthen local production capabilities will be best positioned to thrive in the post-tariff landscape.
Comprehensive Segmentation Highlights for Market Analysis
Market segmentation reveals a multifaceted landscape defined by construction method, material type, application, motor type, end-user industry, manufacturing process, finishing process, performance characteristic, and innovation integration. Based on construction approach, the field divides into cast cores, laminated cores, and sintered cores, each offering distinct benefits in terms of magnetic performance and manufacturing scalability. Material segmentation spans alloy steel-including cobalt alloy steel and nickel alloy steel-silicon steel in both grain-oriented and non-grain-oriented variants, and soft magnetic composite, underscoring the diversity of magnetic substrates driving efficiency gains.
Application analysis shows traction motor cores deployed across aerospace platforms, agricultural vehicles such as harvesters and tractors, electric and hybrid vehicles encompassing battery electric vehicles, hybrid electric vehicles, and plug-in hybrids, as well as industrial equipment in automation and robotics. Motor type segmentation covers AC induction motors, brushed and brushless DC motors, permanent magnet synchronous motors, and switched reluctance motors, each addressing specific performance requirements and cost targets. End-user industries include automotive, defense, healthcare applications like hospital equipment and medical devices, and marine systems. The manufacturing process dimension highlights cold rolling, direct energy deposition, and hot rolling methodologies, while finishing processes extend from coating and heat treatment to precision machining techniques such as CNC milling and laser cutting.
Performance characteristics concentrate on efficiency, thermal stability, and torque density, which are critical for meeting stringent regulatory mandates and consumer expectations for range and reliability. Finally, innovation and technology integration are exemplified by advanced insulation materials and embedded smart sensors, facilitating real-time condition monitoring and predictive maintenance. Together, these segmentation insights provide a comprehensive view of the market’s evolving architecture, enabling stakeholders to tailor strategies for targeted growth segments.
This comprehensive research report categorizes the Car Traction Motor Core market into clearly defined segments, providing a detailed analysis of emerging trends and precise revenue forecasts to support strategic decision-making.
- Construction Method
- Material Type
- Application
- Motor Type
- End-User Industry
- Manufacturing Process
- Finishing Process
- Performance Characteristics
- Innovation and Technology Integration
Regional Dynamics Shaping Market Opportunities
Regional dynamics play a decisive role in shaping market trajectories. In the Americas, growing demand for electrified commercial fleets and supportive policy frameworks are accelerating investment in domestic raw material processing and motor core assembly facilities. Incentives for sustainable manufacturing are encouraging local partnerships and joint ventures, while established automotive clusters in North America remain hubs for R&D collaboration. Moving across the Atlantic, the Europe, Middle East & Africa region is characterized by stringent CO2 reduction targets, prompting aggressive adoption of high-efficiency core technologies and the establishment of recycling infrastructures for end-of-life motor cores. Government subsidies and pan-regional harmonization of efficiency standards are fostering cross-border supply chain integration and innovation ecosystems concentrated in Western Europe.
Meanwhile, Asia-Pacific continues to dominate production volumes, driven by expansive electric vehicle rollouts in China, South Korea, and Southeast Asia. Here, large-scale rolling mills and advanced coating lines are coupled with rapid prototyping capabilities, enabling agile responses to shifting OEM specifications. Infrastructure development in India and Japan is further enhancing regional capacity, while government-backed research consortia are advancing next-generation materials and additive manufacturing applications. Across these geographies, competitive positioning is increasingly linked to proximity to OEM assembly plants, quality certification standards, and the ability to deliver just-in-time supply chain solutions that minimize inventory costs.
This comprehensive research report examines key regions that drive the evolution of the Car Traction Motor Core market, offering deep insights into regional trends, growth factors, and industry developments that are influencing market performance.
- Americas
- Asia-Pacific
- Europe, Middle East & Africa
Leading Companies Driving Innovation and Growth
Market leadership is defined by innovation pipelines, global footprint, and strategic partnerships. BorgWarner Inc. and Continental AG have ramped up R&D in soft magnetic composites to unlock higher torque density, leveraging their deep expertise in automotive powertrain systems. BYD Auto Co., Ltd. and Tesla Inc. are vertically integrating core production to secure critical materials for battery electric vehicles, thus reducing reliance on external suppliers and insulating themselves from tariff fluctuations. Denso Corporation, Hitachi Automotive Systems, Ltd., and Mitsubishi Electric Corporation are collaborating with semiconductor manufacturers to embed smart sensors directly into core laminations, enabling real-time thermal management and predictive analytics.
Meanwhile, Nidec Corporation and Robert Bosch GmbH are expanding production capacity in North America and Europe, capitalizing on reshoring incentives and proximity to leading OEMs. Magna International Inc. and Valeo Group are forging supply alliances to standardize insulation treatments and surface coatings, which streamline certification and reduce time to market. Siemens AG and ZF Friedrichshafen AG are focusing on high-volume, cost-optimized laminated cores for commercial vehicle segments, where durability and lifecycle cost are paramount. Each of these key players is differentiating through targeted investments in advanced materials, digitized manufacturing, and collaborative R&D networks, positioning themselves at the forefront of emerging market segments.
This comprehensive research report delivers an in-depth overview of the principal market players in the Car Traction Motor Core market, evaluating their market share, strategic initiatives, and competitive positioning to illuminate the factors shaping the competitive landscape.
- BorgWarner Inc.
- BYD Auto Co., Ltd.
- Continental AG
- Denso Corporation
- Hitachi Automotive Systems, Ltd.
- Magna International Inc.
- Mitsubishi Electric Corporation
- Nidec Corporation
- Robert Bosch GmbH
- Siemens AG
- Tesla Inc.
- Valeo Group
- ZF Friedrichshafen AG
Actionable Recommendations for Industry Leaders Seeking Competitive Edge
To navigate this complex environment and maintain competitive advantage, industry leaders should prioritize strategic actions across four key dimensions. First, diversify supply chains by establishing hybrid sourcing models that blend local production with global partnerships, thereby mitigating tariff risks and transportation disruptions. Second, accelerate adoption of additive manufacturing and advanced insulation systems to reduce material waste and enhance core performance, while collaborating with universities or technology incubators to co-develop disruptive material formulations.
Third, invest in digital infrastructure such as digital twin platforms and embedded sensor networks to enable predictive maintenance and real-time performance optimization. This not only extends motor lifespan but also delivers actionable insights for continuous improvement. Fourth, forge cross-sector alliances with OEMs, tier-one suppliers, and raw material specialists to co-innovate on motor core geometries and integrate sustainable end-of-life recovery processes. By aligning R&D roadmaps with emerging regulatory mandates and customer demands, companies can accelerate time to market and secure long-term contracts.
Finally, assess regional expansion opportunities against local policy incentives and workforce capabilities. Establish joint ventures or greenfield facilities in strategic geographies to capitalize on electrified mobility trends and secure a foothold in high-growth markets. Through these actionable recommendations, industry leaders can build resilient operations, unlock new performance thresholds, and drive profitable growth in the evolving traction motor core market.
Explore AI-driven insights for the Car Traction Motor Core market with ResearchAI on our online platform, providing deeper, data-backed market analysis.
Ask ResearchAI anything
World's First Innovative Al for Market Research
Conclusion: Leveraging Insights for Strategic Decision-Making
As the car traction motor core market continues to evolve under the influence of electrification, material innovation, and shifting trade policies, stakeholders must adopt a holistic perspective that balances performance objectives with cost imperatives. By synthesizing insights across construction methods, material compositions, application domains, and regional dynamics, decision-makers can identify priority areas for investment and collaboration. Embracing advanced manufacturing technologies such as additive processes and digital twins will unlock efficiencies, while strategic alliances and local production capabilities will mitigate exposure to external shocks such as tariffs and supply chain disruptions. Ultimately, success will hinge on the ability to anticipate regulatory trends, harness cutting-edge materials, and deliver high-performance cores that meet the stringent demands of next-generation electric and hybrid drivetrains. This comprehensive executive summary equips industry participants with the knowledge foundation needed to chart a clear roadmap toward sustained innovation and market leadership.
This section provides a structured overview of the report, outlining key chapters and topics covered for easy reference in our Car Traction Motor Core market comprehensive research report.
- Preface
- Research Methodology
- Executive Summary
- Market Overview
- Market Dynamics
- Market Insights
- Cumulative Impact of United States Tariffs 2025
- Car Traction Motor Core Market, by Construction Method
- Car Traction Motor Core Market, by Material Type
- Car Traction Motor Core Market, by Application
- Car Traction Motor Core Market, by Motor Type
- Car Traction Motor Core Market, by End-User Industry
- Car Traction Motor Core Market, by Manufacturing Process
- Car Traction Motor Core Market, by Finishing Process
- Car Traction Motor Core Market, by Performance Characteristics
- Car Traction Motor Core Market, by Innovation and Technology Integration
- Americas Car Traction Motor Core Market
- Asia-Pacific Car Traction Motor Core Market
- Europe, Middle East & Africa Car Traction Motor Core Market
- Competitive Landscape
- ResearchAI
- ResearchStatistics
- ResearchContacts
- ResearchArticles
- Appendix
- List of Figures [Total: 34]
- List of Tables [Total: 728 ]
Next Steps: Engage with Ketan Rohom for In-Depth Market Research
To delve deeper into this comprehensive analysis and secure tailored recommendations, reach out to Ketan Rohom, Associate Director, Sales & Marketing at 360iResearch. Engage today to obtain the full market research report and position your organization at the forefront of traction motor core innovation.
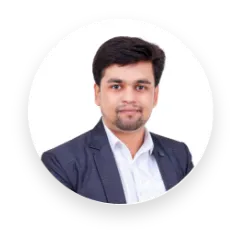
- When do I get the report?
- In what format does this report get delivered to me?
- How long has 360iResearch been around?
- What if I have a question about your reports?
- Can I share this report with my team?
- Can I use your research in my presentation?