The Carbon Fiber Prepreg Market size was estimated at USD 10.19 billion in 2024 and expected to reach USD 11.18 billion in 2025, at a CAGR 9.58% to reach USD 17.65 billion by 2030.

Exploring the Promise of Carbon Fiber Prepreg
Carbon fiber prepreg represents a pivotal advancement in composite manufacturing, combining high-strength fibers with resin systems that optimize performance and processing efficiency. By integrating pre-impregnated fabrics into production workflows, manufacturers achieve precise fiber-resin ratios and uniform distribution, enabling lighter, stronger, and more durable components. This innovation has expanded beyond traditional aerospace applications to encompass automotive, marine, sports, and renewable energy sectors, driving cross-industry demand.
As global industries strive for weight reduction and enhanced durability, the value proposition of carbon fiber prepreg continues to gain traction. Automotive engineers leverage its high tensile strength and corrosion resistance to improve vehicle efficiency, while wind energy developers adopt blade components that withstand cyclic loading in harsh environments. In parallel, sporting goods manufacturers exploit its rigidity-to-weight ratio to deliver consumer products that blend performance with longevity. These diverse adoption vectors underscore the material’s versatility and its capacity to address evolving performance requirements.
This report delves into the critical factors shaping the carbon fiber prepreg landscape, examining shifts in technology, policy, segmentation, and regional dynamics. It equips decision-makers with a clear overview of current market realities and highlights the strategic considerations crucial for navigating an environment marked by rapid innovation and regulatory complexity.
Uncovering the Forces Reshaping the Prepreg Landscape
The carbon fiber prepreg market is undergoing transformative shifts driven by technological breakthroughs and evolving end-use demands. Advancements in resin chemistries, including novel thermoplastic formulations, are enabling faster curing cycles and enhanced recyclability. Meanwhile, digital manufacturing techniques such as automated fiber placement and advanced preforming methods are streamlining production, reducing waste, and elevating precision.
On the demand side, the accelerating transition to electric vehicles has intensified the need for lightweight structural components that extend battery range without compromising safety. Aerospace manufacturers are increasingly specifying high-temperature bismaleimide prepregs for next-generation aircraft, balancing fuel efficiency with stringent safety margins. In the renewable energy sector, offshore wind installations are driving a surge in demand for large-scale composite blades capable of withstanding harsh marine conditions.
Sustainability objectives and circular economy principles are reshaping procurement strategies, prompting suppliers to explore bio-based resin alternatives and closed-loop recycling solutions. As regulatory frameworks tighten around carbon emissions and environmental impact, organizations are prioritizing materials that align performance with eco-credentials. These converging trends underscore a dynamic landscape in which innovation and sustainability coalesce to redefine competitive advantage.
Assessing the 2025 US Tariff Ripple Effect
The introduction of revised United States tariffs in early 2025 has reverberated across the carbon fiber prepreg supply chain. Measures aimed at protecting domestic producers have imposed additional duties on imported composite materials, altering cost structures and prompting a reevaluation of sourcing strategies. Manufacturers reliant on overseas suppliers have faced heightened input expenses, challenging their ability to maintain competitive pricing in sensitive end-use markets.
In response, several suppliers have accelerated investments in domestic production capacity and diversified procurement channels to mitigate tariff exposure. Strategic partnerships between resin formulators and regional fiber manufacturers have emerged to localize value chains and preserve margin integrity. Concurrently, some downstream OEMs have renegotiated long-term contracts or absorbed incremental costs to avoid supply disruptions, illustrating the delicate balance between cost containment and continuity of operations.
The tariff landscape has also stimulated innovation in material substitution and process optimization. Developers are exploring alternative fiber architectures and consolidated prepreg formats to reduce material waste and streamline supply logistics. These initiatives reflect a broader industry shift toward resilience and agility, as stakeholders adapt to policy shifts that influence global trade flows and competitive dynamics.
Decoding Market Segments for Targeted Strategy
Analyzing resin type segmentation illuminates the divergent performance and processing characteristics shaping supplier strategies. Thermoset formulations continue to dominate applications requiring exceptional thermal stability and chemical resistance, with epoxy variants prized for their mechanical strength and bismaleimide resins chosen for high-temperature environments. Phenolic systems occupy a niche in flame-retardant applications, offering critical protection in defense and industrial contexts. In parallel, emerging thermoplastic prepregs are gaining traction due to their rapid cycle times and recyclability, attracting interest from automotive and consumer electronics manufacturers seeking sustainable solutions.
Product form segmentation reveals distinct handling and manufacturing benefits tailored to production volumes and component complexity. Rolls provide flexibility for large-scale layup processes, accommodating extensive surface areas in wind turbine blades and automotive body panels. Sheets offer precision for moderately sized components, optimizing material utilization in aerospace interiors and specialty enclosures. Tapes facilitate automated placement in high-volume applications, enabling rapid contour conformance for critical structural elements in next-generation aircraft and performance vehicles.
Application segmentation underscores the breadth of carbon fiber prepreg utilization across diverse industries. In aerospace and defense, commercial aircraft incorporate lightweight fuselage and wing structures, while military platforms leverage high-temperature resins for thermal protection systems and spacecraft demand ultra-lightweight laminates for launch vehicle components. The automotive sector is bifurcated between electric vehicles, where battery casings and structural reinforcements improve range efficiency, and internal combustion engine vehicles, where weight reduction enhances fuel economy. Marine applications span commercial vessels, which require robust hull reinforcements, to recreational craft that prioritize performance and aesthetics. Sports and leisure products range from bicycles that maximize stiffness, to protective gear designed for impact mitigation, and rackets and bats optimized for responsiveness. In wind energy, offshore installations depend on extra-large blades capable of handling extreme conditions, while onshore turbines benefit from lighter assemblies that streamline transportation and installation.
This comprehensive research report categorizes the Carbon Fiber Prepreg market into clearly defined segments, providing a detailed analysis of emerging trends and precise revenue forecasts to support strategic decision-making.
- Resin Type
- Product Form
- Application
Regional Dynamics Driving Prepreg Adoption Globally
The Americas region is characterized by mature aerospace supply chains and expanding automotive electrification initiatives. Leading manufacturers and OEMs are heavily invested in lightweight solutions to meet rigorous safety standards and reduce lifecycle emissions. Collaboration between government agencies and private enterprises stimulates research into advanced composite technologies, while robust infrastructure supports accelerated adoption across industrial hubs.
In Europe, Middle East & Africa, regulatory mandates on vehicle efficiency and renewable energy deployment drive demand for high-performance prepreg materials. Automotive clusters in Western Europe prioritize integrated manufacturing ecosystems, combining resin innovation with fiber production to reduce carbon footprints. Meanwhile, wind energy developers in Northern Europe and the Middle East are commissioning new offshore farms, creating opportunities for large-scale prepreg applications. In Africa, emerging defense modernization programs are prompting baseline investments in composite armoring and specialty components.
Asia-Pacific remains a focal point for manufacturing capacity expansion and technological adoption. Rapid electrification in major markets stimulates growth in automotive and consumer electronics segments, while government subsidies for wind power projects fuel offshore blade production. Regional producers are investing in localized resin formulation and fiber treatment facilities to optimize supply chain resilience and cost competitiveness. Cross-border partnerships and joint ventures are facilitating technology transfer, accelerating the integration of cutting-edge prepreg advancements across the region.
This comprehensive research report examines key regions that drive the evolution of the Carbon Fiber Prepreg market, offering deep insights into regional trends, growth factors, and industry developments that are influencing market performance.
- Americas
- Europe, Middle East & Africa
- Asia-Pacific
Profiling Leading Players in Carbon Fiber Prepreg
Major players in the carbon fiber prepreg arena have varied strengths that define their competitive positioning. Some firms excel in high-temperature resin systems, leveraging decades of aerospace experience to deliver materials that withstand extreme thermal and mechanical stresses. Others focus on thermoplastic innovation, pioneering recyclable formulations that address circular economy objectives and support rapid manufacturing cycles in automotive contexts.
Key industry leaders have also invested heavily in automated production platforms, deploying tailored fiber placement machines that achieve consistent quality at scale. Partnerships with equipment manufacturers and software developers have accelerated the rollout of integrated solutions, enabling end-users to seamlessly transition from design to full-scale fabrication. This collaborative model fosters continuous improvement, as feedback loops among material scientists, process engineers, and OEMs drive incremental enhancements in performance and cost efficiency.
Strategic alliances between resin formulators and fiber suppliers are further shaping competitive dynamics. By co-developing reinforced fabrics and optimizing matrix compatibility, these joint ventures reduce lead times and expand the range of viable applications. Some companies are establishing regional manufacturing footprints to capitalize on emerging markets, ensuring proximity to growth areas and minimizing logistical complexities. Collectively, these initiatives reflect an industry-wide commitment to advancing material technologies while addressing the supply chain challenges that accompany rapid demand shifts.
This comprehensive research report delivers an in-depth overview of the principal market players in the Carbon Fiber Prepreg market, evaluating their market share, strategic initiatives, and competitive positioning to illuminate the factors shaping the competitive landscape.
- Toray Industries, Inc.
- Hexcel Corporation
- Teijin Limited
- Mitsubishi Chemical Corporation
- Solvay S.A.
- SGL Carbon SE
- Gurit Holding AG
- Hyosung Corporation
- Weihai Guangwei Composite Materials Co., Ltd.
- Haining ANJIE Composite Materials Co., Ltd.
Strategic Imperatives for Industry Advancement
Industry participants should prioritize investment in advanced resin chemistries, focusing on thermoplastic systems that offer accelerated cure cycles and end-of-life recyclability. By integrating bio-based monomers and exploring additive manufacturing compatibility, organizations can address sustainability mandates and differentiate their offerings in a crowded marketplace. Scaling these innovations through pilot programs and targeted application trials will build confidence among OEMs and facilitate broader adoption.
Diversification of supply chains is equally critical, especially in the wake of evolving trade policies and tariffs. Establishing alternative sourcing agreements and qualifying multiple fiber and resin suppliers can mitigate the risk of disruptions. Concurrently, forging strategic partnerships with regional production hubs ensures proximity to key end-use markets, reducing lead times and enhancing responsiveness to fluctuating demand.
Adoption of digital process controls and advanced analytics will unlock efficiency gains across the value chain. Implementing real-time monitoring for cure cycles, fiber alignment, and resin distribution enables rapid identification of quality deviations, minimizing scrap and rework. Additionally, leveraging data-driven insights to optimize inventory levels and streamline logistics fosters agility and cost discipline. By embracing these strategic imperatives, leaders can secure a competitive advantage and navigate the next phase of market evolution.
Methodological Rigor Underpinning Our Analysis
This analysis is grounded in a rigorous multi-stage research approach that synthesizes secondary and primary sources. Extensive reviews of technical papers, patent filings, and industry association publications provided foundational insights into resin technology developments and manufacturing innovations. Complementing this desk research, targeted interviews with composite engineers, procurement executives, and regulatory specialists yielded practical perspectives on application requirements and policy dynamics.
Data triangulation ensured the validity of qualitative findings, as observations from supply-side interviews were cross-referenced with demand-centered discussions among OEM strategists. Analytical frameworks such as Porter’s Five Forces and SWOT analysis were applied to evaluate competitive intensity and identify strategic levers. Segmentation analysis delivered clarity on the performance attributes most valued across resin types, product forms, and applications.
Regional assessments incorporated trade flow data and infrastructure mapping to capture the nuances of market access and logistical dependencies. Rigorous validation of key insights through stakeholder workshops enhanced the robustness of our conclusions. This methodological rigor underpins the recommendations and strategic considerations presented herein, offering decision-makers a comprehensive foundation for informed action.
Explore AI-driven insights for the Carbon Fiber Prepreg market with ResearchAI on our online platform, providing deeper, data-backed market analysis.
Ask ResearchAI anything
World's First Innovative Al for Market Research
Synthesis and Forward-Thinking Perspectives
The trajectory of carbon fiber prepreg underscores a confluence of innovation, regulatory influences, and market diversification. Technological strides in resin systems and process automation are meeting heightened demands for performance and sustainability across industries. At the same time, policy interventions such as tariffs and environmental mandates are reshaping supply chains and compelling stakeholders to adopt resilient strategies.
Through detailed segmentation and regional examination, we have illuminated the distinct value propositions driving adoption in aerospace, automotive, marine, renewable energy, and consumer applications. Profiling the industry’s leading players reveals a landscape defined by collaboration, vertical integration, and relentless pursuit of next-generation materials. As competitive intensity intensifies, organizations that invest in advanced chemistries, digital controls, and supply chain agility will emerge as market leaders.
In the face of evolving challenges, informed decision-making remains paramount. Stakeholders must synthesize technical, commercial, and policy insights to chart a path that aligns performance imperatives with long-term strategic goals.
This section provides a structured overview of the report, outlining key chapters and topics covered for easy reference in our Carbon Fiber Prepreg market comprehensive research report.
- Preface
- Research Methodology
- Executive Summary
- Market Overview
- Market Dynamics
- Market Insights
- Cumulative Impact of United States Tariffs 2025
- Carbon Fiber Prepreg Market, by Resin Type
- Carbon Fiber Prepreg Market, by Product Form
- Carbon Fiber Prepreg Market, by Application
- Americas Carbon Fiber Prepreg Market
- Europe, Middle East & Africa Carbon Fiber Prepreg Market
- Asia-Pacific Carbon Fiber Prepreg Market
- Competitive Landscape
- ResearchAI
- ResearchStatistics
- ResearchContacts
- ResearchArticles
- Appendix
- List of Figures [Total: 22]
- List of Tables [Total: 414 ]
Secure Your In-Depth Carbon Fiber Prepreg Insights Today
For specialized guidance and to secure your comprehensive Carbon Fiber Prepreg market research report, connect with Ketan Rohom, Associate Director, Sales & Marketing. Engage directly to discuss tailored research packages and unlock the insights necessary for confident decision making. Partnering with an authority in industry analysis ensures you gain a strategic edge through deep market understanding and actionable data.
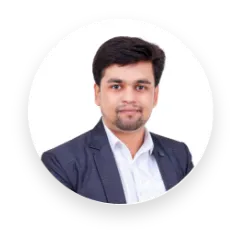
- How big is the Carbon Fiber Prepreg Market?
- What is the Carbon Fiber Prepreg Market growth?
- When do I get the report?
- In what format does this report get delivered to me?
- How long has 360iResearch been around?
- What if I have a question about your reports?
- Can I share this report with my team?
- Can I use your research in my presentation?