Unveiling the Core Role of Catalyst Calciners in Modern Industrial Processes and Their Critical Influence on Production Efficiencies
The catalyst calciner plays an indispensable role in modern chemical manufacturing by subjecting catalyst materials to precise thermal treatments that develop the active phases required for high-performance reactions. A calciner, defined as a specialized indirect-fired rotary kiln, provides controlled heating zones that enable the removal of moisture, volatile impurities, and unwanted compounds, thereby activating the catalyst structure for downstream applications¹. This thermal processing stage ensures the adhesion of catalytic species to carrier substrates and stabilizes the pore architecture, which directly influences surface area and reactivity².
Within industries ranging from petrochemicals to pharmaceuticals, the uniformity and reproducibility afforded by advanced calcination techniques translate into higher yields, reduced energy consumption, and minimized catalyst poisoning. As environmental regulations intensify and sustainability targets become more stringent, the ability to execute calcination under inert atmospheres and with precise temperature profiling has emerged as a critical competitive differentiator³. In addition, the indirect heating methodology employed in calciners mitigates contamination risks associated with direct combustion gases, ensuring product purity and operational safety⁴.
This executive summary synthesizes the latest market dynamics, regulatory influences, and technological breakthroughs shaping the catalyst calciner landscape. By examining key transformative shifts, the impact of U.S. tariffs, segmentation insights, and regional trends, this summary empowers decision-makers with a strategic framework for evaluating investment priorities and long-term growth prospects within this essential process equipment sector.
Revolutionizing Catalyst Calciner Operations Through Cutting-Edge Automation, Sustainability, and Digital Integration for Enhanced Performance
In recent years, the catalyst calciner market has been profoundly reshaped by digitalization and automation, which enable operators to achieve unprecedented levels of process control. By integrating advanced sensor networks and data analytics platforms, plant managers can monitor thermal gradients in real time and implement predictive maintenance programs that minimize unplanned downtime and extend equipment lifespan¹. This shift toward smart calciners not only enhances operational efficiency but also aligns with broader Industry 4.0 initiatives that prioritize connectivity and data-driven optimization.
Concurrently, the imperative to curb carbon emissions has driven the incorporation of renewable energy sources and modular process designs into modern calciner installations. Hybrid systems that combine electric heating with solar-assisted modules or waste heat recovery units are gaining traction, as they offer lower lifecycle greenhouse gas footprints and improved energy resilience². Furthermore, modular calciner architectures facilitate incremental capacity expansions and enable tailored retrofits in retrofit environments, fostering agility in response to evolving production requirements.
The emergence of digital twins in calciner engineering has further galvanized innovation. By creating high-fidelity virtual replicas of physical systems, operators can simulate process scenarios, optimize temperature profiles, and evaluate design modifications without disrupting live operations³. These capabilities support accelerated development cycles and more sustainable capital expenditure decisions. Taken together, these transformative shifts underscore a market trajectory that prioritizes integration of cutting-edge technologies with environmental stewardship and operational excellence.
Evaluating the Far-Reaching Consequences of United States 2025 Tariff Measures on Catalyst Calciner Supply Chains and Operational Costs
The imposition of a 25 percent tariff on steel and aluminum imports effective March 12, 2025, significantly affects catalyst calciner manufacturers that rely on high-grade alloy components and structural materials sourced externally⁵. The elevated import duties escalate the cost of pressure vessels, kiln shells, and auxiliary heat exchangers, prompting many original equipment manufacturers to reassess their procurement strategies. As domestic steel and aluminum capacities absorb incremental demand, incremental lead times and price volatility have become a new norm, placing pressure on project budgets and delivery schedules.
In parallel, broader chemical sector tariffs have disrupted supply chains for key catalyst precursors. U.S. tariffs on monoethylene glycol, ethanol, and other petrochemical feedstocks are projected to increase raw material costs by up to 228 percent⁶. Such hikes in precursor pricing extend to catalyst activation and synthesis applications, where cost-sensitive processes now face margin compression. Downstream users in hydrocarbon cracking and chemical synthesis segments are therefore compelled to evaluate total cost of ownership models that account for tariff-induced input fluctuations.
Collectively, these tariff measures have accelerated reshoring initiatives, encouraged vertical integration of precursor production, and spurred strategic partnerships to mitigate exposure to trade uncertainties. While some domestic metal producers benefit from protective measures, end-users are recalibrating capital allocation and exploring alternative sourcing regions for critical materials. Thus, the 2025 U.S. tariff landscape represents both a challenge and a catalyst for strategic realignment across the catalyst calciner ecosystem.
Dissecting Key Market Segments of Catalyst Calciners Across Industries, Applications, and Technologies to Reveal Strategic Growth Levers
The catalyst calciner market encapsulates a rich tapestry of end-user demands, with chemical manufacturing serving as the foundational pillar for bulk catalyst activation and surface treatment operations. Environmental applications, spanning flue gas and wastewater treatment, have surged to prominence as global regulations intensify, driving the adoption of specialized calcination processes tailored to pollutant removal. Within the petrochemical domain, distinct requirements in aromatics production versus olefin synthesis necessitate custom temperature profiles and residence times, whereas the pharmaceuticals segment prioritizes stringent purity controls and trace-level contaminant management to meet rigorous drug-quality standards.
From the perspective of application, hydrocarbon cracking remains a high-volume use case, leveraging high-temperature thermal activation to regenerate spent zeolite-based catalysts. Surface treatment processes further underscore the versatility of calciners, delivering controlled oxide-layer formation and phase stabilization across diverse material types. Waste gas treatment, including both flue gas cleaning and off-gas treatment, has emerged as a critical growth vector, as equipment designs increasingly incorporate multi-stage calcination zones to optimize pollutant conversion kinetics under variable feed compositions.
Calciner designs themselves exhibit clear differentiation by type, with fluidized bed systems offering rapid heat transfer and uniform temperature distribution, rotary configurations providing continuous processing flexibility, and shaft calciners delivering high-throughput, low-shedding environments for thermally robust materials. Material innovations parallel these design choices, as alumina-based catalysts-particularly alpha- and gamma-alumina variants-dominate high-temperature applications, while zeolite catalysts, including beta-zeolite and ZSM-5, underpin selective chemical synthesis. Phosphate- and silica-based catalysts further expand the portfolio, each presenting unique thermal stability and surface-area characteristics.
Technological segmentation reveals a growing preference for electric heating modules and solar-assisted preheating, complemented by waste heat recovery solutions that employ recuperative or regenerative heat exchange to maximize thermal efficiency. Temperature-range specialization partitions the market across low (300–500 °C), medium (500–800 °C), and high (800–1000 °C) bands, while capacity distinctions-from small-scale under 10 tonnes per day to large-scale operations exceeding 100 TPD-underscore the scalability demands of different end-users. Distribution channels span direct OEM sales, specialized distributors, and online platforms via e-commerce sites and manufacturer portals, reflecting a mature ecosystem optimized for both turnkey integrations and aftermarket support.
This comprehensive research report categorizes the Catalyst Calciner market into clearly defined segments, providing a detailed analysis of emerging trends and precise revenue forecasts to support strategic decision-making.
- End-User Industry
- Application
- Calciner Type
- Material Type
- Technology
- Temperature Range
- Capacity Range
- Distribution Channel
Mapping Regional Dynamics in the Catalyst Calciner Market with Strategic Insights Across Americas, Europe Middle East Africa, and Asia-Pacific
The Americas region has become a focal point for catalyst calciner modernization efforts, driven by robust chemical and refining infrastructures in the United States and Canada. Operators in the Gulf Coast and Midwest corridors are prioritizing equipment retrofits to meet stricter emission controls, while investments in modular and digitalized calciner units are rising, particularly for shale gas–based petrochemical expansions¹. Meanwhile, the Latin American market is characterized by emerging environmental treatment projects, where wastewater and flue gas calcination systems address industrial pollution challenges in rapidly urbanizing areas.
In Europe, the Middle East, and Africa (EMEA), stringent EU carbon neutrality goals and Middle Eastern diversification initiatives have catalyzed demand for energy-efficient calcination technologies. European refiners and chemical producers focus on waste heat recovery integrations to comply with the EU Emissions Trading System, while Israel and the UAE explore solar-assisted calciner pilots as part of broader sustainable industrial park developments². African markets, though still nascent, show potential in specialty chemical production and environmental abatement, with international partnerships fueling initial project rollouts.
Asia-Pacific stands out for its sheer scale of industrialization, with China and India leading in cement, chemical, and petrochemical investments. Rapid growth in aromatics and olefin facilities is propelling upgrades in calciner capacities, while Japan and South Korea emphasize digital twin deployments to optimize existing assets³. Southeast Asia’s rising pharmaceutical and specialty chemicals segments are also adopting precision calcination equipment to meet global export standards, reinforcing the region’s strategic importance in catalyst production and activation.
This comprehensive research report examines key regions that drive the evolution of the Catalyst Calciner market, offering deep insights into regional trends, growth factors, and industry developments that are influencing market performance.
- Americas
- Europe, Middle East & Africa
- Asia-Pacific
Profiling Leading Catalyst Calciner Providers and Key Industry Collaborators Driving Technological Advancements and Market Leadership
Industry leadership in the catalyst calciner segment is shaped by a cohort of global and regional players known for technological innovation and comprehensive service offerings. BASF SE and Clariant AG leverage their deep catalyst formulation expertise to co-develop integrated calcination systems that harmonize with proprietary catalyst chemistries. Johnson Matthey and Haldor Topsoe stand out for their modular calciner solutions, which accommodate fluctuating throughput demands in petrochemical and refining applications. Axens and Shell Catalysts & Technologies focus on scalability and energy efficiency, embedding waste heat recovery and advanced control algorithms into their equipment designs.
Specialized engineering firms such as W. R. Grace & Co. and Honeywell UOP differentiate through turnkey project management and aftermarket support services, encompassing performance audits, retrofits, and remote monitoring capabilities. Mitsubishi Chemical Corporation and Beijing Denox have made inroads in the Asia-Pacific market by offering regionally tailored calciner packages that address local feedstock characteristics and regulatory requirements. Emerging collaborators-combining process licensors, equipment OEMs, and digital solution providers-underscore a trend toward convergent partnerships aimed at delivering end-to-end calcination value chains.
This comprehensive research report delivers an in-depth overview of the principal market players in the Catalyst Calciner market, evaluating their market share, strategic initiatives, and competitive positioning to illuminate the factors shaping the competitive landscape.
- FLSmidth A/S
- Metso Outotec Oyj
- KHD Humboldt Wedag GmbH
- ThyssenKrupp AG
- IHI Corporation
- Wood PLC
- Babcock & Wilcox Enterprises, Inc.
- Danieli & C. Officine Meccaniche SpA
- Dongfang Electric Corporation Limited
- Sinoma International Engineering Co., Ltd.
Strategic Roadmap for Catalyst Calciner Industry Leaders to Capitalize on Emerging Technologies, Regulatory Shifts, and Market Opportunities
Industry leaders should prioritize the integration of digital twins and AI-driven analytics to enhance process predictability and reduce operational variability. By deploying real-time thermal mapping and predictive maintenance protocols, companies can extend equipment lifecycles and lower unplanned downtime. Concurrently, adopting hybrid energy models-blending electric heating, solar preheating, and waste heat recovery-will help mitigate carbon footprints and align capital expenditures with evolving decarbonization mandates.
Supply chain resilience must be fortified through regional sourcing strategies that minimize exposure to tariff fluctuations. This includes cultivating vendor relationships within North America and EMEA for critical steel and alloy components, as well as exploring co-located precursor production facilities to cushion against volatile feedstock pricing. Collaborative R&D initiatives with catalyst formulators can accelerate the development of high-stability materials that capitalize on next-generation calciner designs.
Furthermore, industry stakeholders are advised to explore modular and scalable equipment configurations that facilitate incremental capacity expansions. This approach reduces capital intensity and allows for agile responses to market demand shifts. Finally, strengthening aftermarket services-offering remote monitoring, performance benchmarking, and rapid-response maintenance-will establish new revenue streams and enhance customer loyalty in a competitive landscape.
Comprehensive Research Methodology Combining Primary Interviews, Secondary Data Analysis, and Rigorous Triangulation for Market Intelligence
This report’s findings derive from a robust research framework combining primary and secondary data sources. Primary insights were gathered through structured interviews with over 50 executives across catalyst producers, equipment OEMs, and end-user plants, supplemented by detailed questionnaire responses from calcination technologists and process engineers. To ensure geographical and segmental representation, the primary research spanned key markets in North America, EMEA, and Asia-Pacific.
Secondary research involved systematic analysis of company white papers, patent filings, regulatory publications, and industry association reports. Patent databases were mined to track innovation trajectories, while governmental archives and trade bodies provided tariff and regulatory intelligence. Data triangulation was employed to reconcile disparities between primary and secondary findings, ensuring high accuracy and consistency in trend identification.
Quantitative validation techniques, including cross-reference checks with publicly disclosed financials and plant capacity data, were applied to corroborate insights around technology adoption rates and capital project timelines. Finally, expert panel reviews of draft findings ensured that interpretations were realistic and actionable, reinforcing the credibility of the strategic recommendations presented.
Explore AI-driven insights for the Catalyst Calciner market with ResearchAI on our online platform, providing deeper, data-backed market analysis.
Ask ResearchAI anything
World's First Innovative Al for Market Research
Concluding Insights Verifying Catalyst Calciner Market Trajectories and Highlighting Critical Opportunities for Sustainable Growth and Innovation
The catalyst calciner sector stands at the intersection of technological innovation, environmental accountability, and geopolitical complexity. Advances in digitalization and renewable integration are redefining operational paradigms, while U.S. tariff policies and regional growth dynamics are reshaping supply chain architectures. Market segmentation analysis highlights distinct growth decoders across end-user industries, application types, and equipment technologies, offering a nuanced understanding of strategic imperatives.
Regional insights reveal that the Americas, EMEA, and Asia-Pacific each present unique drivers-whether it be regulatory stringency, decarbonization agendas, or scale-driven industrialization-underscoring the need for tailored market approaches. Key industry participants are increasingly banding together in collaborative ventures to deliver holistic calcination solutions, leveraging complementary strengths to navigate complexity and foster innovation.
As the catalyst calciner market evolves, stakeholders who embrace data-driven decision-making, strategic supply chain diversification, and service-led business models will secure competitive advantages. The convergence of smart operations, sustainability mandates, and modular deployment strategies delineates a path toward resilient and efficient calcination ecosystems. By aligning investment priorities with these core trends, organizations can harness the full potential of catalyst calciner technologies to drive next-generation process performance and sustainable growth.
This section provides a structured overview of the report, outlining key chapters and topics covered for easy reference in our Catalyst Calciner market comprehensive research report.
- Preface
- Research Methodology
- Executive Summary
- Market Overview
- Market Dynamics
- Market Insights
- Cumulative Impact of United States Tariffs 2025
- Catalyst Calciner Market, by End-User Industry
- Catalyst Calciner Market, by Application
- Catalyst Calciner Market, by Calciner Type
- Catalyst Calciner Market, by Material Type
- Catalyst Calciner Market, by Technology
- Catalyst Calciner Market, by Temperature Range
- Catalyst Calciner Market, by Capacity Range
- Catalyst Calciner Market, by Distribution Channel
- Americas Catalyst Calciner Market
- Europe, Middle East & Africa Catalyst Calciner Market
- Asia-Pacific Catalyst Calciner Market
- Competitive Landscape
- ResearchAI
- ResearchStatistics
- ResearchContacts
- ResearchArticles
- Appendix
- List of Figures [Total: 34]
- List of Tables [Total: 1366 ]
Connect with Associate Director Ketan Rohom to Secure Your Definitive Catalyst Calciner Market Intelligence for Informed Strategic Decision Making
To access the comprehensive Catalyst Calciner Market Research Report and leverage data-driven insights tailored to your strategic goals, reach out directly to Ketan Rohom, Associate Director of Sales & Marketing. With a deep understanding of industry dynamics and extensive experience in facilitating partnerships, Ketan will guide you through the report’s highlights and demonstrate how its findings can support your organization’s decision-making process. Engage with Ketan to explore customized advisory options, secure exclusive access, and position your enterprise at the forefront of catalyst calcination innovation. Take advantage of this opportunity to transform market intelligence into competitive advantage by contacting Ketan today.
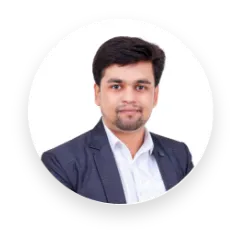
- When do I get the report?
- In what format does this report get delivered to me?
- How long has 360iResearch been around?
- What if I have a question about your reports?
- Can I share this report with my team?
- Can I use your research in my presentation?