Introduction to the CCD Visual Inspection Equipment Market
In an era where precision manufacturing and zero-defect mandates define competitive advantage, charge-coupled device (CCD) visual inspection equipment has become an indispensable cornerstone of quality assurance. Combining high-resolution imaging with real-time processing, CCD-based systems enable manufacturers to detect flaws, verify assembly integrity, and measure critical dimensions at speeds previously unattainable. The convergence of advanced optics, machine learning algorithms, and edge computing has transformed these devices from standalone vision modules into integrated components of smart production lines.
Industry stakeholders are increasingly reliant on these systems to uphold stringent regulatory requirements and customer expectations. From the detection of microscopic surface irregularities in semiconductor wafers to the verification of complex composite structures in aerospace parts, CCD inspection solutions deliver both the granularity and throughput necessary for modern operations. As manufacturing cycles accelerate and product complexity grows, the scalability and adaptability of visual inspection platforms determine not only operational efficiency but also long-term growth trajectories.
This executive summary encapsulates the critical trends, regulatory influences, segmentation dynamics, regional variances, competitive landscape, and strategic pathways that define the CCD visual inspection market today. It aims to equip decision-makers with clarity on where the industry is headed, how external forces reshape priorities, and which levers will unlock sustainable value.
Transformative Shifts Shaping the CCD Visual Inspection Sector
Over the past five years, the CCD visual inspection landscape has undergone transformative shifts driven by technological convergence and evolving production paradigms. Traditional two-dimensional image capture has been complemented - and in some applications overtaken - by advanced three-dimensional inspection methods, including laser profiling, stereoscopic vision, and time-of-flight. This transition responds to a growing demand for volumetric data that can identify defects invisible to planar imaging, particularly in semiconductor wafer inspection and composite structure assessment in aerospace.
Simultaneously, the integration of machine learning algorithms into inspection workflows has redefined system capabilities. Rather than relying solely on rule-based thresholding, modern platforms employ neural network models trained to recognize complex defect patterns across dimensional flaws, structural anomalies, and surface irregularities. This shift enhances detection accuracy while reducing false positives, a critical improvement in high-precision sectors such as medical device manufacturing.
Moreover, the proliferation of edge computing resources allows image processing to occur in close proximity to imaging hardware, minimizing latency and network bandwidth consumption. As manufacturers pursue industry 4.0 objectives, CCD visual inspection systems have evolved from isolated subsystems to fully networked devices that contribute to predictive maintenance, real-time analytics, and adaptive process control. This seamless connectivity underpins higher throughput on continuous manufacturing lines and supports both inline and offline inspection strategies.
Assessing the Cumulative Impact of US Tariffs Coming into Effect in 2025
Anticipated United States tariff implementations in 2025 introduce a pivotal inflection point for CCD visual inspection supply chains. Components such as high-performance sensors, specialized lenses, and semiconductor-based frame grabbers sourced from regions under new levy conditions face cost escalations that ripple through system integrators and end users. As a result, original equipment manufacturers must reevaluate their bill-of-materials strategies and assess the total landed cost of inspection modules.
Rather than absorbing higher duties, many stakeholders are proactively diversifying sourcing portfolios to include suppliers in allied markets or accelerating the qualification of domestic manufacturers. Nearshoring initiatives are gaining traction, with several system providers negotiating partnerships that ensure preferential trade terms and reduce exposure to cross-border delays. Meanwhile, smaller integrators confront sharper financial pressure, prompting consolidation among service providers and fostering collaborative models for shared testing facilities.
In parallel, engineering teams are optimizing optical architectures to reduce reliance on components most affected by tariffs, while software investments aim to extract greater performance from existing hardware configurations. Although short-term implementation challenges may slow adoption rates, these strategic adjustments are poised to yield long-term resilience and foster a more robust domestic ecosystem for CCD visual inspection equipment.
Key Segmentation Insights Driving Market Dynamics
A nuanced understanding of market segmentation reveals the multifaceted drivers influencing investment priorities. When viewed through the lens of technology type, two-dimensional inspection-split between color and monochrome imaging-continues to address general-purpose surface and defect analysis, whereas three-dimensional techniques such as laser profiling, stereoscopic vision, and time-of-flight enable volumetric measurement and surface topography mapping in critical industries. Application type further refines these trends: solutions focused on defect detection handle dimensional flaws, structural anomalies, and surface defects, while measurement instruments encompass coordinate measurement machines, laser scanners, and optical gauges for precise metrology tasks.
Component type segmentation underscores the balance between hardware elements-cameras, frame grabbers, lenses, lighting systems, and sensors-and the software layer, which includes both traditional image processing routines and advanced machine learning algorithms. Industry vertical applications range from aerospace component manufacturing, composite inspection, and structural health monitoring to automotive assembly verification, component inspection, and paint finishing, as well as semiconductor wafer inspection, packaging inspection, and chip validation. End-user type distinguishes manufacturing production lines and quality control functions from pharmaceutical packaging inspection and tablet verification, reflecting regulatory and batch-sensitivity requirements.
Inspection type segmentation, spanning inline inspection on continuous and high-speed lines to offline inspection in batch and critical parts scenarios, aligns with production cadence and risk profiles. Finally, capability type classification into high, medium, and low precision guides specification matching, ensuring that system performance aligns with tolerance thresholds. Together, these segmentation dimensions empower stakeholders to align technology investments with use-case demands and operational objectives.
This comprehensive research report categorizes the CCD Visual Inspection Equipment market into clearly defined segments, providing a detailed analysis of emerging trends and precise revenue forecasts to support strategic decision-making.
- Technology Type
- Application Type
- Component Type
- Industry Vertical
- End-User Type
- Inspection Type
- Capability Type
Key Regional Insights Across Major Global Markets
Regional nuances play a decisive role in shaping adoption patterns and technology road maps. In the Americas, robust demand from the automotive and aerospace sectors underscores the importance of high-speed, high-precision inspection solutions on production lines that prioritize throughput and defect prevention. Collaboration between integrators and vehicle manufacturers in North America has accelerated the deployment of inline continuous inspection, especially for safety-critical assemblies.
Meanwhile, Europe, the Middle East & Africa present a landscape defined by stringent regulatory frameworks-particularly within the pharmaceutical and aerospace verticals-that drive the uptake of validated systems for composite inspection and structural health monitoring. Companies in the EMEA region often integrate portable offline stations alongside full-scale inline installations to accommodate varying compliance requirements and batch sizes.
In Asia-Pacific, the semiconductor and consumer electronics manufacturing clusters in China, South Korea, Taiwan, and Japan sustain the fastest adoption rates. Government incentives aimed at reshoring critical industries further stimulate capital investments in both hardware and software capabilities. Across the region, a growing emphasis on smart factory architectures has elevated the role of connected inspection modules that feed into enterprise resource planning and manufacturing execution systems.
This comprehensive research report examines key regions that drive the evolution of the CCD Visual Inspection Equipment market, offering deep insights into regional trends, growth factors, and industry developments that are influencing market performance.
- Americas
- Asia-Pacific
- Europe, Middle East & Africa
Key Insights into Leading CCD Visual Inspection Equipment Providers
The competitive landscape is defined by a cohort of established technology providers and agile innovators. Companies such as Cognex Corporation and Keyence Corporation lead in integrated machine vision solutions, combining proprietary image processing and deep learning frameworks with modular hardware designs. Basler AG and Allied Vision Technologies GmbH specialize in high-performance camera sensors that deliver exceptional image fidelity for color and monochrome applications, while Teledyne DALSA and ISRA Vision AG extend those capabilities into three-dimensional inspection with laser profiling and stereoscopic vision.
On the software front, Adaptive Vision Sp. z o.o. and National Instruments Corporation provide flexible development environments that empower end users to tailor algorithms to bespoke inspection challenges. In contrast, KUKA AG integrates robotic handling with vision systems to create turnkey automation cells for high-precision assembly verification. Banner Engineering Corp., Datalogic S.p.A., and SICK AG focus on industrial-grade sensor networks and lighting systems that complement core imaging modules, ensuring reliable performance in harsh production environments.
Further specialization is evident in the pharmaceutical and packaging sectors, where Omron Corporation and Zebra Technologies Corporation deliver inline barcode scanning and tablet verification solutions. VITRONIC Dr.-Ing. Stein Bildverarbeitungssysteme GmbH emphasizes integrated track-and-trace architectures, and ISRA Vision AG supports composite structural health monitoring for aerospace. Through strategic partnerships and continuous R&D investment, these leading manufacturers drive feature enhancements, cost efficiencies, and faster time to deployment.
This comprehensive research report delivers an in-depth overview of the principal market players in the CCD Visual Inspection Equipment market, evaluating their market share, strategic initiatives, and competitive positioning to illuminate the factors shaping the competitive landscape.
- Adaptive Vision Sp. z o.o.
- Allied Vision Technologies GmbH
- Banner Engineering Corp.
- Basler AG
- Cognex Corporation
- Datalogic S.p.A.
- ISRA Vision AG
- Keyence Corporation
- KUKA AG
- National Instruments Corporation
- Omron Corporation
- SICK AG
- Teledyne DALSA
- VITRONIC Dr.-Ing. Stein Bildverarbeitungssysteme GmbH
- Zebra Technologies Corporation
Actionable Recommendations for Industry Leaders in CCD Inspection
Industry leaders seeking to capitalize on these dynamics should prioritize a series of strategic initiatives. First, investing in advanced analytics and machine learning integration will enhance defect detection accuracy and reduce reliance on manual oversight. Second, diversifying supply chains to include qualified domestic and alliance-based component manufacturers will mitigate tariff-related disruptions and improve lead-time resilience. Third, adopting a modular hardware architecture allows for rapid scalability and tailored precision levels, from high-precision metrology to medium- and low-precision surface inspections.
Additionally, forging partnerships with software providers and research institutions can accelerate algorithm development for emerging defect profiles. Companies should also standardize communication protocols to facilitate seamless data exchange within smart factory ecosystems. To address workforce skills gaps, industry leaders must implement targeted training programs that equip technicians and engineers with expertise in vision system calibration and AI model validation. Lastly, enhancing cybersecurity measures for networked inspection modules will safeguard sensitive production data and maintain compliance with global data protection regulations.
Explore AI-driven insights for the CCD Visual Inspection Equipment market with ResearchAI on our online platform, providing deeper, data-backed market analysis.
Ask ResearchAI anything
World's First Innovative Al for Market Research
Conclusion: Navigating Opportunities in CCD Visual Inspection
As the CCD visual inspection market continues to evolve, organizations that align technology choices with operational demands, regulatory requirements, and regional considerations will achieve the greatest competitive advantage. By leveraging the insights outlined in this summary-from segmentation-driven use-case alignment to regional strategy execution and supplier diversification-stakeholders can build resilient, high-performance inspection ecosystems. The path forward emphasizes collaboration among hardware innovators, software developers, and end users, underpinned by a shared commitment to defect-free production and continuous improvement.
This section provides a structured overview of the report, outlining key chapters and topics covered for easy reference in our CCD Visual Inspection Equipment market comprehensive research report.
- Preface
- Research Methodology
- Executive Summary
- Market Overview
- Market Dynamics
- Market Insights
- Cumulative Impact of United States Tariffs 2025
- CCD Visual Inspection Equipment Market, by Technology Type
- CCD Visual Inspection Equipment Market, by Application Type
- CCD Visual Inspection Equipment Market, by Component Type
- CCD Visual Inspection Equipment Market, by Industry Vertical
- CCD Visual Inspection Equipment Market, by End-User Type
- CCD Visual Inspection Equipment Market, by Inspection Type
- CCD Visual Inspection Equipment Market, by Capability Type
- Americas CCD Visual Inspection Equipment Market
- Asia-Pacific CCD Visual Inspection Equipment Market
- Europe, Middle East & Africa CCD Visual Inspection Equipment Market
- Competitive Landscape
- ResearchAI
- ResearchStatistics
- ResearchContacts
- ResearchArticles
- Appendix
- List of Figures [Total: 30]
- List of Tables [Total: 902 ]
Call to Action: Engage with Ketan Rohom for In-Depth Market Research
For a comprehensive, data-rich market research report tailored to your strategic needs, contact Ketan Rohom, Associate Director, Sales & Marketing, to secure your copy and gain actionable insights into the CCD visual inspection landscape.
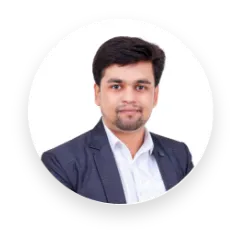
- When do I get the report?
- In what format does this report get delivered to me?
- How long has 360iResearch been around?
- What if I have a question about your reports?
- Can I share this report with my team?
- Can I use your research in my presentation?