Introduction to the Centrifugal Engine Sleeve Couplings Market Landscape
Over the past decade, centrifugal engine sleeve couplings have emerged as critical mechanical interfaces within high-performance rotating systems. By transmitting torque between engine components while accommodating misalignment and thermal expansion, these couplings play a pivotal role in sectors ranging from aerospace propulsion to heavy machinery. This executive summary explores the underlying market landscape, highlighting the technological advancements, regulatory influences, and competitive factors shaping industry evolution. Decision-makers will gain a concise overview of current trends, key drivers, and strategic considerations necessary to navigate this complex environment. The ensuing sections delve into transformative industry shifts, the ramifications of recent U.S. tariff measures, market segmentation analyses, regional dynamics, and an assessment of major manufacturers. We conclude with actionable recommendations to guide product innovation, operational excellence, and strategic partnerships, followed by an invitation to engage with our sales and marketing expert for comprehensive market intelligence. Strategic partnerships and M&A activity continue to shape competitive dynamics, enabling access to new materials and design capabilities while accelerating time to market. This report offers a foundation for informed decision-making and sustained competitive advantage in the centrifugal engine sleeve couplings sector.
Transformative Shifts Reshaping the Centrifugal Couplings Arena
Technological innovation has redefined expectations for engine coupling performance. High-temperature-resistant metal alloys and advanced thermoplastic composites now enable extended service life under extreme conditions. Meanwhile, precision fitting and interlocking sleeve designs have minimized vibration damping concerns, boosting reliability across aerospace and industrial applications. Concurrently, digitalization has introduced predictive maintenance capabilities through embedded sensors, shifting maintenance cycles from corrective to preventive models. Cost pressures have catalyzed a focus on lifecycle cost optimization, prompting manufacturers to refine production processes and leverage automation to lower material and labor costs. Environmental regulations and tightening safety certifications have elevated compliance standards, challenging established players to adhere to both company-specific guidelines and international norms. As the market adapts, firms that integrate multi-material compositions, innovative coupling mechanisms, and smart maintenance solutions will command a strategic advantage, redefining performance benchmarks and accelerating adoption across end-use segments.
These transformative shifts underscore a broader transition from traditional designs towards systems that deliver higher load capacity, enhanced operational temperature tolerance, and streamlined installation. By embracing modular design principles and retrofit compatibility, companies are tailoring offerings to meet diverse application requirements, from aerospace implementation to heavy industrial usage. As digital thread initiatives evolve, lifecycle traceability and provenance tracking for composite and alloy components become critical differentiators, further intensifying the need for integrated data platforms. This confluence of material science, digital integration, and regulatory alignment marks a new era in centrifugal coupling solutions, laying the groundwork for sustained growth and differentiation.
Cumulative Impact of U.S. Tariffs on Sleeve Couplings in 2025
Tariffs introduced by the United States in early 2025 have created complex layers of cost implications for imported raw materials and finished coupling assemblies. Import duties on specialized metal alloys, including corrosion-resistant and high-temperature-grade variants, have increased production costs for domestic manufacturers reliant on global supply chains. Secondary effects have surfaced as domestic producers adjust pricing to maintain margin thresholds, potentially impacting end-user budgets in energy and automotive sectors. Conversely, companies that have localized material sourcing or shifted to compliant thermoplastic composites have mitigated tariff exposure and gained a competitive edge. Supply chain acceleration measures, such as nearshoring and strategic stockpiling, have emerged as proactive responses to uncertainty, reducing lead times while buffering against future policy fluctuations. Importers are also exploring medium-term contracts and vendor-managed inventory models to stabilize pricing and supply volumes, supporting smoother production planning.
The cumulative tariff impact has therefore spurred diversification of mechanical designs, investment in regional manufacturing hubs, and a strategic reevaluation of lifecycle cost imperatives. Partnerships with logistics providers and custom alloy suppliers have become critical to circumventing tariff burdens. By integrating end-to-end supply chain analytics, firms can forecast cost variations, optimize inventory, and safeguard production schedules. Stakeholders that adapt swiftly to regulatory changes and realign material composition strategies will navigate the tariff landscape more effectively, preserving resilience and market share.
Key Segmentation Insights Driving Market Differentiation
Material composition represents a core segmentation axis, where composite materials cater to aerospace weight constraints, custom alloys address specialized corrosion resistance, metal alloys span corrosion-resistant and high-temperature-resistant grades for demanding environments, and thermoplastics deliver cost-competitive light-equipment solutions. Mechanical design-based distinctions emerge through coupling mechanisms that encompass bolt connections or pin type couplings alongside interlocking features, precision fitting tolerances, and sleeve geometries engineered for dynamic balance. Application requirements drive targeted deployments: aerospace implementations focus on weight-to-strength optimization, automotive integration prioritizes vibration damping and extended service life, energy sector applications demand operational temperature resilience, and industrial usage spans heavy machinery to light equipment with varying installation and maintenance demands. Performance standards further differentiate offerings by classifying load capacity into high, moderate, or low categories, defining operational temperature limits, mandating service life benchmarks, and evaluating vibration damping effectiveness. Installation and maintenance considerations, including ease of installation, retrofit compatibility, and the balance between corrective versus preventive maintenance cycles, directly influence total cost of ownership. Cost efficiency factors such as lifecycle cost analysis, operational efficiency metrics, granular production costs including labor and material inputs, and return on investment calculations inform buyer decisions. Finally, compliance requirements anchored in environmental regulations, mandatory safety certifications, and adherence to both internal company guidelines and international norms establish the regulatory framework for product certification. Understanding this multi-dimensional segmentation allows manufacturers to align R&D and marketing strategies with the nuanced demands of each target segment.
This comprehensive research report categorizes the Centrifugal Engine Sleeve Couplings market into clearly defined segments, providing a detailed analysis of emerging trends and precise revenue forecasts to support strategic decision-making.
- Material Composition
- Mechanical Design
- Application Requirements
- Performance Standards
- Installation And Maintenance
- Cost Efficiency Factors
- Compliance And Standards
Regional Dynamics and Their Influence on Market Growth
Growth in the Americas is propelled by robust automotive manufacturing in North America and expanding energy infrastructure projects in South America, creating strong demand for high-load and high-temperature-resistant sleeve couplings. Domestic suppliers have leveraged local alloy sourcing to mitigate import tariff impacts while capitalizing on retrofit compatibility to serve legacy equipment markets. In Europe, Middle East & Africa, stringent environmental regulations and rigorous safety certification standards drive adoption of advanced composite materials and precision-fitting designs. European OEMs prioritize service life and vibration damping for aerospace and industrial installations, whereas Middle Eastern energy producers focus on corrosion-resistant and high-temperature alloy solutions to withstand harsh operating conditions. African markets, though nascent, are emerging with investments in mining and power generation that favor durable heavy machinery couplings. The Asia-Pacific region exhibits a dichotomy of mature markets such as Japan and South Korea, where innovation in sleeve design and interlocking mechanisms leads the sector, and rapidly industrializing economies like India and Southeast Asia, which demand cost-efficient thermoplastic and standard metal alloy offerings. Strategic manufacturing hubs in China and ASEAN countries benefit from economies of scale, reducing production costs and accelerating delivery timelines. These regional dynamics underscore the necessity for tailored go-to-market approaches, balancing performance differentiation with cost competitiveness to address localized application profiles and regulatory landscapes.
This comprehensive research report examines key regions that drive the evolution of the Centrifugal Engine Sleeve Couplings market, offering deep insights into regional trends, growth factors, and industry developments that are influencing market performance.
- Americas
- Asia-Pacific
- Europe, Middle East & Africa
Competitive Landscape: Leading Players and Strategic Positioning
In the global centrifugal sleeve coupling market, a diverse roster of specialized manufacturers defines the competitive landscape. North American leaders such as Advanced Coupling Designs Corp., Advanced Engineering Couplings Inc., AeroCoupling Dynamics Corp., AeroTech Industries LLC, BlueSky Mechanical Systems, Centrifuge Couplings Corporation, Champion Engine Components, Dynamic Engine Solutions LLC, Eagle Precision Engineering Inc., Elite Rotor Dynamics Inc., Frontier Mechanical Engineering LLC, Fusion Motors Engineering, Galactic Engineering Corp., Infinity Coupling Innovations Inc., Innovative Power Systems Inc., National Engineering Couplings Ltd., NexGen Mechanical Solutions, Nimbus Industrial Engineering, Omega Industrial Couplings Corp., OmniTech Engine Solutions, Pinnacle Industrial Products LLC, Precision Engine Components Inc., Prime Mechanical Innovations Ltd., Prime Power Couplings LLC, ProLink Mechanical Inc., Quantum Mechanical Systems Corp., Skybound Couplings Solutions, Stellar Power Systems Inc., Sterling Engine Controls Ltd., StratoTech Manufacturing Ltd., Titan Engineering & Couplings, TurboFusion Technologies LLC, Ultra Coupling Technologies Inc., Vertex Engine Technologies, Vertex Industrial Solutions Inc., and Zenith Coupling Systems Ltd. are instrumental in setting performance benchmarks across segments. Among these, Advanced Engineering Couplings Inc. and Champion Engine Components distinguish themselves through material composition research, while Elite Rotor Dynamics Inc. and StratoTech Manufacturing Ltd. lead in mechanical design innovation. AeroTech Industries LLC and Skybound Couplings Solutions have advanced composite material applications for aerospace, and Fusion Motors Engineering alongside Ultra Coupling Technologies Inc. prioritize cost efficiency and lifecycle cost optimization. Companies such as Quantum Mechanical Systems Corp. and OmniTech Engine Solutions are at the forefront of integrating predictive maintenance features, whereas NexGen Mechanical Solutions and Sterling Engine Controls Ltd. excel in meeting stringent compliance and safety certification requirements. This collective expertise fosters healthy competition, driving continuous product refinement and strategic partnerships.
This comprehensive research report delivers an in-depth overview of the principal market players in the Centrifugal Engine Sleeve Couplings market, evaluating their market share, strategic initiatives, and competitive positioning to illuminate the factors shaping the competitive landscape.
- Advanced Coupling Designs Corp.
- Advanced Engineering Couplings Inc.
- AeroCoupling Dynamics Corp.
- AeroTech Industries LLC
- BlueSky Mechanical Systems
- Centrifuge Couplings Corporation
- Champion Engine Components
- Dynamic Engine Solutions LLC
- Eagle Precision Engineering Inc.
- Elite Rotor Dynamics Inc.
- Frontier Mechanical Engineering LLC
- Fusion Motors Engineering
- Galactic Engineering Corp.
- Infinity Coupling Innovations Inc.
- Innovative Power Systems Inc.
- National Engineering Couplings Ltd.
- NexGen Mechanical Solutions
- Nimbus Industrial Engineering
- Omega Industrial Couplings Corp.
- OmniTech Engine Solutions
- Pinnacle Industrial Products LLC
- Precision Engine Components Inc.
- Prime Mechanical Innovations Ltd.
- Prime Power Couplings LLC
- ProLink Mechanical Inc.
- Quantum Mechanical Systems Corp.
- Skybound Couplings Solutions
- Stellar Power Systems Inc.
- Sterling Engine Controls Ltd.
- StratoTech Manufacturing Ltd.
- Titan Engineering & Couplings
- TurboFusion Technologies LLC
- Ultra Coupling Technologies Inc.
- Vertex Engine Technologies
- Vertex Industrial Solutions Inc.
- Zenith Coupling Systems Ltd.
Actionable Recommendations for Industry Leadership and Innovation
Industry leaders should prioritize material diversification to deliver tailored solutions for high-temperature and corrosion-resistant requirements while exploiting thermoplastic composites to capture cost-sensitive segments. Investing in modular mechanical designs that support both bolt connections and pin type couplings will facilitate streamlined installation and retrofit compatibility. Integrating embedded sensor networks within sleeve assemblies can enable predictive maintenance workflows, reducing downtime and shifting operational models toward preventive maintenance cycles. Companies must also adopt full-scope lifecycle cost analysis, optimizing production processes to balance labor and material expenditures while maximizing return on investment. Strengthening regional manufacturing footprints through strategic partnerships and nearshoring initiatives will mitigate tariff-induced supply chain risks and reduce lead times. Collaborating with industry bodies to shape compliance standards and accelerate certification processes can preempt regulatory bottlenecks and foster market access. A structured roadmap for digital transformation, encompassing end-to-end supply chain analytics and performance monitoring, will support data-driven decision-making and enhance operational efficiency. Finally, cultivating cross-sector alliances with aerospace, automotive, energy, and industrial equipment OEMs will uncover synergistic innovation opportunities and solidify long-term strategic relationships. By executing these targeted strategies, stakeholders will reinforce competitive positioning and capitalize on emerging growth avenues.
Explore AI-driven insights for the Centrifugal Engine Sleeve Couplings market with ResearchAI on our online platform, providing deeper, data-backed market analysis.
Ask ResearchAI anything
World's First Innovative Al for Market Research
Conclusion: Aligning Strategy with Emerging Opportunities
As centrifugal engine sleeve couplings become increasingly integral to advanced rotating systems, the convergence of material science, mechanical design, and regulatory dynamics is reshaping market contours. Transformative shifts such as sensor-enabled predictive maintenance, lifecycle cost optimization, and compliance-driven innovation underscore the complexity and opportunity inherent in this sector. The multifaceted segmentation framework-from material composition to performance standards-provides a strategic lens for aligning product portfolios with specific application and regional demands. Concurrently, major players across North America, EMEA, and Asia-Pacific are driving differentiation through targeted R&D and agile supply chain strategies. By synthesizing these insights, industry participants can navigate tariff challenges, regulatory requirements, and evolving customer expectations with greater confidence. This executive summary offers a foundational perspective that paves the way for informed strategy development, operational excellence, and sustained competitive advantage in the centrifugal engine sleeve coupling market.
This section provides a structured overview of the report, outlining key chapters and topics covered for easy reference in our Centrifugal Engine Sleeve Couplings market comprehensive research report.
- Preface
- Research Methodology
- Executive Summary
- Market Overview
- Market Dynamics
- Market Insights
- Cumulative Impact of United States Tariffs 2025
- Centrifugal Engine Sleeve Couplings Market, by Material Composition
- Centrifugal Engine Sleeve Couplings Market, by Mechanical Design
- Centrifugal Engine Sleeve Couplings Market, by Application Requirements
- Centrifugal Engine Sleeve Couplings Market, by Performance Standards
- Centrifugal Engine Sleeve Couplings Market, by Installation And Maintenance
- Centrifugal Engine Sleeve Couplings Market, by Cost Efficiency Factors
- Centrifugal Engine Sleeve Couplings Market, by Compliance And Standards
- Americas Centrifugal Engine Sleeve Couplings Market
- Asia-Pacific Centrifugal Engine Sleeve Couplings Market
- Europe, Middle East & Africa Centrifugal Engine Sleeve Couplings Market
- Competitive Landscape
- ResearchAI
- ResearchStatistics
- ResearchContacts
- ResearchArticles
- Appendix
- List of Figures [Total: 30]
- List of Tables [Total: 641 ]
Next Steps: Connect with Our Sales and Marketing Expert
To explore these findings in greater depth and access proprietary data, connect with Ketan Rohom, Associate Director, Sales & Marketing. Engaging directly with our expert will equip your organization with tailored insights, comprehensive competitive analyses, and actionable market intelligence. Secure your copy of the full research report today and position your business to capitalize on emerging trends and strategic opportunities in the centrifugal engine sleeve couplings market. Reach out to schedule a personalized briefing and gain immediate access to our detailed study, ensuring your decision-makers have the foresight needed to drive innovation and growth.
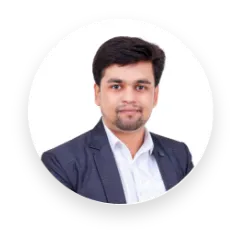
- When do I get the report?
- In what format does this report get delivered to me?
- How long has 360iResearch been around?
- What if I have a question about your reports?
- Can I share this report with my team?
- Can I use your research in my presentation?