Unveiling the strategic context and fundamental principles driving centrifugal grinding and finishing technologies across diverse industrial applications
The centrifugal grinding and finishing equipment sector has emerged as a pivotal enabler of precision and throughput in modern manufacturing. As industries demand ever-tighter tolerances and faster turnaround times, centrifugal machines have evolved to meet these requirements through innovative design, enhanced operational capabilities, and integration with digital tools. This introduction sets the stage by outlining the core principles of centrifugal processing, highlighting its unique ability to accelerate finishing cycles while maintaining consistent quality. More than simply an alternative to conventional barrel or vibratory finishing systems, centrifugal platforms optimize energy transfer and media dynamics to achieve accelerated material removal and surface enhancement.
With applications spanning from high-value aerospace components to delicate medical devices, the centrifugal approach bridges the gap between high-volume processing and exacting surface requirements. Leading machine builders now offer scalable configurations-spanning batch and continuous modes-that cater to diverse production scales and part geometries. Rapid advancements in control systems and sensor-driven monitoring have further increased adaptability, enabling operators to tune variables such as rotational speed, media charge, and compound dosing in real time. Consequently, this technology empowers manufacturers to shorten cycle times, minimize rework, and reduce total cost of ownership.
This report delves into the technological underpinnings, operational advantages, and market catalysts shaping centrifugal grinding and finishing machines. It frames the broader context by connecting evolving performance demands with design innovations, setting the foundation for deeper analysis of transformative shifts, tariff impacts, segmentation insights, and strategic recommendations that follow.
Exploring how automation, digital integration, and sustainable practices are reshaping the centrifugal finishing and grinding machine landscape in manufacturing
The centrifugal grinding and finishing landscape is experiencing a transformative shift driven by three interlocking forces: automation, digital integration, and sustainable practices. Manufacturers are embracing automated loading and unloading modules to reduce manual intervention, enhance process repeatability, and scale production capacities. Simultaneously, digital integration through IoT connectivity and advanced analytics platforms is enabling real-time monitoring of processing parameters and predictive maintenance schedules, mitigating downtime and ensuring consistent quality outcomes.
In parallel, growing regulatory and societal pressures have propelled sustainability to the forefront, prompting machine designers to develop systems with lower energy consumption and optimized media utilization. Modern centrifugal machines incorporate energy-efficient motors, variable frequency drives, and closed-loop water recovery systems to minimize environmental footprint. Manufacturers have also begun adopting bio-based compounds and recyclable media, reflecting an industry-wide commitment to circular economy principles.
These trends converge to reshape the centrifugal finishing and grinding ecosystem: process engineers now have access to data-driven insights for continuous improvement, while plant managers can balance throughput with resource conservation. Together, these shifts are elevating centrifugal technology from a niche solution toward a core element of intelligent, sustainable production systems. The following sections will explore the cumulative impact of trade policies, segmentation nuances, regional drivers, and competitive positioning under this dynamic backdrop.
Evaluating the implications of cumulative United States tariffs implemented by 2025 on the centrifugal grinding and finishing equipment industry
By 2025, a layered framework of United States tariffs has had a profound effect on the centrifugal grinding and finishing machinery supply chain. Early measures under Section 232 imposed levies on steel and aluminum inputs, directly raising the cost base for machine casings, impellers, and support structures. Subsequently, Section 301 tariffs targeted key components and subassemblies sourced from China, prompting machine builders to reexamine sourcing strategies and regionalize procurement to mitigate duty burdens.
As tariffs accumulated, OEMs and contract finishers found themselves navigating increased capital expenditure, fluctuating raw material costs, and extended lead times. Some manufacturers shifted production footprints to local or near-nearshore facilities in Mexico and South America to circumvent high import taxes. Others maintained global supply chains but restructured vendor agreements to share tariff liabilities, thereby preserving price competitiveness. Process innovators responded by redesigning machine components to reduce reliance on high-duty materials and by qualifying alternative alloys that align with trade-friendly tariff codes.
This recalibration extends beyond cost considerations: companies leveraging tariff-aware product architectures and flexible supply networks have demonstrated greater resilience in delivering on customer timelines. As trade policy continues to evolve, the centrifugal finishing market is likely to see continued emphasis on agile sourcing, collaborative supplier models, and modular machine designs that can adapt to changing duty landscapes without disrupting operational performance.
Key segmentation insights into how machine types, end use industries, applications, and materials are defining centrifugal finishing market pathways
Dissecting centrifugal finishing and grinding machines by type reveals distinct performance trade-offs across centrifugal barrel, disc, and drag configurations. Centrifugal barrel systems excel at heavy deburring tasks with robust media agitation, while disc units offer precision polishing under high G-force conditions. Drag finishing solutions deliver fine surface treatments by carefully controlling part orientation and media flow. Within both barrel and disc variants, batch operations provide process flexibility, whereas continuous modes yield high throughput for standardized parts, enabling end users to align equipment selection with production cadence and part complexity.
Segmenting end use industries highlights how aerospace manufacturers leverage centrifugal processes for intricate deburring on turbine blades, while automotive suppliers prioritize rapid grinding cycles for cast and forged components. Hardware producers depend on finishing machines for burr removal on fasteners, whereas jewelry artisans harness low-impact polishing variants to preserve delicate details. In the medical sector, stringent cleanliness and surface finish requirements have driven adoption of drag finishing cells equipped with specialized media to ensure biocompatibility and micro-finish consistency.
Application-based segmentation further delineates capability sets: deburring operations split into external burr removal on edges and internal cavity clean-out; grinding applications bifurcate into fine and rough processes to tackle dimensional refinement or aggressive material removal. Polishing stages unfold across pre-polishing passes to smooth minor imperfections and final polishing cycles to achieve mirror-like luster. Surface finishing strategies encompass chemical treatments that modify surface chemistry and mechanical processes that impart targeted texture and hardness characteristics.
Material segmentation underscores the adaptability of centrifugal machines to process ceramic parts without micro-cracking, metal components across diverse alloys, and sensitive plastic workpieces without overheating. This multifaceted segmentation framework empowers stakeholders to pinpoint optimal equipment footprints and process recipes, driving precise alignment of machine capabilities with part attributes and production objectives.
This comprehensive research report categorizes the Centrifugal Grinding & Finishing Machines market into clearly defined segments, providing a detailed analysis of emerging trends and precise revenue forecasts to support strategic decision-making.
- Type
- End Use Industry
- Application
- Material
Analyzing regional market performance and growth drivers across the Americas, EMEA, and Asia-Pacific influencing centrifugal finishing equipment deployment
Regional analysis of centrifugal finishing and grinding machines reveals differentiated growth drivers and adoption patterns across the Americas, EMEA, and Asia-Pacific zones. In the Americas, robust aerospace and automotive supply chains have fueled demand for high-capacity centrifugal barrel and disc systems. Investments in domestic manufacturing reshoring have accelerated equipment purchases that align with national production strategies, particularly for high-precision medical and defense components.
Over in Europe, Middle East and Africa, stringent environmental regulations and established industrial automation ecosystems have steered the market toward energy-efficient and digitally connected centrifugal solutions. European OEMs often integrate cleaning and drying modules alongside finishing cells to meet cross-border compliance standards, while Middle Eastern and African markets show early interest in smaller footprint systems that cater to burgeoning hardware and jewelry sectors.
Asia-Pacific continues to be the largest adopter by volume, driven by expansive electronics, automotive, and consumer goods industries. Rapid industrialization in Southeast Asia and India has spurred demand for entry-level centrifugal drag and disc machines, whereas established markets in Japan and South Korea prioritize advanced servo-driven models with closed-loop process control. Across all regions, end users are increasingly leveraging regional service hubs and localized partner networks to reduce downtime and streamline spare-parts logistics, reflecting a global move toward agile, decentralized support structures.
This comprehensive research report examines key regions that drive the evolution of the Centrifugal Grinding & Finishing Machines market, offering deep insights into regional trends, growth factors, and industry developments that are influencing market performance.
- Americas
- Europe, Middle East & Africa
- Asia-Pacific
Highlighting the strategic positioning and innovation focus of leading companies driving advancements in centrifugal grinding and finishing machinery solutions
Leading equipment manufacturers are differentiating through strategic investments in advanced process control, media innovation, and service ecosystem expansion. One global OEM has introduced modular machine platforms that allow end users to interchange finishing heads, sensor arrays, and media conveyors, thereby reducing capital outlay for multi-step processes. Another mid-tier provider has focused on proprietary media formulations and compound chemistries, forging partnerships with chemical specialists to deliver tailored surface treatments for highly regulated industries such as medical and aerospace.
Service-driven business models are gaining traction, with several key players rolling out performance-based contracts that bundle equipment, consumables, and maintenance into unified offerings. These contracts often include digital dashboards for process traceability and predictive alerts, ensuring machines maintain optimal cycle parameters and minimizing unplanned stoppages. Moreover, leading firms are establishing regional application laboratories to facilitate hands-on process development and operator training, thereby strengthening customer loyalty and accelerating technology adoption.
Meanwhile, emerging competitors are capitalizing on specialized niches, such as ultra-high G-force finishing for fine jewelry and low-temperature drag finishing for polymer and composite parts. These targeted solutions are capturing share in segments where legacy equipment cannot satisfy nuanced process requirements. By monitoring these diverse strategies-ranging from broad modularization to narrow application specialization-industry stakeholders can better anticipate competitive moves and identify areas for collaboration or differentiation.
This comprehensive research report delivers an in-depth overview of the principal market players in the Centrifugal Grinding & Finishing Machines market, evaluating their market share, strategic initiatives, and competitive positioning to illuminate the factors shaping the competitive landscape.
- Walther Trowal GmbH
- Rösler Oberflächentechnik GmbH
- Sinto Co., Ltd.
- OTEC Präzisionsfinish GmbH
- Progress-Werk Oberkirch AG
- EMZ Maschinenfabrik GmbH
- Friulmac S.p.A.
- EEMAG AG
- Hangzhou Hongda Machinery Manufacturing Co., Ltd.
- Zhejiang Ever-Glory Industrial Machinery Co., Ltd.
Presenting actionable recommendations for industry leaders to leverage emerging trends and address challenges in centrifugal grinding and finishing markets
To harness the full potential of centrifugal finishing technologies, industry leaders should prioritize integration of digital twins and real-time analytics within their process workflows. By simulating machine dynamics and predicting media wear behavior, decision-makers can optimize cycle parameters before committing to physical trials. Additionally, consolidating supplier relationships under long-term agreements that include tariff-protection clauses will help stabilize input costs and insulate operations from further trade policy fluctuations.
Operational teams should also embark on cross-functional training programs to elevate workforce proficiency in machine programming, compound management, and preventive maintenance. Such initiatives not only reduce downtime but also promote continuous improvement cultures, where operators contribute to iterative refinements in process recipes. On the sustainability front, companies can explore partnerships with media recycling specialists and renewable energy providers to minimize environmental impact while advancing corporate responsibility targets.
Finally, R&D investments aimed at modular machine architectures and quick-change tooling systems will future-proof equipment fleets against evolving part geometries and batch size demands. By balancing these tactical moves with strategic foresight-such as aligning capital allocation with emerging end use industries-executives can position their organizations for long-term growth and operational excellence in an increasingly competitive centrifugal finishing market.
Detailing the rigorous research methodology combining primary interviews, secondary data analysis, and expert validation to ensure comprehensive market insights
This research draws upon a rigorous mixed-methodology framework designed to deliver comprehensive and credible insights. Primary data collection involved in-depth interviews with senior process engineers, plant managers, and R&D executives across key end use sectors, providing qualitative perspectives on operational bottlenecks, adoption drivers, and emerging technology requirements. These interviews were complemented by structured surveys targeting equipment buyers and service providers, ensuring broad representation of market sentiment and purchasing criteria.
Secondary research encompassed an extensive review of industry publications, trade association reports, patent filings, and regulatory documents. This phase included analysis of global trade data, tariff schedules, and standards documentation to contextualize the impact of evolving policy landscapes. To validate findings, a panel of subject matter experts-including materials scientists, mechanical designers, and finishing chemists-participated in a two-stage validation process, first reviewing preliminary insights and later affirming the finalized segmentation framework and strategic recommendations.
Data triangulation was performed to reconcile any discrepancies between quantitative metrics and qualitative observations. Statistical validation techniques, such as cross-tabulation and correlation analysis, were applied to ensure the robustness of trend assessments. The result is a thoroughly vetted set of insights that reflect current realities and anticipate future trajectories, equipping stakeholders with the analytical foundation to make informed decisions in the centrifugal grinding and finishing domain.
Explore AI-driven insights for the Centrifugal Grinding & Finishing Machines market with ResearchAI on our online platform, providing deeper, data-backed market analysis.
Ask ResearchAI anything
World's First Innovative Al for Market Research
Summarizing the key strategic takeaways and long-term outlook for stakeholders in the centrifugal grinding and finishing equipment sector
In conclusion, centrifugal grinding and finishing machines have ascended from niche offerings to core assets within diverse manufacturing ecosystems. Their ability to deliver accelerated cycle times and consistent surface quality positions them as indispensable tools for aerospace, automotive, medical, jewelry, and hardware producers. However, staying ahead of competition requires more than simply deploying new equipment; it necessitates a holistic approach that incorporates digital transformation, sustainability commitments, and adaptive supply chain strategies.
The cumulative effect of United States tariffs, shifting segmentation demands, and regional dynamics underscores the importance of agility. Organizations that have prioritized modular machine designs, localized sourcing models, and data-driven process control are already reaping the benefits of resilience and cost efficiency. As market participants look ahead, aligning investment priorities with emerging application niches and environmental regulations will determine long-term success.
Ultimately, the centrifugal finishing landscape will continue to evolve in response to technological breakthroughs and policy shifts. Stakeholders who leverage the insights presented in this report-while proactively engaging with innovative machine builders and service ecosystems-will find themselves best positioned to capture new opportunities, mitigate risks, and drive superior operational performance in the years to come.
This section provides a structured overview of the report, outlining key chapters and topics covered for easy reference in our Centrifugal Grinding & Finishing Machines market comprehensive research report.
- Preface
- Research Methodology
- Executive Summary
- Market Overview
- Market Dynamics
- Market Insights
- Cumulative Impact of United States Tariffs 2025
- Centrifugal Grinding & Finishing Machines Market, by Type
- Centrifugal Grinding & Finishing Machines Market, by End Use Industry
- Centrifugal Grinding & Finishing Machines Market, by Application
- Centrifugal Grinding & Finishing Machines Market, by Material
- Americas Centrifugal Grinding & Finishing Machines Market
- Europe, Middle East & Africa Centrifugal Grinding & Finishing Machines Market
- Asia-Pacific Centrifugal Grinding & Finishing Machines Market
- Competitive Landscape
- ResearchAI
- ResearchStatistics
- ResearchContacts
- ResearchArticles
- Appendix
- List of Figures [Total: 26]
- List of Tables [Total: 912 ]
Contact Associate Director Ketan Rohom to access exclusive market insights and support strategic investment decisions in centrifugal grinding and finishing
To begin transforming data into strategic advantage, reach out to Associate Director Ketan Rohom to unlock the full breadth of unparalleled market intelligence. By engaging directly with Ketan, decision-makers can gain targeted guidance on integrating these insights into their investment planning. His consultative approach will help tailor nuances of the centrifugal grinding and finishing machinery landscape to your organization’s unique positioning. Take this next step to leverage expert support in navigating competitive dynamics, enhancing procurement strategies, and optimizing product innovation roadmaps. Secure your competitive edge today by contacting Ketan to discuss how this comprehensive research can power your strategic initiatives and drive measurable value across operations.
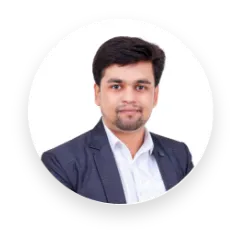
- When do I get the report?
- In what format does this report get delivered to me?
- How long has 360iResearch been around?
- What if I have a question about your reports?
- Can I share this report with my team?
- Can I use your research in my presentation?