Introduction: Unveiling the Ceramic Diaphragm Pipeline Grinding Machine Market
The ceramic diaphragm pipeline grinding machine has emerged as a pivotal enabler of precision and efficiency in high-value manufacturing. Leveraging advanced ceramic materials and state-of-the-art grinding technologies, these machines ensure consistently tight tolerances, superior surface finishes, and long operational lifespans. As industries such as aerospace, automotive, biomedical, and electronics demand ever-greater accuracy in component fabrication, the role of pipeline grinding systems equipped with ceramic diaphragms has grown exponentially.
With configurable architectures ranging from fully automated to semi-automated or standalone operations, manufacturers can tailor solutions to specific throughput, quality, and cost targets. Integration with programmable logic control and human-machine interfaces further enhances process stability, while modular designs allow for rapid deployment and future upgrades. As sustainability becomes a non-negotiable priority, ceramic diaphragm grinding machines also contribute by reducing material waste and energy consumption through optimized abrasive processes.
This introduction sets the stage for a comprehensive exploration of transformative market shifts, regulatory headwinds, segmentation insight, regional dynamics, and strategic imperatives. By unpacking these dimensions, decision-makers will gain a nuanced understanding of current challenges and opportunities, enabling informed strategies that drive competitive advantage in the evolving landscape of precision grinding.
Transformative Shifts Reshaping the Precision Grinding Landscape
The landscape for ceramic diaphragm pipeline grinding machines is undergoing a profound evolution driven by digital transformation, sustainability mandates, and geopolitical realignments. As Industry 4.0 initiatives proliferate, manufacturers are embedding sensors and IoT connectivity into grinding platforms, enabling real-time monitoring of spindle loads, grit wear, and coolant quality. Machine-learning algorithms analyze this data to predict maintenance needs, optimize cutting parameters, and minimize unplanned downtime.
Simultaneously, environmental regulations and carbon-neutral targets are prompting OEMs and end users to adopt low-waste, energy-efficient abrasive media and closed-loop coolant systems. This shift highlights the importance of ceramic diaphragms in retaining fine particulate matter and extending filter life. At the same time, supply chain disruptions-exacerbated by trade tensions and raw material shortages-have accelerated nearshoring efforts and supplier diversification strategies.
These transformative shifts are converging to reshape competitive positioning. Organizations that embrace automation, data-driven maintenance, and eco-friendly process innovations are gaining ground, while laggards risk margin erosion and compliance challenges. Against this backdrop, a deeper understanding of tariff impacts, segmentation nuances, and regional dynamics becomes essential for crafting resilient, future-proof growth strategies.
Cumulative Impact of United States Tariffs 2025 on Cost and Supply Chains
The cumulative impact of United States tariffs implemented in 2025 has reverberated across the ceramic diaphragm grinding ecosystem, raising input costs and compelling recalibration of global sourcing strategies. Ceramic powders, rare-earth additives, and specialized grinding media imported from key Asian markets now carry additional levies, inflating the landed cost of finished machines and spare parts.
Machine builders have responded by seeking alternative suppliers in low-tariff jurisdictions, renegotiating long-term contracts, and accelerating domestic production of critical ceramic components. While this localized approach mitigates duty exposure, it has introduced variability in raw material properties, requiring close collaboration between material scientists and equipment engineers to maintain performance consistency.
End users, particularly in aerospace and automotive segments, are adjusting procurement cycles and leveraging scale advantages to absorb incremental costs. Some have negotiated pass-through pricing with OEMs, while others have extended maintenance intervals via predictive analytics to reduce lifecycle expenses. Collectively, these measures are reshaping price structures, contract terms, and competitive dynamics, underscoring the imperative for stakeholders to monitor tariff developments and adapt supply chain architectures proactively.
Key Segmentation Insights Across Type, Industry, Application, and Maintenance
When examining machine type, fully automated solutions dominate high-volume production environments and subdivide into human-machine interface platforms that prioritize operator intuitiveness and programmable logic control systems that deliver repeatable precision. Integrated machines unite grinding, inspection, and loading functions into a single footprint, while semi-automated variants exist as either partially automatic cells or configurations that blend manual and mechanized operations; standalone equipment serves specialized, low-throughput applications.
On the end-use front, the aerospace sector harnesses these machines for complex commercial aviation components and mission-critical defense parts. In the automotive industry, both OEM assembly lines and aftermarket refurbishment facilities leverage grinding systems for shafts, valves, and high-precision drivetrain elements. Biomedical applications span sterile research laboratories and regulated medical device manufacturing, whereas electronics producers employ ceramic pipeline grinders for consumer gadgets and semiconductor wafer carriers.
Application-driven selection spans component shaping to fine surface finish optimization, including material removal processes that range from rough grinding to ultra-high-precision finishes. Prototyping and testing workflows utilize rapid prototyping techniques alongside failure analysis protocols to validate new ceramic geometries. Operating modes cover CNC-controlled machining, manual setups for custom jobs, and robotic-assisted cells equipped with either force/torque sensing or machine-vision inspection. The choice of grinding media extends from aluminum oxide and silicon carbide to cubic boron nitride and diamond solutions, the latter available as single-crystal or polycrystalline bonds. Finally, compatibility with ceramics like alumina or zirconia, composites from carbon fiber to glass fiber, ferrous and non-ferrous metals, and engineering plastics defines material versatility, while maintenance regimes range from AI-powered predictive analytics to professional servicing contracts and user self-maintenance kits.
This comprehensive research report categorizes the Ceramic Diaphragm Pipeline Grinding Machine market into clearly defined segments, providing a detailed analysis of emerging trends and precise revenue forecasts to support strategic decision-making.
- Type
- End Use Industry
- Application
- Machine Operation
- Grinding Media
- Material Compatibility
- Maintenance And Serviceability
Key Regional Insights Driving Market Adoption and Innovation
Regional dynamics in the Americas revolve around a mature aerospace and automotive base, where stringent certification requirements and lean manufacturing principles drive adoption of advanced grinding systems. In North America, machine builders are investing in smart factories and additive integration to reduce cycle times, while Latin American markets exhibit growing interest in retrofit solutions and cost-effective automation.
Europe, Middle East & Africa showcases a diverse landscape: Western Europe leads with sustainability-focused innovations, such as closed-loop coolant recovery and low-emission grinding cells, supported by rigorous environmental standards. The Middle East is investing in oil and gas component refurbishment, leveraging machine resilience in corrosive environments. Africa’s nascent industrial hubs are prioritizing modular grinding platforms that balance performance with capital expenditures.
Asia-Pacific remains the fastest-growing region, propelled by electronics and semiconductor manufacturing in East Asia, automotive and biomedical expansions in South Asia, and infrastructure modernization across Southeast Asia. Local machine tool OEMs are forging partnerships with global technology providers to integrate vision-guided grinding and AI-driven process optimization, while end users seek turnkey solutions that minimize integration complexity and accelerate time to market.
This comprehensive research report examines key regions that drive the evolution of the Ceramic Diaphragm Pipeline Grinding Machine market, offering deep insights into regional trends, growth factors, and industry developments that are influencing market performance.
- Americas
- Asia-Pacific
- Europe, Middle East & Africa
Key Company Insights and Competitive Differentiators
Market leadership in ceramic diaphragm pipeline grinding is defined by a combination of technological excellence, global footprint, and service ecosystems. Alpine AHM has distinguished itself through rapid prototyping services and modular machine architectures, enabling swift customization. Bühler Group’s strength lies in its integrated material science expertise and scalable automation platforms, which serve diverse processing environments.
Ceramic Technics Ltd. focuses on bespoke ceramic engineering and tight development cycles, capturing niche biomedical and research segments. FLSmidth & Co. A/S leverages decades of powder handling experience to offer robust, dust-controlled grinding solutions for high-throughput operations. Glen Mills Inc. delivers compact, laboratory-scale grinders, appealing to R&D settings that demand versatile, user-friendly interfaces.
Hosokawa Micron Group integrates granular control of abrasive media distribution with turnkey maintenance services, while Keramos Mineral Co. capitalizes on proprietary grinding media formulations to enhance consistency and tool life. NETZSCH Grinding & Dispersing excels in high-precision bench-scale units, ideal for specialized component finishing. Schenck Process and VibraScreener, Inc. both augment core grinding platforms with advanced material handling and sieving solutions, ensuring seamless integration and minimal process variability.
This comprehensive research report delivers an in-depth overview of the principal market players in the Ceramic Diaphragm Pipeline Grinding Machine market, evaluating their market share, strategic initiatives, and competitive positioning to illuminate the factors shaping the competitive landscape.
- Alpine AHM
- Bühler Group
- Ceramic Technics Ltd.
- FLSmidth & Co. A/S
- Glen Mills Inc.
- Hosokawa Micron Group
- Keramos Mineral Co.
- NETZSCH Grinding & Dispersing
- Schenck Process
- VibraScreener, Inc.
Actionable Recommendations for Driving Growth and Resilience
To capture emerging opportunities and mitigate evolving risks, industry leaders should consider the following initiatives:
• Embed machine-vision systems and force/torque control modules into next-generation grinding platforms to elevate precision, throughput, and automated quality assurance.
• Develop a dual-sourcing strategy for ceramic powders and grinding media to minimize tariff exposure and ensure material consistency across geographies.
• Invest in AI-driven predictive maintenance offerings that bundle analytics subscriptions with on-site sensor retrofits, enhancing uptime guarantees and creating recurring revenue streams.
• Expand service portfolios to include pay-as-you-go maintenance plans, self-service toolkits, and annual contract options, catering to diverse customer risk profiles and budget constraints.
• Pursue strategic partnerships with regional integrators and research institutions to co-innovate specialized applications in aerospace, biomedical, and semiconductor segments.
• Prioritize low-waste, eco-friendly abrasive formulations and closed-loop coolant systems to align with global sustainability targets and regulatory requirements.
• Scale digital training platforms and augmented-reality support tools to accelerate customer onboarding and reduce reliance on field service technicians.
Explore AI-driven insights for the Ceramic Diaphragm Pipeline Grinding Machine market with ResearchAI on our online platform, providing deeper, data-backed market analysis.
Ask ResearchAI anything
World's First Innovative Al for Market Research
Conclusion: Navigating Complexity to Achieve Competitive Advantage
The ceramic diaphragm pipeline grinding machine market stands at an inflection point where technological innovation, regulatory headwinds, and shifting supply chains converge. Organizations that proactively integrate digital instrumentation, diversify material sourcing, and expand service models will secure a competitive edge. By seamlessly blending advanced ceramic science with data-driven maintenance and eco-efficient processes, machine builders can deliver unparalleled precision and sustainability.
Understanding granular segmentation-across machine types, end-use industries, and maintenance paradigms-enables tailored value propositions that resonate with distinct customer profiles. Regional nuances underscore the importance of localized partnerships and flexible integration frameworks. Furthermore, strategic alignment with key component suppliers and regulatory developments ensures cost predictability and process integrity.
Ultimately, success hinges on a holistic approach that balances product innovation with service excellence and regulatory foresight. Executives equipped with these insights will be well-positioned to navigate tariff fluctuations, capitalize on emerging applications, and spearhead industry transformation. The path forward demands collaboration, agility, and an unwavering commitment to precision.
This section provides a structured overview of the report, outlining key chapters and topics covered for easy reference in our Ceramic Diaphragm Pipeline Grinding Machine market comprehensive research report.
- Preface
- Research Methodology
- Executive Summary
- Market Overview
- Market Dynamics
- Market Insights
- Cumulative Impact of United States Tariffs 2025
- Ceramic Diaphragm Pipeline Grinding Machine Market, by Type
- Ceramic Diaphragm Pipeline Grinding Machine Market, by End Use Industry
- Ceramic Diaphragm Pipeline Grinding Machine Market, by Application
- Ceramic Diaphragm Pipeline Grinding Machine Market, by Machine Operation
- Ceramic Diaphragm Pipeline Grinding Machine Market, by Grinding Media
- Ceramic Diaphragm Pipeline Grinding Machine Market, by Material Compatibility
- Ceramic Diaphragm Pipeline Grinding Machine Market, by Maintenance And Serviceability
- Americas Ceramic Diaphragm Pipeline Grinding Machine Market
- Asia-Pacific Ceramic Diaphragm Pipeline Grinding Machine Market
- Europe, Middle East & Africa Ceramic Diaphragm Pipeline Grinding Machine Market
- Competitive Landscape
- ResearchAI
- ResearchStatistics
- ResearchContacts
- ResearchArticles
- Appendix
- List of Figures [Total: 30]
- List of Tables [Total: 991 ]
Call to Action: Connect with Ketan Rohom to Access the Full Market Research Report
To secure comprehensive insights and actionable strategies for the ceramic diaphragm pipeline grinding machine market, please contact Ketan Rohom, Associate Director, Sales & Marketing at 360iResearch. Engage directly to obtain the full market research report, which delivers in-depth analysis, proprietary data, and tailored recommendations designed to empower informed decision-making and drive sustainable growth.
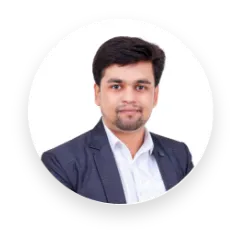
- When do I get the report?
- In what format does this report get delivered to me?
- How long has 360iResearch been around?
- What if I have a question about your reports?
- Can I share this report with my team?
- Can I use your research in my presentation?