The Chemical Surface Treatment Market size was estimated at USD 16.74 billion in 2024 and expected to reach USD 17.84 billion in 2025, at a CAGR 6.27% to reach USD 24.12 billion by 2030.

Unveiling the Dynamics of Chemical Surface Treatment
The chemical surface treatment sector has emerged as a critical enabler of performance, durability, and aesthetics across countless industrial applications. At its core, this dynamic field leverages targeted chemical processes to modify the surface properties of materials, enhancing factors such as corrosion resistance, adhesion, wear performance, and decorative appeal. As global manufacturing networks evolve under the pressure of sustainability goals and advanced material demands, surface treatment technologies have become a focal point for innovation and strategic investment.
Decision-makers today must navigate an intricate matrix of treatment types, substrate compatibilities, applications, equipment options, and regional regulatory environments. Anodizing variants address the needs of high-strength aluminum components, while conversion coatings and passivation processes safeguard metals across sectors. Electroplating and pickling continue to refine surface characteristics for electronics, automotive, aerospace, and healthcare end-users. Simultaneously, the industry confronts shifts in trade policy, supply chain localization, and the imperative to adopt greener chemistries.
This executive summary sets the stage for a comprehensive exploration of transformative market shifts, tariff impacts on US imports, segmentation insights, regional trends, competitive landscapes, and actionable recommendations. By weaving together these elements, industry leaders will obtain a clear line of sight into opportunities and risks shaping the path forward in chemical surface treatment.
Navigating Transformative Shifts Shaping the Industry
Over the past decade, the chemical surface treatment industry has been reshaped by a wave of technological breakthroughs and evolving customer expectations. Advanced process controls, driven by real-time monitoring and automation, have elevated operational precision and reduced waste, while the push toward eco-friendly chemistries has catalyzed the development of novel water-based and low-temperature formulations. These innovations are not mere incremental improvements; they represent a fundamental departure from legacy practices, empowering manufacturers to meet stringent environmental regulations without compromising performance.
Concurrently, digital transformation has accelerated the adoption of data-driven decision making. IoT-enabled equipment platforms now deliver continuous insights into bath chemistry, cycle consistency, and energy usage, allowing plant managers to optimize throughput and minimize downtime. This convergence of chemical expertise with Industry 4.0 architectures is shifting the competitive frontier toward integrated solutions that marry hardware, software, and consumables.
Supply chain transparency has also entered the spotlight. Stakeholders across the value chain are demanding visibility into raw material sourcing, product life cycles, and end-of-life disposal. As a result, traceability protocols and third-party certifications have become pivotal differentiators. Leaders in this space are those embracing these transformative shifts and positioning surface treatment not merely as a step in manufacturing, but as a strategic lever for sustainability and product differentiation.
Assessing the Cumulative Impact of US Tariffs in 2025
In 2025, newly enacted tariffs on chemical surface treatment inputs and equipment imports into the United States have introduced a fresh layer of complexity for domestic producers and end-users. Import duties of up to 15 percent on key precursor chemicals and critical processing machinery have elevated input costs, triggering reevaluation of existing procurement strategies and regional sourcing footprints.
Manufacturers relying on specialized additives or foreign-sourced plating equipment have experienced margin compression, compelling them to negotiate with domestic suppliers or invest in backward integration. Some industry players have shifted production to facilities outside tariff-affected categories, while others have leveraged long-term contracts and hedging mechanisms to stabilize raw material pricing. The cumulative effect has been a recalibration of cost structures, with ripple effects felt across downstream sectors such as automotive, aerospace, and electronics.
Despite these headwinds, the tariff landscape has also incentivized innovation. Companies are accelerating R&D into higher-efficiency process chemistries and localized equipment fabrication, reducing reliance on imported inputs. Collaborative ventures between chemical formulators and equipment manufacturers have emerged to co-develop turnkey solutions compliant with tariff constraints. As a result, the US market is witnessing a dynamic interplay between policy-induced cost pressure and the quest for competitive resilience.
Decoding Key Segmentation Insights Across Diverse Parameters
The market’s structure can only be fully understood by examining the diverse treatment modalities that cater to distinct performance requirements. Anodizing remains a foundational process for aluminum substrates, and within this domain, specialized hard anodizing, organic anodizing, and sulfuric anodizing methodologies each address unique hardness, adhesion, and corrosion resistance profiles. Conversion coating extends across chromate and phosphate variants, providing a thin, adherent film that primes metal surfaces for subsequent finishing operations. Degreasing, in its alkaline and solvent-based forms, prepares parts by removing contaminants through controlled chemical reactions, while electroplating spans chromium, copper, nickel, precious metal, and zinc plating to deliver aesthetic and functional surface layers. Passivation processes leverage inorganic and organic chemistries to remove free iron and stabilize stainless steel surfaces, and pickling etches metallic surfaces to eliminate scale and oxide layers.
Surface treatment intricacies deepen when substrate classifications are introduced. Ceramics, composites, and glass demand specialized pretreatments to ensure coating adhesion, while metals are further dissected into ferrous and non-ferrous categories. Non-ferrous alloys, including aluminum, copper, nickel, and zinc, each interact differently with treatment baths, requiring tailored process parameters. Plastics, with their low surface energy, often necessitate plasma activation or chemical etchants to promote bonding.
Industry verticals illustrate where these treatments find their highest value. Aerospace applications, whether commercial aircraft, defense and space, or general aviation, emphasize weight reduction and fatigue resistance, driving adoption of advanced anodizing and electroplating solutions. Automotive segments covering body and chassis, interior components, and powertrain systems rely on corrosion protection and decorative finishes. Electronics and semiconductors, from connector components to printed circuit boards and wafers, demand micron-level control and pristine surface cleanliness. Construction, energy and power, healthcare, and marine sectors each apply surface treatments to address durability, sterilization, and harsh environmental conditions.
Applications such as adhesion promotion, corrosion protection, decoration, surface activation, and wear resistance define performance outcomes across end-use markets. Flow modalities-batch or continuous-balance flexibility and throughput, with continuous lines favored for high-volume production. Equipment ecosystems, from conveyorized and spray systems to carousel and immersion tanks, as well as high-frequency and standard ultrasonic units, underpin the physical execution of chemical protocols. The interplay of these segmentation dimensions illuminates the market’s complexity and the pathways for targeted value creation.
This comprehensive research report categorizes the Chemical Surface Treatment market into clearly defined segments, providing a detailed analysis of emerging trends and precise revenue forecasts to support strategic decision-making.
- Treatment Type
- Substrate
- Industry Vertical
- Application
- Flow Type
- Equipment Type
Unearthing Regional Growth Patterns and Market Drivers
The Americas region continues to command a significant share of global surface treatment activity, driven by robust automotive, aerospace, and electronics manufacturing ecosystems. In the United States, policy initiatives promoting reshoring and infrastructure investment have translated into elevated demand for corrosion protection and wear-resistant coatings. Canada and Mexico complement this dynamic with specialized operations focused on energy equipment and heavy machinery, underpinned by favorable trade agreements that predate recent tariff measures.
Europe, Middle East and Africa encompass a mosaic of mature and emerging markets. Western Europe leads in green chemistry adoption, leveraging stringent environmental regulations to accelerate the uptake of water-based and low-VOC treatments. Eastern Europe and the Middle East exhibit growth in construction and energy sectors, fueling demand for protective coatings and chemical pretreatments. Africa’s expanding mining and infrastructure projects have spurred interest in heavy-duty pickling and passivation processes, even as supply chain logistics pose ongoing challenges.
Asia-Pacific remains the fastest-growing region, propelled by rapid industrialization in China, India, and Southeast Asia. The electronics and semiconductor verticals in Taiwan and South Korea are nexus points for advanced plating techniques. Automotive assembly in Japan and India relies heavily on anodizing and conversion coatings for chassis and body components. Moreover, the region’s aggressive investments in renewable energy infrastructure have expanded opportunities for corrosion protection systems on wind turbine and solar mounting structures. Across Asia-Pacific, a confluence of low labor costs, scaling capacity, and evolving environmental standards continues to reshape the competitive playing field.
This comprehensive research report examines key regions that drive the evolution of the Chemical Surface Treatment market, offering deep insights into regional trends, growth factors, and industry developments that are influencing market performance.
- Americas
- Europe, Middle East & Africa
- Asia-Pacific
Analyzing Leading Players and Strategic Imperatives
A handful of global enterprises and specialized niche players collectively shape the competitive landscape of chemical surface treatment. Established conglomerates leverage extensive R&D budgets, integrated supply chains, and global service networks to deliver end-to-end solutions. These organizations invest heavily in sustainable chemistries and digital analytics platforms, seeking to differentiate through value-added services and performance guarantees.
In parallel, agile mid-tier suppliers often excel in rapid formulation customization and region-specific compliance. Their lean structures enable swift market entry and close collaboration with local OEMs. Meanwhile, equipment manufacturers are forging strategic alliances with chemical formulators to provide turnkey process cells that integrate bath chemistry, filtration systems, and process controls in a single package.
Joint ventures and licensing agreements have become prevalent pathways for technology transfer, especially in markets with stringent localization requirements. Companies with proprietary proprietary coatings or automation software are selectively partnering with regional players to navigate regulatory landscapes and tap into established distribution channels. This mosaic of alliances underscores the importance of ecosystem partnerships in capturing cross-border growth opportunities and delivering comprehensive treatment solutions that meet the exacting demands of end-use industries.
This comprehensive research report delivers an in-depth overview of the principal market players in the Chemical Surface Treatment market, evaluating their market share, strategic initiatives, and competitive positioning to illuminate the factors shaping the competitive landscape.
- Henkel AG & Co. KGaA
- Element Solutions Inc.
- Ecolab Inc.
- BASF SE
- MKS Instruments, Inc.
- Solvay SA
- DuPont de Nemours, Inc.
- Akzo Nobel N.V.
- Ashland Global Holdings Inc.
- RPM International Inc.
Actionable Strategies to Drive Competitive Advantage
The following recommendations are designed to help industry leaders fortify their market position and unlock new growth levers. First, investing in modular, digitized equipment platforms will enable real-time process optimization and predictive maintenance, reducing operational variability and extending service lifecycles. Embedding analytics at every stage of the production chain can drive continuous improvement and foster a culture of data-driven decision making.
Second, diversifying supply chains by qualifying multiple raw material sources and exploring localized production of key additives will mitigate tariff‐related risks and raw material volatility. Establishing strategic partnerships or joint ventures with domestic chemical producers can secure preferential access to critical inputs and enhance logistical resilience.
Third, accelerating the transition to sustainable chemistries by prioritizing low‐emission, water‐based formulations will not only meet regulatory mandates but also create competitive differentiation. Collaborating with regulatory bodies and certification agencies early in the development cycle can streamline approvals and position organizations as environmental stewards.
Lastly, deepening engagement with end‐use customers through collaborative pilot programs and co‐development initiatives will strengthen customer loyalty and generate insights for next‐generation process designs. By aligning technology roadmaps with evolving end‐market requirements, companies can deliver bespoke solutions that command premium pricing and reinforce their leadership in a rapidly evolving industry.
Rigorous Research Methodology Underpinning the Analysis
This analysis rests on a hybrid research model synthesizing both primary and secondary data sources. Industry experts, including process engineers, quality managers, and R&D directors, were engaged through structured interviews and surveys to capture firsthand perspectives on emerging trends, technology adoption, and operational challenges. Secondary sources ranged from technical journals and patent filings to government reports and trade association publications, providing a robust contextual backdrop for primary findings.
Quantitative data on import/export flows, tariff schedules, and regional production capacities were validated against customs records and industry databases to ensure accuracy. A detailed segmentation framework was developed by cross-referencing product portfolios of leading suppliers with end-use vertical demands. Regional market dynamics were analyzed through a combination of macroeconomic indicators, capital expenditure trends, and regulatory landscapes.
To gauge competitive positioning, public disclosures, investor presentations, and patent portfolios were scrutinized, revealing strategic priorities and innovation pipelines. Data triangulation techniques were employed throughout the research lifecycle to reconcile discrepancies between sources and bolster the reliability of conclusions. This rigorous methodological approach ensures that the insights presented herein are both credible and actionable for strategic decision making.
Explore AI-driven insights for the Chemical Surface Treatment market with ResearchAI on our online platform, providing deeper, data-backed market analysis.
Ask ResearchAI anything
World's First Innovative Al for Market Research
Concluding Perspectives on Market Trajectory
The chemical surface treatment market stands at the intersection of technological innovation, regulatory evolution, and shifting global trade conditions. Throughout this summary, we have traced the contours of transformative shifts, from the integration of digital monitoring systems to the acceleration of green chemistries. We have examined the tariff landscape reshaping US operations and unpacked the multifaceted segmentation that defines process selection and end-use applications. Regional insights have highlighted the varied growth trajectories across the Americas, EMEA, and Asia-Pacific, while competitive analysis has illuminated the strategic maneuvers of key players.
As the industry moves forward, success will hinge on the ability to harmonize operational excellence with sustainability imperatives and supply chain resilience. Organizations that embrace modular, data-driven process platforms, diversify sourcing strategies, and deepen customer partnerships will be best positioned to capture incremental value. By synthesizing these strategic priorities with a clear understanding of regional dynamics and emerging tariff influences, decision makers can navigate complexity with confidence.
This concluding perspective underscores the market’s vibrancy and the imperative for continuous innovation. The pathway to competitive advantage lies in the proactive alignment of technology investments and strategic collaborations with evolving regulatory and customer requirements.
This section provides a structured overview of the report, outlining key chapters and topics covered for easy reference in our Chemical Surface Treatment market comprehensive research report.
- Preface
- Research Methodology
- Executive Summary
- Market Overview
- Market Dynamics
- Market Insights
- Cumulative Impact of United States Tariffs 2025
- Chemical Surface Treatment Market, by Treatment Type
- Chemical Surface Treatment Market, by Substrate
- Chemical Surface Treatment Market, by Industry Vertical
- Chemical Surface Treatment Market, by Application
- Chemical Surface Treatment Market, by Flow Type
- Chemical Surface Treatment Market, by Equipment Type
- Americas Chemical Surface Treatment Market
- Europe, Middle East & Africa Chemical Surface Treatment Market
- Asia-Pacific Chemical Surface Treatment Market
- Competitive Landscape
- ResearchAI
- ResearchStatistics
- ResearchContacts
- ResearchArticles
- Appendix
- List of Figures [Total: 28]
- List of Tables [Total: 917 ]
Next Steps with Ketan Rohom for Market Intelligence Investment
Are you ready to harness detailed market intelligence and gain a strategic edge in the chemical surface treatment sector Engage today with Ketan Rohom (Associate Director, Sales & Marketing at 360iResearch) who will guide you through tailored solutions aligned with your growth objectives Connect for personalized consultation to secure your copy of the comprehensive market research report and propel your organization toward informed success
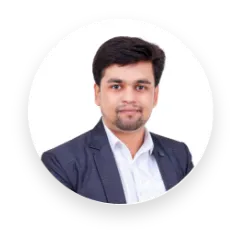
- How big is the Chemical Surface Treatment Market?
- What is the Chemical Surface Treatment Market growth?
- When do I get the report?
- In what format does this report get delivered to me?
- How long has 360iResearch been around?
- What if I have a question about your reports?
- Can I share this report with my team?
- Can I use your research in my presentation?