Introduction to the Circumferential Welding Machine Market
The circumferential welding machine has become a cornerstone of precision engineering across industries that demand reliable, high-quality seams around tubular components. As manufacturers strive to optimize productivity and ensure consistent weld integrity, these specialized welding systems deliver programmable accuracy, repeatability and minimal rework. This executive summary provides a clear overview of the defining market drivers shaping this segment, along with in-depth analysis of trade policies, regional dynamics, segmentation breakdowns and competitive benchmarks. By examining the transformative shifts in technology adoption, the evolving regulatory landscape and the strategies of leading equipment providers, decision-makers will gain actionable insights to guide investment, innovation and risk mitigation strategies. Throughout the following sections, a structured narrative will illuminate key trends, strategic imperatives and recommendations to navigate an increasingly complex operating environment, positioning stakeholders to harness growth opportunities and strengthen their market foothold.
Transformative Shifts Reshaping Welding Technology
Manufacturers are witnessing a rapid convergence of digital, materials and automation trends that are fundamentally reshaping circumferential welding technology. Industrial Internet of Things connectivity now enables real-time monitoring of weld parameters, empowering predictive maintenance strategies and reducing unplanned downtime. Meanwhile, advances in artificial intelligence are enhancing adaptive control systems, allowing machines to automatically optimize heat input and travel speed in response to minor variations in tube diameter or material composition.
At the same time, hybrid welding techniques-combining laser and arc energy sources-are gaining traction for their ability to deliver deeper penetration at higher travel rates. This shift has been accelerated by demand for lightweight alloys in aerospace and electric vehicles, where stringent strength-to-weight ratios are critical. Sustainability has also emerged as a key priority, prompting equipment manufacturers to integrate energy-recovery modules and to develop systems capable of handling recycled feedstock with minimal performance loss.
These transformative forces are converging to create a new wave of precision welding platforms that emphasize flexibility, efficiency and digital integration. As a result, businesses that embrace these technological advances will secure a competitive edge in meeting customer requirements across high-value end-use segments.
Assessing the Cumulative Impact of United States Tariffs in 2025
The imposition of additional United States tariffs in 2025 on imported steel and aluminum components has triggered a series of adjustments across welding equipment supply chains. End-users have faced increased raw material costs, squeezing profit margins and compelling manufacturers to reassess sourcing strategies. In response, many welding machine producers have diversified their supplier base, forging partnerships with mills in tariff-exempt regions or nearshoring component production to mitigate duty exposure.
Compliance requirements have also become more stringent, with customs authorities requiring detailed documentation to validate origin claims. This has driven investments in traceability systems that integrate with welding machines’ data logs, ensuring seamless audits and minimizing clearance delays. At the same time, organizations are renegotiating contracts to include tariff-adjustment clauses, sharing risk across the value chain.
Despite the short-term cost pressures, these policy shifts have accelerated supply chain resilience initiatives. Companies now prioritize dual-sourcing strategies, enhanced inventory management and closer collaboration between procurement, engineering and compliance teams. Over the long run, these practices will yield more agile operations and foster a deeper integration of tariff-risk assessments into capital expenditure decisions for welding equipment.
Key Segmentation Insights for Circumferential Welding Machines
A clear view of market segmentation is essential for targeting strategic investments and tailoring product portfolios. When evaluated by technology, arc welding remains foundational, with traditional MIG processes dominating high-volume tube fabrication, submerged arc systems excelling in heavy-wall applications, and TIG processes prized for precision in thin-wall tubes. Hybrid welding solutions that fuse laser-arc or laser-MIG technologies are rapidly gaining interest in sectors that demand deep penetration combined with minimal heat-affected zones. Laser-based systems-including CO2, diode, fiber and solid-state configurations-offer ultra-high speed for thin metals, while plasma welding techniques such as keyhole and micro-plasma provide a balance of penetration control and localized heat input. Resistance welding, encompassing seam and spot variants, continues to play a key role in high-speed assembly lines where cycle time is critical.
End-use industry segmentation highlights distinct application drivers. Aerospace players leverage these machines for both commercial and military aircraft, as well as spacecraft pressure vessels, where weld integrity is non-negotiable. Automotive manufacturers apply circumferential welding across commercial vehicle chassis components and passenger vehicle exhaust systems. Construction demand arises in building and infrastructure projects, with safety and compliance standards driving adoption. Oil & gas operators rely on these machines for upstream well casings, midstream pipeline sections and downstream processing equipment. In shipbuilding, both commercial shipyards and naval vessel fabricators require robust, repeatable circumferential welds on hull pipes and tanks.
From an application standpoint, metal furniture producers-serving both office and commercial sectors-use these machines to ensure aesthetic consistency on tubular frames. Pipe and tube welding spans aluminum and steel variants, while pressure vessel manufacturers leverage automated circumferential systems to meet stringent ASME codes. Storage tank producers, covering aboveground and underground installations, demand machines that deliver defect-free seams to prevent leakage and prolong service life.
Machine type further refines the landscape. Fully automatic systems built on computer numeric control or programmable logic control architectures dominate in high-volume operations, whereas semi-automatic and advanced manual configurations retain a foothold in job-shop environments that require operator flexibility. Manual machines range from basic units to advanced models with integrated digital controls.
Material selection drives equipment customization. Nickel and titanium alloys present unique challenges in heat management and require special torch designs, while aluminum, carbon steel and stainless steel remain staples, each necessitating optimized parameter sets and gas mixtures. Understanding these layers of segmentation equips decision-makers to align technology road maps with evolving product requirements and end-user demands.
This comprehensive research report categorizes the Circumferential Welding Machine market into clearly defined segments, providing a detailed analysis of emerging trends and precise revenue forecasts to support strategic decision-making.
- Technology
- End-Use Industry
- Application
- Type
- Material
Key Regional Insights Driving Market Expansion
Regional market dynamics reveal distinct growth patterns and operational priorities. In the Americas, an emphasis on infrastructure modernization and energy projects has fueled demand for robust circumferential welding solutions, prompting suppliers to enhance aftermarket service networks and engineer machines capable of withstanding variable field conditions. Regulatory focus on safety and emissions has also spurred the adoption of integrated monitoring systems to ensure compliance.
Within Europe, the Middle East & Africa, stringent quality standards in aerospace, automotive and energy sectors have driven demand for high-precision platforms with advanced defect-detection capabilities. Equipment manufacturers are collaborating with research bodies on digital twins and augmented reality tools to streamline setup and training, addressing the region’s skilled-labor constraints. Meanwhile, in Middle East subsea projects and African mining expansions, machines tailored for harsh environments gain traction.
Asia-Pacific stands out for its rapid industrialization and strong manufacturing base. Major economies in this region are investing heavily in smart factory initiatives, integrating circumferential welding machines into fully automated production lines. In response, providers are localizing production hubs and offering on-site training programs to accelerate adoption. Additionally, the region’s materials-handling expertise has led to innovations in robotic loading systems that seamlessly feed components into welding cells, boosting throughput and consistency.
This comprehensive research report examines key regions that drive the evolution of the Circumferential Welding Machine market, offering deep insights into regional trends, growth factors, and industry developments that are influencing market performance.
- Americas
- Asia-Pacific
- Europe, Middle East & Africa
Competitive Landscape: Leading Companies and Strategic Momentum
The competitive landscape is characterized by a mix of established conglomerates and specialized innovators. Amada Miyachi America, Inc. continues to lead with turnkey laser-based welding cells, while Daihen Corporation has enhanced its robot-integrated arc welding solutions for high-speed processing. ESAB Group, Inc. leverages its global footprint to deliver modular systems with universal power supplies, and Fronius International GmbH differentiates through high-efficiency welding converters and integrated energy-recovery units.
Illinois Tool Works Inc. and ITW Welding jointly advance multi-process platforms capable of switching between arc, plasma and resistance modes. Kawasaki Heavy Industries, Ltd. has intensified its focus on fiber-laser applications, partnering with local integrators to penetrate automotive supply chains. Koike Aronson, Inc. brings decades of torch design expertise to niche markets, while Kuka AG’s robotic cells deliver seamless circumferential welds in complex geometries.
Lincoln Electric Holdings, Inc. and Miller Electric Manufacturing LLC both emphasize digital control suites, offering cloud-enabled analytics to optimize welding parameters. Panasonic Corporation continues to refine its laser diode modules for enhanced beam quality, and Sonics & Materials, Inc. introduces ultrasonic enhancements for hybrid applications. TWI Ltd fosters collaborative research on next-generation welding processes, and Yaskawa Electric Corporation integrates multi-axis robots with advanced sensor arrays to push automation frontiers.
This comprehensive research report delivers an in-depth overview of the principal market players in the Circumferential Welding Machine market, evaluating their market share, strategic initiatives, and competitive positioning to illuminate the factors shaping the competitive landscape.
- Amada Miyachi America, Inc.
- Daihen Corporation
- ESAB Group, Inc.
- Fronius International GmbH
- Illinois Tool Works Inc.
- ITW Welding
- Kawasaki Heavy Industries, Ltd.
- Koike Aronson, Inc.
- Kuka AG
- Lincoln Electric Holdings, Inc.
- Miller Electric Manufacturing LLC
- Panasonic Corporation
- Sonics & Materials, Inc.
- TWI Ltd
- Yaskawa Electric Corporation
Actionable Recommendations for Industry Leaders
Industry leaders should prioritize several strategic initiatives to capitalize on emerging opportunities and hedge against evolving risks. First, invest in next-generation sensors and analytics platforms to enable real-time quality assurance and predictive maintenance, reducing downtime and improving yield. Second, develop modular hybrid welding lines that can seamlessly switch between arc, laser and plasma processes, catering to diverse material requirements and application needs.
Third, build supply chain resilience by identifying alternate suppliers in low-tariff regions and establishing nearshore production hubs; incorporate tariff-adjustment mechanisms in procurement contracts to shield margins. Fourth, partner with technology providers specializing in digital twin and augmented reality tools to accelerate machine commissioning, operator training and remote troubleshooting, addressing skilled-labor shortages.
Fifth, expand service networks and aftermarket offerings, including subscription-based maintenance programs and remote monitoring services, to create recurring revenue streams and deepen customer relationships. Sixth, collaborate with end-users in aerospace, automotive and energy sectors to co-develop bespoke solutions, ensuring compliance with sector-specific quality standards. Finally, embed sustainability metrics into product design by optimizing energy consumption, reducing consumable waste and evaluating lifecycle emissions to meet corporate and regulatory ESG targets.
Explore AI-driven insights for the Circumferential Welding Machine market with ResearchAI on our online platform, providing deeper, data-backed market analysis.
Ask ResearchAI anything
World's First Innovative Al for Market Research
Conclusion: Strategic Imperatives for Sustained Growth
The circumferential welding machine landscape is entering a new era defined by digital integration, materials innovation and strategic supply chain management. Organizations that embrace adaptive control systems, hybrid process capabilities and robust tariff-risk mitigation will secure competitive advantages. Regional initiatives-from smart factory investments in Asia-Pacific to quality-driven adoption in EMEA and infrastructure modernization in the Americas-underscore the importance of localized strategies supported by global expertise.
As the industry moves forward, collaboration between equipment providers, end-users and research institutions will accelerate the development of systems that deliver both productivity gains and sustainability benefits. By following the strategic recommendations outlined above, stakeholders can position themselves for sustained growth and resilience in a complex, rapidly evolving market.
This section provides a structured overview of the report, outlining key chapters and topics covered for easy reference in our Circumferential Welding Machine market comprehensive research report.
- Preface
- Research Methodology
- Executive Summary
- Market Overview
- Market Dynamics
- Market Insights
- Cumulative Impact of United States Tariffs 2025
- Circumferential Welding Machine Market, by Technology
- Circumferential Welding Machine Market, by End-Use Industry
- Circumferential Welding Machine Market, by Application
- Circumferential Welding Machine Market, by Type
- Circumferential Welding Machine Market, by Material
- Americas Circumferential Welding Machine Market
- Asia-Pacific Circumferential Welding Machine Market
- Europe, Middle East & Africa Circumferential Welding Machine Market
- Competitive Landscape
- ResearchAI
- ResearchStatistics
- ResearchContacts
- ResearchArticles
- Appendix
- List of Figures [Total: 26]
- List of Tables [Total: 994 ]
Next Steps: Connect with Ketan Rohom for In-Depth Insights
To explore the full suite of insights, data and strategic recommendations in this report, contact Ketan Rohom (Associate Director, Sales & Marketing at 360iResearch) today. Gain the competitive intelligence you need to optimize your technology investments and navigate trade-policy complexities with confidence.
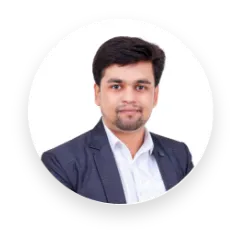
- When do I get the report?
- In what format does this report get delivered to me?
- How long has 360iResearch been around?
- What if I have a question about your reports?
- Can I share this report with my team?
- Can I use your research in my presentation?