Introduction to Closed Mold Carbon Fiber Composites
Closed mold carbon fiber composites have become synonymous with engineering excellence, delivering high strength-to-weight ratios, enhanced durability, and cost-effective production cycles. As industries worldwide seek solutions to reduce weight, improve performance, and lower environmental impact, closed mold processes such as Resin Transfer Molding (RTM) and Compression Molding stand out for their precision and repeatability. Innovations in fiber architecture and matrix formulation have unlocked applications ranging from aerospace airframes to automotive chassis components. This introduction lays the foundation for understanding how closed mold carbon fiber composites are redefining manufacturing paradigms through controlled process environments, superior surface finishes, and scalable production models that meet the stringent requirements of modern end users.
Transformative Shifts Reshaping the Closed Mold Carbon Fiber Composites Market
The landscape of closed mold carbon fiber composites is undergoing several transformative shifts. Advanced manufacturing technologies now combine automation with real-time process monitoring, enabling defect-free components at unprecedented cycle times. Material innovation has accelerated, with hybrid composites marrying carbon fiber with glass or aramid reinforcements to balance cost and performance, while nano enhanced resins improve interlaminar toughness and thermal stability. End users in aerospace demand ever-higher fatigue life and damage tolerance, prompting suppliers to refine prepreg formulations and optimize cure profiles. In automotive, the transition to electric vehicles drives demand for lightweight structural parts, pushing resin transfer molding to the forefront as a cost-competitive alternative to traditional autoclave processing. These converging dynamics are reshaping value chains and redefining how closed mold carbon fiber composites deliver strategic advantages.
Assessing the Cumulative Impact of U.S. Tariffs 2025 on Carbon Fiber Composites
The introduction of new U.S. tariffs in 2025 has exerted significant pressure across global supply chains for carbon fiber composites. Import duties on raw fibers and specialty resins have elevated material costs, prompting manufacturers to re-evaluate sourcing strategies and negotiate long-term agreements with domestic suppliers. This regulatory environment has also catalyzed investment in regional production capabilities to minimize cross-border exposures. As a result, some companies are accelerating the adoption of compression molding, which relies on less expensive intermediate materials, while others are exploring second-tier markets in Latin America and Southeast Asia. At the same time, original equipment manufacturers are revisiting design specifications to offset higher input costs through part consolidation and topology optimization. The cumulative impact of these tariffs underscores the need for agile procurement and strategic partnerships that can withstand shifting trade policies.
Key Segmentation Insights for Closed Mold Carbon Fiber Composites
A granular look at segmentation reveals critical insights into customer preferences and technological requirements. Product composition splits the market among composite laminates offering tailored ply orientations, prepreg composites providing controlled resin-to-fiber ratios, and sandwich structures delivering exceptional stiffness through lightweight cores. In the realm of manufacturing technology, practitioners leverage compression molding for high-volume automotive trim and structural inserts, while resin transfer molding dominates aerospace components where void-free laminates and tight tolerances are essential. Application sectors further diversify demand, with aerospace prioritizing weight reduction and fatigue resistance, automotive focusing on crash energy management and aesthetics, industrial equipment valuing corrosion resistance and load-bearing capacity, and sport and leisure emphasizing ergonomic performance and surface finish. When viewed by end use, commercial solutions such as wind turbine blades rely on reproducible closed mold processes, industrial applications like pressure vessels demand chemical compatibility, and special purpose products including robotic arms require high dimensional accuracy. Lastly, material innovation drives differentiation through hybrid composites that blend multiple fiber types for cost and performance balance, and nano enhanced composites that leverage nanoparticles to boost mechanical properties and thermal conductivity. Together, these segmentation dimensions chart the pathways by which suppliers and end users align capability with requirement.
This comprehensive research report categorizes the Closed Mold Carbon Fiber Composites market into clearly defined segments, providing a detailed analysis of emerging trends and precise revenue forecasts to support strategic decision-making.
- Product Composition
- Manufacturing Technology
- Application Sector
- End Use Industry
- Material Innovation
Key Regional Insights Across Global Markets
Regional dynamics exert notable influence on production strategies and end-user adoption. In the Americas, strong industrial equipment and automotive sectors support a diversified mix of compression molded and resin transfer molded components, while ongoing investments in green energy bolster demand for blade structures and bonded joints. Europe, Middle East & Africa present a dual landscape: European aerospace and automotive OEMs push for sustainable manufacturing and circular materials, the Middle East pursues large infrastructure projects with stringent performance criteria, and Africa explores niche sport and leisure applications as disposable incomes rise. The Asia-Pacific region drives volume through high-rate automotive assembly lines and expanding consumer electronics, supported by abundant fiber production in Japan and growing resin capacity in China. These distinct regional profiles underscore the need for tailored business models that respond to local regulatory frameworks, skill availability, and customer preferences.
This comprehensive research report examines key regions that drive the evolution of the Closed Mold Carbon Fiber Composites market, offering deep insights into regional trends, growth factors, and industry developments that are influencing market performance.
- Americas
- Asia-Pacific
- Europe, Middle East & Africa
Key Insights on Leading Companies in the Closed Mold Carbon Fiber Composites Market
A competitive scan reveals a diverse ecosystem of established leaders, specialized fabricators, and emerging innovators. Major chemical conglomerates such as Arkema S.A., Covestro AG, and Solvay S.A. continue to advance matrix chemistries, enabling higher cure temperatures and faster cycle times. Fiber specialists like Toray Industries, Inc., SGL Carbon SE, and Mitsubishi Chemical Corporation push the envelope on filament strength and modulus, supporting the most demanding aerospace and automotive applications. System integrators including Hexcel Corporation, Gurit Holding AG, and Owens Corning Incorporated bundle fibers, resins, and engineering services to deliver turnkey composite structures. Niche providers such as Advanced Composite Structures, Inc., CNC Molding Inc., and Composite Forming Technologies LLC excel in custom tooling and prototyping, while scalable contract manufacturers-Bravo Composites Corporation, Carbon Fiber Solutions Inc., and Delta Composites LLC-address high-volume requirements. Technology-centric firms like EPOLAM Composites LLC and Fusion Composite Technologies Inc. focus on nano enhanced resins and in situ monitoring, whereas Universal Composites Inc. and NextGen Composites Ltd. explore hybrid architectures for mid-market sectors. This mosaic of capability demonstrates how collaboration across the value chain drives differentiation, cost efficiency, and end-user satisfaction.
This comprehensive research report delivers an in-depth overview of the principal market players in the Closed Mold Carbon Fiber Composites market, evaluating their market share, strategic initiatives, and competitive positioning to illuminate the factors shaping the competitive landscape.
- Advanced Composite Structures, Inc.
- Advanced Mold Solutions Inc.
- Alpha Molding Solutions Inc.
- AOC Resins Inc.
- Arkema S.A.
- Bravo Composites Corporation
- Carbon Fiber Solutions Inc.
- CNC Molding Inc.
- Composite Forming Technologies LLC
- Composite Innovations Ltd.
- Composites One, Inc.
- Continental Composites Inc.
- Covestro AG
- Delta Composites LLC
- Elite Composite Solutions Corp.
- EPOLAM Composites LLC
- Fibre Glast Developments Ltd.
- Fusion Composite Technologies Inc.
- Gurit Holding AG
- Hexcel Corporation
- Innovative Composite Materials LLC
- Mitsubishi Chemical Corporation
- NextGen Composites Ltd.
- Norbond Inc.
- Owens Corning Incorporated (Composite Division)
- Pinnacle Composites Corporation
- Precision Composite Technologies Inc.
- PRYME Composite Systems Inc.
- SGL Carbon SE
- Solvay S.A.
- Synergetic Composites LLC
- Teijin Limited
- Toray Industries, Inc.
- Ultra Composite Technologies Ltd.
- Universal Composites Inc.
- Zoltek Industries Inc.
Actionable Recommendations for Industry Leaders
To capitalize on emerging opportunities, industry leaders should adopt a multi-faceted strategy. First, diversify material sources by establishing partnerships with regional fiber and resin producers to mitigate tariff volatility. Second, invest in automation and digital twins to optimize closed mold cycle times, reduce scrap rates, and enable predictive maintenance. Third, prioritize material innovation pipelines that integrate nanotechnology and hybrid fibers, delivering performance gains with minimal cost impact. Fourth, engage end users through joint development programs that align component designs with specific operational requirements in aerospace, automotive, and industrial segments. Fifth, expand service portfolios to include on-site training, repair services, and lifecycle analysis, reinforcing customer loyalty and unlocking recurring revenue streams. Finally, maintain flexibility in manufacturing footprints, deploying modular compression molding lines in growth markets while retaining high-precision resin transfer molding cells in regions with aerospace clusters.
Explore AI-driven insights for the Closed Mold Carbon Fiber Composites market with ResearchAI on our online platform, providing deeper, data-backed market analysis.
Ask ResearchAI anything
World's First Innovative Al for Market Research
Conclusion
Closed mold carbon fiber composites stand at the intersection of material science and manufacturing engineering, offering a path to lighter, stronger, and more sustainable structures. By understanding the interplay between segmentation dynamics, regional demands, and competitive positioning, companies can navigate trade policy headwinds and technological disruptions with confidence. Success hinges on agile supply chain design, proactive material innovation, and collaborative development models that anticipate customer needs. As industry stakeholders refine their strategic priorities, closed mold processes will continue to unlock new performance frontiers and operational efficiencies across diverse end-use sectors.
This section provides a structured overview of the report, outlining key chapters and topics covered for easy reference in our Closed Mold Carbon Fiber Composites market comprehensive research report.
- Preface
- Research Methodology
- Executive Summary
- Market Overview
- Market Dynamics
- Market Insights
- Cumulative Impact of United States Tariffs 2025
- Closed Mold Carbon Fiber Composites Market, by Product Composition
- Closed Mold Carbon Fiber Composites Market, by Manufacturing Technology
- Closed Mold Carbon Fiber Composites Market, by Application Sector
- Closed Mold Carbon Fiber Composites Market, by End Use Industry
- Closed Mold Carbon Fiber Composites Market, by Material Innovation
- Americas Closed Mold Carbon Fiber Composites Market
- Asia-Pacific Closed Mold Carbon Fiber Composites Market
- Europe, Middle East & Africa Closed Mold Carbon Fiber Composites Market
- Competitive Landscape
- ResearchAI
- ResearchStatistics
- ResearchContacts
- ResearchArticles
- Appendix
- List of Figures [Total: 26]
- List of Tables [Total: 235 ]
Contact Ketan Rohom to Unlock Strategic Advantages
To explore detailed analysis, customized insights, and comprehensive data on closed mold carbon fiber composites, reach out to Ketan Rohom, Associate Director, Sales & Marketing. He will guide you through the full report and help you secure the strategic intelligence your organization needs.
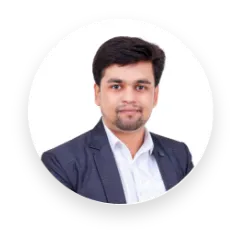
- When do I get the report?
- In what format does this report get delivered to me?
- How long has 360iResearch been around?
- What if I have a question about your reports?
- Can I share this report with my team?
- Can I use your research in my presentation?