The Closed Molding Composites Market size was estimated at USD 66.17 billion in 2024 and expected to reach USD 70.07 billion in 2025, at a CAGR 5.80% to reach USD 92.81 billion by 2030.

Shaping the Future of Manufacturing with Closed Molding Composites
Closed molding composites represent a transformative approach to fabricating high-performance, lightweight components that meet the rigorous demands of today’s leading industries. By encapsulating reinforcement fibers within a controlled resin environment, manufacturers achieve exceptional mechanical properties while minimizing scrap and environmental footprint. This executive summary distills critical perspectives on technological advances, policy shifts, and market dynamics to inform strategic planning and investment decisions.
The narrative opens with an overview of key closed molding techniques such as sheet molding compound, resin transfer molding, light resin transfer molding, and vacuum infusion. It underscores the growing imperative for sustainable production, total cost reduction, and supply chain resilience. From the adoption of next-generation fibers to the integration of digital manufacturing tools and high-performance resins, the introduction establishes the foundational drivers setting the stage for deeper analysis. Executives will gain a succinct yet comprehensive appreciation of the market’s current state, emerging opportunities, and the guideposts for optimizing operations and capital allocation as they navigate an increasingly competitive environment.
Emerging Forces Redefining the Closed Molding Composites Landscape
Several powerful trends are converging to redefine the closed molding composites landscape. First, the pursuit of lighter, stronger, and more durable materials has accelerated investment in carbon and aramid fibers, while interest in natural fiber alternatives grows in parallel with sustainability mandates. Advanced fiber architectures and hybrid composite solutions are unlocking new performance thresholds for applications ranging from aerospace structural panels to consumer goods enclosures.
Simultaneously, digitalization is infusing closed molding processes with real-time monitoring, automated resin flow simulation, and adaptive control systems. These innovations enhance yield, consistency, and cycle times, elevating competitiveness for both high-volume automotive producers and specialized end-use manufacturers. The advent of high-temperature resins and bio-based thermoplastics is expanding the application envelope, enabling composites to replace metals in demanding environments. As regulatory pressures intensify around carbon footprint and recyclability, closed molding technologies are poised to surpass traditional open molding in environmental credentials. Together, these shifts herald a new era of precision-driven, eco-focused composite manufacturing that demands agile strategies and robust partnerships.
Assessing the Ripple Effects of US Tariffs on Closed Molding Composites
The implementation of revised United States tariffs in 2025 has created a pronounced ripple effect across closed molding composite supply chains. Heightened duties on imported fibers and resin precursors have prompted manufacturers to reassess sourcing strategies, accelerating the search for domestic and nearshore suppliers. In response, several Tier-1 OEMs have initiated collaborative ventures to secure stable feedstock and negotiate volume-based pricing, thus mitigating margin erosion and preserving competitive pricing.
Moreover, compliance complexities have spurred investments in customs expertise and trade-compliance software to streamline import-export operations. While the tariffs have temporarily elevated input costs, they have also stimulated innovation by incentivizing local material development and reinforcing supplier diversity. Downstream, these dynamics have influenced procurement strategies for body panel producers, housing and enclosure fabricators, and structural component manufacturers. The net impact has been a market that, although facing near-term cost pressures, is becoming more resilient and vertically integrated. This evolution underscores the importance of proactive tariff scenario planning and cross-border collaboration to maintain supply continuity and cost efficiency.
Unveiling Critical Segmentation Trends Driving Closed Molding Applications
Understanding closed molding composites requires a nuanced look across fiber, resin, process, application, and industry dimensions. Fiber type preferences reflect a balance between strength, weight, and cost. Aramid fibers, typified by Kevlar and Nomex, deliver exceptional impact resistance for aerospace and defense uses, while carbon fiber variants, including pan-based and pitch-based grades, are driving lightweighting in high-performance automotive segments. Glass fiber choices such as E glass and S glass remain cost-effective for mass-market applications, and natural fibers like flax and hemp are gaining traction under sustainability mandates.
Resin architectures equally inform performance and processing. Thermoplastics such as nylon, PEEK, polyethylene, and polypropylene offer rapid cycle times and recyclability advantages, whereas thermosets including epoxy, polyester, and vinyl ester afford superior mechanical integrity and chemical resistance. Process selection-from bulk molding compound and compression molding to injection molding, light resin transfer molding, resin transfer molding, sheet molding compound, and vacuum infusion-depends on geometry complexity, production volume, and surface finish requirements.
Application sectors frame demand patterns, with body panels, decorative items, housings and enclosures, pipes and tanks, plus structural components each presenting distinct technical specifications. Finally, end-use industries such as aerospace and defense, automotive, construction, consumer goods, electrical and electronics, marine, and wind energy shape investment priorities and supply chain configurations. This segmentation analysis highlights where targeted innovation and capacity expansion can yield the greatest competitive advantage.
This comprehensive research report categorizes the Closed Molding Composites market into clearly defined segments, providing a detailed analysis of emerging trends and precise revenue forecasts to support strategic decision-making.
- Fiber Type
- Resin Type
- Process Type
- Application
- End Use Industry
Mapping Regional Dynamics in the Closed Molding Composites Sector
Regional dynamics shape the trajectory of closed molding composites with distinct factors driving growth in the Americas, Europe, Middle East & Africa, and Asia-Pacific. In the Americas, a mature automotive manufacturing base and robust aerospace programs anchor demand, while reshoring initiatives and infrastructure investments reinforce domestic supply chains. Manufacturers in North and South America are prioritizing local fiber production and resin compounding to minimize exposure to global tariff fluctuations and logistical bottlenecks.
In Europe, heightened sustainability regulations and ambitious renewable energy targets have propelled wind energy blade production and lightweight mass transit solutions. Defense modernization in the Middle East supports demand for high-performance composites, while infrastructure projects in Africa offer emerging opportunities for corrosion-resistant structural panels. Meanwhile, Asia-Pacific remains the fastest-growing market, driven by rapid expansion in automotive assembly, consumer electronics, and construction. Investment in advanced manufacturing clusters across China, Japan, South Korea, and India continues to accelerate process innovation and localized material sourcing. Together, these regional profiles underscore the need for flexible strategies that align production footprints and R&D efforts with localized demand and regulatory frameworks.
This comprehensive research report examines key regions that drive the evolution of the Closed Molding Composites market, offering deep insights into regional trends, growth factors, and industry developments that are influencing market performance.
- Americas
- Europe, Middle East & Africa
- Asia-Pacific
Competitive Movements and Strategic Positioning of Leading Composite Suppliers
Leading players are differentiating through strategic investments in R&D, capacity expansions, and partnerships. Global fiber producers are scaling next-generation aramid and carbon facilities to meet heightened performance requirements and are collaborating with resin suppliers to co-develop customized chemistries. Composite fabricators are integrating digital process controls and establishing pilot lines for emerging resin systems to accelerate time-to-market for complex parts.
Several established conglomerates have secured alliances with OEMs to create application-specific solutions for body panels and structural components, while niche innovators are gaining traction by offering bio-based fibers and recyclable thermoplastics. Mergers and acquisitions remain prevalent as companies seek to broaden their geographic reach and enhance vertical integration. Service providers specializing in simulation, tooling, and composite design are forging collaborative networks with material suppliers to deliver end-to-end support, facilitating faster adoption among key account customers. This competitive landscape reflects a dual focus on technological leadership and supply chain resilience, with each major player carving out unique value propositions to capture growth in targeted segments.
This comprehensive research report delivers an in-depth overview of the principal market players in the Closed Molding Composites market, evaluating their market share, strategic initiatives, and competitive positioning to illuminate the factors shaping the competitive landscape.
- Owens Corning
- Toray Industries, Inc.
- Teijin Limited
- Solvay SA
- SGL Carbon SE
- Hexcel Corporation
- Gurit Holding AG
- Mitsubishi Chemical Corporation
- Huntsman Corporation
- BASF SE
Strategic Imperatives for Leadership in the Closed Molding Composites Market
Industry leaders should prioritize the integration of advanced fiber and resin innovations into scalable production platforms. Establishing collaborative R&D consortia with academic and government laboratories can accelerate the commercialization of high-performance and sustainable materials. Concurrently, investing in digital process monitoring and predictive analytics will enhance quality consistency and reduce cycle times, delivering immediate cost benefits.
Supply chain diversification remains critical amid evolving trade policies. Executives should forge strategic partnerships with regional suppliers and explore nearshoring to mitigate tariff risk and logistics volatility. Implementing comprehensive life-cycle assessments and sustainability certifications will differentiate offerings in tender evaluations and support compliance with tightening environmental regulations. Organizations must also cultivate talent with expertise in composite design, automation, and data science to drive continuous improvement. Finally, proactive engagement with regulatory bodies and standards organizations will shape favorable policy frameworks and unlock new market access. By aligning these imperatives into a cohesive strategy, industry leaders can secure competitive advantage and future-proof their operations.
Ensuring Robust Insights Through a Rigorous Market Research Approach
This analysis draws on a robust, multi-tiered research framework designed to ensure accuracy and objectivity. Primary research comprised in-depth interviews with executives across composite material suppliers, OEM engineering teams, process technology vendors, and industry consultants. Complementary surveys of manufacturing facilities provided quantitative validation of process adoption rates and material preferences.
Secondary sources included regulatory filings, trade association reports, patent databases, and peer-reviewed journals, ensuring comprehensive coverage of technological advancements and policy developments. Data triangulation techniques cross-verified findings, while regional expert panels reviewed interpretations to capture local market nuances. Segmentation frameworks were constructed to align with industry classification standards and refined through scenario analysis to test sensitivity to key variables. This rigorous methodology underpins each insight presented, delivering a defensible and actionable perspective on the closed molding composites landscape.
Explore AI-driven insights for the Closed Molding Composites market with ResearchAI on our online platform, providing deeper, data-backed market analysis.
Ask ResearchAI anything
World's First Innovative Al for Market Research
Synthesizing Core Takeaways on Closed Molding Composites Evolution
Closed molding composites are poised at the intersection of performance demand, sustainability imperatives, and supply chain evolution. Technological breakthroughs in fiber architecture, resin systems, and digital process controls are redefining application possibilities and enabling cost-competitive alternatives to traditional materials. At the same time, trade policy shifts and regional incentives are shaping manufacturing footprints and strategic collaborations.
Segmentation analysis reveals targeted opportunities in high-growth applications and end-use industries, while regional insights underscore the importance of localization and regulatory alignment. Competitive mapping highlights differentiated strategies and the value of integrated solutions spanning materials, process, and design. By synthesizing these findings into actionable recommendations, stakeholders can navigate uncertainties, foster innovation, and accelerate adoption. This executive summary offers a consolidated view of the market’s critical inflection points, equipping decision-makers with the perspective needed to chart a clear path forward.
This section provides a structured overview of the report, outlining key chapters and topics covered for easy reference in our Closed Molding Composites market comprehensive research report.
- Preface
- Research Methodology
- Executive Summary
- Market Overview
- Market Dynamics
- Market Insights
- Cumulative Impact of United States Tariffs 2025
- Closed Molding Composites Market, by Fiber Type
- Closed Molding Composites Market, by Resin Type
- Closed Molding Composites Market, by Process Type
- Closed Molding Composites Market, by Application
- Closed Molding Composites Market, by End Use Industry
- Americas Closed Molding Composites Market
- Europe, Middle East & Africa Closed Molding Composites Market
- Asia-Pacific Closed Molding Composites Market
- Competitive Landscape
- ResearchAI
- ResearchStatistics
- ResearchContacts
- ResearchArticles
- Appendix
- List of Figures [Total: 26]
- List of Tables [Total: 513 ]
Secure Comprehensive Closed Molding Composites Insights from Ketan Rohom
Elevate your strategic roadmap with an authoritative deep dive into closed molding composites by reaching out to Ketan Rohom, Associate Director, Sales & Marketing at 360iResearch. His expert guidance will connect you with the full market research report, offering unparalleled visibility into fiber innovations, resin breakthroughs, processing efficiencies, tariff implications, regional nuances, and competitive dynamics.
Secure tailored insights today and accelerate your decision-making with data-driven perspectives designed to strengthen your positioning in this rapidly evolving sector. Engage directly to customize your report package, explore exclusive add-ons, and ensure your organization capitalizes on every opportunity within the closed molding composites landscape.
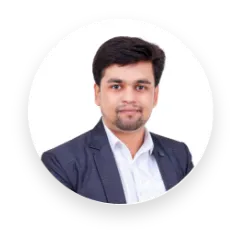
- How big is the Closed Molding Composites Market?
- What is the Closed Molding Composites Market growth?
- When do I get the report?
- In what format does this report get delivered to me?
- How long has 360iResearch been around?
- What if I have a question about your reports?
- Can I share this report with my team?
- Can I use your research in my presentation?