Introduction to the Evolving CNC Machining CAM Software Landscape
Manufacturers are increasingly turning to computer-aided manufacturing solutions to optimize toolpaths, improve throughput, and maintain stringent quality standards. As global supply chains become more complex and product lifecycles shorten, the demand for high-precision machining workflows has never been greater. Advanced solutions now seamlessly integrate design, simulation, and testing functionalities within a unified environment, reducing the risk of errors, shortening programming cycles, and enabling rapid response to engineering changes. Moreover, cloud-enabled deployment models and subscription-based pricing have lowered barriers to entry, allowing small to medium enterprises to leverage capabilities once reserved for large original equipment manufacturers. With multi-axis machining and real-time process feedback, manufacturers can achieve tighter tolerances while enhancing overall equipment effectiveness.
At the heart of this transformation lies the integration of machine learning algorithms that predict tool wear and optimize cutting parameters autonomously. Organizations that invest in these digital workflows report measurable gains in cycle time and material utilization. As regulatory requirements tighten and sustainability goals become non-negotiable, advanced CAM platforms offer waste reduction features and energy consumption analytics. From prototype development to high-volume production, the ability to simulate complex operations, validate post-processing routines, and generate error-free G-code has become a competitive differentiator. Against this backdrop, leaders in aerospace, automotive, medical device manufacturing, and heavy machinery are forging strategic partnerships with software providers to co-develop tailored solutions. This introduction sets the stage for an in-depth analysis of transformative shifts, tariff impacts, segmentation insights, regional trends, and key players shaping the future of CNC machining CAM software.
Transformative Shifts Reshaping CNC Machining CAM Software
Building on this foundation, the CNC machining ecosystem has experienced several paradigm shifts. First, the rise of Industry 4.0 has propelled demand for end-to-end digital thread continuity, driving CAD/CAM integration and real-time shop floor analytics. Next, artificial intelligence and machine learning capabilities have become embedded within CAM platforms, enabling predictive maintenance, adaptive toolpath optimization, and enhanced collision avoidance. Furthermore, deployment flexibility has evolved, with cloud-based environments offering on-demand scalability and collaborative programming across distributed teams, while on-premises solutions continue to address security and data sovereignty concerns.
Another significant shift is the maturation of multi-axis machining. As part geometries grow increasingly complex, three-axis systems have given way to five-axis centers capable of producing intricate contours in a single setup. This evolution reduces cycle times and eliminates secondary operations, boosting throughput. Additionally, simulation and validation functionalities have reached new levels of fidelity, ensuring that virtual run-throughs accurately reflect real-world machine behavior. Moreover, open API architectures have emerged, giving manufacturers the ability to tailor workflows, integrate enterprise resource planning systems, and automate cross-departmental processes.
Simultaneously, subscription-based and pay-per-use pricing models have disrupted traditional licensing paradigms, aligning costs with consumption and facilitating rapid scaling for small and medium enterprises. Taken together, these transformative shifts are redefining competitive dynamics, compelling industry leaders to re-evaluate technology roadmaps, invest in upskilling, and forge collaborative ecosystems to stay ahead of the curve.
Cumulative Impact of United States Tariffs in 2025 on CAM Software
Since the introduction of new tariff measures in 2025, CNC machining CAM software providers and end users have navigated increased import duties on foreign-manufactured hardware, tooling components, and software licenses. These levies have translated into upward price pressures, driving many organizations to re-assess supply chain strategies and explore cost containment measures. In response, some providers have localized data centers, shifted hosting to domestic cloud service partners, or restructured pricing tiers to accommodate fluctuating duties.
Operational teams have reported that increased duty costs on multi-axis machine components and ancillary devices have indirectly affected software procurement budgets, prompting manufacturers to prioritize solutions that deliver demonstrable efficiency gains. To mitigate margin erosion, firms are consolidating software vendors, negotiating integrated license agreements that span design, simulation, and testing modules. Additionally, rising cross-border compliance requirements have accelerated the adoption of on-premises deployments in highly regulated sectors such as defense and medical device manufacturing.
Furthermore, suppliers are enhancing integration capabilities to support ERP and MES platforms, enabling real-time visibility into duty calculations and production costs. This level of transparency allows decision makers to isolate tariff-driven expenditures and optimize production schedules accordingly. Some early adopters have piloted pay-per-use models, deferring capital outlays and aligning software expenses with actual machining throughput. Moreover, geographic diversification strategies are gaining traction, with manufacturers establishing secondary production hubs in tariff-exempt regions to hedge risk. Together, these adaptive measures illustrate how the sector is proactively responding to 2025 tariff regimes, balancing cost pressures with the imperative to innovate and maintain operational resilience.
Key Segmentation Insights Driving Market Differentiation
An in-depth segmentation analysis reveals how market dynamics vary across distinct dimensions. When examining software type, two-dimensional CAM solutions remain foundational for basic drilling and turning tasks, while three-dimensional platforms are increasingly favored for milling and grinding operations that demand precise contouring. The most advanced users, particularly in aerospace and medical device manufacturing, are migrating toward multi-axis solutions that enable five-axis programming, reducing setup times and providing superior geometric accuracy.
Deployment mode bears a significant influence on adoption strategies; organizations with stringent data governance requirements continue to rely on on-premises systems, whereas manufacturers pursuing rapid scalability leverage cloud-based offerings to facilitate distributed collaboration and real-time updates. End-user industries also exhibit divergent requirements. Aerospace and defense firms prioritize tight integration with PLM systems to manage complex design revisions, automotive manufacturers emphasize high-volume machining consistency, and electronics producers focus on micro-milling capabilities. In the medical segment, companies involved in implants gravitate toward simulation-intensive workflows, while those manufacturing surgical devices value robust post-processing to ensure patient safety.
Applications such as drilling, grinding, milling, and turning each drive specific feature preferences. For instance, CNC lathes and mills used in turning demand sophisticated toolpath generation algorithms, and drilling operations benefit from modules that dynamically adjust feed rates. Functionality-driven segmentation highlights that design, simulation, and testing features are no longer optional; instead, users expect a cohesive environment that supports the entire machining cycle. Additionally, pricing models include one-time licenses for permanent access, pay-per-use schemes for flexibility, and subscription-based plans tailored to predictable budgeting.
Some organizations still favor one-time license agreements to secure permanent access and avoid ongoing subscription costs. Enterprise size further shapes procurement decisions: OEMs and tier one suppliers within large enterprises negotiate enterprise-wide licenses, while small and medium enterprises often choose subscription-based or pay-per-use pricing. Axis count segmentation is closely linked to platform choice, with three-axis systems dominating routine milling tasks, four-axis platforms serving niche applications, and five-axis machines enabling complex form machining.
Operating system compatibility remains a consideration, with Windows platforms leading market share, Linux solutions appreciated for customization, and Mac OS favored by design-centric teams. Integration capability further differentiates offerings, as ERP, MES, and PLM integrations-backed by robust post-processing support-form the backbone of connected manufacturing architectures. ERP integration often leverages Oracle and SAP connectors to harmonize production planning, while MES interfaces streamline real-time shop floor control and PLM linkages manage design data revisions. Finally, software features such as CAD compatibility, toolpath generation, advanced post-processing, and workflow automation are critical levers for vendors to address evolving customer needs.
This comprehensive research report categorizes the CNC Machining CAM Software market into clearly defined segments, providing a detailed analysis of emerging trends and precise revenue forecasts to support strategic decision-making.
- Software Type
- Deployment Mode
- End-User Industry
- Application
- Functionality
- User Type
- Number of Axes
- Operating Platform
- Integration Capability
- Pricing Model
- Software Features
Regional Dynamics Shaping CNC Machining CAM Software Adoption
In the Americas, robust manufacturing infrastructures, particularly in North America, support widespread adoption of advanced CAM solutions. The presence of major aerospace OEMs and automotive plants coupled with a mature network of system integrators accelerates deployment of cloud-based and multi-axis platforms. Latin American hubs, meanwhile, are gradually embracing digital machining workflows as local governments incentivize modernization. Overall, the region’s focus on end-to-end digital thread implementation drives demand for solutions that seamlessly connect CAD, CAM, and shop floor data.
Moving to Europe, Middle East & Africa, the landscape is highly diverse. European Union countries champion stringent regulatory compliance and sustainability, driving investments in simulation-driven software and real-time energy consumption analytics. In the Middle East, national manufacturing initiatives are catalyzing technology transfers that prioritize indigenous workforce development. Across Africa, cost-sensitive small and medium enterprises often select pay-per-use or one-time license models to optimize capital budgets, while gradually ramping up adoption of advanced features.
In the Asia-Pacific region, rapid industrialization and government-led smart manufacturing programs fuel demand for integrated CAM suites. China and South Korea lead in high-volume production environments, prioritizing automation compatibility and ERP integration with Oracle and SAP ecosystems. Japan’s manufacturers focus on high-precision micro-machining, embracing five-axis and cloud-enabled deployments. Southeast Asian markets show strong interest in subscription-based models that reduce upfront investment, enabling smaller firms to access CAD/CAM capabilities. These regional dynamics underscore the need for vendors to offer flexible deployment, localized support, and compliance-driven features aligned with specific market maturities.
This comprehensive research report examines key regions that drive the evolution of the CNC Machining CAM Software market, offering deep insights into regional trends, growth factors, and industry developments that are influencing market performance.
- Americas
- Asia-Pacific
- Europe, Middle East & Africa
Competitive Landscape and Leading Player Insights
The competitive landscape is characterized by a mix of established incumbents and emerging innovators, each vying for market share through differentiated value propositions. Alphacam by Hexagon AB and Edgecam by Hexagon AB leverage a unified architectural framework that emphasizes integrated CAD compatibility and robust post-processing across diverse controller platforms. Autodesk, Inc. extends its software portfolio with Powermill and core CAM solutions, delivering end-to-end CAD/CAM workflows that tightly integrate with design suites.
BobCAD-CAM, Inc. distinguishes itself through modular offerings that cater to both entry-level two-dimensional applications and five-axis machining tasks, while CAMWorks by HCL Technologies Ltd. capitalizes on feature-based programming and seamless SOLIDWORKS integration to accelerate setup times. Dassault Systèmes SE brings a high level of product lifecycle management interoperability, enabling clients to manage design revisions and machining data within a single system. DP Technology Corp.’s Esprit focuses on high-performance milling and turning operations for complex aerospace and medical components, supported by an advanced simulation engine.
GibbsCAM, part of 3D Systems, Inc., and Mastercam from CNC Software Inc. maintain robust installed bases, offering extensive post-processing libraries and workflow automation tools. Hypertherm, Inc. complements its hardware leadership in cutting technology with CAM software that emphasizes precision and efficiency. Siemens Digital Industries Software enters the fray with its NX CAM suite, positioning itself as a platform for fully integrated digital manufacturing. SolidCAM Ltd. rounds out the competitive picture, delivering iMachining modules that optimize toolpath generation and reduce cycle times.
Together, these companies are driving innovation through partnerships, open API strategies, and tiered pricing models-ranging from one-time licenses to subscription-based and pay-per-use plans-that address the evolving needs of large enterprises, OEMs, tier one suppliers, and small to medium enterprises alike.
This comprehensive research report delivers an in-depth overview of the principal market players in the CNC Machining CAM Software market, evaluating their market share, strategic initiatives, and competitive positioning to illuminate the factors shaping the competitive landscape.
- Alphacam by Hexagon AB
- Autodesk, Inc.
- CAD/CAM Software by BobCAD-CAM, Inc.
- CAMWorks by HCL Technologies Ltd.
- Dassault Systèmes SE
- Edgecam by Hexagon AB
- Esprit by DP Technology Corp.
- GibbsCAM/3D Systems, Inc.
- Hypertherm, Inc.
- Mastercam/CNC Software Inc.
- Powermill by Autodesk, Inc.
- Siemens Digital Industries Software
- SolidCAM Ltd.
Actionable Recommendations for Industry Leaders
To capitalize on emerging opportunities in the CNC machining CAM software market, industry leaders should consider a multi-pronged strategic approach. First, investing in the development and integration of multi-axis programming capabilities will address growing demand for complex part geometries and reduce secondary operations. Simultaneously, prioritizing cloud-based architectures and flexible pricing-including subscription and pay-per-use models-can attract a broader base of small and medium enterprises while maintaining recurring revenue streams.
Second, deepening integration capabilities by offering out-of-the-box connectors for leading enterprise resource planning, manufacturing execution, and product lifecycle management systems-especially Oracle and SAP environments-will enhance value propositions and drive stickiness. Incorporating advanced simulation and virtual commissioning functionalities will help clients validate processes, minimize machine downtime, and meet increasingly stringent quality and regulatory requirements.
Third, vendors should develop modular add-ons for specialized industries, such as micro-machining modules for medical and electronics sectors or high-speed turning packages for heavy machinery applications. Offering comprehensive training and certification programs will bolster user proficiency, foster customer loyalty, and accelerate time to value. Furthermore, embracing open API ecosystems and cultivating partnerships with third-party hardware and software providers will create cohesive digital threads, enabling manufacturers to leverage data analytics and IoT-driven insights. Lastly, maintaining a customer-centric service model-with localized support, continuous software updates, and proactive maintenance services-will reinforce long-term relationships and position providers as strategic innovation partners.
Explore AI-driven insights for the CNC Machining CAM Software market with ResearchAI on our online platform, providing deeper, data-backed market analysis.
Ask ResearchAI anything
World's First Innovative Al for Market Research
Conclusion: Aligning Strategy with Emerging Market Realities
Bringing the analysis together, the CNC machining CAM software market is at an inflection point defined by digitalization, shifting cost structures, and evolving customer expectations. The combined effects of Industry 4.0, tariff dynamics, and regional policy initiatives are reshaping competitive imperatives. Segmentation insights demonstrate that one-size-fits-all approaches are no longer viable; instead, tailored solutions that align with deployment preferences, application requirements, and budgetary constraints will win.
Leading companies are responding by enhancing multi-axis capabilities, expanding integration frameworks, and diversifying pricing models to address the full spectrum of manufacturing complexities. As businesses navigate regulatory landscapes and strive for operational excellence, the strategic focus must remain on delivering measurable improvements in productivity, quality, and sustainability. Ultimately, success will hinge on the ability to foster collaborative ecosystems, anticipate emerging use cases, and deliver software platforms that evolve in tandem with manufacturing innovation. This conclusion underscores the urgency for decision-makers to recalibrate technology roadmaps, invest in digital capabilities, and forge partnerships that drive long-term competitiveness.
This section provides a structured overview of the report, outlining key chapters and topics covered for easy reference in our CNC Machining CAM Software market comprehensive research report.
- Preface
- Research Methodology
- Executive Summary
- Market Overview
- Market Dynamics
- Market Insights
- Cumulative Impact of United States Tariffs 2025
- CNC Machining CAM Software Market, by Software Type
- CNC Machining CAM Software Market, by Deployment Mode
- CNC Machining CAM Software Market, by End-User Industry
- CNC Machining CAM Software Market, by Application
- CNC Machining CAM Software Market, by Functionality
- CNC Machining CAM Software Market, by User Type
- CNC Machining CAM Software Market, by Number of Axes
- CNC Machining CAM Software Market, by Operating Platform
- CNC Machining CAM Software Market, by Integration Capability
- CNC Machining CAM Software Market, by Pricing Model
- CNC Machining CAM Software Market, by Software Features
- Americas CNC Machining CAM Software Market
- Asia-Pacific CNC Machining CAM Software Market
- Europe, Middle East & Africa CNC Machining CAM Software Market
- Competitive Landscape
- ResearchAI
- ResearchStatistics
- ResearchContacts
- ResearchArticles
- Appendix
- List of Figures [Total: 38]
- List of Tables [Total: 684 ]
Call to Action: Engage with Ketan Rohom for In-Depth Analysis
For a comprehensive deep dive into these findings and to access proprietary data on market segmentation, regional dynamics, and competitive intelligence, connect directly with Ketan Rohom, Associate Director, Sales & Marketing. He can guide you through the report’s strategic insights, answer specific questions, and facilitate a tailored briefing. Secure your copy of the full market research report to inform procurement strategies, technology roadmaps, and growth initiatives in CNC machining CAM software. Reach out via email at [email protected] or by phone to schedule your personalized consultation today. Don’t miss the opportunity to gain actionable intelligence that will drive competitive advantage and operational resilience in the years ahead.
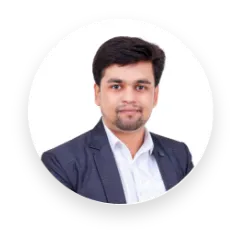
- When do I get the report?
- In what format does this report get delivered to me?
- How long has 360iResearch been around?
- What if I have a question about your reports?
- Can I share this report with my team?
- Can I use your research in my presentation?