The Coating Pretreatment Market size was estimated at USD 4.05 billion in 2024 and expected to reach USD 4.25 billion in 2025, at a CAGR 4.79% to reach USD 5.36 billion by 2030.

Setting the Stage for a New Era in Coating Pretreatment
Coating pretreatment stands as a critical foundation in the lifecycle of coated products, delivering both functional performance and aesthetic quality. As manufacturers strive to meet increasingly stringent environmental standards while enhancing corrosion resistance and adhesion, pretreatment processes have evolved far beyond their traditional roles in industrial finishing. This section introduces the key forces reshaping the pretreatment landscape and sets the stage for a detailed exploration of market trends, regulatory impacts, and strategic imperatives.
Over the past decade, the industry has witnessed a paradigm shift driven by regulatory pressures, sustainability mandates, and rising customer expectations for durability and environmental stewardship. Legacy chemistries are being replaced by innovative solutions that reduce hazardous by-products and improve operational efficiency. At the same time, global supply chain complexities and trade policies are reshaping sourcing strategies and cost structures for suppliers and end users alike.
This executive summary distills the most salient insights gleaned from rigorous primary interviews with industry leaders and comprehensive secondary research. It highlights transformative shifts in regulatory frameworks, the cumulative impact of recent tariff developments, granular segmentation analysis, regional performance drivers, competitive positioning, and prescriptive recommendations. The goal is to equip decision makers with actionable intelligence to navigate a rapidly changing pretreatment environment and capitalize on emerging opportunities.
Emerging Forces Redefining Pretreatment Practices
The pretreatment sector is undergoing transformative shifts as sustainability, digitalization, and material innovation converge to redefine best practices. Regulatory authorities around the globe are phasing out hexavalent chromium processes, prompting companies to accelerate the adoption of non-chromate conversion coatings and zirconium-based treatments. These novel chemistries deliver comparable corrosion resistance while aligning with environmental compliance and workplace safety objectives.
Meanwhile, the rise of digital process controls and advanced analytics is enhancing quality assurance and operational efficiency in pretreatment lines. Real-time monitoring of bath chemistries, temperature profiles, and surface cleanliness enables rapid adjustments and predictive maintenance, minimizing downtime and reducing chemical waste. This data-driven approach is becoming a must-have capability for industry leaders seeking to differentiate on service reliability and cost-effectiveness.
Supply chain resilience has also taken center stage, with raw material diversification and nearshoring strategies mitigating the risk of disruptions. Manufacturers are forging collaborative partnerships with chemical specialists to co-develop tailor-made pretreatment solutions, accelerating product innovation cycles and reinforcing customer loyalty. These strategic alliances are poised to shape competitive dynamics in the years ahead.
Evaluating US Tariffs’ Ripple Effects in 2025
The introduction of United States tariffs on imported steel, aluminum, and strategic chemicals in 2025 has had a cascading impact on the pretreatment ecosystem. Elevated input costs for galvanizing chemicals and metal substrates have squeezed margins for pretreatment providers and downstream applicators. Many organizations have responded by passing incremental cost increases to end users, but prolonged price adjustments have triggered a reassessment of procurement and process configurations.
Far-reaching supply chain realignments have become commonplace. Equipment fabricators and chemical formulators are evaluating domestic sourcing options and multi-supplier strategies to cushion against tariff volatility. These shifts have also sparked renewed interest in high-efficiency pretreatment systems that minimize chemical consumption and waste generation, effectively offsetting some of the added import levies.
From a market perspective, the tariff-induced headwinds have catalyzed consolidation among smaller regional players. Larger pretreatment specialists with diversified global footprints and robust innovation pipelines are reinforcing their competitive advantage. As companies adapt to the new cost realities, the focus is increasingly on securing long-term supply agreements, optimizing process yields, and exploring alternative substrate materials that may reduce dependency on tariff-affected imports.
Decoding Segmentation Trends Shaping Pretreatment Market
A nuanced understanding of pretreatment technologies reveals distinct growth vectors and optimization opportunities. Chromate conversion remains a stalwart choice for high-performance applications, with both hexavalent and trivalent variants delivering industry-proven corrosion control. Yet the trajectory is shifting toward non-chromate conversion alternatives, including phosphorosilicate treatments and silanization chemistries, which are gaining traction in sectors demanding stringent environmental compliance. Outside of conversion coatings, passivation processes continue to safeguard stainless surfaces, while phosphating options-ranging from iron phosphate to manganese and zinc phosphate-offer tailored adhesion and wear properties. Zirconium treatments, prized for their environmentally benign profile, are emerging as a versatile solution for multi-metal substrates.
Material substrate considerations further refine pretreatment strategies. Aluminum and its alloys, whether cast or wrought, represent a core substrate class for industries such as automotive and aerospace, requiring specialized chemistries to address porosity and surface oxide layers. Galvanized steel has long dominated construction and general industrial markets, while iron and steel-spanning carbon steel to stainless variants-demand differentiated phosphate and conversion treatments to balance cost and performance.
On the end user front, appliances and general industrial equipment continue to drive volume demand, while electronics and construction segments prioritize thin-film pretreatment solutions with minimal environmental footprint. The automotive sector, inclusive of OEM and aftermarket channels, exerts considerable influence on specification standards and innovation roadmaps. Across all usage scenarios, decision makers are gravitating toward modular pretreatment lines that can be quickly reconfigured to accommodate evolving substrate and regulatory requirements.
This comprehensive research report categorizes the Coating Pretreatment market into clearly defined segments, providing a detailed analysis of emerging trends and precise revenue forecasts to support strategic decision-making.
- Pretreatment Technology
- Substrate Material
- End Use Industry
Regional Dynamics Steering Market Trajectories
Regional dynamics are exerting a profound influence on pretreatment market trajectories as manufacturers calibrate their strategies to localized regulatory frameworks and demand patterns. In the Americas, there is heightened emphasis on compliance with stringent environmental statutes and workplace safety regulations, which has accelerated the uptake of non-chromate and zirconium-based pretreatment chemistries. The North American appetite for lightweight materials in automotive and aerospace applications is also driving specialized solutions for aluminum alloys.
Across Europe, Middle East, and Africa, a mosaic of regulatory regimes is fueling innovation in low-emission pretreatment technologies. The European Union’s REACH directives have catalyzed the phase-out of hazardous substances, prompting an uptick in passivation and silanization processes. In the Middle East, rapid infrastructure development is elevating demand for galvanized steel applications, while Africa’s expanding industrial base is opening new avenues for cost-efficient phosphate treatments.
The Asia-Pacific region remains the largest growth engine, buoyed by robust manufacturing activity in electronics, construction, and general industrial sectors. Countries within this region are investing heavily in digital pretreatment platforms that integrate Industry 4.0 capabilities, enabling automated bath monitoring and closed-loop process control. Meanwhile, the push for greener chemistries is intensifying as major end users seek to align with global sustainability benchmarks.
This comprehensive research report examines key regions that drive the evolution of the Coating Pretreatment market, offering deep insights into regional trends, growth factors, and industry developments that are influencing market performance.
- Americas
- Europe, Middle East & Africa
- Asia-Pacific
Competitive Landscape Spotlight
The competitive landscape in pretreatment is defined by a blend of global chemical majors and specialized process solution providers. Leading firms are leveraging deep formulation expertise to expand product portfolios with advanced non-chromate, zirconium, and passivation chemistries. Strategic alliances with equipment manufacturers are enabling bundled offerings that simplify integration for end users, while digital service platforms provide remote monitoring and maintenance support.
Innovation investments are particularly pronounced in R&D for next-generation pretreatment processes that emphasize low temperature operation, reduced cycle times, and closed-loop resource management. Some market leaders are piloting bio-based chemistries that promise to further diminish environmental impact without compromising performance. Meanwhile, a wave of targeted acquisitions is consolidating niche players that excel in region-specific technologies or end use verticals.
Market incumbents are also differentiating through technical support networks and training programs designed to bolster customer proficiency in new process implementations. This consultative approach not only accelerates technology adoption but also fosters long-term partnerships built on shared sustainability goals and operational excellence.
This comprehensive research report delivers an in-depth overview of the principal market players in the Coating Pretreatment market, evaluating their market share, strategic initiatives, and competitive positioning to illuminate the factors shaping the competitive landscape.
- Henkel AG & Co. KGaA
- PPG Industries, Inc.
- Akzo Nobel N.V.
- BASF SE
- Axalta Coating Systems Ltd.
- 3M Company
- MKS Instruments, Inc.
- Element Solutions Inc.
- Quaker Houghton Corporation
- DuPont de Nemours, Inc.
Strategic Imperatives for Market Leadership
To thrive in the evolving pretreatment environment, industry leaders must pursue a dual strategy of sustainable innovation and operational resilience. Investing in green chemistries-such as non-chromate conversion treatments and zirconium-based systems-will ensure compliance with tightening environmental regulations and unlock differentiated value propositions for customers. Concurrently, companies should deploy digital monitoring solutions across pretreatment lines to achieve real-time visibility into process parameters and proactively address deviations.
Supply chain agility will be critical in navigating tariff fluctuations and raw material volatility. Establishing multi-sourcing agreements and nearshoring key components can mitigate risk, while long-term partnerships with chemical experts support joint development of custom formulations. Additionally, fostering cross-functional collaboration between R&D, operations, and sustainability teams will expedite the commercialization of next-generation pretreatment solutions.
Finally, cultivating deep customer engagement through training initiatives and service ecosystems will strengthen loyalty and provide a platform for upselling advanced technologies. By aligning product roadmaps with end user requirements and regulatory trends, pretreatment providers can secure enduring competitive advantage.
Methodological Rigor Behind the Analysis
This analysis integrates a rigorous, multi-faceted research methodology designed to ensure both depth and accuracy. The study began with exhaustive secondary research, encompassing industry publications, regulatory filings, and technical journals to map the competitive and regulatory landscape. Complementing this desk research, we conducted in-depth interviews with senior executives, process engineers, and procurement specialists across key end use industries to capture firsthand perspectives on technology adoption, supply chain challenges, and strategic priorities.
Quantitative data was cross-verified through a triangulation approach, synthesizing information from public financial disclosures, trade association reports, and government statistics. Proprietary databases provided granular transaction-level details on raw material pricing, equipment investments, and merger and acquisition activities. Where possible, we benchmarked findings against comparable markets to validate assumptions and identify outlier trends.
Throughout the process, all insights were subjected to a multi-tiered quality control review, including peer validation and expert panel discussions, to confirm the robustness of conclusions and recommendations. This comprehensive methodology underpins the credibility of the strategic insights presented herein.
Explore AI-driven insights for the Coating Pretreatment market with ResearchAI on our online platform, providing deeper, data-backed market analysis.
Ask ResearchAI anything
World's First Innovative Al for Market Research
Synthesis of Pretreatment Market Evolution
The coating pretreatment sector stands at the nexus of regulatory evolution, technological innovation, and shifting trade policies. As legacy chemistries yield to greener alternatives, and digital process controls become mainstream, the market is redefining its parameters for success. Navigating the intricate interplay of tariffs, raw material sourcing, and customer requirements demands a forward-looking strategy grounded in rigorous segmentation analysis and regional intelligence.
Key findings emphasize that companies prioritizing sustainable innovation and supply chain flexibility will outpace peers in both developed and emerging markets. The transition toward modular pretreatment platforms and closed-loop resource management systems represents a critical enabler for cost optimization and environmental compliance. Moreover, deep collaboration between pretreatment providers and end users will accelerate the co-development of customized solutions that meet exacting performance and regulatory standards.
Armed with a clear understanding of market segment dynamics, regional growth drivers, and the competitive landscape, decision makers can craft targeted strategies that leverage core strengths and mitigate emerging risks. This executive summary serves as your strategic compass for steering through a period of rapid industry transformation.
This section provides a structured overview of the report, outlining key chapters and topics covered for easy reference in our Coating Pretreatment market comprehensive research report.
- Preface
- Research Methodology
- Executive Summary
- Market Overview
- Market Dynamics
- Market Insights
- Cumulative Impact of United States Tariffs 2025
- Coating Pretreatment Market, by Pretreatment Technology
- Coating Pretreatment Market, by Substrate Material
- Coating Pretreatment Market, by End Use Industry
- Americas Coating Pretreatment Market
- Europe, Middle East & Africa Coating Pretreatment Market
- Asia-Pacific Coating Pretreatment Market
- Competitive Landscape
- ResearchAI
- ResearchStatistics
- ResearchContacts
- ResearchArticles
- Appendix
- List of Figures [Total: 22]
- List of Tables [Total: 459 ]
Drive Growth with Customized Pretreatment Market Intelligence
To unlock a deeper understanding of coating pretreatment market dynamics and equip your organization with tailored strategic insights, engage with Ketan Rohom, Associate Director of Sales & Marketing at 360iResearch. His expertise in guiding leaders through complex regulatory landscapes and technological disruptions ensures you receive a bespoke research package aligned to your business imperatives. Reach out today to secure access to the full market research report and position your team at the forefront of industry transformation.
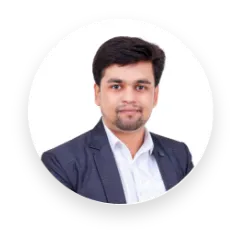
- How big is the Coating Pretreatment Market?
- What is the Coating Pretreatment Market growth?
- When do I get the report?
- In what format does this report get delivered to me?
- How long has 360iResearch been around?
- What if I have a question about your reports?
- Can I share this report with my team?
- Can I use your research in my presentation?