Introduction to Coil and Extrusion Coating Market Dynamics
The coil and extrusion coating market has emerged as a cornerstone of modern manufacturing, delivering enhanced surface properties, corrosion resistance, and aesthetic appeal across diverse sectors. At its core, coil coating applies thin polymeric layers to metal coils, while extrusion coating bonds molten polymers to substrates under high pressure. Together, these processes optimize performance characteristics-ranging from chemical resistance and UV stability to electrical insulation and decorative finish-without compromising throughput or cost efficiency.
In recent years, the industry has navigated shifting customer demands, evolving regulatory landscapes, and intensified competition. Manufacturers increasingly prioritize sustainable chemistries and energy-efficient processes to meet stringent environmental standards. Simultaneously, the integration of digital controls and predictive maintenance has elevated operational reliability, reducing downtime and waste.
As stakeholders seek resilient supply chains and agile production capabilities, understanding the interplay of raw material selection, substrate compatibility, and coating technology becomes paramount. This executive summary frames the transformative forces reshaping the market and lays out critical insights to inform strategic decision-making. Through a detailed examination of tariff impacts, segment dynamics, regional nuances, and competitive positioning, industry leaders can chart a course for innovation, growth, and long-term value creation.
Transformative Shifts Shaping the Coating Landscape
Over the past decade, the coil and extrusion coating landscape has undergone a profound metamorphosis driven by four interrelated forces. First, tightening environmental regulations have accelerated the shift from solvent-based to water-based and radiation-curable coatings, compelling formulators to invest in low-VOC chemistries and closed-loop recycling systems.
Second, sustainability mandates and circular economy principles have spurred adoption of fluoropolymer and advanced polymer blends, enabling longer service life, enhanced recyclability, and reduced life-cycle emissions. This has elevated coatings from a purely functional layer to a strategic enabler of product stewardship.
Third, digital transformation has permeated production floors. Industry 4.0 technologies-such as real-time process monitoring, predictive analytics, and automated quality inspection-have sharpened process control, trimmed waste, and shortened time-to-market.
Finally, supply chain resilience has become a competitive differentiator. Manufacturers are diversifying feedstock sources, reshoring critical processes, and forging strategic alliances with substrate producers to mitigate volatility in aluminum, steel, and plastic markets. Together, these shifts set the stage for a more agile, sustainable, and technology-driven coating ecosystem.
Cumulative Impact of United States Tariffs in 2025
The imposition of new United States tariffs in 2025 on coated steel and aluminum products has reverberated throughout the supply chain. Raw material suppliers have recalibrated pricing models, passing higher input costs downstream. Coating formulators have responded by streamlining formulations to reduce reliance on tariff-sensitive substrates and by negotiating long-term contracts to hedge against further fluctuations.
Original equipment manufacturers and end-use sectors faced a dual challenge: absorbing cost inflation or transferring charges to customers. Many opted for product differentiation-such as premium UV-resistant finishes or integrated corrosion inhibitors-to justify price adjustments, while others explored alternative substrates and hybrid coil-extrusion workflows.
At the distribution level, importers have shifted sourcing strategies toward regional partners, stimulating growth in localized coil coating lines and extrusion plants. Simultaneously, tariff-driven supply realignment has accelerated investments in domestic capacity expansion, particularly in high-value segments like electric vehicle enclosures and architectural panels.
Though short-term margins faced pressure, the industry’s collective focus on innovation and process optimization has fostered new value propositions, enabling some players to emerge stronger post-tariff.
Comprehensive Segmentation Insights Across Multiple Lenses
Dissecting the market through multiple segmentation lenses reveals nuanced growth trajectories and investment priorities. When analyzed by application type, Automotive demands continue to surge-especially among Electric Vehicles-while Building & Construction gains traction in both commercial high-rise facades and residential roofing. Consumer Goods coatings are evolving with consumer electronics and smart furniture, and Packaging applications for food and beverage benefit from barrier-enhancing extrusion films.
From an end-use industry perspective, Agriculture coatings are adapting to harsher agrochemical exposures, prompting extruded irrigation pipes to incorporate UV-stabilized PE. Appliance finishes favor water-based polyester resins for large and small appliances alike, and OEMs and aftermarket channels for Electric Vehicle Manufacturers are partnering on next-generation coil-coated battery enclosures and charging infrastructure components.
Material type insights highlight a resurgence of aluminum coils for lightweight structures, while cold-rolled steel continues to dominate building panels. Polymer extrusion is diversifying beyond PE and PVC toward high-performance films. Technology segmentation underscores a gradual transition from traditional solvent-based liquid systems to thermoset powder and UV-curable coatings, driven by efficiency and compliance goals.
Resin type differentiation shows fluoropolymer PVDF coatings retaining their leadership in architectural markets, whereas silicone blends gain ground in high-temperature industrial applications. Manufacturing process segmentation indicates that continuous coil coating lines with real-time quality feedback are outpacing batch processes, and twin-screw extrusion techniques are enabling more consistent multi-layer barrier films.
Substrate choice remains critical: galvanized steel offers cost advantages for infrastructure panels, while stainless steel underlays are preferred for food-grade extrusion. Finally, finish preferences vary by end market-high-gloss surfaces dominate appliance aesthetics, satin matte is popular in office furniture, and textured finishes enhance building envelope performance.
This comprehensive research report categorizes the Coil & Extrusion Coating market into clearly defined segments, providing a detailed analysis of emerging trends and precise revenue forecasts to support strategic decision-making.
- Application Type
- End-Use Industry
- Material Type
- Technology
- Resin Type
- Manufacturing Process
- Substrate
- Finish Type
Key Regional Insights and Market Drivers
Regional performance patterns underscore divergent drivers and adoption curves. In the Americas, strong infrastructure spending and electrification initiatives boost demand for corrosion-resistant coil coatings in both automotive and construction. Latin American markets are increasingly localizing extrusion capacity to serve agricultural and packaging segments with UV-stabilized films.
Within Europe, Middle East & Africa, regulatory stringency is highest, fostering leadership in water-based and radiation-curable technologies. Architectural and industrial coatings benefit from stringent EU emissions targets, while Gulf markets prioritize corrosion protection against maritime climates. African agricultural coatings are gaining momentum as food security projects scale.
Asia-Pacific remains the largest consumption hub, with rapid urbanization fueling building & construction coatings and consumer electronics finishes in key markets such as China, India, and Southeast Asia. Domestic formulators are expanding continuous coil coating capacity, and extrusion lines are being retrofitted to handle advanced polymer blends for high-barrier packaging.
This comprehensive research report examines key regions that drive the evolution of the Coil & Extrusion Coating market, offering deep insights into regional trends, growth factors, and industry developments that are influencing market performance.
- Americas
- Asia-Pacific
- Europe, Middle East & Africa
Key Competitive Insights Among Leading Players
The competitive landscape features global conglomerates, regional specialists, and emerging innovators. AkzoNobel N.V. maintains leadership through its high-performance fluoropolymer portfolio, while AmeriCoats, Inc. focuses on niche building envelope solutions. Anderol Specialty Lubricants and Ashland Global Holdings Inc. differentiate via customized extrusion compounds and functional additives. Axalta Coating Systems Ltd. and BASF SE invest heavily in digital process solutions, and Beckers Group leverages an extensive coil coating network in Europe.
Berndorf Band Group and Dura Coat Products, Inc. address steel substrate challenges with integrated line solutions, and ECKART Ltd. specializes in metallic effect pigments for decorative finishes. Freudenberg Group pioneers sustainable binder chemistries, while Henkel AG & Co. KGaA and ILVA Group co-develop UV-curable systems. Jotun Group expands its extrusion footprint in marine applications, and Kansai Paint Co., Ltd. accelerates water-based coating adoption in Asia.
Nippon Paint Holdings Co., Ltd. and PPG Industries, Inc. sustain growth through broad resin portfolios, and Sherwin-Williams Company (including Valspar) leverages cross-segment synergies. Wacker Chemie AG rounds out the landscape with silicone and specialty resins for extreme-environment coatings.
This comprehensive research report delivers an in-depth overview of the principal market players in the Coil & Extrusion Coating market, evaluating their market share, strategic initiatives, and competitive positioning to illuminate the factors shaping the competitive landscape.
- AkzoNobel N.V.
- AmeriCoats, Inc.
- Anderol Specialty Lubricants
- Ashland Global Holdings Inc.
- Axalta Coating Systems Ltd.
- BASF SE
- Beckers Group
- Berndorf Band Group
- Dura Coat Products, Inc.
- ECKART Ltd.
- Freudenberg Group
- Henkel AG & Co. KGaA
- ILVA Group
- Jotun Group
- Kansai Paint Co., Ltd.
- Nippon Paint Holdings Co., Ltd.
- PPG Industries, Inc.
- Sherwin-Williams Company
- Valspar (part of Sherwin-Williams)
- Wacker Chemie AG
Actionable Recommendations for Industry Leaders
To navigate this dynamic environment, industry leaders should prioritize three strategic imperatives. First, accelerate the deployment of automation and digital twins to enhance throughput and quality consistency. Real-time analytics can preempt defects, optimize resource utilization, and support agile production scaling.
Second, deepen partnerships across the value chain-from substrate suppliers and equipment OEMs to end-use industry stakeholders-to co-innovate sustainable chemistries and modular coating lines. Collaborative research and co-development agreements will expedite time-to-market for next-generation products.
Third, tailor regional go-to-market strategies by leveraging local regulatory knowledge and customer insights. Whether adapting extrusion film formulations for tropical climates or introducing low-temperature cure systems for cold-chain packaging, localized solutions will differentiate providers and strengthen customer loyalty.
Explore AI-driven insights for the Coil & Extrusion Coating market with ResearchAI on our online platform, providing deeper, data-backed market analysis.
Ask ResearchAI anything
World's First Innovative Al for Market Research
Conclusion and Future Outlook
The coil and extrusion coating industry stands at a pivotal juncture, where regulatory pressures, sustainability demands, and technological breakthroughs converge. Stakeholders who anticipate shifting raw material dynamics, invest in next-generation process controls, and cultivate deep value-chain collaborations will emerge as market designers rather than followers.
By embracing digital integration, green chemistry, and agile supply chain models, organizations can not only mitigate risks tied to tariffs and compliance but also unlock new revenue streams in high-growth end markets-such as electric mobility, smart infrastructure, and advanced packaging.
Ultimately, success will hinge on the ability to transform coating lines into adaptive platforms, capable of rapid product changeovers and data-informed optimization. Those who master this balance of innovation and operational excellence will define the future contours of the market.
This section provides a structured overview of the report, outlining key chapters and topics covered for easy reference in our Coil & Extrusion Coating market comprehensive research report.
- Preface
- Research Methodology
- Executive Summary
- Market Overview
- Market Dynamics
- Market Insights
- Cumulative Impact of United States Tariffs 2025
- Coil & Extrusion Coating Market, by Application Type
- Coil & Extrusion Coating Market, by End-Use Industry
- Coil & Extrusion Coating Market, by Material Type
- Coil & Extrusion Coating Market, by Technology
- Coil & Extrusion Coating Market, by Resin Type
- Coil & Extrusion Coating Market, by Manufacturing Process
- Coil & Extrusion Coating Market, by Substrate
- Coil & Extrusion Coating Market, by Finish Type
- Americas Coil & Extrusion Coating Market
- Asia-Pacific Coil & Extrusion Coating Market
- Europe, Middle East & Africa Coil & Extrusion Coating Market
- Competitive Landscape
- ResearchAI
- ResearchStatistics
- ResearchContacts
- ResearchArticles
- Appendix
- List of Figures [Total: 32]
- List of Tables [Total: 1342 ]
Call to Action: Connect with Ketan Rohom for Expert Insights
To explore comprehensive data, strategic analysis, and tailored insights on the coil and extrusion coating market, reach out to Ketan Rohom, Associate Director, Sales & Marketing. He can guide you through the research methodology, address your specific industry challenges, and help secure the full report to support your strategic initiatives.
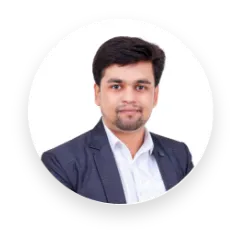
- When do I get the report?
- In what format does this report get delivered to me?
- How long has 360iResearch been around?
- What if I have a question about your reports?
- Can I share this report with my team?
- Can I use your research in my presentation?