Introduction: Market Dynamics and Strategic Priorities in Cold Drawn Bar Industry
The cold drawn bar market plays a critical role in modern manufacturing by delivering precision-engineered metal bars with tight dimensional tolerances and superior surface finishes. As industries from automotive to oil and gas demand components that combine strength, reliability, and cost efficiency, cold drawn bars have emerged as a go-to solution for shafts, fasteners, gears, and structural components. Their enhanced mechanical properties arise from a controlled deformation process that improves grain structure, increases tensile strength, and minimizes surface imperfections. This executive summary examines key dynamics shaping the market, offering decision-makers an authoritative snapshot of technological shifts, regulatory impacts, and strategic priorities.
Amid rising infrastructure investments, intensified competition, and evolving end-use requirements, stakeholders must navigate a complex environment of tariff fluctuations, sustainability mandates, and customization demands. By integrating advanced manufacturing methods, material innovations, and data-driven quality controls, leading producers are redefining value propositions across segments. This introduction sets the stage for an in-depth exploration of transformative trends, tariff implications, segmentation analytics, regional distinctions, competitive positioning, and actionable recommendations that will inform strategic roadmaps for industry leaders.
Transformative Shifts Redefining the Cold Drawn Bar Market
Rapid digitization and heightened emphasis on sustainability have catalyzed transformative shifts across the cold drawn bar landscape. Automation of finishing lines, real-time process monitoring, and predictive maintenance are driving unprecedented gains in throughput and consistency. Manufacturers investing in Industry 4.0 technologies now leverage advanced sensors and AI-powered analytics to detect micro-defects before they propagate, reducing scrap rates while optimizing production schedules.
Concurrently, an industry-wide pivot toward low-carbon and recycled feedstocks is reshaping supply chains. Producers are collaborating with steel mills to qualify high-strength low alloy and micro alloy variants that meet stringent carbon footprint targets without compromising performance. In parallel, development of new stainless steel grades-spanning austenitic, duplex, ferritic, martensitic, and precipitation hardened families-reflects an imperative to balance corrosion resistance with weight reduction and cost control.
Finally, demand for bespoke profiles in flat, hexagon, round, and square shapes underscores the rise of mass customization. Whether tailored hydraulic shafts for heavy machinery or precision round bars for medical instruments, manufacturers are augmenting cold drawn, cold finished, peeled, and turned capabilities to deliver short-run variants with lead times that align with agile production models. These combined technological and sustainability vectors are reshaping competitiveness and value creation across the value chain.
Cumulative Impact of United States Tariffs 2025 on Cold Drawn Bars
The introduction of new tariffs on imported steel in 2025 has generated a cumulative impact that reverberates across procurement, pricing, and trade strategies. Building on previous Section 232 duties, these measures have increased duties on specific cold drawn bar categories, prompting buyers to reassess sourcing models. Domestic producers have seized the opportunity to expand capacity and renegotiated long-term supply agreements to capture redirected demand.
For importers, the heightened duty structure has increased landed costs for carbon steel variants-from high carbon and medium carbon to low carbon-while stainless steel imports face additional charges on duplex and precipitation hardened grades. Industry stakeholders report a shift toward nearshoring suppliers in the Americas and Europe, where tariff barriers remain lower and logistical lead times are more predictable. This realignment, however, has introduced new challenges in terms of materials qualification and inventory management.
To mitigate margin erosion, several participants are pursuing vertical integration, securing downstream capabilities in peeling and turning operations to add value domestically. Others are leveraging free trade agreements in key regions to obtain duty-exempt access for specialized bars used in structural components, reinforcement bars, and engine segments. As the market absorbs these tariff adjustments, flexibility in sourcing and agile contract frameworks have become essential to preserve competitiveness and cost discipline.
Key Segmentation Insights Driving Market Differentiation
A granular view across material type, shape, manufacturing method, diameter range, industry vertical, surface finish, grade standard, and application highlights nuanced opportunities and challenges. In alloy steel, high strength low alloy bars dominate demand for structural sections and powertrain components, while micro alloy variants gain traction in applications where weight savings translate to performance gains. Among carbon steel offerings, medium carbon grades strike an optimal balance of machinability and tensile strength, making them the workhorse choice for reinforcement bars and fasteners. Stainless steel segments reveal distinct growth paths: austenitic types lead in corrosion-critical applications, whereas duplex and ferritic bars are selected for elevated strength and lower nickel content respectively.
Shape preferences diverge by end use. Round profiles remain the most popular for shafts and rods, hexagon and square bars prevail in fastener production, and flat bars cater to reinforcement and structural component manufacturing. On the production floor, cold drawn processes maintain their dominance for high-precision tolerances, with peeled and turned methods employed for specialty finishes and tight surface requirements. Diameter segmentation further refines product strategies: sub-one-inch ranges-particularly the 0.500–0.999 inch window-drive demand in hydraulic components and small-diameter tools, while bars above one inch, especially in the 1.001–2.000 inch bracket, serve heavy machinery and structural frames.
Diverse industry applications reinforce the importance of tailored offerings. Engine components in aerospace demand stringent material certifications, whereas automotive powertrain bars prioritize fatigue resistance. Construction applications lean on reinforcement bars with predictable yield properties, and oil and gas sectors rely on corrosion-resistant variants. Surface finish choices-from galvanized or powder coated to polished and unpolished-complement grade standards like ASTM A108, A36, EN8, EN19, and JIS specifications to meet unique customer requirements. Finally, end-use applications such as gears, hydraulic components, shafts, and tools underscore the market’s need for integrated quality assurance and process control across the value chain.
This comprehensive research report categorizes the Cold Drawn Bar market into clearly defined segments, providing a detailed analysis of emerging trends and precise revenue forecasts to support strategic decision-making.
- Material Type
- Shape
- Manufacturing Method
- Diameter Range
- Industry
- Surface Finish
- Grade Standard
- Application
Key Regional Insights Shaping Global Supply and Demand
Regional dynamics are reshaping global supply and demand flows in distinct ways. In the Americas, robust infrastructure spending and nearshoring trends underpin steady growth in carbon steel reinforcements and high strength alloy bars. Producers benefit from proximity to major automotive and machinery OEMs, enabling just-in-time deliveries for manufacturing hubs in North America and Brazil.
Across Europe, the Middle East, and Africa, stringent environmental regulations and decarbonization pledges are accelerating adoption of recycled and low-carbon feedstocks. Demand for stainless steel bars remains strong in the energy sector, particularly for oil and gas infrastructure in the Middle East and corrosion-resistant structural components in northern Europe. Manufacturers in EMEA are investing in green steel initiatives and digital quality management systems to secure a competitive edge.
Asia-Pacific continues to account for the largest volume consumption, driven by rapid urbanization, industrial expansion in China and India, and a booming electronics sector in Southeast Asia. The region’s integrated steel mills and cold drawing facilities offer cost advantages, but rising labor costs and environmental scrutiny are prompting strategic investments in automation and energy-efficient processes. As trade policies evolve, Asia-Pacific suppliers are increasingly targeting export markets with value-added offerings, while regional buyers seek diversified sourcing to balance cost, quality, and delivery reliability.
This comprehensive research report examines key regions that drive the evolution of the Cold Drawn Bar market, offering deep insights into regional trends, growth factors, and industry developments that are influencing market performance.
- Americas
- Asia-Pacific
- Europe, Middle East & Africa
Key Companies Insights: Competitive Strategies and Market Positioning
Leading players are deploying varied strategies to capture market share and reinforce supply chains. AK Steel Holding Corporation has expanded its cold drawing capacity through partnerships focused on automotive and machinery segments, while ArcelorMittal S.A. emphasizes its advanced steel grades and integrated processing to serve high-end industrial applications. Gerdau S.A. leverages its Latin American footprint to supply reinforcement bars and structural sections for infrastructure projects.
Kobe Steel, Ltd. and Nippon Steel Corporation are driving joint development projects for specialty stainless alloys, targeting markets in oil and gas and chemical processing. Nucor Corporation and Steel Dynamics, Inc. differentiate through nimble production models that prioritize short-cycle, high-mix runs for fasteners and tool manufacturers. POSCO is channeling investments into low-carbon steelmaking and digital quality controls, while Tata Steel Limited focuses on localized value chain integration in both Europe and Asia.
ThyssenKrupp AG continues to refine its cold rolled and peeled offerings to support precision engineering sectors, and SSAB AB is capitalizing on its expertise in high-strength steels for heavy equipment. Sidenor Steel Industries, S.A. has carved a niche in rebar and structural profiles for European construction, and Nucor’s sister companies have bolstered turn-key services that integrate peeling, turning, and coating. Through these differentiated approaches, top companies are solidifying their positions by aligning product portfolios with evolving customer requirements and regulatory landscapes.
This comprehensive research report delivers an in-depth overview of the principal market players in the Cold Drawn Bar market, evaluating their market share, strategic initiatives, and competitive positioning to illuminate the factors shaping the competitive landscape.
- AK Steel Holding Corporation
- ArcelorMittal S.A.
- Gerdau S.A.
- Kobe Steel, Ltd.
- Nippon Steel Corporation
- Nucor Corporation
- POSCO
- Sidenor Steel Industries, S.A.
- SSAB AB
- Steel Dynamics, Inc.
- Tata Steel Limited
- ThyssenKrupp AG
Actionable Recommendations for Industry Leaders
Industry leaders should prioritize integrated supply chain resilience by diversifying raw material sources and forging strategic alliances with steel mills. Establishing flexible contracts that allow for rapid scale-up of cold drawing, peeling, and turning capacities will mitigate uncertainties arising from tariff changes and raw material volatility. Investing in advanced process analytics and real-time monitoring systems can reduce scrap rates by identifying defects early, thereby improving margins and delivery reliability.
Sustainability must be a core pillar of future strategy: collaborating with suppliers to qualify recycled feedstocks and low-carbon alloys will address customer decarbonization mandates and differentiate offerings. Additionally, expanding value-added services-such as in-house finishing, custom heat-treating, and end-user technical support-will foster stronger customer loyalty and higher ASPs. Leaders should also explore digital platforms that enable order tracking, performance analytics, and predictive maintenance, transforming the buying experience into a data-driven partnership.
Finally, engaging proactively with regulatory bodies to shape trade policies and standards will ensure favorable conditions for cross-border trade. By aligning innovation roadmaps with industry 4.0 initiatives, sustainability goals, and localized production models, firms can unlock new growth corridors and reinforce competitive moats.
Explore AI-driven insights for the Cold Drawn Bar market with ResearchAI on our online platform, providing deeper, data-backed market analysis.
Ask ResearchAI anything
World's First Innovative Al for Market Research
Conclusion: Charting a Path Forward in the Cold Drawn Bar Market
Throughout this executive summary, we have dissected the critical forces redefining the cold drawn bar market-from digital transformation and sustainability imperatives to tariff impacts and segmentation insights. A clear picture has emerged: success will hinge on agility, technical excellence, and strategic foresight. By harnessing advanced manufacturing technologies, embracing eco-friendly materials, and cultivating resilient supplier networks, market participants can navigate volatility and secure long-term growth.
As regional dynamics continue to evolve, and as leading companies refine their competitive positions, the imperative for informed decision-making intensifies. Stakeholders who integrate comprehensive market intelligence with pragmatic action plans are best positioned to deliver superior value to customers while meeting rigorous cost and performance targets. This conclusion underscores the importance of ongoing vigilance and collaborative innovation within the cold drawn bar ecosystem.
This section provides a structured overview of the report, outlining key chapters and topics covered for easy reference in our Cold Drawn Bar market comprehensive research report.
- Preface
- Research Methodology
- Executive Summary
- Market Overview
- Market Dynamics
- Market Insights
- Cumulative Impact of United States Tariffs 2025
- Cold Drawn Bar Market, by Material Type
- Cold Drawn Bar Market, by Shape
- Cold Drawn Bar Market, by Manufacturing Method
- Cold Drawn Bar Market, by Diameter Range
- Cold Drawn Bar Market, by Industry
- Cold Drawn Bar Market, by Surface Finish
- Cold Drawn Bar Market, by Grade Standard
- Cold Drawn Bar Market, by Application
- Americas Cold Drawn Bar Market
- Asia-Pacific Cold Drawn Bar Market
- Europe, Middle East & Africa Cold Drawn Bar Market
- Competitive Landscape
- ResearchAI
- ResearchStatistics
- ResearchContacts
- ResearchArticles
- Appendix
- List of Figures [Total: 32]
- List of Tables [Total: 868 ]
Call to Action: Connect with Ketan Rohom for In-Depth Market Report
To explore these insights in greater depth and access proprietary analysis on market segmentation, regional dynamics, company strategies, and actionable roadmaps, we invite you to engage with Ketan Rohom, Associate Director, Sales & Marketing. Reach out today to secure your authoritative market research report and equip your organization with the intelligence needed to stay ahead in a rapidly evolving industry.
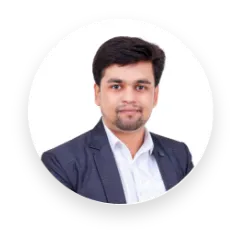
- When do I get the report?
- In what format does this report get delivered to me?
- How long has 360iResearch been around?
- What if I have a question about your reports?
- Can I share this report with my team?
- Can I use your research in my presentation?