Introduction
The combustion chamber lies at the heart of every high-performance engine, channeling intense heat and extreme pressure to convert fuel into thrust or mechanical power. This analysis begins by exploring how materials science, manufacturing techniques, and regulatory dynamics converge to shape today’s casting methods for combustion chambers. As industries pursue higher efficiency and lower emissions, innovations in composite reinforcements and advanced metal alloys have emerged alongside digital tooling and process control systems. Over the course of this report, we survey the key drivers that have propelled the casting segment forward, examine the evolving competitive landscape, and introduce critical insights into market segmentation, regional performance, and leading players. By starting with a clear understanding of current capabilities and challenges, decision-makers can align strategic investments with technological trends, securing both short-term gains and long-term resilience in a demanding global environment.
Transformative Shifts in the Landscape
In recent years, the casting industry for combustion chambers has undergone a seismic transformation driven by shifting performance requirements and sustainability imperatives. Traditional metal alloys, once favored for their strength and thermal resilience, are now complemented by fiber-reinforced composites that reduce weight while maintaining structural integrity. Digital twins and simulation platforms have replaced manual pattern making, streamlining everything from mold design to post-casting inspection. At the same time, additive manufacturing technologies such as binder jetting and selective laser sintering have moved from prototyping stages into pilot production runs, enabling complex geometries and internal cooling channels previously impossible with conventional processes.
Regulatory bodies worldwide have tightened emissions and efficiency standards, forcing engine and power system manufacturers to push for thinner walls and higher operating temperatures. In response, smart manufacturing systems equipped with in-process control are maximizing yield and reducing scrap, while nano-coatings and self-healing materials bolster both thermal performance and corrosion resistance. As a result, companies that once competed on cost alone now vie on a combination of material innovation, digital expertise, and rapid iteration capabilities. This landscape demands that stakeholders adapt swiftly or risk ceding ground to more agile, tech-driven rivals.
Cumulative Impact of United States Tariffs 2025
The introduction of tariffs on imported raw materials and cast components in the United States in 2025 has had far-reaching implications across the combustion chamber casting value chain. Excise duties on alloys such as aluminum, nickel, and specialty steels have raised input costs for domestic foundries, squeezing margins and accelerating efforts to near-shore production. As a result, several manufacturers have renegotiated supply contracts to secure lower duties through quota allocations or free trade agreement exemptions. Others have invested in advanced recycling programs to recapture high-value alloy content from scrap, offsetting increased procurement expenses.
The cumulative impact of tariffs extends beyond material costs, influencing customer purchasing patterns and project timelines. Aerospace and defense contractors have adopted dual-sourcing strategies to mitigate delays, while automotive OEMs have absorbed incremental charges through higher pricing tiers or longer lead times. Simultaneously, foundries with vertically integrated operations-those combining casting, machining, and heat treatment under one roof-have demonstrated greater resilience, leveraging in-house capabilities to control costs more effectively. Moving forward, the industry will likely witness further consolidation as smaller players seek partnerships and alliances to share the burden of tariff-driven capital investments.
Key Segmentation Insights
A deep dive into segmentation uncovers distinct corridors of growth and specialization. When materials form the basis of analysis, composites emerge as a compelling option, with fiber-reinforced systems supporting ultra-light chamber walls and particulate composites enhancing thermal insulation. Metal alloys remain essential, with aluminum grades-high-silicon variants for improved fluidity and low-magnesium formulations for reduced casting defects-standing out. Nickel-based superalloys like Inconel and Monel deliver unmatched heat resistance, whereas stainless and carbon steels balance cost and performance for mid-range applications.
Turning to manufacturing processes, die casting commands attention through both high-pressure and low-pressure variants, delivering rapid cycle times but requiring significant capital expenditures. Investment casting offers unparalleled surface finish and geometric complexity, while sand casting-available in both dry and green sand forms-provides flexibility for large or structurally demanding components. Shell molding completes the spectrum, blending aspects of precision and throughput.
Application-driven segmentation reveals aerospace’s emphasis on lean, high-reliability chambers for commercial aviation and defense, alongside automotive’s dual focus on heavy-duty commercial vehicles and fuel-efficient passenger cars. Oil & gas stakeholders, split between upstream exploration components and downstream processing units, demand corrosion-resistant alloys. In power generation, gas turbines favor nickel alloys, whereas steam turbines continue to rely on cost-effective steels.
End-user industries reinforce these themes: civil aviation and military programs under aerospace & defense, OEM and aftermarket channels in automotive, and a broad energy spectrum spanning renewables to fossil fuels. Characteristic requirements further refine choices: corrosion resistance and tensile strength form the backbone of structural integrity, while tolerance to extreme temperatures underscores thermal performance. Finally, innovation trends highlight additive manufacturing’s rising influence through binder jetting and selective laser sintering, advanced materials like nano-coatings and self-healing compounds, and smart manufacturing solutions encompassing automated workflows and in-process monitoring.
This comprehensive research report categorizes the Combustion Chamber Casting market into clearly defined segments, providing a detailed analysis of emerging trends and precise revenue forecasts to support strategic decision-making.
- Materials Used
- Manufacturing Process
- Application
- End-User Industry
- Characteristics
- Innovation Trend
Key Regional Insights
Regional dynamics for combustion chamber casting reflect both mature industrial bases and emerging market demand. In the Americas, established aerospace hubs in the United States and Canada drive consistent orders for high-precision chambers, while Latin American foundries are expanding downstream machining and finishing capabilities to integrate more deeply into global supply chains. Across Europe, the Middle East, and Africa, stringent environmental regulations in Western Europe have spurred adoption of green casting processes, whereas Gulf-region energy sector growth underpins demand for corrosion-resistant alloys. Eastern Europe offers competitive labor rates, attracting capacity for medium-volume investment and sand casting operations.
Asia-Pacific stands out for its rapid infrastructure development and booming power generation projects. China and India are scaling up domestic production of both aluminum and nickel alloys to reduce import dependency, and Japan and South Korea continue to pioneer advanced materials and smart factory implementations. Southeast Asia has emerged as a regional hub for contract manufacturing, blending lower costs with rising technical expertise. As supply chains diversify, each region’s unique strengths and policy incentives shape capital deployment and partnership strategies.
This comprehensive research report examines key regions that drive the evolution of the Combustion Chamber Casting market, offering deep insights into regional trends, growth factors, and industry developments that are influencing market performance.
- Americas
- Asia-Pacific
- Europe, Middle East & Africa
Key Companies Insights
Leading organizations in combustion chamber casting demonstrate diverse approaches to innovation and market positioning. Alcoa Corporation has leveraged its expertise in aluminum alloys and high-precision machining to serve aerospace giants, while Barron Industries focuses on lean manufacturing and rapid prototyping for specialty applications. Doncasters Group Ltd has strengthened its global footprint through strategic acquisitions, integrating both sand casting and investment casting facilities to meet varied customer demands.
Dynacast International distinguishes itself with micro-casting capabilities and stringent quality controls, targeting sectors that require intricate geometries. Farinia Group, with its extensive footprint in Eastern Europe, emphasizes cost-effective production and nimble floor-to-flight supply chains. Hitachi Metals, Ltd. brings decades of research in nickel superalloys, fueling innovations in thermal barrier coatings. Hitchiner Manufacturing Co., Inc. specializes in rapid cycle high-pressure die casting for automotive turbocharger housings and compact gas turbine components.
Precision Castparts Corp. remains a powerhouse in large-scale, high-temperature castings for land-based turbines, while TITAL GmbH focuses on tailor-made alloys and aftermarket services. Finally, Wescast Industries Inc. merges advanced design software with in-house machining to deliver turnkey solutions for defense and industrial gas turbines. Together, these companies shape a competitive environment driven by both technological differentiation and strategic geographic positioning.
This comprehensive research report delivers an in-depth overview of the principal market players in the Combustion Chamber Casting market, evaluating their market share, strategic initiatives, and competitive positioning to illuminate the factors shaping the competitive landscape.
- Alcoa Corporation
- Barron Industries
- Doncasters Group Ltd
- Dynacast International
- Farinia Group
- Hitachi Metals, Ltd.
- Hitchiner Manufacturing Co., Inc.
- Precision Castparts Corp.
- TITAL GmbH
- Wescast Industries Inc.
Actionable Recommendations for Industry Leaders
To capitalize on emerging opportunities, industry leaders should prioritize three strategic imperatives. First, invest selectively in digital transformation by integrating simulation, real-time monitoring, and predictive maintenance into casting lines; this will reduce defects and shorten time to market. Second, bolster material portfolios by partnering with research institutions or acquiring smaller firms specializing in advanced composites, nano-coatings, or self-healing matrices, thereby capturing value in high-margin segments.
Third, diversify supply chains through near-shoring and dual-sourcing arrangements, mitigating exposure to tariff fluctuations and geopolitical disruptions. In addition, develop circular economy initiatives that reclaim alloy scrap and reintroduce it into production, reducing reliance on volatile raw material markets. Furthermore, cultivate talent pipelines by instituting apprenticeship programs and cross-disciplinary training that bridge process engineering, digital analytics, and materials science, ensuring a workforce equipped to tackle tomorrow’s challenges.
By executing these recommendations in a synchronized manner, companies can secure immediate efficiency gains while building the resilience needed for long-term growth.
Explore AI-driven insights for the Combustion Chamber Casting market with ResearchAI on our online platform, providing deeper, data-backed market analysis.
Ask ResearchAI anything
World's First Innovative Al for Market Research
Conclusion
This exploration of combustion chamber casting underscores a sector in the midst of rapid evolution. From composite reinforcements and advanced alloys to additive processes and smart factories, technological progress is redefining what combustion chambers can achieve in engines and turbines. Tariff dynamics have injected new complexity into supply chain management, while segmentation insights highlight pockets of innovation across materials, processes, and end-use industries.
Regional analysis illustrates how local policies and infrastructure shape capacity and competitiveness, and the profiles of leading companies demonstrate varied pathways to differentiation. By aligning strategic investments with the trends identified here, organizations can not only navigate current headwinds but also position themselves as pioneers in a market that demands both technical excellence and operational agility.
This section provides a structured overview of the report, outlining key chapters and topics covered for easy reference in our Combustion Chamber Casting market comprehensive research report.
- Preface
- Research Methodology
- Executive Summary
- Market Overview
- Market Dynamics
- Market Insights
- Cumulative Impact of United States Tariffs 2025
- Combustion Chamber Casting Market, by Materials Used
- Combustion Chamber Casting Market, by Manufacturing Process
- Combustion Chamber Casting Market, by Application
- Combustion Chamber Casting Market, by End-User Industry
- Combustion Chamber Casting Market, by Characteristics
- Combustion Chamber Casting Market, by Innovation Trend
- Americas Combustion Chamber Casting Market
- Asia-Pacific Combustion Chamber Casting Market
- Europe, Middle East & Africa Combustion Chamber Casting Market
- Competitive Landscape
- ResearchAI
- ResearchStatistics
- ResearchContacts
- ResearchArticles
- Appendix
- List of Figures [Total: 28]
- List of Tables [Total: 1118 ]
Call-To-Action (CTA) with Ketan Rohom
To gain deeper insights and access granular data on combustion chamber casting-covering materials, processes, regional nuances, and competitor analysis-contact Ketan Rohom, Associate Director, Sales & Marketing at 360iResearch, today. Secure the intelligence needed to drive informed decisions and stay ahead of industry trends.
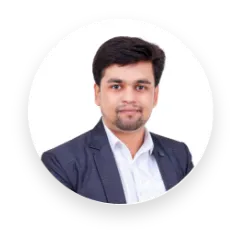
- When do I get the report?
- In what format does this report get delivered to me?
- How long has 360iResearch been around?
- What if I have a question about your reports?
- Can I share this report with my team?
- Can I use your research in my presentation?