The Commercial Aerospace Coatings Market size was estimated at USD 2.02 billion in 2024 and expected to reach USD 2.14 billion in 2025, at a CAGR 5.62% to reach USD 2.81 billion by 2030.

Introduction to the Dynamics of Commercial Aerospace Coatings
Commercial aerospace coatings serve as the first line of defense and the finishing touch for modern aircraft, balancing performance, aesthetics, and regulatory demands. As fleets expand and maintenance cycles intensify, coatings engineers and decision-makers confront a rapidly evolving mix of material innovations, application techniques, and environmental regulations. This executive summary offers a compelling overview of how emerging technologies, tariff shifts, and regional dynamics are reshaping the market, equipping leaders with the insights needed to navigate complex supply chains, optimize product portfolios, and anticipate shifting customer requirements.
Transformative Shifts Reshaping the Coatings Landscape
Over the past decade, the commercial aerospace coatings landscape has undergone transformative shifts driven by digitalization, sustainability imperatives, and advanced materials science. Coating formulators harness formulations embedded with nanomaterials and self-healing chemistries to extend service intervals, while smart coatings capable of real-time damage detection are transitioning from laboratory prototypes to on-wing demonstrations. Concurrently, airlines and MRO providers invest in AI-powered quality control systems that automate film-thickness measurement, defect detection, and curing verification, dramatically reducing rework rates.
At the same time, end-users demand eco-friendly alternatives that comply with increasingly stringent global VOC regulations, sparking accelerated adoption of powder coatings and water-borne technologies. Meanwhile, additive manufacturing introduces new substrate geometries that challenge conventional spraying methods and drive innovation in dip and brush application systems. These converging forces are redefining supplier–customer relationships, as coatings manufacturers pivot from transactional product supply to collaborative platform partnerships that integrate digital tools, regulatory guidance, and service-based support.
Assessing the Cumulative Impact of U.S. Tariffs in 2025
The cumulative impact of United States tariffs enacted in 2025 has reverberated across the commercial aerospace coatings supply chain, altering raw material sourcing, pricing strategies, and risk management practices. Faced with increased duties on imported resins and pigments, OEMs and MRO operators have accelerated qualification of domestic suppliers and reengineered formulations to incorporate locally produced feedstocks. This strategic pivot has mitigated exposure to currency fluctuations and shortened lead times, but it has also fueled upward pressure on unit costs, prompting firms to pursue operational efficiencies and volume discounts to preserve margins.
Tariff-driven cost increases have spurred greater collaboration between coatings formulators and substrate manufacturers, leading to co-development of pre-treated panels that minimize coating requirements without compromising corrosion resistance. At the same time, market participants are exploring free trade agreements and regional partnerships to diversify procurement networks for critical ingredients such as epoxy hardeners and specialized pigments. These adaptive measures are essential for maintaining competitive positioning in a landscape defined by policy volatility and global trade realignments.
Key Segmentation Insights Across Thirteen Market Dimensions
Analyzing the market by coating type reveals that electrocoatings are gaining traction for their uniform deposition and superior corrosion protection on fuselage assemblies, whereas primer coatings remain indispensable for ensuring adhesion to challenging substrates like carbon-fiber composites. Specialty coatings, formulated to withstand elevated service temperatures and resist erosion on propeller components, are witnessing incremental preference alongside advanced topcoat coatings that deliver UV stability and customizable branding finishes.
From a technology standpoint, powder coatings appeal to operators seeking zero-VOC solutions, while radiation cure coatings win favor in high-throughput paint shops for their rapid cure cycles and low energy consumption. Solvent-borne coatings continue to play a role in niche applications requiring high-solids formulations, even as water-borne systems steadily displace them in environmentally regulated regions.
In terms of application, the large-jet segment within the business aircraft category demands high-performance coatings optimized for extended maintenance intervals, whereas small jets focus on weight-saving formulations. Commercial aircraft coatings prioritize fast cure and minimal downtime, while helicopter applications require flexible, abrasion-resistant finishes. Military aircraft coatings emphasize stealth and durability under extreme operational conditions.
Examining material types, acrylic coatings offer excellent gloss retention and color stability, epoxy coatings deliver robust chemical and corrosion resistance, and polyurethane coatings strike an optimal balance between flexibility and hardness. Maintenance, repair and overhaul activities drive recurring demand for restoration-grade coatings, whereas original equipment manufacturers and aircraft manufacturers collaborate on integrated coating specifications during the production phase.
Finish type differentiation shows that gloss finishes remain the default for flagship fleet livery, matte finishes provide glare reduction for military and helicopter platforms, and satin finishes offer a compromise between aesthetic sheen and surface imperfection tolerance. Coating requirements for fuselage sections differ substantially from those for propellers and wings, with aerodynamic surfaces demanding low-drag, high-adhesion chemistries and complex curvatures necessitating specialized spray application techniques.
When considering durability class, high-durability coatings justify premium investment through extended service life on long-haul aircraft, while standard-durability alternatives serve commuter fleets with less rigorous cycle demands. Color options span pure white coatings that optimize thermal reflectivity, colored coatings aligned with airline branding strategies, and custom designs that enable unique liveries.
Purpose-driven formulations are emerging to meet aesthetic enhancement goals, deliver targeted corrosion protection in salt-spray environments, and embed environmental sustainability via bio-based resins and low-emission curing agents. Differences in substrate-whether composite material coatings designed for carbon-fiber reinforced panels or metal coatings tailored for aluminum and titanium alloys-influence primer selection and surface preparation protocols. Application methods range from automated spray booths for high-volume lines to manual brush and dip operations for complex assemblies. Finally, market trends highlight the growing influence of eco-friendly coatings that reduce carbon footprints, nano-coatings offering barrier properties at ultra-thin film weights, and smart coatings embedded with self-diagnostic capabilities.
This comprehensive research report categorizes the Commercial Aerospace Coatings market into clearly defined segments, providing a detailed analysis of emerging trends and precise revenue forecasts to support strategic decision-making.
- Coating Type
- Technology
- Application
- Material Type
- End-Use
- Finish Type
- Aircraft Part
- Durability Class
- Color Options
- Purpose
- Base Type
- Application Method
- Market Trends
Key Regional Insights Influencing Market Dynamics
Regional dynamics further shape market priorities and adoption rates. In the Americas, regulatory bodies emphasize low-VOC formulations and incentivize domestic production, driving growth in both OEM and MRO sectors across North and South America. Europe, Middle East & Africa collectively enforce strict environmental directives that accelerate water-borne and powder coatings deployment, while Gulf states invest heavily in MRO infrastructure to support expanding fleets. The Asia-Pacific region leads in volume demand, fueled by rapid fleet expansion in China and India and rising local manufacturing capacity in Southeast Asia, where strategic partnerships between global formulators and regional distributors streamline market entry.
This comprehensive research report examines key regions that drive the evolution of the Commercial Aerospace Coatings market, offering deep insights into regional trends, growth factors, and industry developments that are influencing market performance.
- Americas
- Asia-Pacific
- Europe, Middle East & Africa
Key Company Insights Defining the Competitive Ecosystem
The competitive landscape features a mix of global leaders, specialist innovators, and service-oriented providers. Akzo Nobel N.V. and BASF SE spearhead research into next-generation resin chemistries and sustainable pigment solutions, leveraging extensive R&D networks. Axalta Coating Systems LLC and The Sherwin-Williams Company command broad market share in MRO through integrated service offerings and rapid turnaround capabilities. Henkel AG & Co. KGaA has advanced radiation cure formulations, while APV Engineered Coatings focuses on solvent-free powder technologies.
Bodycote PLC and Hardide Plc differentiate via thermal spray coatings and surface engineering services that enhance wear resistance on landing gear components. Hentzen Coatings, Inc and Hohman Plating specialize in low-temperature cures and corrosion-inhibitive pretreatments for composite substrates. IHI Ionbond AG and OC Oerlikon Corporation AG invest heavily in PVD and nanostructured coatings to meet stringent military specifications. Mankiewicz Gebr. & Co. collaborates directly with aircraft manufacturers to co-develop tailored topcoat solutions, while Saint-Gobain Group offers advanced ceramic-based barrier coatings for high-heat applications.
Hentzen and Hohman’s expertise in pretreatment chemistries complements Zircotec Ltd.’s development of thermal barrier coatings for engine components, and Henkel’s adhesive primers support composite repair protocols. Together, these companies form an ecosystem that balances scale, innovation, and service excellence.
This comprehensive research report delivers an in-depth overview of the principal market players in the Commercial Aerospace Coatings market, evaluating their market share, strategic initiatives, and competitive positioning to illuminate the factors shaping the competitive landscape.
- Akzo Nobel N.V.
- APV Engineered Coatings
- Axalta Coating Systems LLC
- BASF SE
- Bodycote PLC
- Hardide Plc
- Henkel AG & Co. KGaA
- Hentzen Coatings, Inc
- Hohman Plating
- IHI Ionbond AG
- Mankiewicz Gebr. & Co.
- OC Oerlikon Corporation AG
- Saint-Gobain Group
- The Sherwin-Williams Company
- Zircotec Ltd.
Actionable Recommendations for Industry Leaders
Industry leaders must adopt a multifaceted approach to secure long-term growth. First, integrating eco-friendly chemistries and advanced materials into core product lines will satisfy regulatory mandates and position firms as sustainability champions. Second, diversifying supply chains by forging alliances with regional raw material producers will mitigate tariff risks and ensure continuity. Third, embracing digital process controls-such as AI-driven defect detection and IoT-enabled cure monitoring-will enhance quality and reduce rework costs.
Additionally, companies should pursue strategic collaboration with both OEMs and MRO operators to accelerate co-development of bespoke coating solutions, ensuring alignment with emerging aircraft architectures and maintenance practices. Investing in workforce training programs will be crucial to maximize the benefits of automated application systems and novel chemistry handling procedures. Finally, prioritizing market intelligence and regulatory scanning will enable proactive adaptation to evolving trade policies and environmental standards.
Explore AI-driven insights for the Commercial Aerospace Coatings market with ResearchAI on our online platform, providing deeper, data-backed market analysis.
Ask ResearchAI anything
World's First Innovative Al for Market Research
Conclusion: Navigating the Intersection of Innovation and Regulation
The commercial aerospace coatings market stands at a pivotal juncture where technological breakthroughs, regulatory shifts, and geopolitical factors intersect. Organizations that harness these dynamics by aligning product portfolios with sustainability targets, leveraging digitalization to optimize operations, and building resilient supply chains will secure competitive advantage. A nuanced understanding of segmentation requirements, regional priorities, and competitor strategies will empower decision-makers to allocate resources effectively and accelerate time-to-market for next-generation coatings.
This section provides a structured overview of the report, outlining key chapters and topics covered for easy reference in our Commercial Aerospace Coatings market comprehensive research report.
- Preface
- Research Methodology
- Executive Summary
- Market Overview
- Market Dynamics
- Market Insights
- Cumulative Impact of United States Tariffs 2025
- Commercial Aerospace Coatings Market, by Coating Type
- Commercial Aerospace Coatings Market, by Technology
- Commercial Aerospace Coatings Market, by Application
- Commercial Aerospace Coatings Market, by Material Type
- Commercial Aerospace Coatings Market, by End-Use
- Commercial Aerospace Coatings Market, by Finish Type
- Commercial Aerospace Coatings Market, by Aircraft Part
- Commercial Aerospace Coatings Market, by Durability Class
- Commercial Aerospace Coatings Market, by Color Options
- Commercial Aerospace Coatings Market, by Purpose
- Commercial Aerospace Coatings Market, by Base Type
- Commercial Aerospace Coatings Market, by Application Method
- Commercial Aerospace Coatings Market, by Market Trends
- Americas Commercial Aerospace Coatings Market
- Asia-Pacific Commercial Aerospace Coatings Market
- Europe, Middle East & Africa Commercial Aerospace Coatings Market
- Competitive Landscape
- ResearchAI
- ResearchStatistics
- ResearchContacts
- ResearchArticles
- Appendix
- List of Figures [Total: 42]
- List of Tables [Total: 683 ]
Call to Action: Secure Your In-Depth Market Report Today
Elevate your strategic planning with comprehensive data and expert analysis. Contact Ketan Rohom, Associate Director, Sales & Marketing, to procure the full market research report and gain unparalleled insights into commercial aerospace coatings.
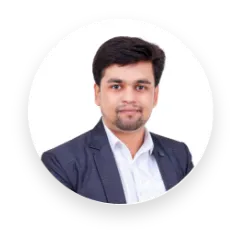
- How big is the Commercial Aerospace Coatings Market?
- What is the Commercial Aerospace Coatings Market growth?
- When do I get the report?
- In what format does this report get delivered to me?
- How long has 360iResearch been around?
- What if I have a question about your reports?
- Can I share this report with my team?
- Can I use your research in my presentation?