Introduction: Drivers Shaping the Airframe Materials Market
In today’s competitive aerospace environment, selection of airframe materials directly influences aircraft performance, lifecycle costs, and environmental footprint. As carriers prioritize fuel efficiency and sustainability, demand for lightweight, high-strength solutions has intensified, challenging traditional aluminum alloys and opening the door for advanced composites and novel metal formulations. At the same time, stringent regulatory standards and certification processes drive material innovation, while digital engineering tools accelerate design optimization. Geopolitical shifts and supply chain disruptions further underscore the need for resilient sourcing strategies.
This executive summary distills the latest insights into the commercial aircraft airframe materials landscape, highlighting emerging trends, regulatory dynamics, and strategic imperatives. It integrates analysis across material types, applications, aircraft segments, and end-user channels, while examining the impact of evolving trade measures and regional growth patterns. By contextualizing these factors, decision-makers can align investments, innovate resilient product portfolios, and anticipate market shifts.
Simultaneously, the aftermarket and MRO sectors are driving interest in materials that enhance durability, reparability, and recyclability, supporting life-extension strategies and circular economy objectives. Partnerships among OEMs, suppliers, and technology developers are accelerating breakthroughs in alloy design, composite resin formulations, and powder metallurgy, propelling the industry toward more efficient production and enhanced supply chain visibility.
Transformative Shifts Redefining Airframe Material Strategies
Over the past decade, advanced composites have shifted from fringe applications to mainstream airframe construction, driven by their superior strength-to-weight ratio and fatigue resistance. Parallel advances in additive manufacturing have enabled rapid prototyping of complex geometries and localized repair of critical structural components. Digital twins and simulation platforms now allow real-time monitoring of material behavior under operational loads, accelerating design iterations and improving safety margins. At the same time, next-generation aluminum-lithium alloys and high-performance titanium formulations are expanding capabilities for sections where metal remains essential.
Environmental stewardship and regulatory pressures have catalyzed the adoption of sustainable material solutions that reduce carbon emissions throughout the product lifecycle. Bio-based resin systems, recyclable thermoplastic composites, and novel surface treatments minimize waste and facilitate end-of-life recovery. Stringent certification requirements from agencies worldwide are harmonizing safety standards, yet also raising the bar for material qualification, forcing suppliers to invest in testing infrastructure and cross-border technology validation.
Furthermore, the pursuit of supply chain resilience has intensified collaboration between OEMs and specialty material providers, resulting in joint ventures and co-development agreements. Blockchain-enabled traceability and digital supply networks improve transparency, while onshoring initiatives and strategic stockpiling mitigate risks associated with global disruptions. These transformative shifts are redefining competitive dynamics and reshaping the roadmap for future airframe material integration.
Cumulative Impact of US Tariffs 2025 on Airframe Materials
With the advent of new tariff measures set to take effect in 2025, the airframe materials sector is preparing for significant cost and supply chain realignments. These tariffs target key raw materials and semi-finished components, including certain high-strength aluminum alloys and advanced composite preforms. As a result, domestic manufacturers face elevated input costs, while import-dependent suppliers must reassess sourcing strategies to preserve margin structures and maintain technical compliance.
In response, industry players are exploring diversification of procurement channels by forging partnerships with alternative suppliers across Asia-Pacific and Europe. Strategic nearshoring initiatives are gaining traction, as firms seek to balance tariff liabilities against logistical efficiencies. Simultaneously, vertical integration models are resurfacing, with some OEMs and tier-1 contractors investing in in-house material processing capabilities to reduce exposure to external trade shocks.
Despite these headwinds, tariff-induced price adjustments are catalyzing innovation in material substitution and process optimization. Research efforts into alloy and resin chemistries that circumvent tariff classifications are underway, while lean manufacturing and scrap reduction programs lower overall cost structures. Moreover, long-term contracts and hedging mechanisms are being renegotiated to secure stable relationships and predictable pricing. These cumulative impacts underscore the necessity for agile supply chain governance and proactive policy engagement to safeguard competitiveness in the 2025 landscape.
Key Segmentation Insights by Material, Application, Aircraft Type, and End User
Analysis of material types reveals that traditional alloys retain a dominant role due to their proven performance, cost-effectiveness, and established manufacturing bases, yet composites are rapidly gaining share as weight reduction imperatives intensify. Metals, including titanium and specialty steels, continue to support high-load structural applications and engine interfaces, benefiting from refinements in powder metallurgy and surface treatment technologies.
Application-based insights indicate that wings and fuselage structures remain the primary battlegrounds for material innovation, driven by the need to improve aerodynamic efficiency and load distribution. Engine components demand the highest thermal and fatigue resistance, prompting close collaboration between alloy specialists and propulsion integrators. Empennage assemblies, though smaller in volume, require precision materials with exceptional stiffness-to-weight ratios to ensure stability and control responsiveness.
Within aircraft types, commercial aircraft platforms absorb the majority of advanced materials demand owing to large fleet expansions and retrofit programs, while military aircraft continue to push the envelope with bespoke formulations and life-extension initiatives. Private and recreational segments exhibit growing adoption of lightweight composites to enhance performance and reduce ownership costs. From an end-user perspective, OEM sourcing drives initial material specification and qualification, whereas aftermarket channels prioritize repairability, modular upgrades, and cost-efficient component replacement.
The interplay among these segmentation dimensions shapes supplier strategies: composite resin developers tailor formulations to wing and fuselage applications, while alloy producers optimize chemistries for engine and structural integration. Aftermarket specialists increasingly focus on repair-friendly material variants and streamlined certification pathways that align with OEM specifications, ensuring seamless maintenance cycles and minimizing aircraft downtime.
This comprehensive research report categorizes the Commercial Aircraft Airframe Materials market into clearly defined segments, providing a detailed analysis of emerging trends and precise revenue forecasts to support strategic decision-making.
- Material Type
- Application
- Aircraft Type
- End User
Key Regional Insights Across Americas, EMEA, and Asia-Pacific
North America remains a key hub for raw material extraction, primary processing, and advanced alloy development, underpinned by the presence of leading aluminum and titanium producers. OEMs headquartered in the region benefit from robust R&D ecosystems and a mature MRO infrastructure that supports aftermarket innovation. Government incentives for domestic manufacturing and defense contracts further reinforce local material supply chains, fostering resilience against external shocks.
Europe, Middle East, and Africa boast a diverse manufacturing landscape anchored by flagship OEM and tier-1 operations across the United Kingdom, Germany, and France. European composites research institutes and chemical processing centers drive breakthroughs in carbon-fiber resins and hybrid materials. Middle Eastern investment in aerospace hubs and free zones is catalyzing production partnerships, while Africa’s emerging metal processing capabilities present opportunities for niche alloy supply and scrap recycling initiatives.
Asia-Pacific is experiencing the fastest expansion in commercial aircraft fleets, fueling demand for indigenous airframe material capabilities. China, Japan, and South Korea are scaling up composite manufacturing facilities, while India is investing heavily in specialty metals and certification infrastructure. Strategic government-led programs prioritize technology transfer and joint ventures with global suppliers, accelerating local competency across material science, quality assurance, and industry standards compliance.
This comprehensive research report examines key regions that drive the evolution of the Commercial Aircraft Airframe Materials market, offering deep insights into regional trends, growth factors, and industry developments that are influencing market performance.
- Americas
- Asia-Pacific
- Europe, Middle East & Africa
Key Company Insights and Strategic Positioning in Airframe Materials
Leading simulation and digital prototyping provider Akselos S.A. is enabling predictive maintenance workflows, while Alcoa Corporation leverages its integrated mining-to-production footprint for high-strength aluminum alloys. Aleris and Arconic Corporation focus on bespoke extruded profiles, integrating novel alloy chemistries to meet fatigue resistance requirements. ATI Inc. and Constellium N.V. advance specialty alloy portfolios for engine interfaces, demonstrating strong technical credentials. Cytec Solvay Group and DuPont de Nemours, Inc. drive resin system innovation across thermoset and thermoplastic composites.
GKN Aerospace and Hexcel Corporation expand composite manufacturing capacities through automated fiber placement and out-of-autoclave curing, improving throughput and cost efficiency. Hexpol Compounding supplies specialized polymer blends that enhance pultruded composite elements, while Hindalco Industries Limited and Kaiser Aluminum provide competitively priced aluminum products across OEM and aftermarket channels. Materion Corporation supports niche structural applications with beryllium and intermetallic solutions, and Mitsubishi Chemical Corporation invests in carbon fiber precursor technologies.
SGL Carbon SE and Solvay S.A. broaden material portfolios via strategic acquisitions and joint development agreements targeting high-temperature composites. Teijin Limited and Toray Industries, Inc. maintain leadership in carbon fiber and laminates, offering solutions from fiber production to finished prepregs. Lastly, Triumph Group, Inc. integrates airframe substructures, combining material expertise with downstream fabrication to streamline supplier networks and reduce assembly complexity.
Collectively, these companies span the full value chain from raw material processing to structural integration, underscoring the critical role of collaborative innovation and vertical integration in advancing the commercial airframe materials market.
This comprehensive research report delivers an in-depth overview of the principal market players in the Commercial Aircraft Airframe Materials market, evaluating their market share, strategic initiatives, and competitive positioning to illuminate the factors shaping the competitive landscape.
- Akselos S.A.
- Alcoa Corporation
- Aleris
- Arconic Corporation
- ATI Inc.
- Constellium N.V.
- Cytec Solvay Group
- DuPont de Nemours, Inc.
- GKN Aerospace
- Hexcel Corporation
- Hexpol Compounding
- Hindalco Industries Limited
- Kaiser Aluminum
- Materion Corporation
- Mitsubishi Chemical Corporation
- SGL Carbon SE
- Solvay S.A.
- Teijin Limited
- Toray Industries, Inc.
- Triumph Group, Inc.
Actionable Recommendations for Industry Leaders
-
Diversify raw material procurement by establishing strategic partnerships across multiple regions, securing long-term supply agreements, and leveraging dual-sourcing models to mitigate exposure to tariffs, geopolitical tensions, and logistical disruptions.
-
Accelerate qualification and certification processes for next-generation composites and advanced alloys by co-investing in shared test laboratories, sponsoring cross-company pilot projects, and fostering regulatory collaboration to reduce time-to-market.
-
Invest in digital supply chain platforms that leverage blockchain, IoT, and predictive analytics to enhance traceability, forecast potential supply disruptions, optimize inventory levels, and improve responsiveness to shifting demand patterns.
-
Expand local production and nearshore processing capabilities for high-volume aluminum-lithium alloys, titanium components, and composite preforms to shorten lead times, lower transportation costs, and enhance resilience against international trade uncertainties.
-
Drive sustainability by integrating recyclable thermoplastic composites, bio-based resin systems, and closed-loop recycling programs into material development, product design, and aftermarket services to meet emerging environmental regulations and customer expectations.
-
Strengthen policy engagement by collaborating with industry associations, certification bodies, and government agencies to shape trade regulations, harmonize certification standards, and secure R&D incentives that align with long-term competitiveness.
-
Foster cross-functional integration within organizations by aligning R&D, procurement, and operations teams to accelerate materials innovation and streamline qualification-to-production workflows.
Explore AI-driven insights for the Commercial Aircraft Airframe Materials market with ResearchAI on our online platform, providing deeper, data-backed market analysis.
Ask ResearchAI anything
World's First Innovative Al for Market Research
Conclusion: Navigating the Future of Airframe Materials
In summary, the commercial aircraft airframe materials landscape is undergoing rapid evolution driven by the dual imperatives of performance enhancement and environmental responsibility. Advanced composites, next-generation alloys, and innovative manufacturing techniques are converging to deliver structures that are lighter, stronger, and more sustainable. Stakeholders must stay attuned to regulatory changes, trade dynamics, and certification requirements to maintain competitive advantage.
As the industry grapples with cost pressures, tariff-driven disruptions, and ambitious sustainability targets, strategic collaboration and supply chain agility will be paramount. By leveraging digital tools, co-development frameworks, and localized production strategies, manufacturers and suppliers can mitigate risk while accelerating material innovation.
By synthesizing material, application, regional, and company insights, decision-makers are equipped to optimize supply chains, foster resilient partnerships, and drive scalable adoption of high-performance materials. This holistic perspective will enable the aerospace community to confidently navigate the challenges and opportunities that lie ahead.
This section provides a structured overview of the report, outlining key chapters and topics covered for easy reference in our Commercial Aircraft Airframe Materials market comprehensive research report.
- Preface
- Research Methodology
- Executive Summary
- Market Overview
- Market Dynamics
- Market Insights
- Cumulative Impact of United States Tariffs 2025
- Commercial Aircraft Airframe Materials Market, by Material Type
- Commercial Aircraft Airframe Materials Market, by Application
- Commercial Aircraft Airframe Materials Market, by Aircraft Type
- Commercial Aircraft Airframe Materials Market, by End User
- Americas Commercial Aircraft Airframe Materials Market
- Asia-Pacific Commercial Aircraft Airframe Materials Market
- Europe, Middle East & Africa Commercial Aircraft Airframe Materials Market
- Competitive Landscape
- ResearchAI
- ResearchStatistics
- ResearchContacts
- ResearchArticles
- Appendix
- List of Figures [Total: 24]
- List of Tables [Total: 191 ]
Next Steps: Secure Your Comprehensive Market Analysis
For deeper insights and tailored briefings, contact Ketan Rohom, Associate Director, Sales & Marketing. Secure your copy of the full market research report and leverage detailed data, strategic frameworks, and expert analysis to inform investments and innovation in commercial aircraft airframe materials.
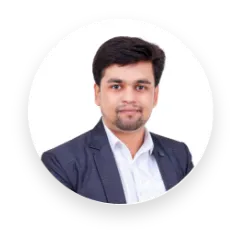
- When do I get the report?
- In what format does this report get delivered to me?
- How long has 360iResearch been around?
- What if I have a question about your reports?
- Can I share this report with my team?
- Can I use your research in my presentation?