Introduction to the Commercial Aircraft Engine Forging Market
The commercial aircraft engine forging sector plays a pivotal role in ensuring the structural integrity, performance and safety of modern aviation propulsion systems. As global air travel continues to expand, demand for robust and reliable engine components intensifies, driving innovation in materials and processes. Forged parts such as discs, shafts and rings serve as critical load-bearing elements capable of withstanding extreme temperatures and stresses. Together with evolving regulatory requirements and sustainability mandates, these factors underscore the strategic importance of forging as a core manufacturing discipline.
This report introduces the current state of the market, outlines recent technological advancements and frames the competitive environment. Beginning with an overview of key drivers and constraints, it then explores how emerging technologies and shifting trade policies are reshaping supply chains and production strategies. By presenting a structured analysis of segmentation, regional dynamics and competitive positioning, this executive summary equips decision-makers with the insights needed to navigate complexities and capitalize on growth opportunities.
Transformative Shifts Reshaping the Industry
Over the past five years, the landscape of engine forging has undergone transformative shifts driven by digitalization, material science breakthroughs and heightened sustainability expectations. Additive manufacturing integration within forging workflows now enables near-net-shape blank production, reducing scrap and downstream machining steps. At the same time, the rise of smart forging techniques-powered by real-time process monitoring sensors and data analytics-has enhanced quality control and accelerated cycle times.
Moreover, shifts in global supply chains have prompted manufacturers to reconsider sourcing strategies. Nearshoring initiatives in Western economies aim to secure critical raw materials and mitigate disruptions. Concurrently, strategic partnerships between forging houses and OEMs are evolving to include joint R&D programs focused on high-temperature alloys. As the industry transitions to these new paradigms, it must balance innovation with cost-efficiency while maintaining the extreme reliability standards that commercial aviation demands.
Analyzing the 2025 US Tariff Impact on Forging
The cumulative impact of the United States’ 2025 tariff adjustments has reverberated throughout the forging ecosystem. Import duties on key alloy ingots drove raw material costs upward, prompting mills to pass through at least 10–15% of the increase in production charges. In response, some domestic forgers have accelerated investments in in-house melting capabilities to insulate operations from volatile global metal prices.
Meanwhile, affected Tier-One suppliers have pursued dual-sourcing strategies, leveraging European and Asia-Pacific forging hubs to maintain continuity for commercial airliner programs. Logistical realignments include longer-term contracts with freight carriers to absorb potential future tariff escalations. Despite the short-term cost pressures, these shifts have catalyzed supply-chain resilience, as stakeholders diversify their footprint and establish secured pipelines for critical forging inputs.
In-Depth Segmentation Insights
A granular examination of industry segmentation reveals nuanced performance across multiple axes. In terms of material, nickel-based superalloys retain supremacy for turbine disks and blades due to their exceptional high-temperature strength, whereas titanium alloys are increasingly favored where weight reduction is paramount. Aluminum alloys and stainless steel continue to occupy niches in non-critical structural components, offering cost-effective solutions when thermal loads permit.
By application area, commercial airliners command the largest share, driven by sustained fleet expansions among global carriers. Regional jets and business aircraft follow closely, their operators seeking fuel-efficient engines with rapid turnarounds. Military aircraft demand the highest material specifications and traceability, often involving tiered qualification programs, while cargo aircraft focus on durability for heavy-lift operations.
End-user belts exhibit distinct purchasing behaviors: original equipment manufacturers prioritize long-lead, stable supply contracts; Tier-One suppliers emphasize technical collaboration on novel forging processes; and MRO providers capitalize on aftermarket repair services, where seamless rolled ring forgings meet urgent turnaround timelines.
Engine type segmentation aligns closely with application demands. Turbofan engines dominate commercial fleets thanks to their high bypass ratios and efficiency, while turboprop engines retain relevance for short-haul regional routes. Turbojet engines find limited use in niche defense applications, whereas rotary piston engines appear primarily in emerging urban air mobility concepts.
Manufacturing processes also vary: closed die forging is preferred for intricate shapes such as blades and pans, providing superior dimensional precision. Open die forging excels for large, high-volume rings and shafts, where flexibility outweighs tooling complexity. Seamless rolled ring forging bridges these approaches, producing uniform rings with minimal machining allowance.
Component-type insights highlight blades and discs as the volume leaders, reflecting their central role in power generation. Pans, rings and shafts, while lower in unit count, contribute significantly to total forging tonnage due to their mass and dimensional demands.
Forging technology adoption ranges from traditional hot forging, which remains the backbone for superalloy parts, to cold forging for high-strength steel components. Near-net-shape and precision forging techniques have gained traction as they reduce waste and machining costs while maintaining tight tolerances.
Functional segmentation underscores the criticality of high-temperature bearings and sealing systems within combustion environments. These elements demand both material innovation and process control to ensure leak-free performance under cyclic loading.
Performance characteristics such as corrosion resistance and thermal resistance continue to influence alloy selection, especially for build-to-print replacement parts. Durability and lightweight attributes form a delicate balance, with lightweight wrought alloys tailored to deliver performance without compromising safety margins.
Service-type analysis indicates that maintenance services and repair/retrofit operations provide recurring revenue streams for specialized forgers. New installation orders, while less frequent, anchor long-term OEM partnerships and large-scale capacity planning.
Engine configuration segmentation further refines demand patterns: multi-shaft and mixed-shaft configurations, common in high-bypass turbofans, require multiple forging variants, whereas single-shaft designs streamline part counts and simplify supply chains.
Finally, emerging technology adoption highlights a clear trend toward smart forging techniques and integration of IoT in manufacturing. Additive manufacturing is being piloted for tooling and blanks, accelerating development cycles and enabling complex geometries that were previously impractical.
This comprehensive research report categorizes the Commercial Aircraft Engine Forging market into clearly defined segments, providing a detailed analysis of emerging trends and precise revenue forecasts to support strategic decision-making.
- Type of Material
- Application Area
- End-User Belts
- Engine Type
- Manufacturing Process
- Component Type
- Forging Technology
- Functional Segmentation
- Performance Characteristics
- Service Type
- Engine Configuration
- Emerging Technology Adoption
Key Regional Performance Highlights
Regional dynamics play a pivotal role in shaping forging strategies and investment decisions. In the Americas, robust defense budgets and a resurgence of nearshoring initiatives have driven new forging capacity additions in the United States and Canada. The push for domestic supply resilience has also unlocked federal incentives for advanced manufacturing.
The Europe, Middle East & Africa region remains anchored by established aerospace hubs in France, Germany and the United Kingdom. OEMs and forgers here navigate stringent environmental regulations while leveraging deep technical expertise. Growth in the Middle East is supported by ambitious fleet expansions among regional carriers, creating demand for localized MRO and forging services.
Asia-Pacific registers the most rapid fleet growth, particularly in China and India. Regional forgers have scaled up capacity to meet surging demand for single-aisle airliners. Cost-competitiveness drives partnerships between local players and global forging leaders, while government-backed initiatives fund research into advanced alloy development and process automation.
This comprehensive research report examines key regions that drive the evolution of the Commercial Aircraft Engine Forging market, offering deep insights into regional trends, growth factors, and industry developments that are influencing market performance.
- Americas
- Asia-Pacific
- Europe, Middle East & Africa
Competitive Landscape and Company Analysis
The competitive terrain encompasses a diverse mix of legacy forging giants and specialized technology providers. Alcoa Corporation leads in aluminum alloy expertise, with a track record of supplying lightweight components to major engine OEMs. Arconic Inc. builds on its extensive portfolio of high-temperature alloys and closed die forging capabilities, targeting both commercial and military platforms.
Within Europe, Aubert & Duval distinguishes itself through advanced superalloy processing for turbine disks. Doncasters Group Ltd. capitalizes on seamless rolled ring and open die operations to serve both airframe and engine markets. Rolls-Royce Holdings plc, while primarily an engine OEM, maintains in-house forging capabilities for strategic components, reducing lead times and ensuring quality control.
In North America, Precision Castparts Corp. and Wyman-Gordon remain pillars of the forging community, offering a broad range of forging technologies from hot die to precision forging. Honeywell Aerospace focuses on aftermarket and service-type contracts, while Pratt & Whitney leverages its OEM status to foster collaborative R&D with forging partners.
Asia-based forgers such as Kawasaki Heavy Industries, Ltd. and IHI Corporation have expanded downstream into integrated forging and engine assembly operations. MTU Aero Engines AG in Germany invests heavily in near-net-shape forging innovations, while Safran Aircraft Engines advances in-house ring forging to support its propulsion systems.
Emerging players like Alp Aviation and Fountaintown Forgings Inc. carve out niches in specialty alloys and MRO-focused parts respectively. GKN Aerospace maintains a global footprint with seamless integration across forging, finishing and assembly stages. Haynes International, Inc. and Schmolz + Bickenbach provide critical superalloy and steel alloy inputs, supporting both captive forgers and contract houses.
This comprehensive research report delivers an in-depth overview of the principal market players in the Commercial Aircraft Engine Forging market, evaluating their market share, strategic initiatives, and competitive positioning to illuminate the factors shaping the competitive landscape.
- Alcoa Corporation
- Alp Aviation
- Arconic Inc.
- Aubert & Duval
- Doncasters Group Ltd.
- Fountaintown Forgings Inc.
- GE Aviation
- GKN Aerospace
- Haynes International, Inc.
- Honeywell Aerospace
- IHI Corporation
- Kawasaki Heavy Industries, Ltd.
- LISI Aerospace
- MTU Aero Engines AG
- Pratt & Whitney
- Precision Castparts Corp.
- Rolls-Royce Holdings plc
- Safran Aircraft Engines
- Schmolz + Bickenbach
- Wyman-Gordon
Actionable Recommendations for Industry Leaders
Industry leaders should prioritize several strategic initiatives to secure long-term resilience and growth. First, accelerating the deployment of smart forging technologies-such as connected sensors and digital twins-will unlock further efficiencies and reduce defect rates. Equally important is diversifying alloy portfolios to include next-generation materials that address sustainability and performance demands.
Supply-chain resilience must remain a top priority. Establishing dual-sourcing agreements across multiple regions, combined with strategic raw-material stockpiling, will mitigate future tariff disruptions and logistics bottlenecks. Concurrently, forging houses should deepen partnerships with OEMs and Tier-One suppliers by co-investing in process development programs.
Investing in workforce upskilling is vital. As forging becomes more digitized, operators and engineers will require training in data analytics, automation and advanced quality-control techniques. Launching joint training initiatives with academic institutions can build a pipeline of skilled talent.
Finally, pursuing targeted mergers and acquisitions can enhance scale, broaden geographical reach and integrate complementary technologies. This approach will position organizations to capitalize on the expanding aftermarket and emerging urban air mobility segments.
Explore AI-driven insights for the Commercial Aircraft Engine Forging market with ResearchAI on our online platform, providing deeper, data-backed market analysis.
Ask ResearchAI anything
World's First Innovative Al for Market Research
Conclusion and Strategic Imperatives
In summary, the commercial aircraft engine forging market stands at the confluence of technological innovation, trade-policy shifts and evolving aerospace demand patterns. Advanced superalloys and smart forging techniques are redefining production paradigms, while regional and company-level dynamics underscore the importance of agile strategies. A thorough understanding of segmentation insights, coupled with proactive supply-chain management and investment in emerging capabilities, will differentiate winners in this competitive environment.
This section provides a structured overview of the report, outlining key chapters and topics covered for easy reference in our Commercial Aircraft Engine Forging market comprehensive research report.
- Preface
- Research Methodology
- Executive Summary
- Market Overview
- Market Dynamics
- Market Insights
- Cumulative Impact of United States Tariffs 2025
- Commercial Aircraft Engine Forging Market, by Type of Material
- Commercial Aircraft Engine Forging Market, by Application Area
- Commercial Aircraft Engine Forging Market, by End-User Belts
- Commercial Aircraft Engine Forging Market, by Engine Type
- Commercial Aircraft Engine Forging Market, by Manufacturing Process
- Commercial Aircraft Engine Forging Market, by Component Type
- Commercial Aircraft Engine Forging Market, by Forging Technology
- Commercial Aircraft Engine Forging Market, by Functional Segmentation
- Commercial Aircraft Engine Forging Market, by Performance Characteristics
- Commercial Aircraft Engine Forging Market, by Service Type
- Commercial Aircraft Engine Forging Market, by Engine Configuration
- Commercial Aircraft Engine Forging Market, by Emerging Technology Adoption
- Americas Commercial Aircraft Engine Forging Market
- Asia-Pacific Commercial Aircraft Engine Forging Market
- Europe, Middle East & Africa Commercial Aircraft Engine Forging Market
- Competitive Landscape
- ResearchAI
- ResearchStatistics
- ResearchContacts
- ResearchArticles
- Appendix
- List of Figures [Total: 40]
- List of Tables [Total: 559 ]
Call to Action: Engage with Ketan Rohom for the Full Report
To explore the full breadth of analysis and actionable insights contained within the complete market research report, please reach out to Ketan Rohom, Associate Director, Sales & Marketing. He can guide you through tailored solutions and provide immediate access to data-driven recommendations for optimizing your forging operations.
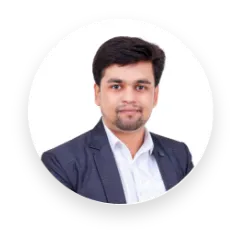
- When do I get the report?
- In what format does this report get delivered to me?
- How long has 360iResearch been around?
- What if I have a question about your reports?
- Can I share this report with my team?
- Can I use your research in my presentation?