Introduction to Composite Materials Shaping Oil & Gas Operations
Composites have become indispensable in modern oil and gas operations, offering superior strength-to-weight ratios, corrosion resistance, and durability under extreme conditions. By combining fibers and resins, these advanced materials reduce maintenance requirements for pipelines exposed to high-pressure subsea environments and storage tanks operating under corrosive atmospheres. As project economics tighten and regulatory scrutiny intensifies, industry leaders are turning to composites to extend asset life, lower total cost of ownership, and improve safety performance.
This summary presents a concise analysis of the composite materials landscape within oil and gas. It explores the transformative technological shifts redefining material selection and manufacturing, assesses the cumulative impact of the United States’ 2025 tariff regime on global supply chains, and highlights granular segmentation insights across material types, applications, product categories, end-user sectors, process technologies, operating environments, and innovation platforms. Furthermore, it delivers regional perspectives and profiles of leading industry participants. Finally, it offers actionable recommendations designed to help decision-makers capitalize on emerging opportunities and mitigate evolving challenges.
By synthesizing these core themes, this executive overview equips stakeholders with the essential intelligence required to guide strategic planning, investment decisions, and operational excellence in a rapidly evolving landscape.
Transformative Shifts Redefining Composite Adoption in Oil & Gas
The composite materials sector is undergoing significant evolution driven by Industry 4.0 integration, advanced material science breakthroughs, and sustainability imperatives. Manufacturers are embedding sensors into pipe liners to enable real-time condition monitoring, while self-healing matrices extend component life by automatically sealing micro-fractures. Nanocomposite platforms, leveraging carbon nanotube enhancements and graphene additives, are elevating mechanical and thermal performance to meet more demanding subsea and high-pressure service conditions.
Simultaneously, production processes are transitioning towards digitalized tooling, with automated filament winding systems and resin transfer molding presses equipped with predictive maintenance analytics. These process improvements not only increase throughput but also improve reproducibility and quality control. The emphasis on lightweight, recyclable thermoplastic composites such as polyetheretherketone (PEEK) and polyphenylene sulfide (PPS) is growing, driven by pressure to reduce carbon footprints and simplify end-of-life recovery. Collaboration between fiber producers, resin formulators, and oilfield service companies accelerates product qualification cycles, enabling faster deployment in drilling, transportation, and storage applications.
Collectively, these technological shifts are creating a dynamic environment in which agility, cross-industry partnerships, and continuous innovation will determine leadership in the composite-driven transformation of oil and gas infrastructure.
Cumulative Impact of United States Tariffs Effective in 2025
The implementation of new U.S. tariffs on composite imports in 2025 has disrupted established supply chains and reshaped competitive dynamics. Tariffs imposed on specialized thermoplastic composites and advanced fiber reinforcements from key exporting regions have elevated input costs for domestic manufacturers. The additional duties on resin formulations, particularly epoxy, polyester, and vinyl ester grades, have prompted producers to reassess sourcing strategies and pursue greater vertical integration.
For materials based on polyamide (PA), PEEK and PPS that previously relied on European and Asian supply, the tariff burden has accelerated investment in local production capacities. In the fiber segment, higher levies on aramid, carbon and glass fibers have led oilfield service providers to forge strategic alliances with North American fiber mills. Meanwhile, resin transfer molding and prepreg fabricators are exploring alternative additive packages to offset cost impacts without compromising performance.
These policy shifts have also incentivized midstream operators to adopt composite-lined pipelines and storage tank solutions manufactured domestically, reducing exposure to tariff volatility. While they introduce near-term pricing pressures, the tariffs are catalyzing an expanded domestic ecosystem capable of meeting rigorous operating environment demands under corrosive, high-pressure, and high-temperature conditions.
Key Segmentation Insights Across Material, Application and End-Use Profiles
Analysis by material type reveals that thermoplastic composites are driving innovation through polyamide systems for chemical resistance, PEEK for high-temperature performance and PPS for cost-effective durability, while thermoset composites remain indispensable in structural and insulation coatings. In application, composite solutions for cables and umbilicals enable lightweight deepwater deployment, grids and networks integrate composite supports in freeze-resistant platforms, pipelines benefit from corrosion-resistant linings both offshore-deepwater and shallow water-and onshore, and storage solutions span above ground and underground tanks with enhanced integrity.
When examining product categories, additives tailor matrix properties to specific service conditions, fibers deliver reinforcement via aramid, carbon or glass constituents, prepreg systems offer process efficiencies, and resins from epoxy, polyester and vinyl ester portfolios are calibrated to meet strength and chemical compatibility requirements. From an end-user perspective, upstream exploration and drilling operations leverage lighter drilling risers, midstream storage and transportation infrastructures adopt composite-insulated pipes, and downstream refining and processing units integrate corrosion-resistant components to extend equipment lifecycles.
Process technologies such as compression molding, filament winding, pultrusion and resin transfer molding enable cost-efficient production geometries and structural consistency, while operating environments characterized by high pressures, elevated temperatures and corrosive agents validate the use of these composite configurations. Finally, the surge in nanocomposites-reinforced with carbon nanotube enhancements and graphene additives-and smart composites equipped with embedded sensors and self-healing functionalities underscores a transition toward self-monitoring and adaptive asset platforms.
This comprehensive research report categorizes the Composites for the Oil & Gas Industry market into clearly defined segments, providing a detailed analysis of emerging trends and precise revenue forecasts to support strategic decision-making.
- Material Type
- Application
- Product
- End-User
- Process Technology
- Operating Environment
- Innovation and Advancements
Key Regional Insights Shaping Market Dynamics
In the Americas, robust upstream drilling activity and extensive pipeline networks have generated sustained demand for composite materials optimized for high-pressure subsea and CO₂ injection services. Local resin and fiber production hubs intensified capital investments to mitigate the impact of import tariffs and secure domestic supply chains. Meanwhile, regulatory frameworks encouraging infrastructure resilience have accelerated retrofitting projects across refining and transportation.
In Europe, Middle East & Africa, stringent environmental standards and aging North Sea installations have propelled adoption of corrosion-resistant solutions. The region’s focus on renewable energy integration and carbon capture has increased interest in smart composites with embedded sensors. Gulf Cooperation Council nations continue to channel investment into LNG and petrochemical storage facilities requiring composite-lined tanks to ensure leak-proof integrity under variable temperature cycles.
Asia-Pacific remains one of the fastest-growing markets, driven by large-scale refinery expansions in India and China’s push for import substitution in high-performance composites. Local conglomerates are enhancing manufacturing capabilities for thermoplastic matrices and pultruded tubing, while offshore exploration projects in Australia demand deepwater-compatible materials. Government-led initiatives targeting advanced materials research further bolster regional innovation capacity.
This comprehensive research report examines key regions that drive the evolution of the Composites for the Oil & Gas Industry market, offering deep insights into regional trends, growth factors, and industry developments that are influencing market performance.
- Americas
- Asia-Pacific
- Europe, Middle East & Africa
Key Companies Delivering Composite Solutions
Ashland Global Holdings Inc. is advancing resin chemistry with specialized epoxy and vinyl ester formulations, and Baker Hughes Company integrates digital drilling systems with composite riser technologies. Chevron Phillips Chemical Company LLC leverages its polymer expertise to supply PEEK and PPS resins for downhole tools, while ExxonMobil Corporation focuses on high-performance thermoplastic composites for high-temperature and pressure-critical applications. Magnum Composites LLC designs lightweight tubulars reinforced with carbon fiber for unconventional wells, and NOV Inc. expands its equipment portfolio through automated filament winding and pultrusion cells.
Schlumberger Limited enhances real-time monitoring capabilities by embedding sensor networks into composite casings, and Strongwell Corporation’s pultruded structural members support offshore platform modifications. TMP Technologies Inc. streamlines resin transfer molding operations with advanced mold controls, and ZCL Composites Inc. specializes in composite-lined storage tanks that resist chemical attack and thermal cycling. Together, these leaders are jointly shaping supply chain resilience, elevating performance standards, and accelerating time-to-market for next-generation composite solutions.
This comprehensive research report delivers an in-depth overview of the principal market players in the Composites for the Oil & Gas Industry market, evaluating their market share, strategic initiatives, and competitive positioning to illuminate the factors shaping the competitive landscape.
- Ashland Global Holdings Inc.
- Baker Hughes Company
- Chevron Phillips Chemical Company LLC
- ExxonMobil Corporation
- Magnum Composites LLC
- NOV Inc.
- Schlumberger Limited
- Strongwell Corporation
- TMP Technologies Inc.
- ZCL Composites Inc.
Actionable Recommendations for Industry Leaders
To maintain competitive advantage, organizations should prioritize research into nanocomposite and smart composite platforms, ensuring their portfolios include carbon nanotube and graphene-reinforced matrices alongside embedded sensor systems. Executives must evaluate supply chain vulnerability by mapping critical resin and fiber dependencies and establishing alternative sources through joint ventures or local partnerships. Diversifying material selection to blend thermoplastic and thermoset composites can optimize weight, cost, and environmental resistance across varying operating scenarios.
Investments in digital manufacturing technologies-such as automated filament winding, pultrusion lines and resin transfer molding systems with closed-loop quality controls-will enhance throughput and reduce scrap rates. Engagement in industry consortia to influence standardization of self-healing specifications and sensor interoperability will facilitate broader market adoption. Workforce development programs must be implemented to cultivate expertise in composite design, process engineering and data analytics.
Finally, sustainability objectives should guide material innovation toward recyclable and bio-based resin systems, aligning with global carbon reduction targets. Strategic mergers, acquisitions or collaborative R&D agreements can secure access to proprietary technologies, accelerating time-to-market and reinforcing leadership positions in the evolving composite landscape.
Explore AI-driven insights for the Composites for the Oil & Gas Industry market with ResearchAI on our online platform, providing deeper, data-backed market analysis.
Ask ResearchAI anything
World's First Innovative Al for Market Research
Conclusion: Seizing the Composite Advantage
As the oil and gas sector contends with tighter regulations, aging infrastructure and evolving energy demands, composites offer a transformative pathway to enhance asset performance and operational reliability. Technological advances in nanocomposites, smart materials and digital manufacturing are redefining application boundaries, while the 2025 U.S. tariff environment has stimulated domestic capability expansion. Granular segmentation insights reveal opportunity pockets across material types, application areas, product categories and process technologies, and regional analysis highlights where investment and innovation are concentrated.
Leading companies are already aligning resin chemistries, fiber reinforcements and sensor integration to deliver customized composite solutions for upstream, midstream and downstream challenges. By embracing strategic recommendations-spanning R&D prioritization, supply chain diversification, digitalization and sustainability-industry leaders can capitalize on emerging trends and mitigate policy-driven disruptions. This consolidated intelligence equips decision-makers to navigate the transition toward a resilient, composite-enabled oil and gas infrastructure.
This section provides a structured overview of the report, outlining key chapters and topics covered for easy reference in our Composites for the Oil & Gas Industry market comprehensive research report.
- Preface
- Research Methodology
- Executive Summary
- Market Overview
- Market Dynamics
- Market Insights
- Cumulative Impact of United States Tariffs 2025
- Composites for the Oil & Gas Industry Market, by Material Type
- Composites for the Oil & Gas Industry Market, by Application
- Composites for the Oil & Gas Industry Market, by Product
- Composites for the Oil & Gas Industry Market, by End-User
- Composites for the Oil & Gas Industry Market, by Process Technology
- Composites for the Oil & Gas Industry Market, by Operating Environment
- Composites for the Oil & Gas Industry Market, by Innovation and Advancements
- Americas Composites for the Oil & Gas Industry Market
- Asia-Pacific Composites for the Oil & Gas Industry Market
- Europe, Middle East & Africa Composites for the Oil & Gas Industry Market
- Competitive Landscape
- ResearchAI
- ResearchStatistics
- ResearchContacts
- ResearchArticles
- Appendix
- List of Figures [Total: 30]
- List of Tables [Total: 814 ]
Contact Ketan Rohom to Secure Your Comprehensive Market Analysis
To access the full report detailing in-depth market segmentation, regional analysis, competitive landscapes and strategic guidance, reach out to Ketan Rohom, Associate Director, Sales & Marketing. Discover how your organization can leverage the latest insights on composite materials to drive innovation, optimize performance and achieve sustainable growth in the oil and gas industry.
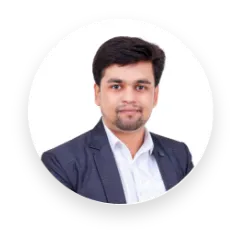
- When do I get the report?
- In what format does this report get delivered to me?
- How long has 360iResearch been around?
- What if I have a question about your reports?
- Can I share this report with my team?
- Can I use your research in my presentation?