The Computer Integrated Manufacturing Market size was estimated at USD 2.53 billion in 2024 and expected to reach USD 2.72 billion in 2025, at a CAGR 7.42% to reach USD 3.88 billion by 2030.
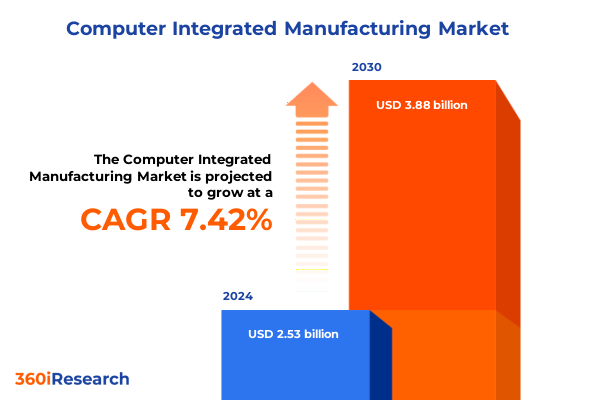
Introduction to Computer Integrated Manufacturing and Its Strategic Imperatives
Computer Integrated Manufacturing (CIM) represents the convergence of digital design, automation, and real-time data analytics to streamline production processes. As the manufacturing sector confronts mounting pressures-ranging from evolving customer expectations and disruptive technologies to complex global trade dynamics-organizations must adapt digital frameworks that integrate design, planning, execution, and quality control. This introduction outlines the strategic imperative for decision-makers to embrace a holistic CIM approach that emphasizes interoperability, scalability, and agility. By leveraging advanced software, robotics, and intelligent systems, manufacturers can reduce cycle times, minimize defects, and optimize resource utilization.
Over the past decade, the proliferation of Industry 4.0 technologies has catalyzed a paradigm shift in which connectivity and data-driven feedback loops replace siloed operations. Enterprises that harness CIM architectures gain a competitive advantage through predictive maintenance, real-time production adjustments, and seamless collaboration across engineering, operations, and supply chain stakeholders. As we transition into an era defined by customization, sustainability, and resilience, the integration of digital twins, collaborative robotics, and cloud-based platforms becomes not only desirable, but mandatory for market leaders. This section sets the stage for a deeper exploration of transformative trends, tariff impacts, segmentation nuances, regional dynamics, and strategic recommendations.
Transformative Shifts in the Computer Integrated Manufacturing Landscape
The manufacturing landscape is undergoing transformative shifts driven by the convergence of smart technologies and shifting market dynamics. Digital twins now serve as virtual blueprints that enable rapid scenario testing, reducing the need for costly physical prototypes. Cloud-based ERP systems have supplanted on-premise installations, enabling real-time data sharing across global facilities and reducing downtime. Meanwhile, collaborative robots are evolving beyond traditional pick-and-place tasks to work safely alongside human operators, leveraging AI-powered vision and motion planning to handle complex assembly and inspection processes.
Furthermore, the integration of Computer-Aided Design and Manufacturing (CAD/CAM) platforms has become seamless, allowing design iterations to flow directly into manufacturing workflows. This interoperability accelerates product development cycles and fosters innovation in areas such as additive manufacturing and hybrid machining techniques. Enterprise resource planning has incorporated advanced analytics modules for predictive maintenance, ensuring equipment uptime and enhancing operational efficiency.
Consequently, manufacturers are re-evaluating their legacy systems and forging partnerships with technology providers to build modular, adaptive ecosystems. By embracing open architectures and standardized communication protocols, businesses can integrate emergent technologies-such as blockchain for traceability and edge computing for low-latency control-without disrupting core operations.
Cumulative Impact of United States Tariffs 2025 on Manufacturing
In 2025, the implementation of new United States tariffs has reverberated across global manufacturing supply chains, compelling enterprises to reassess sourcing and production strategies. Tariffs imposed on imported industrial machinery and components have increased costs for capital-intensive assets such as CNC machines, sensors, and robotics modules. As a result, manufacturers reliant on tariff-affected imports have faced margin compression, prompting a shift toward local sourcing and domestic partners.
Moreover, higher duties on semiconductor and control system components have spurred inventory stocking and advance procurement strategies, creating working capital challenges. Some organizations have responded by relocating assembly lines closer to end markets in an effort to mitigate additional levies, while others have invested in redesigning products to utilize tariff-neutral alternatives.
In addition, these tariffs have accelerated the adoption of nearshoring models and spurred onshore investments in manufacturing modernization. Government incentives aimed at strengthening domestic production capacity have further influenced capital allocation decisions. As a result, companies are balancing compliance with cost management and risk mitigation, reevaluating supplier diversification, and fortifying their inbound logistics networks to sustain competitiveness in a high-tariff environment.
Key Segmentation Insights Across Technology, Industry, Components, Application, and Technique
An in-depth analysis of market segmentation reveals nuanced insights that guide strategic investment and product development decisions. When examining the technology type dimension, distinctions emerge among computer-aided design software, which spans 2D CAD, 3D CAD, and emerging collaborative CAD; computer-aided manufacturing software, which encompasses hybrid manufacturing CAM, mill CAM, and turn CAM; enterprise resource planning systems that offer both cloud-based and on-premise ERP solutions; and robotics platforms, which include articulated, Cartesian, cylindrical, SCARA, and next-generation AI-enhanced robotics.
Turning to the end-user industry dimension, aerospace and defense sectors subdivide into commercial aviation and defense applications, each demanding stringent precision standards and certification processes. Automotive end-users split between manufacturing operations and research and development facilities that require rapid prototyping and flexible production cells. Electronics markets include consumer electronics, expanding segments such as wearable electronics, and robust industrial electronics applications. Healthcare spans medical device manufacturing and pharmaceutical production, both facing rigorous regulatory scrutiny and traceability requirements.
Component type segmentation distinguishes hardware elements-covering control systems, conveyors, robots, and sensors-from services offerings such as consulting, maintenance and support, and system integration. The software component category includes integrated system software, manufacturing execution systems, and product lifecycle management platforms.
Application segmentation highlights logistics and storage operations, from automated storage and retrieval systems to in-plant logistics and warehousing; maintenance and repair functions, encompassing condition-based, predictive, and preventive maintenance; production planning strategies that range from finite to infinite scheduling horizons; and quality management frameworks, including statistical process control and total quality management.
Finally, manufacturing technique segmentation differentiates between flexible manufacturing systems-such as doubling back systems, operator-supervised systems, and linear systems-and lean manufacturing methodologies, which leverage 5S, just-in-time delivery, and Six Sigma process improvement to minimize waste and enhance throughput.
This comprehensive research report categorizes the Computer Integrated Manufacturing market into clearly defined segments, providing a detailed analysis of emerging trends and precise revenue forecasts to support strategic decision-making.
- Technology Type
- End-User Industry
- Component Type
- Application
- Manufacturing Technique
Key Regional Insights Shaping Global Manufacturing Dynamics
A regional lens offers valuable context for market entry and expansion strategies. In the Americas, established automotive and aerospace hubs are complemented by growing medical device clusters, driving demand for integrated manufacturing solutions and localized support ecosystems. The region’s emphasis on resilience and reshoring aligns with governmental programs that incentivize domestic production.
Meanwhile, Europe, Middle East & Africa combine mature manufacturing economies in Western Europe with emerging industrial corridors in the Middle East and North Africa. Sustainability mandates, digital transformation initiatives, and cross-border collaborations define the competitive landscape, encouraging investments in energy-efficient automation and circular economy practices.
Asia-Pacific stands out for its scale and diversification, with automotive, electronics, and consumer goods sectors leading the adoption of advanced robotics and Industry 4.0 platforms. China, Japan, South Korea, and Southeast Asian nations are driving high-volume deployments and fostering innovation in collaborative automation and smart factory architectures. oriented expansion plans must align with regional regulatory frameworks, talent availability, and infrastructure capabilities to capitalize on growth opportunities effectively.
This comprehensive research report examines key regions that drive the evolution of the Computer Integrated Manufacturing market, offering deep insights into regional trends, growth factors, and industry developments that are influencing market performance.
- Americas
- Asia-Pacific
- Europe, Middle East & Africa
Key Company Insights Driving Innovation and Competition
Leading technology providers and automation specialists are shaping the evolution of integrated manufacturing by introducing innovative solutions and forging strategic alliances. ABB Ltd. continues to advance its robotics portfolio with AI-driven controllers and modular power systems, targeting high-precision industries. Autodesk, Inc. leverages cloud-hosted design platforms that integrate seamlessly with downstream production workflows, enhancing collaboration across distributed teams.
Beckhoff Automation GmbH & Co. KG utilizes PC-based control approaches to offer scalable automation architectures, while CNC Software, LLC. delivers feature-rich CAM solutions optimized for complex machining operations. Cognex Corporation differentiates through vision systems that enable real-time inspection and traceability. Dassault Systèmes S.E. provides collaborative digital twin environments that align virtual design iterations with physical production constraints.
Emerson Electric Co. and Honeywell International Inc. extend their process automation expertise into discrete manufacturing, integrating advanced analytics and edge computing capabilities. Fuji Electric Manufacturing Co., Ltd. and Hitachi Solutions, Ltd. focus on energy-efficient drives and smart factory integration services. Hexagon AB enhances metrology and sensor solutions, reinforcing quality management protocols across high-precision sectors.
Johnson Controls International plc and KEYENCE CORPORATION. target facility management and inspection instrumentation, respectively, while KUKA AG by Midea Group. and Mitsubishi Electric Corporation deliver robotic systems and controllers tailored for diverse workloads. Oracle Corporation and SAP SE embed enterprise analytics within ERP platforms, enabling data-driven decision-making. Panasonic Corporation and PTC Inc. drive the development of IoT-enabled hardware and software ecosystems.
Robert Bosch GmbH and Rockwell Automation Inc. champion integrated safety and connectivity solutions within manufacturing cells. Schneider Electric SE and Siemens AG invest heavily in digital infrastructure and district-level automation frameworks. SolidCAM Ltd. optimizes CAM performance for high-speed machining, and Yokogawa Electric Corporation pioneers process control solutions adapted to discrete production lines. Collectively, these companies influence product roadmaps, interoperability standards, and service delivery models across the CIM landscape.
This comprehensive research report delivers an in-depth overview of the principal market players in the Computer Integrated Manufacturing market, evaluating their market share, strategic initiatives, and competitive positioning to illuminate the factors shaping the competitive landscape.
- ABB Ltd.
- Autodesk, Inc.
- Beckhoff Automation GmbH & Co. KG
- CNC Software, LLC.
- Cognex Corporation
- Dassault Systèmes S.E.
- Emerson Electric Co.
- Fuji Electric Manufacturing Co., Ltd.
- Hexagon AB
- Hitachi Solutions, Ltd.
- Honeywell International Inc.
- Johnson Controls International plc
- KEYENCE CORPORATION.
- KUKA AG by Midea Group.
- Mitsubishi Electric Corporation
- Oracle Corporation
- Panasonic Corporation
- PTC Inc.
- Robert Bosch GmbH
- Rockwell Automation Inc.
- SAP SE
- Schneider Electric SE
- Siemens AG
- SolidCAM Ltd.
- Yokogawa Electric Corporation
Actionable Recommendations for Industry Leaders
Industry leaders should consider the following strategic priorities to navigate evolving market conditions and sustain competitive advantage:
-
Embrace Open Ecosystems: Prioritize platforms and interfaces that support multi-vendor integration and data interoperability. By adopting standard communication protocols and open APIs, organizations can integrate best-of-breed solutions while avoiding vendor lock-in.
-
Invest in Workforce Transformation: Develop competency frameworks that blend digital, analytical, and domain-specific skills. Implement continuous learning programs focused on augmented reality-based training and cross-functional collaboration to ensure operational excellence.
-
Optimize Tariff Mitigation Strategies: Conduct a comprehensive review of global supply networks to identify tariff-exposed nodes. Leverage nearshoring opportunities, tariff engineering, and local content expansion to minimize duty impacts and maintain cost competitiveness.
-
Prioritize Modular Scalability: Design production cells and software architectures that can scale in line with demand fluctuations. Modular robotics and cloud-native ERP deployments allow rapid capacity adjustments and incremental capital investments.
-
Strengthen Cybersecurity Posture: Secure integrated manufacturing environments by implementing zero-trust frameworks, real-time threat monitoring, and segmented network architectures. Establish governance protocols that align with emerging regulatory requirements for data privacy and industrial control system security.
-
Drive Sustainability Initiatives: Incorporate life-cycle assessment tools and energy-efficient automation to achieve circular manufacturing targets. Engage in collaborative partnerships across the value chain to reduce carbon footprints and promote resource recovery.
Explore AI-driven insights for the Computer Integrated Manufacturing market with ResearchAI on our online platform, providing deeper, data-backed market analysis.
Ask ResearchAI anything
World's First Innovative Al for Market Research
Conclusion: Navigating the Future of Computer Integrated Manufacturing
The journey toward fully integrated manufacturing is both complex and rewarding. By internalizing transformative trends, understanding tariff implications, and leveraging segmentation and regional insights, decision-makers can craft robust strategies that deliver continuous improvement and long-term growth. A balanced approach-anchored in open technologies, workforce development, and sustainability-will position organizations to thrive in a digital economy defined by agility and resilience.
This section provides a structured overview of the report, outlining key chapters and topics covered for easy reference in our Computer Integrated Manufacturing market comprehensive research report.
- Preface
- Research Methodology
- Executive Summary
- Market Overview
- Market Dynamics
- Market Insights
- Cumulative Impact of United States Tariffs 2025
- Computer Integrated Manufacturing Market, by Technology Type
- Computer Integrated Manufacturing Market, by End-User Industry
- Computer Integrated Manufacturing Market, by Component Type
- Computer Integrated Manufacturing Market, by Application
- Computer Integrated Manufacturing Market, by Manufacturing Technique
- Americas Computer Integrated Manufacturing Market
- Asia-Pacific Computer Integrated Manufacturing Market
- Europe, Middle East & Africa Computer Integrated Manufacturing Market
- Competitive Landscape
- ResearchAI
- ResearchStatistics
- ResearchContacts
- ResearchArticles
- Appendix
- List of Figures [Total: 26]
- List of Tables [Total: 1000 ]
Call-to-Action: Connect with Ketan Rohom to Secure Your Market Research Report
Unlock the full potential of your manufacturing operations by securing in-depth market research insights. To explore comprehensive analysis, segmentation breakdowns, and strategic recommendations tailored to your unique objectives, reach out to Ketan Rohom (Associate Director, Sales & Marketing) today. Transform uncertainty into opportunity-contact Ketan Rohom to purchase the complete report and drive your competitive edge.
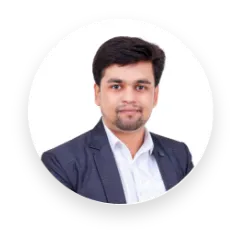
- How big is the Computer Integrated Manufacturing Market?
- What is the Computer Integrated Manufacturing Market growth?
- When do I get the report?
- In what format does this report get delivered to me?
- How long has 360iResearch been around?
- What if I have a question about your reports?
- Can I share this report with my team?
- Can I use your research in my presentation?