The Conductive Silicone Tubing Market size was estimated at USD 5.12 billion in 2024 and expected to reach USD 5.42 billion in 2025, at a CAGR 5.73% to reach USD 7.15 billion by 2030.

Unveiling the Role of Conductive Silicone Tubing in Modern Applications
Conductive silicone tubing has emerged as a critical enabler of electrical conductivity in applications demanding both flexibility and durability. By integrating conductive fillers into a resilient silicone matrix, this specialized tubing maintains consistent performance across a broad range of temperatures and environmental conditions. Increasingly stringent design requirements in sectors spanning advanced electronics, medical devices, and automotive systems have driven engineers to adopt these tubing solutions as a means of ensuring reliable conductive pathways without sacrificing mechanical flexibility.
The maturation of filler dispersion techniques and advances in extrusion processes have unlocked new performance thresholds, enabling a spectrum of solutions tailored to high-frequency signal transmission, EMI shielding, and electrostatic discharge mitigation. As manufacturers compete to deliver thinner wall profiles and tighter tolerances, collaborative efforts between material scientists and original equipment manufacturers become vital. At the same time, compliance with evolving regulatory standards around biocompatibility and flame retardancy adds complexity to product development. In this context, a nuanced perspective on market drivers, material innovations, and supply chain dynamics is essential for stakeholders aiming to position themselves at the forefront of this high-value niche.
Moreover, cost optimization strategies have gained prominence as raw material prices fluctuate and regional manufacturing footprints diversify. Decision-makers must weigh the trade-offs between localized production and global sourcing to maintain both agility and competitiveness. The role of sustainability also looms large, as end users increasingly demand materials that align with circular economy principles. Taken together, these factors underscore the necessity of a strategic approach that aligns technical requirements with evolving market expectations.
Navigating Industry Transformations Shaping Silicone Tubing Dynamics
In recent years, the conductive silicone tubing landscape has been reshaped by the accelerating pace of digitalization and the Industry 4.0 revolution. Connected devices now demand tubing that not only conducts electricity effectively but also integrates seamlessly with sensor networks and communication architectures. At the same time, regulatory frameworks such as RoHS and REACH have imposed stricter controls on hazardous substances, prompting material scientists to explore novel filler chemistries and recycling strategies. Sustainability imperatives have driven the development of bio-based silicones and closed-loop manufacturing processes, underscoring a shift towards resource efficiency and environmental stewardship across the supply chain.
Parallel to regulatory and environmental pressures, the transition to electrified mobility and distributed energy systems has elevated the strategic importance of conductive silicone tubing. Electric vehicles and renewable energy installations require robust, high-performance insulation that can sustain frequent thermal cycling and offer consistent electrical characteristics. In the medical sector, the rise of telemedicine and wearable devices has spurred demand for tubing that conforms to complex geometries while meeting stringent biocompatibility standards. These converging forces-technological innovation, regulatory evolution, and shifting end-user requirements-have collectively transformed the market into a dynamic arena where adaptability and performance leadership define success.
Assessing the 2025 United States Tariffs and Their Cascading Effects
The introduction of elevated tariff regimes in the United States in 2025 has had a cascading effect on the conductive silicone tubing sector. Higher duty rates imposed on imported silicone base polymers and conductive fillers, including specialty carbon black and metal-coated powders, have prompted manufacturers to reassess their sourcing strategies. Supply chain disruptions have emerged as suppliers redirect volumes to mitigate exposure to tariff liabilities, leading to delivery delays and increased freight costs. In turn, these pressures have strained profit margins and compelled a reevaluation of pricing models across the value chain, particularly for high-purity material grades used in critical applications.
In response to these headwinds, industry stakeholders have implemented a range of strategic countermeasures. Advocacy for tariff exemptions and classification clarifications has gained traction, with consortiums engaging policymakers to limit the impact on essential components. Concurrently, a wave of near-shore and onshore sourcing initiatives has unfolded, as manufacturers seek to localize production closer to key end markets. Material engineers are exploring alternative conductive fillers to balance performance and cost, while procurement teams emphasize agile inventory management to buffer against potential disruptions. These adaptive strategies highlight the sector’s resilience and willingness to innovate in the face of evolving trade landscapes.
Decoding Market Segmentation for Targeted Strategy Development
Material selection serves as the cornerstone of competitive advantage in the conductive silicone tubing market. Carbon black-filled formulations continue to deliver a balance of cost-effectiveness and baseline conductivity, making them a go-to choice for standard EMI shielding and ESD mitigation. Metal coated polymer variants, with their precise filler encapsulation, offer enhanced corrosion resistance, while silver coated copper composites command premium performance in high-frequency signal transmission scenarios. Meanwhile, stainless steel-infused tubing delivers superior mechanical reinforcement and long-term stability in harsh chemical or thermal environments, albeit at a higher price point. These distinct material pathways enable producers to tailor solutions across varied performance thresholds.
The interplay between application requirements and end-use industry demands further refines segmentation dynamics. Automotive harness assemblies and transportation systems hinge on tubing that can endure repetitive flexing and exposure to fluids, whereas electronics enclosures in consumer devices prioritize tight tolerances and minimal signal loss. Industrial sensor networks, operating in temperature extremes and chemical exposures, require formulations that balance durability with conductivity fidelity. In the medical sector and broader healthcare landscape, biocompatibility and sterilization resilience become paramount, guiding the selection of tubing compounds designed for patient-contact scenarios.
Sales channel strategies intersect with product attributes to influence market reach. Direct engagement with OEMs fosters collaborative development for bespoke tubing solutions, while established distribution networks widen access to standard grades across regional markets. The rise of digital procurement platforms complements traditional channels, offering expedited lead times for off-the-shelf configurations. Shore hardness also plays a decisive role, with harder durometers delivering structural support in static assemblies and softer formulations facilitating tight bends and dynamic movement without compromising conductive continuity.
Manufacturing process choices underpin cost structures and performance consistency. Extrusion remains the predominant method for continuous lengths of uniform wall thickness, enabling high-volume throughput and rapid prototyping. Conversely, injection molding caters to complex, integrated geometries such as custom connectors and multi-lumen assemblies, supporting higher filler loadings and tighter dimensional control. These process-driven distinctions inform capital investment decisions and production scalability for market participants.
This comprehensive research report categorizes the Conductive Silicone Tubing market into clearly defined segments, providing a detailed analysis of emerging trends and precise revenue forecasts to support strategic decision-making.
- Material Type
- Application
- End Use Industry
- Sales Channel
- Shore Hardness
- Manufacturing Process
Unearthing Regional Trends Influencing Silicone Tubing Adoption
In the Americas, a mature industrial landscape underpins robust demand for conductive silicone tubing. Automotive wiring harness manufacturers in North America have integrated these tubing solutions to satisfy rigorous safety and performance mandates, while medical device producers leverage local supply chains to secure biocompatible materials with rapid lead times. Simultaneously, a growing network of specialty polymers plants in South America has begun to address regional demand fluctuations, mitigating the effects of cross-border tariffs and logistical bottlenecks. This localized capacity, combined with end-user preference for near-term stocking, underscores the strategic importance of the Americas as both a consumption and production hub.
Within Europe, the Middle East, and Africa, stringent environmental and chemical regulations have elevated the significance of compliant conductive silicone solutions. European automakers advancing electric vehicle programs prioritize tubing compounds that meet recycled content targets and fuel cell compatibility. In parallel, the energy sector in the Middle East and Africa has driven demand for tubing that withstands extreme temperatures and corrosive environments in oil and gas applications. A network of specialized distributors supports market penetration across diverse industries, while collaborative research initiatives in leading European research institutes continue to refine material performance benchmarks.
The Asia-Pacific region remains the fulcrum of global manufacturing prowess, with China, Japan, South Korea, and India accounting for a substantial share of production capacity. Electronics assembly clusters in East Asia demand tubing that can handle high-speed data transmission and intricate device architectures. Rapidly expanding telemedicine and wearable health monitor markets in India and Southeast Asia have spurred local development of biocompatible formulations. Cost efficiencies achieved through economies of scale, coupled with government incentives for advanced materials production, position Asia-Pacific as a dynamic frontier for both emerging applications and incremental innovation.
This comprehensive research report examines key regions that drive the evolution of the Conductive Silicone Tubing market, offering deep insights into regional trends, growth factors, and industry developments that are influencing market performance.
- Americas
- Europe, Middle East & Africa
- Asia-Pacific
Profiling Industry Leaders Driving Innovation in Silicone Tubing
Leading material conglomerates have reinforced their market positions through substantial investments in research and development, focusing on next-generation conductive fillers and proprietary silicone blends. These firms maintain integrated production facilities that span raw polymer synthesis to final tubing extrusion, enabling stringent quality control and rapid scalability. Their extensive global networks allow for synchronized capacity expansions in strategic regions, ensuring responsiveness to regional demand fluctuations and tariff-induced disruptions.
In contrast, nimble specialists have carved out niches by offering highly customized tubing solutions tailored to specific performance requirements. These companies emphasize agile customer collaboration, deploying technical service teams to co-engineer compounds and configurations for unique applications in aerospace, precision instrumentation, and advanced medical therapeutics. Through modular production cells and rapid prototyping capabilities, they accelerate time-to-market for novel designs, creating competitive differentiation based on responsiveness and depth of expertise.
Across the competitive landscape, partnership strategies and digital enablement stand out as key differentiators. Alliances with filler technology innovators and collaborative ventures with research institutes have expanded the material horizons available to tubing manufacturers. Concurrently, the adoption of digital tools for virtual design validation and predictive maintenance in production facilities has enhanced operational efficiency. Mergers and acquisitions continue to reshape the sector, consolidating complementary capabilities and broadening portfolios in response to evolving customer demands.
This comprehensive research report delivers an in-depth overview of the principal market players in the Conductive Silicone Tubing market, evaluating their market share, strategic initiatives, and competitive positioning to illuminate the factors shaping the competitive landscape.
- 3M Company
- Parker-Hannifin Corporation
- Saint-Gobain Performance Plastics Corporation
- Trelleborg AB
- Rogers Corporation
- Dow Inc.
- Wacker Chemie AG
- KCC Corporation
- Shin-Etsu Chemical Co., Ltd.
- Elkem ASA
Strategic Imperatives for Leaders to Capitalize on Emerging Opportunities
To secure a competitive edge, industry leaders should intensify investment in advanced material research, focusing on emerging conductive fillers and next-generation silicone matrices. Establishing cross-functional teams that integrate material scientists, process engineers, and application specialists will accelerate innovation cycles and enable more precise customization. Harnessing digital simulation tools for virtual design validation can minimize trial iterations and shorten development timelines.
Diversification of supply chains is another critical imperative. By establishing regional sourcing hubs and cultivating relationships with alternative raw material suppliers, companies can mitigate exposure to trade policy fluctuations and logistical disruptions. Concurrently, material engineers should evaluate the feasibility of lower-cost conductive fillers to maintain price competitiveness without compromising core performance attributes.
Elevating sustainability credentials will resonate with increasingly eco-conscious end users and regulators. Implementing recycling partnerships and exploring closed-loop material programs can reduce environmental footprints and enhance brand reputation. Transparent reporting on lifecycle assessments will further reinforce stakeholder trust and differentiate offerings in a crowded marketplace.
Strategic partnerships and targeted acquisitions can broaden technological capabilities and expand market access. Collaborations with filler technology developers and alliances with software providers for production automation will drive holistic value creation. Finally, integrating digital channels into sales and customer support operations will improve market responsiveness and deepen engagement with OEMs and distributors, laying the foundation for sustained growth.
Ensuring Rigor Through a Comprehensive Research Framework
This study employed a comprehensive research framework combining both secondary and primary methodologies to ensure the highest level of rigor. Secondary research encompassed an exhaustive review of industry publications, technical journals, regulatory filings, and patent databases, providing a foundational understanding of material innovations, regulatory landscapes, and competitive dynamics. Market participant disclosures and corporate sustainability reports supplemented this base with real-world insights into strategic priorities and product roadmaps.
Primary research initiatives involved in-depth interviews with key stakeholders across the supply chain, including material suppliers, original equipment manufacturers, and end users. These qualitative engagements yielded granular intelligence on performance requirements, procurement decision criteria, and emerging adoption patterns. Structured surveys were deployed to capture quantitative feedback on product attributes and channel preferences, while site visits to manufacturing facilities validated process descriptions and capacity configurations.
Data obtained from both streams underwent rigorous triangulation, with cross-verification against multiple sources to identify and rectify discrepancies. Analytical techniques, such as comparative benchmarking and gap analysis, were applied to distill actionable insights. The final output was subjected to peer review by independent experts with domain-specific experience, ensuring that findings are both accurate and operationally relevant. This multifaceted approach underpins the credibility and depth of the study’s conclusions.
Explore AI-driven insights for the Conductive Silicone Tubing market with ResearchAI on our online platform, providing deeper, data-backed market analysis.
Ask ResearchAI anything
World's First Innovative Al for Market Research
Concluding Perspectives on the Conductive Silicone Tubing Frontier
The conductive silicone tubing market stands at the nexus of technological innovation, regulatory evolution, and shifting global trade dynamics. Across material variants and application classes, stakeholders must navigate a complex interplay of performance demands and cost pressures against a backdrop of tariff volatility and evolving sustainability mandates. Segmentation analyses reveal distinct pathways for differentiation, whether through advanced material systems, tailored distribution models, or process-centric manufacturing strategies. Regional insights underscore the importance of localized production footprints and regulatory compliance, while competitive profiling highlights the ongoing convergence of scale advantages and specialized expertise.
Looking ahead, the ability to anticipate regulatory shifts, adapt supply chain structures, and foster collaborative innovation will define the leading enterprises in this sector. Stakeholders who invest in agile research and development capabilities, embrace digital transformation, and commit to environmental stewardship will be best positioned to capitalize on emerging opportunities. Ultimately, a strategic outlook that integrates technical excellence with market responsiveness will unlock the full potential of conductive silicone tubing solutions across the most demanding applications.
This section provides a structured overview of the report, outlining key chapters and topics covered for easy reference in our Conductive Silicone Tubing market comprehensive research report.
- Preface
- Research Methodology
- Executive Summary
- Market Overview
- Market Dynamics
- Market Insights
- Cumulative Impact of United States Tariffs 2025
- Conductive Silicone Tubing Market, by Material Type
- Conductive Silicone Tubing Market, by Application
- Conductive Silicone Tubing Market, by End Use Industry
- Conductive Silicone Tubing Market, by Sales Channel
- Conductive Silicone Tubing Market, by Shore Hardness
- Conductive Silicone Tubing Market, by Manufacturing Process
- Americas Conductive Silicone Tubing Market
- Europe, Middle East & Africa Conductive Silicone Tubing Market
- Asia-Pacific Conductive Silicone Tubing Market
- Competitive Landscape
- ResearchAI
- ResearchStatistics
- ResearchContacts
- ResearchArticles
- Appendix
- List of Figures [Total: 28]
- List of Tables [Total: 283 ]
Secure Your In-Depth Conductive Silicone Tubing Report Today
Unlock the full suite of insights and strategic guidance with our in-depth conductive silicone tubing market research report. Equip your team with detailed analyses of segmentation dynamics, regional trends, and competitive strategies to inform your next strategic move. Reach out to Ketan Rohom, Associate Director of Sales & Marketing, to explore customized licensing options and receive a comprehensive executive briefing. Secure access to actionable data and expert commentary that will empower your organization to navigate supply chain complexities, regulatory shifts, and technological advancements with confidence.
Contact Ketan Rohom to discuss pricing tiers and value-added consulting services that align with your strategic objectives. With tailored support and priority updates, you can drive innovation initiatives, optimize procurement strategies, and establish a competitive advantage. Act now to gain immediate access and transform your understanding of this critical materials market
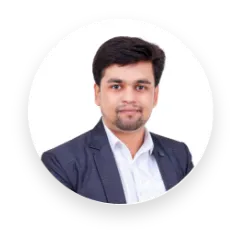
- How big is the Conductive Silicone Tubing Market?
- What is the Conductive Silicone Tubing Market growth?
- When do I get the report?
- In what format does this report get delivered to me?
- How long has 360iResearch been around?
- What if I have a question about your reports?
- Can I share this report with my team?
- Can I use your research in my presentation?