Introduction to Continuous Casting Moulds: Market Context and Significance
Continuous casting moulds are the linchpin of modern metal manufacturing, providing a precise interface between molten alloys and the final shaped product. By maintaining optimal cooling rates and uniform solidification, these moulds ensure consistent slab, billet and bloom quality, driving efficiency across steel, aluminum, copper and specialty alloy production. As industries from automotive to aerospace demand higher-performance materials with tighter tolerances, continuous casting mould technology has evolved to address quality, throughput and cost pressures. Furthermore, environmental regulations and energy constraints have intensified the need for more efficient thermal management and resource utilization. This introduction frames the continuous casting mould market within a broader context of technological innovation, sustainability imperatives and shifting global supply chains, setting the stage for an in-depth exploration of recent shifts and strategic insights without relying on market sizing or forecasting.
Transformative Shifts Reshaping the Continuous Casting Mould Landscape
Over the past decade, continuous casting mould technology has undergone transformative shifts driven by digitalization, automation and sustainability mandates. Industry 4.0 adoption has introduced real-time sensor networks and predictive analytics, enabling adaptive control of cooling and solidification parameters. Advanced materials for mould lining and copper alloys enhance thermal conductivity while extending service life. Moreover, the push toward net-zero emissions has spurred integration of low-carbon energy sources and waste-heat recovery solutions within casting lines. Supply chain disruptions and volatile raw material costs have prompted manufacturers to diversify sourcing strategies and embrace modular, scalable installations that support rapid changeovers. Additionally, collaboration between equipment suppliers and end users has accelerated co-development of bespoke mould designs optimized for next-generation high-strength alloys. These converging trends have not only elevated process stability and product quality but are also redefining competitive benchmarks for productivity, environmental performance and lifecycle costs in continuous casting operations.
Cumulative Impact of United States Tariffs on the Continuous Casting Mould Market in 2025
In 2025, revised United States tariff policies targeted steel and aluminum inputs critical to continuous casting mould production, generating a ripple effect across the supply chain. Elevated duties on imported alloys have increased material procurement costs, compelling mould manufacturers to negotiate new contracts with domestic metal producers or to explore duty-free trade agreements. As a result, some equipment fabricators have accelerated investments in localized recycling and remelting initiatives to mitigate tariff exposure. Furthermore, key downstream industries such as automotive and construction have responded by adjusting their sourcing strategies, favoring integrated suppliers capable of delivering turnkey casting solutions within domestic borders. These shifts have also encouraged partnerships between mould designers and foundries to co-locate services, reducing cross-border logistics and compliance overhead. While tariffs have introduced pricing pressures, they have simultaneously opened opportunities for regional consolidation, strategic alliances and vertically integrated models that enhance resilience and cost competitiveness.
Key Segmentation Insights: Technology, Material, Application, End-User, Process, and Parameters
The continuous casting mould market can be dissected across multiple dimensions that reveal nuanced growth vectors and innovation hotspots. Based on technology type, horizontal continuous casting dominates due to its versatility and throughput, bolstered by advancements in casting speed control and solidification management. Within this segment, metallic compositions such as brass, bronze and stainless steel are gaining traction for specialized slab applications. In parallel, vertical continuous casting leverages tailored application techniques for bars, billets and slabs, using aluminum, copper and zinc alloys to serve niche markets requiring precise cross-sections. Material type segmentation further illuminates demand patterns, with boron and titanium alloys emerging under the alloys category, while ferrous metals encompass alloy steels, carbon steels and stainless steels. Non-ferrous metals-comprising aluminum, copper and nickel alloys-are fueling growth in corrosion-resistant and lightweight structures. The application segmentation underscores the prominence of aerospace structures and landing gear in aircraft, alongside engine components and transmission systems within automotive manufacturing. Construction infrastructure projects and structural components leverage large-scale slab casting, and shipbuilding relies on deck equipment and hull components produced via robust continuous casting lines. End-user industries add another layer of insight: electrical and electronics markets depend on conductors, semiconductors, transformers and motors; industrial machinery production prioritizes components manufacturing and heavy machinery; transportation equipment manufacturers source automotive parts and railway components. When viewed through the lens of process type, cold rolled processing stands out for precise dimensions adjustment and surface finishing, whereas direct chill casting and hot rolling continue to serve high-volume feedstock requirements. Finally, casting parameters such as cooling and solidification techniques-ranging from direct or indirect cooling to soft or hard reduction-mould dimensions featuring length adjustment and taper design, and stringent temperature control protocols collectively define the performance envelope of modern continuous casting mould solutions.
This comprehensive research report categorizes the Continuous Casting Mould market into clearly defined segments, providing a detailed analysis of emerging trends and precise revenue forecasts to support strategic decision-making.
- Technology Type
- Material Type
- Application
- End-User Industry
- Process Type
- Casting Parameters
Key Regional Insights Across the Americas, EMEA, and Asia-Pacific
Regional dynamics exert a powerful influence on continuous casting mould deployment and innovation trajectories. In the Americas, strong momentum in automotive, construction and industrial machinery sectors drives demand for versatile mould systems that support high-volume steel and aluminum production. Local emphasis on near-shoring and infrastructure renewal has incentivized mould manufacturers to offer rapid delivery schedules and integrated service networks. Across Europe, the Middle East and Africa, energy transition goals and industrial modernization programs are catalyzing investments in low-emission casting lines and advanced alloy capabilities. Manufacturers in this region are increasingly partnering with technology providers to retrofit existing facilities, emphasizing modular upgrades that align with circular economy principles. In Asia-Pacific, robust growth in shipbuilding, electronics and consumer durables, particularly in China, India and Southeast Asia, has positioned this market as a hotbed for both installed capacity expansion and greenfield investments. High demand for lightweight metals in aerospace and automotive applications is prompting continuous casting mould suppliers to develop specialized copper-based and aluminum-based solutions, often in collaboration with local steelworks and foundries.
This comprehensive research report examines key regions that drive the evolution of the Continuous Casting Mould market, offering deep insights into regional trends, growth factors, and industry developments that are influencing market performance.
- Americas
- Asia-Pacific
- Europe, Middle East & Africa
Key Company Insights Driving Innovation and Competitive Advantage
Leading companies are shaping the continuous casting mould landscape through differentiated technology portfolios, global service networks and strategic R&D. AG der Dillinger Hüttenwerke applies its deep expertise in heavy steel plates to supply robust, wear-resistant moulds for high-speed slabs. Danieli & C. Officine Meccaniche S.p.A. continues to pioneer fully integrated casting lines that combine digital control systems with optimized copper mould designs. The EIRICH GROUP (Gustav Eirich GmbH & Co KG) brings specialized metallurgy and granulation know-how to produce bespoke alloy mould bits. KME Germany GmbH & Co. KG leverages its copper product heritage to introduce innovative cooling channels and reinforced mould frames. Luvata Special Products Oy focuses on precision machining of copper alloys, delivering tight tolerance mould components for critical engineering applications. Ningbo Xinxing Casting Technology Co., Ltd. distinguishes itself with lean manufacturing processes and rapid prototyping capabilities. Primetals Technologies Limited integrates AI-driven thermal models within its mould control platforms. Sinosteel Equipment & Engineering Co., Ltd. emphasizes turnkey casting installations across emerging markets. SMS Concast AG couples its metallurgical simulation tools with field service expertise to optimize mould performance. Vesuvius Group SA rounds out the competitive landscape by offering refractory and coating solutions that enhance thermal efficiency and service life.
This comprehensive research report delivers an in-depth overview of the principal market players in the Continuous Casting Mould market, evaluating their market share, strategic initiatives, and competitive positioning to illuminate the factors shaping the competitive landscape.
- AG der Dillinger Hüttenwerke
- Danieli & C. Officine Meccaniche S.p.A.
- EIRICH GROUP (Gustav Eirich GmbH & Co KG)
- KME Germany GmbH & Co. KG
- Luvata Special Products Oy
- Ningbo Xinxing Casting Technology Co., Ltd.
- Primetals Technologies Limited
- Sinosteel Equipment & Engineering Co., Ltd.
- SMS Concast AG
- Vesuvius Group SA
Actionable Recommendations for Continuous Casting Mould Industry Leaders
Industry leaders should prioritize digital transformation initiatives that embed real-time monitoring and adaptive control within continuous casting mould operations. Investing in digital twin simulations can accelerate troubleshooting, optimize cooling profiles and extend mould life cycles. To mitigate geopolitical uncertainties, companies must diversify their supplier networks and explore strategic alliances with regional foundries. Embracing sustainable practices-such as waste-heat recovery, water recycling and low-carbon energy integration-will not only reduce environmental footprints but also strengthen regulatory compliance and brand reputation. Furthermore, deepening collaboration between equipment designers and end users will foster co-innovation of custom mould geometries tailored for advanced high-strength alloys. Upskilling the workforce through targeted training in metallurgical principles and process analytics will ensure that the benefits of emerging technologies are fully realized. By executing on these initiatives, industry participants can enhance resilience, drive cost efficiency and capture new market opportunities.
Explore AI-driven insights for the Continuous Casting Mould market with ResearchAI on our online platform, providing deeper, data-backed market analysis.
Ask ResearchAI anything
World's First Innovative Al for Market Research
Conclusion: Strategic Imperatives for Continuous Casting Mould Excellence
Continuous casting mould market success hinges on strategic agility, technical excellence and sustainable innovation. By aligning mould design advancements with evolving metallurgical requirements and regulatory frameworks, manufacturers can deliver differentiated value to end users across diverse industries. Integrating digital tools for process optimization, combined with robust service and maintenance programs, will underpin long-term performance and customer satisfaction. Moreover, a clear focus on regional market nuances and localized partnerships can accelerate market entry and secure competitive advantage. Ultimately, firms that embrace a holistic approach-melding technological leadership with environmental stewardship and collaborative ecosystems-will lead the next chapter of continuous casting mould evolution.
This section provides a structured overview of the report, outlining key chapters and topics covered for easy reference in our Continuous Casting Mould market comprehensive research report.
- Preface
- Research Methodology
- Executive Summary
- Market Overview
- Market Dynamics
- Market Insights
- Cumulative Impact of United States Tariffs 2025
- Continuous Casting Mould Market, by Technology Type
- Continuous Casting Mould Market, by Material Type
- Continuous Casting Mould Market, by Application
- Continuous Casting Mould Market, by End-User Industry
- Continuous Casting Mould Market, by Process Type
- Continuous Casting Mould Market, by Casting Parameters
- Americas Continuous Casting Mould Market
- Asia-Pacific Continuous Casting Mould Market
- Europe, Middle East & Africa Continuous Casting Mould Market
- Competitive Landscape
- ResearchAI
- ResearchStatistics
- ResearchContacts
- ResearchArticles
- Appendix
- List of Figures [Total: 28]
- List of Tables [Total: 1079 ]
Next Steps: Contact Ketan Rohom to Secure the Full Market Research Report
To access the comprehensive market research report featuring in-depth segmentation analysis, regional deep dives and competitor benchmarking, reach out to Ketan Rohom (Associate Director, Sales & Marketing) today. Gain unparalleled insights into mould technology trends, tariff impact assessments and actionable strategies that will empower your organization to thrive. Secure your copy now to unlock the data-driven roadmap you need to steer continuous casting mould investments with confidence.
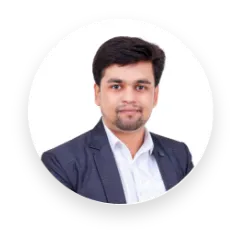
- When do I get the report?
- In what format does this report get delivered to me?
- How long has 360iResearch been around?
- What if I have a question about your reports?
- Can I share this report with my team?
- Can I use your research in my presentation?