Revolutionizing Catalyst Regeneration in Modern Oil Refining
Continuous catalyst regeneration stands at the heart of modern oil refining, delivering sustained activity levels and minimizing downtime by enabling catalysts to be reactivated without full shutdowns. This process not only curtails operational expenditure associated with frequent replacements but also enhances product yield consistency under variable feedstock conditions. As industry stakeholders confront stricter environmental regulations and pursue greater refinery margins, the imperative to optimize regeneration protocols has intensified.
This executive summary delves into how continuous catalyst regeneration has evolved into a strategic enabler. It outlines fundamental shifts in technology adoption, analyzes the regulatory headwinds introduced by the United States tariffs effective in 2025, and explores the intricate dynamics across key segmentation dimensions-from catalyst chemistries such as alumina based materials including eta and gamma alumina to zeolite formulations like HZSM-5 and ultrastable Y.
By examining applications ranging from catalytic reforming through desulfurization, fluid catalytic cracking, and hydrocracking, and considering both fluidized bed and moving bed regeneration technologies along with diverse catalyst forms and end users, this introduction frames the comprehensive insights to follow. The ensuing sections will equip decision makers with an authoritative perspective on how to leverage continuous regeneration to achieve resilient, cost-effective, and compliant refining operations.
Navigating the Evolution of Continuous Catalyst Regeneration
The landscape of continuous catalyst regeneration is undergoing profound transformation driven by advances in material science, process intensification, and digital integration. High-performance mixed oxide catalysts now exhibit enhanced thermal stability, while next-generation zeolite architectures leverage tailored pore structures to maximize selectivity under increasingly severe process conditions. In parallel, refiners are adopting real-time monitoring tools-incorporating spectroscopic sensors and machine learning algorithms-to predict deactivation trajectories and optimize regeneration cycles, thereby reducing unplanned outages and maximizing on-stream performance.
Furthermore, the drive toward lower carbon footprints has catalyzed development of energy-efficient regeneration methods. Moving bed systems, once considered niche, are now being retrofitted to existing units to deliver continuous reactivation with reduced thermal inertia. Process intensification strategies are also enabling more compact reactor designs, facilitating easier integration of regeneration sections without extensive plant modifications.
Moreover, strategic alliances between catalyst producers, automation developers, and refining operators are fostering co-development of turnkey regeneration solutions. These collaborative ecosystems are accelerating innovation adoption, shortening implementation timelines, and de-risking capital investments. As a result, refiners can now approach catalyst regeneration not as a necessary chore but as a value-creation platform for operational excellence and environmental compliance.
Assessing the Cumulative Effects of 2025 US Tariffs on Catalyst Regeneration
The United States has introduced a series of tariffs effective in 2025 that impact key raw materials and finished catalyst products integral to continuous regeneration operations. Aluminum oxide and specialty zeolite imports have become subject to additional duties, elevating input costs and prompting critical reassessments of supply chain resilience. Consequently, many refiners and catalyst suppliers are exploring domestic sourcing options and strategic inventory buffers to mitigate price volatility and safeguard production continuity.
In response, certain catalyst producers have accelerated investments in local manufacturing facilities, enabling closer alignment with regional demand and reducing lead times. At the same time, refiners are negotiating long-term contracts with alternative providers in regions not affected by the tariffs, thereby diversifying their procurement channels. This shift has underscored the importance of flexible supplier networks and adaptive supply chain strategies that can absorb tariff-induced cost shocks while preserving technical performance standards.
Moreover, the tariffs have spurred greater emphasis on regeneration efficiency. By extending catalyst cycle life through optimized regeneration schedules and advanced deactivation modeling, operators can offset higher acquisition expenses with reduced consumption rates. Ultimately, the cumulative tariff impact is reshaping commercial agreements, driving localized production, and reinforcing the strategic value of continuous regeneration as a lever for cost containment and operational agility.
Unveiling Critical Segmentation Insights in Catalyst Regeneration Market
Segmentation analysis reveals that the choice of catalyst type exerts a profound influence on regeneration strategy and performance. Refiners utilizing alumina based catalysts must decide between eta alumina, prized for its mechanical strength, and gamma alumina, valued for its surface area and acid site distribution. Those focused on hydrocarbon reforming and fluid catalytic cracking frequently deploy zeolite based materials, selecting HZSM-5 for its shape-selective cracking properties and ultrastable Y for enhanced hydrothermal resilience.
Application-driven differentiation further nuances market dynamics. Catalytic reforming units emphasize regeneration protocols that preserve metal dispersion on catalyst supports, whereas desulfurization plants require stable alumina frameworks to maintain high sulfur removal efficiencies. Fluid catalytic cracking operations, characterized by high throughput and cyclic deactivation, benefit from extrudate forms that deliver robust attrition resistance, while hydrocracking applications often favor pellet or powder configurations to optimize mass transfer.
Regeneration technology choice acts as a critical determinant of operational continuity. Fluidized bed systems offer rapid heat transfer and uniform reactivation, making them well suited for large-scale refinery operations, whereas moving bed units provide continuous, low-amplitude temperature swings ideal for maintaining catalyst integrity. Finally, distinctions between end users-whether petrochemical complexes focused on selective olefin production or petroleum refineries targeting transportation fuels-shape regeneration frequency, performance targets, and service agreements.
This comprehensive research report categorizes the Continuous Catalyst Regeneration Catalyst for Oil Refinery market into clearly defined segments, providing a detailed analysis of emerging trends and precise revenue forecasts to support strategic decision-making.
- Catalyst Type
- Application
- Regeneration Technology
- Catalyst Form
- End User
Decoding Regional Dynamics Shaping Catalyst Regeneration Adoption
Regional dynamics play a decisive role in shaping continuous catalyst regeneration strategies. In the Americas, abundant shale feedstocks and stringent environmental mandates drive refiners to invest heavily in advanced regeneration systems that support high sulfur content processing while minimizing emissions. The proximity of catalyst manufacturers to major refinery hubs also facilitates agile supply chains and collaborative R&D initiatives, enhancing regional competitiveness.
Europe, the Middle East and Africa present a complex tapestry of mature refining infrastructure and evolving regulatory landscapes. European operators, under pressure to reduce carbon intensity, are integrating energy-efficient regeneration technologies and digital analytics to extend run lengths. In the Middle East and Africa, the expansion of new refinery projects coexists with efforts to retrofit legacy units, creating demand for modular regeneration solutions that can be deployed with minimal site disruption.
Across Asia-Pacific, rapid growth in petrochemical and fuel consumption is accelerating the adoption of continuous regeneration capabilities. India and China are at the forefront, commissioning large-scale hydrocracking and fluid catalytic cracking complexes that rely on locally developed catalysts and regeneration expertise. Elsewhere in the region, Southeast Asian refiners are partnering with global technology providers to leapfrog incremental upgrades and establish cutting-edge regeneration platforms from the outset.
This comprehensive research report examines key regions that drive the evolution of the Continuous Catalyst Regeneration Catalyst for Oil Refinery market, offering deep insights into regional trends, growth factors, and industry developments that are influencing market performance.
- Americas
- Europe, Middle East & Africa
- Asia-Pacific
Profiling Industry Leaders Driving Catalyst Regeneration Innovation
The competitive arena for continuous catalyst regeneration is anchored by a handful of multinational catalyst producers and specialized service providers. Leading players have established integrated value chains encompassing catalyst synthesis, performance testing, and on-site regeneration services. These organizations differentiate themselves through proprietary formulations that offer enhanced lifespans, tailored regeneration protocols, and value-added analytics platforms that deliver process transparency.
Several emerging entrants are challenging incumbents by focusing on niche applications or cost-effective regeneration models. These agile companies leverage partnerships with equipment OEMs to bundle automated reactor modules with their proprietary catalysts, offering turnkey regeneration solutions that bypass traditional CAPEX cycles. Meanwhile, established firms continue to bolster their portfolios through targeted acquisitions of technology-focused startups, thereby expanding their intellectual property assets and deepening their domain expertise.
In addition, leading players are cooperating with academic and research institutions to pilot next-generation materials such as hierarchical zeolites and mesoporous alumina composites. These collaborations are accelerating time-to-market for breakthrough innovations that promise to lower regeneration temperatures, reduce energy consumption, and deliver superior resistance to coking and sintering under severe operating conditions.
This comprehensive research report delivers an in-depth overview of the principal market players in the Continuous Catalyst Regeneration Catalyst for Oil Refinery market, evaluating their market share, strategic initiatives, and competitive positioning to illuminate the factors shaping the competitive landscape.
- Albemarle Corporation
- BASF SE
- Haldor Topsoe A/S
- Clariant AG
- W. R. Grace & Co.
- Johnson Matthey plc
- Honeywell UOP LLC
- Axens SA
- Criterion Catalysts & Technologies LLC
- Sinopec Catalyst Co., Ltd.
Strategic Imperatives for Advancing Catalyst Regeneration Performance
To capitalize on the opportunities within continuous catalyst regeneration, industry leaders should prioritize strategic investments in advanced catalyst formulations and integrated digital monitoring platforms. Refiners must assess their existing regeneration infrastructure and determine whether to retrofit fluidized bed units or adopt continuous moving bed designs based on their throughput requirements and operational priorities. Collaborating with catalyst developers to co-design materials that align with specific process conditions will yield improved cycle lifetimes and lower total cost of ownership.
Supply chain resilience is another critical imperative. By establishing multi-regional sourcing arrangements and qualifying alternate suppliers for key materials such as alumina and zeolite precursors, companies can mitigate the impact of geopolitical disruptions and tariff fluctuations. Additionally, implementing predictive maintenance protocols-underpinned by machine learning algorithms that analyze sensor data-will reduce unplanned outages and optimize regeneration scheduling.
Finally, aligning regeneration strategies with corporate sustainability goals is essential. Organizations should benchmark emissions reductions achieved through energy-efficient regeneration cycles and integrate those KPIs into broader decarbonization roadmaps. Cross-functional teams involving operations, procurement, and sustainability professionals can ensure that regeneration decisions support overarching environmental and financial objectives.
Methodological Framework Underpinning Catalyst Regeneration Analysis
The analysis underpinning this report follows a rigorous, multi-stage methodological framework. Initially, secondary research was conducted on open-source documents, regulatory filings, patent databases, and technical publications to map the technological landscape and identify relevant catalysts, regeneration technologies, and applications. This was complemented by primary interviews with refining engineers, catalyst developers, and procurement leaders to validate assumptions, quantify operational pain points, and gather qualitative insights on emerging trends.
Data triangulation techniques were employed to reconcile information from disparate sources, ensuring accuracy and consistency in the segmentation by catalyst type, application, regeneration technology, form factor, and end user. A separate regional analysis was carried out to examine supply chain structures, regulatory environments, and infrastructure developments across the Americas, Europe, the Middle East and Africa, and Asia-Pacific.
Competitive benchmarking was conducted by evaluating product portfolios, technology roadmaps, patent filings, and strategic partnerships among key catalyst producers and service providers. Finally, the findings were subjected to peer review by independent experts in catalysis and refining process engineering to ensure objectivity and relevance for decision makers.
Explore AI-driven insights for the Continuous Catalyst Regeneration Catalyst for Oil Refinery market with ResearchAI on our online platform, providing deeper, data-backed market analysis.
Ask ResearchAI anything
World's First Innovative Al for Market Research
Synthesis of Insights Driving Next-Generation Catalyst Regeneration Strategies
Continuous catalyst regeneration is poised to redefine operational excellence in oil refining by delivering sustained performance, cost efficiencies, and environmental compliance. The convergence of advanced catalyst formulations, innovative regeneration technologies, and data-driven monitoring tools is accelerating this shift. Meanwhile, regulatory actions such as the 2025 US tariffs have underscored the need for resilient supply chains and adaptive procurement strategies.
Segmentation insights illuminate how material choices-from eta and gamma alumina to HZSM-5 and ultrastable Y-interact with applications across reforming, desulfurization, fluid catalytic cracking, and hydrocracking. Regeneration technology selection, catalyst form factors, and end-user priorities further nuance this landscape. Regional dynamics across the Americas, EMEA, and Asia-Pacific highlight diverse adoption patterns and investment drivers.
Key market participants are deploying both organic innovation and strategic partnerships to maintain leadership positions, while emerging players target niche applications with specialized solutions. By synthesizing these findings into actionable recommendations, the report equips stakeholders to optimize catalyst lifecycle management, align regeneration strategies with sustainability objectives, and secure durable competitive advantages.
This section provides a structured overview of the report, outlining key chapters and topics covered for easy reference in our Continuous Catalyst Regeneration Catalyst for Oil Refinery market comprehensive research report.
- Preface
- Research Methodology
- Executive Summary
- Market Overview
- Market Dynamics
- Market Insights
- Cumulative Impact of United States Tariffs 2025
- Continuous Catalyst Regeneration Catalyst for Oil Refinery Market, by Catalyst Type
- Continuous Catalyst Regeneration Catalyst for Oil Refinery Market, by Application
- Continuous Catalyst Regeneration Catalyst for Oil Refinery Market, by Regeneration Technology
- Continuous Catalyst Regeneration Catalyst for Oil Refinery Market, by Catalyst Form
- Continuous Catalyst Regeneration Catalyst for Oil Refinery Market, by End User
- Americas Continuous Catalyst Regeneration Catalyst for Oil Refinery Market
- Europe, Middle East & Africa Continuous Catalyst Regeneration Catalyst for Oil Refinery Market
- Asia-Pacific Continuous Catalyst Regeneration Catalyst for Oil Refinery Market
- Competitive Landscape
- ResearchAI
- ResearchStatistics
- ResearchContacts
- ResearchArticles
- Appendix
- List of Figures [Total: 26]
- List of Tables [Total: 324 ]
Secure Your Comprehensive Catalyst Regeneration Market Intelligence Today
Don't miss the opportunity to deepen your strategic understanding of continuous catalyst regeneration in oil refining. Reach out to Ketan Rohom, Associate Director, Sales & Marketing at 360iResearch, to secure the comprehensive market research report that will empower your organization with actionable intelligence. This report distills complex regulatory impacts, cutting-edge technological shifts, and segmentation and regional insights into a cohesive framework designed to guide your investment and operational decisions. Engage directly with our sales team to customize the scope of the analysis, gain executive-level briefings, and unlock expert guidance tailored to your refining objectives. Take decisive action now to ensure your organization remains at the forefront of process efficiency, sustainability, and competitive advantage in a rapidly evolving marketplace
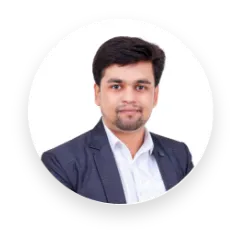
- When do I get the report?
- In what format does this report get delivered to me?
- How long has 360iResearch been around?
- What if I have a question about your reports?
- Can I share this report with my team?
- Can I use your research in my presentation?