Introduction to Next-Generation Laser Welding Advancements
Continuous laser welding machines are redefining how manufacturers join metals with unmatched precision, speed, and consistency. As industries across the automotive, aerospace, electronics, and medical sectors push the limits of design complexity and throughput, the transition from traditional welding to continuous laser processes has accelerated. This shift reflects a broader move toward automated, digitalized production lines that prioritize both quality and efficiency.
Advancements in laser sources, beam delivery systems, and closed-loop monitoring have converged to deliver welding solutions capable of handling a diverse array of materials-from carbon and stainless steels to high-conductivity copper and lightweight titanium. Leading equipment providers now offer platforms that accommodate flexible power ranges and adaptable beam profiles, enabling manufacturers to fine-tune welds for thin sheet metals as well as thick structural components. The result is a landscape where continuous laser welding machines not only boost throughput but also reduce defects and rework, driving down total cost of ownership.
Driving Forces Reshaping the Welding Equipment Landscape
The continuous laser welding market is undergoing transformative shifts driven by innovations in source technology and integration capabilities. Fiber laser systems have leapfrogged legacy CO2 equipment by delivering higher beam quality, improved electrical efficiency, and reduced maintenance overhead. Moreover, the refinement of single-mode fiber lasers is unlocking ultra-narrow weld seams suited for miniature electronics, while multi-mode variants excel in high-throughput applications such as thick steel and aluminum joining.
Beyond the laser source itself, the integration of real-time monitoring sensors and adaptive control loops has elevated process reliability. Manufacturing execution systems now link welding machines to enterprise resource planning platforms, enabling predictive maintenance and just-in-time production scheduling. Robotics and collaborative automation are further embedding continuous laser welding into flexible, reconfigurable lines capable of handling small batches to mass production runs with minimal changeover.
Sustainability considerations are also reshaping the landscape. Lower energy consumption per unit length of weld, coupled with reduced filler material usage, is bolstering the environmental case for laser processes. As a result, manufacturers are reevaluating capital investments, prioritizing systems that deliver both operational excellence and a smaller carbon footprint.
Assessing the Impact of New US Tariffs in 2025
In 2025, the introduction of revised United States tariffs on imported laser welding machinery and critical raw materials has injected fresh complexity into procurement decisions. Components such as specialized optics, beam delivery fibers, and high-precision motion stages sourced from overseas now carry additional duties, prompting manufacturers to reassess total landed costs and supplier portfolios.
Many end-users have responded by pursuing dual-sourcing strategies, combining domestic machine builders with established international partners to balance cost, lead time, and technology access. Some have accelerated plans to localize assembly operations, viewing nearshoring as a hedge against further tariff escalations. Furthermore, the shifting cost structure has spurred a wave of design modifications aimed at reducing reliance on tariff-sensitive imports without compromising performance or reliability.
While higher equipment costs have compressed short-term margins for both OEMs and system integrators, the trend is also fostering innovation. Suppliers are investing in modular designs that simplify upgrades and serviceability, effectively lowering lifecycle expenses and insulating customers from future trade disruptions. As a result, the market is moving toward a more resilient and adaptable model that balances geopolitical risks with technological advancement.
Deep Dive into Segment-Specific Market Dynamics
Segment performance in the continuous laser welding machine market varies considerably by laser source, power rating, material compatibility, and end-use application. Carbon dioxide laser platforms, once dominant for sheet metal processing, are ceding ground to fiber lasers, especially single-mode variants that deliver ultrafine welds in high-precision electronics. Multi-mode fiber lasers, by contrast, excel in thicker section welding for automotive and heavy equipment manufacturing, thanks to their higher average power and beam flexibility. Nd:YAG systems remain relevant for niche medical and jewelry applications where beam stability and short-pulse control are critical.
Power range dynamics reveal that mid-power systems in the 2-6 kilowatt band serve as the workhorse for general manufacturing. Within this bracket, 2-4 kilowatt machines command widespread adoption for thin aluminum and stainless-steel assemblies, while the 4-6 kilowatt class scales to moderate thickness materials such as mild steel frameworks. Lower-power units under 2 kilowatts, particularly the 500-1,000 watt and 1,000-2,000 watt increments, are burgeoning in micro-electronics and consumer device fabrication. Conversely, high-power lasers above 6 kilowatts, including 6-10 kilowatt and ultra-high-power systems exceeding 10 kilowatts, are gaining traction in heavy-duty sectors like aerospace structural bonding and large-scale shipbuilding.
Material versatility drives adoption across multiple industries. Aluminum welding applications split between cast and forged alloys, each demanding distinct beam parameters to counteract high reflectivity. Copper systems have advanced to address the challenges of ETP grades and oxygen-free variants, leveraging beam shaping and pre-heat modules to ensure consistent fusion. Steel welding spans carbon grade frameworks in construction to high-grade stainless-steel tubing in pharmaceutical and food-grade equipment. Titanium processing, particularly in aerospace and medical implants, relies on grade 2 for corrosion-resistant structural parts and grade 5 for high-strength components.
Applications segmentation underscores the market’s diversity. Aerospace manufacturers leverage laser welding for precision structural bonding and fuel system assemblies. Automotive producers deploy laser systems for bodyin-white construction, engine subassemblies, and emission control system welding. In electronics, consumer device casings and printed circuit board assemblies benefit from low-heat inputs and minimal distortion. Jewelry craftsmanship utilizes controlled energy delivery to join precious metals without deforming intricate details, while medical device fabricators employ pulsed and continuous laser modes to produce leak-tight microfluidic and implantable components.
This comprehensive research report categorizes the Continuous Laser Welding Machine market into clearly defined segments, providing a detailed analysis of emerging trends and precise revenue forecasts to support strategic decision-making.
- Laser Type
- Power Range
- Material
- Application
Regional Market Performance and Strategic Opportunities
Regional performance in the continuous laser welding sector reflects each area’s industrial priorities and supply chain strengths. In the Americas, robust automotive manufacturing in North America and burgeoning electronics fabrication in Central and South America create a steady demand for mid-power fiber laser systems and integrated robotic cells. Local OEMs and system integrators are expanding service networks to support clients seeking rapid deployment and turnkey solutions.
Across Europe, the Middle East, and Africa, the emphasis lies on high-precision applications in aerospace and luxury automotive segments. European machine builders leverage advanced beam shaping, closed-loop quality controls, and digital twins to meet stringent defect-free mandates. Middle Eastern infrastructure projects are integrating laser welding into large-scale fabrication yards, while African manufacturers are gradually adopting continuous laser technology to modernize legacy welding workshops.
Asia-Pacific remains the largest growth engine, driven by its electronics, automotive, and medical device clusters. Manufacturers in East Asia lead in the adoption of ultra-low power systems for consumer electronics, while Southeast Asian plants are rapidly automating body-in-white production lines. In South Asia, rising healthcare investment is propelling demand for laser welding solutions that deliver sterile, precision joints for surgical instruments and implantables.
This comprehensive research report examines key regions that drive the evolution of the Continuous Laser Welding Machine market, offering deep insights into regional trends, growth factors, and industry developments that are influencing market performance.
- Americas
- Europe, Middle East & Africa
- Asia-Pacific
Competitive Landscape and Leading Innovators
The competitive landscape features a blend of global technology leaders and agile regional specialists. Major fiber laser innovators have broadened their portfolios to include turnkey welding cells, integrating coaxial beam delivery, vision systems, and software analytics. These firms have prioritized open architecture controls to enable seamless integration with third-party automation and enterprise software.
Regional players differentiate through value-added engineering services and localized support. Some companies focus on rapid machine customization to cater to specific alloy welding challenges or application niches such as microelectronics and medical instrumentation. Others emphasize their service infrastructure, offering on-site calibration, preventive maintenance contracts, and remote diagnostic tools to minimize downtime.
Strategic alliances between laser source manufacturers and robotics integrators are also reshaping the market. By co-developing combined hardware and software ecosystems, these partnerships accelerate time-to-market for advanced welding solutions. Meanwhile, aftermarket service providers are introducing subscription-based models for consumables, software updates, and performance analytics, fostering recurring revenue streams and deeper customer engagement.
This comprehensive research report delivers an in-depth overview of the principal market players in the Continuous Laser Welding Machine market, evaluating their market share, strategic initiatives, and competitive positioning to illuminate the factors shaping the competitive landscape.
- TRUMPF GmbH + Co. KG
- IPG Photonics Corporation
- Coherent, Inc.
- Han's Laser Technology Industry Group Co., Ltd.
- Jenoptik AG
- Prima Industrie S.p.A.
- Amada Co., Ltd.
- Panasonic Corporation
- Mitsubishi Electric Corporation
- Bystronic Laser AG
Strategic Recommendations for Market Leadership
To secure a leadership position, equipment providers should accelerate investments in fiber laser research and development, refining single-mode beam quality and boosting multi-mode power efficiency. Embracing open protocol architectures will allow smoother integration with robotics and digital factory platforms, reducing adoption barriers for end-users.
Manufacturers must also fortify their global service networks. Establishing regional centers of excellence for machine calibration, preventive maintenance, and operator training will enhance customer satisfaction and loyalty. In parallel, adopting subscription and outcome-based pricing models can shift customer focus from upfront capital costs to long-term productivity gains.
Sustainability will remain a key differentiator. Leaders should introduce energy-recovery systems, recyclable optics modules, and packaged solutions that minimize consumable waste. Collaboration with materials suppliers to co-develop weld-ready alloys can further reduce defect rates and streamline process qualification. Ultimately, organizations that integrate technological innovation, responsive support, and environmental stewardship will capture the greatest share of an evolving market.
Comprehensive Research Approach and Data Triangulation
This analysis draws on a multi-tiered research approach combining primary interviews with key equipment manufacturers, system integrators, and end-users across major industries. Secondary data were sourced from industry journals, trade associations, technical white papers, and patent databases to ensure a comprehensive view of technology trends and competitive activity.
Quantitative data were validated through cross-referencing shipment records, trade statistics, and public financial disclosures. We applied data triangulation techniques to reconcile discrepancies and ensure consistency. Market segmentation frameworks were developed to reflect laser source, power range, material, and application dimensions, enabling nuanced insight into performance drivers and adoption patterns.
Qualitative inputs underwent expert panel review, incorporating feedback from welding engineers, automation specialists, and procurement leaders. Statistical sampling and confidence interval analyses underpin our conclusions, while proprietary forecasting models simulate scenario impacts such as tariff shifts and supply chain disruptions. The research process adheres to rigorous quality checks and transparent documentation standards.
Explore AI-driven insights for the Continuous Laser Welding Machine market with ResearchAI on our online platform, providing deeper, data-backed market analysis.
Ask ResearchAI anything
World's First Innovative Al for Market Research
Synthesis and Future Perspectives
Continuous laser welding machines are at the forefront of modern manufacturing, bridging the gap between precision engineering and high-volume production. Fiber laser sources have rapidly ascended to dominance, propelled by their adaptability and efficiency gains. Market dynamics remain sensitive to geopolitical factors, notably tariff regimes that influence supply chain strategies and equipment costs.
Segmentation analysis reveals a balanced ecosystem where mid-power machines anchor mainstream manufacturing, low-power units enable microfabrication, and ultra-high-power systems serve capital-intensive industries. Material and application diversity further underscore the technology’s versatility. Regional insights point to a matured landscape in Europe, resurgent growth in the Americas, and leadership momentum in Asia-Pacific.
Looking ahead, the interplay between technological innovation, service models, and sustainability objectives will determine which players flourish. Organizations that anticipate customer needs, invest in modular platforms, and embed digital services will capture a disproportionate share of opportunities. This executive summary offers a strategic roadmap for stakeholders seeking to navigate the evolving world of continuous laser welding.
This section provides a structured overview of the report, outlining key chapters and topics covered for easy reference in our Continuous Laser Welding Machine market comprehensive research report.
- Preface
- Research Methodology
- Executive Summary
- Market Overview
- Market Dynamics
- Market Insights
- Cumulative Impact of United States Tariffs 2025
- Continuous Laser Welding Machine Market, by Laser Type
- Continuous Laser Welding Machine Market, by Power Range
- Continuous Laser Welding Machine Market, by Material
- Continuous Laser Welding Machine Market, by Application
- Americas Continuous Laser Welding Machine Market
- Europe, Middle East & Africa Continuous Laser Welding Machine Market
- Asia-Pacific Continuous Laser Welding Machine Market
- Competitive Landscape
- ResearchAI
- ResearchStatistics
- ResearchContacts
- ResearchArticles
- Appendix
- List of Figures [Total: 24]
- List of Tables [Total: 635 ]
Engage Our Associate Director for Exclusive Market Insights
To explore the full breadth of our continuous laser welding machine analysis, connect with Ketan Rohom, Associate Director of Sales & Marketing. He brings deep industry insight and can guide you through the report’s comprehensive findings, strategic recommendations, and custom data solutions. Engage today to secure your competitive edge with actionable intelligence tailored to your organization’s specific needs.
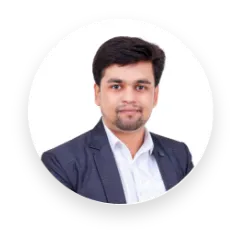
- When do I get the report?
- In what format does this report get delivered to me?
- How long has 360iResearch been around?
- What if I have a question about your reports?
- Can I share this report with my team?
- Can I use your research in my presentation?