The Copper Additive Manufacturing Market size was estimated at USD 4.43 billion in 2024 and expected to reach USD 4.74 billion in 2025, at a CAGR 7.41% to reach USD 6.80 billion by 2030.

Introduction to the Copper Additive Revolution
Copper additive manufacturing stands at the forefront of industrial transformation, combining the exceptional properties of copper with the agility of additive processes. As demand intensifies for lighter, more complex, and thermally efficient components, manufacturers are adopting innovative methods to exploit copper’s high thermal and electrical conductivity. This introduction outlines the motivations driving market growth, from the pursuit of faster prototyping cycles to the production of end-use parts that meet rigorous performance standards. Stakeholders across aerospace, automotive, electronics, and medical sectors are recognizing additive manufacturing’s capacity to reduce lead times and enhance design freedom when working with copper and its alloys.
Recent technological advancements have addressed historical challenges related to copper’s high reflectivity and thermal conductivity, enabling processes such as laser powder bed fusion and binder jetting to deliver precise geometry and consistent quality. As material science continues to refine copper feedstocks and process parameters, opportunities are emerging for applications ranging from heat exchangers to electric vehicle components. This introduction establishes the context for exploring how the interplay of innovation, regulation, and strategic partnerships shapes the copper additive manufacturing market today.
Fundamental Shifts Reshaping the Manufacturing Landscape
The landscape of copper additive manufacturing is undergoing transformative shifts, driven by breakthroughs in equipment capabilities, materials engineering, and digital integration. Manufacturers are increasingly deploying hybrid systems that combine subtractive and additive techniques to achieve complex geometries while maintaining tight tolerances. Advances in powder atomization and surface treatment have expanded the range of copper-based alloys compatible with high-energy beam processes, paving the way for parts that balance conductivity, strength, and durability.
Simultaneously, digital process control, underpinned by machine learning and real-time monitoring, is elevating yield rates and reducing waste. By leveraging in situ sensing and closed-loop feedback, producers can detect defects as they form, adjusting parameters on the fly to ensure consistent quality. These technological enhancements are complemented by a growing ecosystem of software platforms that optimize build orientation, support structures, and thermal management in virtual simulations before any physical layer is deposited.
The convergence of these developments is redefining supply chains. Tier-one suppliers are forging partnerships with specialized service bureaus to decentralize production and increase responsiveness. Meanwhile, the proliferation of standardized metal powders and certification schemes is instilling greater confidence among end users, accelerating adoption in regulated industries such as aerospace and medical. This section unpacks the critical trends reshaping how copper additive manufacturing is practiced and the value it delivers.
Evaluating the Cumulative Impact of US Tariffs in 2025
The imposition of cumulative tariffs by the United States in 2025 has introduced new considerations for copper additive manufacturing stakeholders. By targeting key raw material imports and finished metal components, these duties have influenced supply chain strategies, cost structures, and regional sourcing decisions. Manufacturers reliant on imported copper powders and pre-alloyed feedstocks have responded by seeking domestic alternatives, investing in local powder production facilities, and renegotiating contracts to mitigate the impact of duty escalations.
Consequently, the landscape of supplier partnerships is evolving. Firms are prioritizing integrated procurement agreements that bundle raw materials, equipment maintenance, and technical support, thereby cushioning the effect of tariff-induced price fluctuations. Additionally, end users are assessing total cost of ownership more rigorously, balancing higher upfront material costs against savings derived from reduced lead times and lower inventory carrying costs when materials are sourced domestically.
At the same time, policy-driven incentives for reshoring critical manufacturing capabilities have gained traction, particularly in strategic sectors like defense and energy. These programs offer grants and tax credits to underwrite the establishment of advanced metal additive facilities, further reshaping capital allocation decisions. This section examines how the 2025 tariff environment has catalyzed strategic realignments across the copper additive manufacturing ecosystem.
Deep Dive into Market Segmentation for Copper AM
The market segmentation for copper additive manufacturing reveals nuanced preferences and growth trajectories across multiple axes. When processes are compared, binder jetting is recognized for its high throughput and cost-effective powder utilization, while direct energy deposition addresses repair and large-part construction needs, and powder bed fusion offers superior surface finish and geometric resolution. Material type segmentation distinguishes pure copper, valued for its unmatched conductivity, from copper alloys, which are further differentiated into copper-aluminum compositions prized for their strength-to-weight ratios and copper-tin blends known for enhanced wear resistance.
Service type analysis shows a clear divide between in-house manufacturing teams seeking full control over intellectual property and quality, and outsourced manufacturing providers offering specialized expertise. Within outsourced services, contract manufacturers are often engaged for high-volume runs under defined specifications, whereas professional service providers deliver bespoke consulting and post-processing capabilities. Application-driven segmentation spans the production of functional parts requiring end-use readiness, rapid prototyping to validate new designs, research and development efforts focused on material testing and process development, and tooling applications where thermal management and part longevity are critical.
Finally, end-use industries illustrate the breadth of opportunity. In aerospace and defense, manufacturers leverage additive designs for aircraft components and satellite subsystems. Automotive segments include electric vehicle powertrain parts and legacy engine components. The electrical and electronics domain capitalizes on conductive components and heat sinks to manage thermal loads. Meanwhile, medical and dental applications range from custom dental crowns to load-bearing orthopedic implants. This segmentation framework underscores the interdependence of process, material, service, application, and end-use in charting the market’s path.
This comprehensive research report categorizes the Copper Additive Manufacturing market into clearly defined segments, providing a detailed analysis of emerging trends and precise revenue forecasts to support strategic decision-making.
- Manufacturing Process
- Material Type
- Service Type
- Application
- End-Use Industry
Regional Dynamics Driving Copper Additive Manufacturing Adoption
Regional dynamics exert a powerful influence on adoption patterns and investment flows in copper additive manufacturing. In the Americas, a convergence of regulatory support and private sector funding has bolstered domestic powder production and the deployment of advanced metal printers. The presence of leading aerospace primes and a mature defense supply chain underpins demand for high-value, mission-critical components, while an expanding electric vehicle sector drives growth in powertrain and thermal management applications.
Across Europe, the Middle East, and Africa, a diverse array of national initiatives has emerged to cultivate additive ecosystems. Collaborative research consortia in Europe focus on harmonizing standards and accelerating certification for copper parts in aviation and medical implants. In the Middle East, sovereign wealth funds are channeling investments into specialized manufacturing hubs. Africa’s additive journey remains nascent but shows promise in leveraging copper’s recyclability and local capacity building to support energy infrastructure projects.
The Asia-Pacific region stands out for its rapid integration of China, Japan, South Korea, and Southeast Asian nations into the copper additive manufacturing value chain. Subsidies aimed at reducing dependence on imported metals have spurred the construction of large-scale powder facilities and high-volume printing centers. Local equipment manufacturers are scaling up to contest established global OEMs, while electronics and automotive conglomerates pioneer novel copper-based cooling solutions and lightweight structural parts. These regional insights highlight the strategic imperatives and collaborative models driving market expansion.
This comprehensive research report examines key regions that drive the evolution of the Copper Additive Manufacturing market, offering deep insights into regional trends, growth factors, and industry developments that are influencing market performance.
- Americas
- Europe, Middle East & Africa
- Asia-Pacific
Competitive Landscape: Key Players and Strategic Moves
The competitive landscape is defined by a balance between established equipment OEMs, specialist powder producers, and agile service bureaus. Global system manufacturers continually refine laser source integration, motion control accuracy, and process monitoring to maintain their leadership in metal powder bed and directed energy platforms. Simultaneously, independent powder suppliers invest heavily in particle size distribution control and alloy customization to meet evolving specifications for conductivity and mechanical performance.
Service bureaus and contract manufacturers carve out niches by offering end-to-end solutions, from design for additive manufacturing consultancy to post-processing and quality certification. Strategic collaborations between equipment vendors and service providers have emerged to bundle hardware sales with guaranteed material supply and technical training, reducing barriers for new adopters. Additionally, software developers specializing in print preparation, build simulation, and thermal modeling have become indispensable partners, enabling users to optimize build strategies and minimize trial-and-error.
Mergers and acquisitions play a pivotal role in shaping market structure, allowing firms to vertically integrate across feedstock, hardware, and services. Alliances with research institutions further catalyze innovation in copper powder formulations and process parameter libraries. This section dissects the strategies that leading companies employ to secure competitive advantage and capture expanding market share in copper additive manufacturing.
This comprehensive research report delivers an in-depth overview of the principal market players in the Copper Additive Manufacturing market, evaluating their market share, strategic initiatives, and competitive positioning to illuminate the factors shaping the competitive landscape.
- Additive Industries b.v.
- Allegheny Technologies Incorporated
- 3D Systems Corporation
- Bright Laser Technologies Co., Ltd
- Carpenter Technology Corporation
- Advanced Powder & Coatings, Inc.
- Desktop Metal, Inc.
- DMG MORI AG
- EOS GmbH
- ExOne Company, Inc.
- General Electric Company
- Höganäs AB
- L3Harris Technologies, Inc
- Markforged Inc.
- Materion Corporation
- Optomec, Inc.
- Renishaw plc
- Sandvik AB
- Sciaky Inc.
- SLM Solutions Group AG
- Southern Copper Corporation
- Stratasys, Ltd.
- TRUMPF Group
- Velo3D Inc.
- Xact Metal Inc.
Strategic Recommendations for Industry Leaders
Industry leaders should prioritize the development of robust materials roadmaps that align copper alloy innovation with targeted applications. By collaborating with universities and government labs, organizations can accelerate alloy optimization for specific performance criteria. Investing in digital twins and in situ monitoring technologies will further enhance process reliability, reducing scrap rates and enabling rapid scale-up from prototyping to production.
To mitigate tariff-related cost pressures, firms should diversify supply chains by establishing regional powder production partnerships and exploring alternative feedstock sources. Formalizing long-term agreements with contract manufacturers and service bureaus can stabilize pricing and delivery timelines. In parallel, companies must deepen their expertise in design for additive manufacturing methodologies to extract maximum value from copper’s unique thermal-electrical properties, thereby differentiating their offerings in competitive markets.
Strategic alliances with software providers are essential to integrate workflow automation and predictive maintenance capabilities, ensuring consistent part quality and throughput. Finally, targeted investments in workforce training and certification will cultivate the specialized talent pool necessary for sustaining advanced metal additive operations. These recommendations equip industry leaders with a clear path to drive growth and secure technological leadership.
Rigorous Methodology Underpinning the Analysis
The analysis underpinning this report draws on a comprehensive blend of primary and secondary research. Primary insights were gathered through in-depth interviews with senior executives at equipment manufacturers, powder suppliers, contract service providers, and end-use industry leaders. These dialogues provided qualitative context on strategic priorities, technology roadmaps, and adoption drivers. Secondary research encompassed a review of industry white papers, patent filings, regulatory filings, and trade association publications to quantify technology maturation and investment trends.
Data on regional manufacturing capacities and policy frameworks were compiled from government reports and cross-validated with proprietary databases. Market participant financial statements and public disclosures informed assessments of competitive positioning and growth strategies. To ensure methodological rigor, triangulation techniques were employed, correlating interview feedback with observed market activity. All sources underwent strict credibility checks, and findings were peer-reviewed by domain experts to maintain objectivity.
This blended approach yields a multidimensional perspective on copper additive manufacturing, balancing strategic foresight with tangible operational insights. The structured framework of process, material, service, application, and regional analysis serves as the foundation for the report’s conclusions and recommendations.
Explore AI-driven insights for the Copper Additive Manufacturing market with ResearchAI on our online platform, providing deeper, data-backed market analysis.
Ask ResearchAI anything
World's First Innovative Al for Market Research
Concluding Reflections on Copper Additive Manufacturing
Copper additive manufacturing is poised to redefine how industries approach complex part production, moving beyond traditional casting and machining paradigms. As material formulations advance and process control technologies mature, the capacity to deliver high-performance copper components at scale draws nearer. Strategic realignments catalyzed by tariff pressures and regional investment incentives will continue to reshape supply chain architectures, favoring localized production clusters supported by integrated technology ecosystems.
Future growth will hinge on the successful integration of digital tools, from predictive analytics to automated quality assurance, enabling manufacturers to transition from pilot projects to full-scale operations with minimal downtime. Cross-sector collaboration will remain vital, with partnerships between OEMs, service providers, and research institutions driving the co-development of application-specific alloys and certification protocols. Stakeholders that embrace open innovation and align materials roadmaps with end-user requirements will unlock the greatest value in copper additive manufacturing.
In conclusion, the copper additive manufacturing market is at an inflection point where strategic investment, technological innovation, and regulatory adaptation converge to create new pathways for industrial competitiveness. Those who navigate these currents decisively will shape the future of electrically and thermally optimized components across critical sectors.
This section provides a structured overview of the report, outlining key chapters and topics covered for easy reference in our Copper Additive Manufacturing market comprehensive research report.
- Preface
- Research Methodology
- Executive Summary
- Market Overview
- Market Dynamics
- Market Insights
- Cumulative Impact of United States Tariffs 2025
- Copper Additive Manufacturing Market, by Manufacturing Process
- Copper Additive Manufacturing Market, by Material Type
- Copper Additive Manufacturing Market, by Service Type
- Copper Additive Manufacturing Market, by Application
- Copper Additive Manufacturing Market, by End-Use Industry
- Americas Copper Additive Manufacturing Market
- Europe, Middle East & Africa Copper Additive Manufacturing Market
- Asia-Pacific Copper Additive Manufacturing Market
- Competitive Landscape
- ResearchAI
- ResearchStatistics
- ResearchContacts
- ResearchArticles
- Appendix
- List of Figures [Total: 26]
- List of Tables [Total: 544 ]
Engage Our Associate Director to Access the Full Report
To secure a comprehensive perspective on copper additive manufacturing and unlock tailored insights for strategic planning, reach out directly to Ketan Rohom, Associate Director, Sales & Marketing at 360iResearch. Ketan will guide you through the report’s depth, elaborate on specific data, and discuss licensing options that fit your organizational objectives. Engage with an expert who understands the nuances of this market and is prepared to help you leverage the findings for competitive advantage. Elevate your decision-making with personalized support from a seasoned professional today.
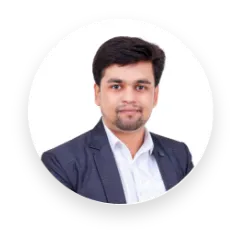
- How big is the Copper Additive Manufacturing Market?
- What is the Copper Additive Manufacturing Market growth?
- When do I get the report?
- In what format does this report get delivered to me?
- How long has 360iResearch been around?
- What if I have a question about your reports?
- Can I share this report with my team?
- Can I use your research in my presentation?