1. Introduction to the Evolving Copper Foil Landscape
In recent years, copper foil has emerged as a critical enabler for next-generation printed circuit boards (PCBs), powering everything from high-speed communication devices to advanced automotive electronics. As the backbone of multilayer PCB fabrication, copper foil delivers essential electrical conductivity, thermal management, and mechanical stability required by increasingly complex circuit designs. This introduction provides context for the current market environment, highlighting the convergence of technological advances, evolving industry demands, and regulatory influences that are shaping the copper foil landscape.
PCB manufacturers are under growing pressure to deliver thinner, lighter, and higher-performance solutions. The proliferation of 5G infrastructure, electric vehicles, and wearable devices has driven demand for ultra-thin and high-reliability copper foils. Simultaneously, global supply chain constraints and shifting trade policies have introduced new complexities for raw material sourcing and cost management. Stakeholders across the value chain-from raw material suppliers and copper foil producers to PCB fabricators and end users-must navigate these intersecting forces to maintain competitiveness and drive innovation.
This executive summary distills key market dynamics, examines transformative shifts, evaluates tariff impacts, and presents segmentation and regional insights. It also highlights leading players, recommends strategic actions, and offers a forward-looking perspective to support informed decision-making in this vital segment of the electronics materials industry.
2. Transformative Shifts Reshaping the Copper Foil Market
The copper foil market is undergoing transformative shifts fueled by rapid technological innovation and changing end-user requirements. The miniaturization of electronic components has increased demand for ultra-thin and high-performance electrodeposited copper foil, while large-format applications continue to rely on rolled copper foil featuring annealed or stress-relief properties. Advanced PCB packaging methods, including embedded components and high-density interconnects, are pushing producers toward thinner and more uniform thickness profiles.
Meanwhile, the advent of 5G networks and the automotive industry’s electrification trajectory have elevated performance attributes such as thermal conductivity and tensile strength. Manufacturers are increasingly prioritizing copper foil variants with high adhesion strength and specialized surface textures to support improved heat dissipation in power modules and autonomous driving systems. These technological imperatives coincide with a broader shift toward sustainable production methods, encouraging adoption of greener electrodeposition and rolling procedures.
Supply chain resilience has become equally critical. Companies are diversifying raw material sources and strengthening regional production capabilities to mitigate the risks associated with geopolitical tensions and logistical bottlenecks. Digital transformation, including real-time process monitoring and predictive maintenance, is enhancing operational efficiency and quality control, enabling producers to deliver copper foil variants tailored to exacting specifications.
3. Cumulative Impact of United States Tariffs on Copper Foil in 2025
In 2025, the United States extended its tariff regime on copper foil imports to address trade imbalances and support domestic manufacturing. This policy adjustment levied additional duties on key import categories, prompting global suppliers to reassess pricing strategies and regional distribution networks. The tariff increase contributed to higher input costs for PCB fabricators, which in turn accelerated cost-recovery efforts through product premiumization and supply chain realignment.
Suppliers responded by exploring tariff mitigation strategies, such as establishing tolling agreements and relocating finishing operations to tariff-exempt zones. Some producers diversified their geographic footprint, expanding capacity in Asia-Pacific locations less affected by U.S. duties, while others sought preferential trade terms through regional trade agreements. These moves have fostered a more fragmented supply landscape, where regional pricing differentials and lead-time considerations play a decisive role in procurement decisions.
Despite the cost pressures, the tariff environment has catalyzed innovation in production efficiency. Producers intensified investments in process optimization and waste reduction to contain cost escalations. Concurrently, downstream manufacturers accelerated development of higher-value copper foil offerings-such as high-performance electrodeposited variants and ultra-thin rolled products-to justify price adjustments and maintain margin integrity.
4. Key Segmentation Insights Across Copper Foil Types and Applications
Analysis across multiple segmentation criteria reveals nuanced demand patterns. Type segmentation shows that electrodeposited copper foil, particularly high-performance electrodeposited grades, is gaining prominence for advanced multilayer PCBs, while stress-relief rolled foil is preferred for large-format boards requiring superior formability. Thickness segmentation highlights a surge in ultra-thin copper foil demand, especially sub-0.5 micron variants used in miniaturized wearable devices and foldable electronics, while standard and thin foils continue to serve mainstream consumer and industrial segments.
Application segmentation indicates strong growth in automotive electronics driven by advanced driver assistance and battery management systems, alongside steady uptake in consumer electronics for smartphones and wearables. Industrial equipment applications, such as power management modules, also rely on copper foil with enhanced thermal conductivity. Production method segmentation underscores the coexistence of electrodeposition processes for precision control and rolling procedures for cost-effective large-scale output.
Material characteristic segmentation reveals that high adhesion strength and matte surface textures are in greater demand for rigid-flex PCBs, while smooth surface finishes facilitate fine line etching in high-density interconnects. End-user industry segmentation shows that aerospace & defense applications, particularly aviation systems, require copper foil with rigorous performance attributes, while telecommunications equipment benefits from wide-width variants exceeding 600 mm for backplane manufacture. Performance attribute segmentation confirms that enhanced tensile strength and high thermal conductivity grades are critical for power modules and high-speed data transmission. Width segmentation indicates that foil below 300 mm serves precision PCB fabrication, whereas widths above 600 mm cater to large panels and backplanes.
This comprehensive research report categorizes the Copper Foil for PCB market into clearly defined segments, providing a detailed analysis of emerging trends and precise revenue forecasts to support strategic decision-making.
- Type
- Thickness
- Application
- Production Method
- Material Characteristics
- End-User Industry
- Performance Attributes
- Width
5. Key Regional Insights Driving Market Dynamics
Regional dynamics demonstrate distinct growth drivers and challenges. In the Americas, proximity to semiconductor and automotive hubs in the United States and Mexico fuels demand for both standard and advanced copper foils. Local production expansions and nearshoring initiatives help mitigate tariff impacts and shorten lead times. Meanwhile, Europe, Middle East & Africa present a diverse landscape, with Western Europe focusing on high-performance foil for industrial automation and renewable energy systems, while Middle Eastern investments in telecommunications infrastructure drive demand for ultra-thin and wide-width variants.
In Asia-Pacific, the epicenter of electronics manufacturing, rapid adoption of 5G, consumer electronics innovations, and increasing EV production underpin robust growth in both electrodeposited and rolled copper foils. Manufacturers in China, Taiwan, and South Korea are ramping up capacity to meet localized needs and capitalize on export opportunities. Across these regions, evolving trade agreements and strategic alliances continue to shape competitive positioning, with companies aligning production footprints to leverage preferential trade terms and local incentives.
This comprehensive research report examines key regions that drive the evolution of the Copper Foil for PCB market, offering deep insights into regional trends, growth factors, and industry developments that are influencing market performance.
- Americas
- Asia-Pacific
- Europe, Middle East & Africa
6. Key Companies Shaping the Copper Foil Industry
The competitive landscape features established players and agile challengers driving innovation and capacity expansion. Chang Chun Group leverages its integrated chemical capabilities to optimize adhesion properties, while Circuit Foil Luxembourg focuses on premium rolled copper foil for high-frequency applications. Civen Metal Material (Shanghai) Co., Ltd. invests in ultra-thin electrodeposited processes tailored to wearable electronics. Corinth Aluminium differentiates through wide-width foil production for large-scale backplanes.
Doosan Corporation Electro-Materials BG emphasizes sustainable electrodeposition technologies, and Furukawa Electric Co., Ltd. strengthens its footprint with advanced surface treatments. Hitachi Metals, Ltd. integrates value-added services, including slitting and lamination, to meet custom specifications. JX Nippon Mining & Metals Corporation capitalizes on raw material synergies to enhance supply chain resilience. Kingboard Copper Foil Holdings Limited focuses on capacity expansion in Asia-Pacific, while Lintec Corporation develops high adhesion matte foils for flexible PCBs.
Mitsui Mining & Smelting Co., Ltd. advances high thermal conductivity grades for power electronics, and Nan Ya Plastics Corporation collaborates with system integrators on embedded component solutions. These companies collectively shape market standards through R&D investments, strategic partnerships, and regional production realignment, reinforcing their positions in both commodity and specialty segments.
This comprehensive research report delivers an in-depth overview of the principal market players in the Copper Foil for PCB market, evaluating their market share, strategic initiatives, and competitive positioning to illuminate the factors shaping the competitive landscape.
- Chang Chun Group
- Circuit Foil Luxembourg
- Civen Metal Material (Shanghai) Co., Ltd.
- Corinth Aluminium
- Doosan Corporation Electro-Materials BG
- Furukawa Electric Co., Ltd.
- Hitachi Metals, Ltd.
- JX Nippon Mining & Metals Corporation
- Kingboard Copper Foil Holdings Limited
- Lintec Corporation
- Mitsui Mining & Smelting Co., Ltd.
- Nan Ya Plastics Corporation
7. Actionable Recommendations for Industry Leaders
Industry leaders must adopt a proactive, multi-pronged strategy to navigate evolving market conditions. First, diversifying production footprints across tariff-advantaged regions can mitigate cost pressures and supply chain disruptions. Establishing tolling arrangements and joint ventures in regions with favorable trade terms ensures reliable access to high-performance electrodeposited and rolled foils.
Second, intensifying R&D efforts to develop ultra-thin copper foils with superior adhesion and optimized surface textures will address the accelerating demand from miniaturized and high-frequency applications. Collaborative innovation partnerships with equipment suppliers and end-user OEMs can accelerate time-to-market for specialty foil grades.
Third, integrating digital manufacturing solutions-such as in-line thickness monitoring and predictive maintenance-will drive yield improvements and reduce process variability. Implementing circular economy initiatives, including electrolyte recycling and scrap recovery, can enhance cost efficiency and sustainability credentials.
Fourth, forging closer ties with strategic end-users in automotive, telecommunications, and aerospace sectors enables co-development of tailored foil solutions. Finally, building resilience through scenario planning and dynamic pricing models will empower businesses to respond swiftly to tariff fluctuations and raw material cost volatility.
Explore AI-driven insights for the Copper Foil for PCB market with ResearchAI on our online platform, providing deeper, data-backed market analysis.
Ask ResearchAI anything
World's First Innovative Al for Market Research
8. Conclusion: Charting the Future of Copper Foil for PCBs
The copper foil sector stands at a pivotal juncture, driven by technological imperatives, regulatory dynamics, and shifting consumption patterns. Companies that embrace strategic diversification, innovation-led differentiation, and operational excellence will secure a competitive edge. By aligning production capacity with regional demand centers, advancing material science capabilities, and investing in digital transformation, stakeholders can meet the rising performance requirements of modern PCBs while maintaining cost discipline.
As market boundaries expand into emerging applications-such as 5G network infrastructure, electric mobility, and flexible electronics-the capacity to pivot quickly and collaborate across the ecosystem will define success. A forward-looking approach that balances growth ambitions with sustainability objectives will not only optimize profitability but also reinforce long-term resilience in an increasingly complex marketplace.
This section provides a structured overview of the report, outlining key chapters and topics covered for easy reference in our Copper Foil for PCB market comprehensive research report.
- Preface
- Research Methodology
- Executive Summary
- Market Overview
- Market Dynamics
- Market Insights
- Cumulative Impact of United States Tariffs 2025
- Copper Foil for PCB Market, by Type
- Copper Foil for PCB Market, by Thickness
- Copper Foil for PCB Market, by Application
- Copper Foil for PCB Market, by Production Method
- Copper Foil for PCB Market, by Material Characteristics
- Copper Foil for PCB Market, by End-User Industry
- Copper Foil for PCB Market, by Performance Attributes
- Copper Foil for PCB Market, by Width
- Americas Copper Foil for PCB Market
- Asia-Pacific Copper Foil for PCB Market
- Europe, Middle East & Africa Copper Foil for PCB Market
- Competitive Landscape
- ResearchAI
- ResearchStatistics
- ResearchContacts
- ResearchArticles
- Appendix
- List of Figures [Total: 32]
- List of Tables [Total: 1073 ]
9. Call to Action: Secure Your Comprehensive Market Study
For a deeper dive into comprehensive market analysis, strategic insights, and actionable opportunities, reach out to Ketan Rohom, Associate Director, Sales & Marketing. Connect today to secure your copy of the full market research report and empower your organization with the intelligence needed to capitalize on evolving copper foil dynamics.
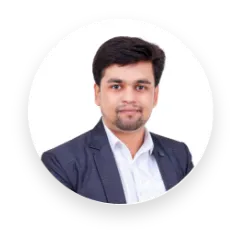
- When do I get the report?
- In what format does this report get delivered to me?
- How long has 360iResearch been around?
- What if I have a question about your reports?
- Can I share this report with my team?
- Can I use your research in my presentation?