Setting the Stage for Precision in Copper Foil Inspection
Precision in copper foil manufacturing plays a pivotal role across industries that demand consistent electrical conductivity and mechanical reliability. As product designs evolve toward greater miniaturization and higher energy densities, even microscopic surface defects can cascade into significant failures. Manufacturers and quality engineers are therefore under increasing pressure to detect and quantify irregularities in copper foils with real-time accuracy. This report delves into the surface defect detection system market, examining current capabilities, technological advances, and key market drivers. By analyzing the integration of advanced profiling modalities, non-destructive testing techniques, and inline inspection architectures, it provides a holistic view of how defect detection solutions enhance yield and reduce downstream failures. Stakeholders will gain insights into the interplay between equipment performance and production throughput, uncovering how strategic investments in accurate surface analysis yield measurable returns in cost savings and product reliability. Moreover, as regulatory requirements tighten and end-use applications span from consumer electronics to aerospace, the need for standardized inspection protocols becomes more pronounced. This introduction sets the foundation for exploring the transformative shifts redefining inspection workflows and the evolving competitive landscape that follows.
Throughout the subsequent sections, readers will encounter a deep-dive into tariff influences, segmentation dynamics, regional growth trends, and actionable strategies that underpin competitive advantage. This foundational overview bridges the technical and commercial realms, equipping leaders with the context necessary for informed decision making in an increasingly complex manufacturing environment.
Emergence of Cutting-Edge Technologies Reshaping Defect Detection
In recent years, defect detection has transitioned from periodic manual sampling to continuous, automated inspection integrated directly into production lines. Manufacturers increasingly rely on inline machine vision systems powered by artificial intelligence algorithms to identify submicron anomalies without halting throughput. Concurrently, advances in laser scanning and 3D profilometry techniques have elevated measurement precision, capturing nanoscale topographical variations that previously went unnoticed. These innovations not only accelerate defect identification but also enable predictive analytics, feeding real-time process adjustments that minimize yield losses and operational disruptions.
Underpinning these developments, eddy current testing has evolved from rudimentary coil designs to phased array configurations that deliver higher sensitivity and deeper penetration, effectively detecting subsurface irregularities in multi-layer foil structures. Meanwhile, high-resolution machine vision cameras equipped with spectral imaging capabilities differentiate between oxidation artifacts and actual surface defects, reducing false positives and inspection cycle times. The convergence of these technologies fosters a multi-modal inspection ecosystem, empowering quality teams to deploy hybrid systems tailored to specific defect typologies and production rates.
As the market continues to embrace digital transformation, stakeholders must evaluate the tradeoffs between capital expenditure and inspection performance. The subsequent section examines how external factors, particularly tariff policies slated for 2025, further complicate investment strategies and supply chain resilience.
Tariff Dynamics and Their Compound Effect on US Operations in 2025
Recent trade policies have introduced incremental tariffs on raw copper and imported foil components, culminating in a notable increase scheduled for 2025. These measures aim to bolster domestic refining but have added cost layers that affect the entire value chain. Producers sourcing copper foil for circuit boards, battery laminates, and packaging must now absorb higher input prices that compress margins and complicate supply agreements.
These tariff escalations have spurred some manufacturers to localize procurement of inspection equipment to avoid import duties, albeit at the expense of longer lead times and a limited supplier base. Quality teams are revising risk frameworks to balance capital outlays against supply security, while exploring alternative materials and forward-looking hedging programs to soften cost volatility.
To navigate this evolving tariff landscape, companies are adopting holistic strategies that integrate procurement optimization, enhanced inspection throughput, and risk mitigation. By investing in high-throughput automated inspection platforms, manufacturers can offset raw material cost increases through lower scrap rates and higher yields. Forward contracts and material hedging have gained traction as complementary financial tools, while partnerships with domestic testing facilities offer supply security. This multi-pronged approach underscores the growing importance of aligning quality assurance decisions with broader financial and operational imperatives.
Simultaneously, the drive toward high-throughput, low-defect inspection systems has intensified, as improved operational efficiency provides a buffer against tariff-induced cost pressures. Selecting equipment that combines rapid cycle times with submicron resolution has become a strategic imperative for manufacturers aiming to sustain competitive pricing and uphold quality standards.
Unveiling Market Segmentation That Drives Strategic Focus
Dissecting the market through multiple segmentation lenses empowers stakeholders to tailor inspection solutions according to unique performance requirements and end-user expectations. This granular understanding facilitates precise product positioning and optimizes resource allocation for maximum market impact.
Regarding technology, the landscape comprises 3D Profilometry, Eddy Current, Laser Scanning, and Machine Vision. 3D Profilometry delivers high-resolution surface topology mapping, Eddy Current testing detects both surface and subsurface anomalies, Laser Scanning balances inspection speed with accuracy, and Machine Vision leverages advanced pattern recognition and spectral analysis to identify complex defect morphologies.
Application segmentation spans Battery, Circuit Board, Foil Packaging, Aerospace, Automotive, and Electronics sectors. Battery divides into Lithium Ion and Nickel Metal Hydride cell laminates with distinct thickness and conductivity inspection demands. Circuit Board inspection differentiates Flexible and Rigid substrates with tailored illumination and image processing. Foil Packaging addresses Food & Beverage and Pharmaceutical compliance needs. In Aerospace, Avionics and Defense components operate under zero-tolerance defect criteria. Automotive inspection includes Body Electronics and Powertrain parts. Electronics covers Consumer Smartphones and Tablets alongside Industrial control system applications.
Additional segmentation examines Deployment Mode - from At Line and Inline to Offline and Real Time configurations - alongside Coating Process variants Electroless and Electrolytic, and Thickness Range categories of Less Than 5 Micron, 5 To 20 Micron, and Greater Than 20 Micron. These multifaceted segmentation insights guide focused R&D investments and targeted go-to-market strategies.
This comprehensive research report categorizes the Copper Foil Surface Defect Detection System market into clearly defined segments, providing a detailed analysis of emerging trends and precise revenue forecasts to support strategic decision-making.
- Technology
- Application
- End Use
- Deployment Mode
- Coating Process
- Thickness Range
Regional Variances Define Adoption and Growth Trajectories
Regional dynamics significantly influence the adoption and evolution of copper foil surface defect detection systems, shaped by local manufacturing capabilities, regulatory environments, and end-use demand. Recognizing these regional nuances is critical for suppliers seeking to align their offerings with the specific requirements and growth drivers of each geography.
In the Americas, robust semiconductor and automotive manufacturing hubs in North America have driven early adoption of advanced inspection platforms. Expansion of the battery industry, propelled by electric vehicles and grid storage initiatives, intensifies demand for high-throughput, high-resolution defect detection systems. Emphasis on domestic supply chain resilience has led suppliers to establish local service networks, ensuring rapid deployment and minimal downtime.
In Europe, Middle East & Africa, stringent quality standards within aerospace, defense, and automotive sectors have cemented demand for zero-defect inspection solutions. Leading EU design centers spearhead digitalization and Industry 4.0 frameworks, fostering interoperability and standardized compliance across inspection protocols. Emerging packaging and pharmaceutical hubs in North Africa and the Gulf offer incremental growth opportunities as regulatory alignment simplifies technology adoption.
Asia-Pacific remains the largest and fastest-growing region, driven by consumer electronics manufacturing scale in East Asia and accelerating automotive electrification in China and South Korea. Japan’s precision manufacturing legacy underpins continued investment in laser scanning and machine vision platforms, while India’s nascent semiconductor capability spurs demand for scalable, cost-effective inspection systems. Southeast Asia’s packaging clusters increasingly leverage inline defect detection to meet global export quality standards. These regional insights highlight the necessity for flexible market entry strategies that accommodate local operational and regulatory demands.
This comprehensive research report examines key regions that drive the evolution of the Copper Foil Surface Defect Detection System market, offering deep insights into regional trends, growth factors, and industry developments that are influencing market performance.
- Americas
- Europe, Middle East & Africa
- Asia-Pacific
Key Players Steering Innovation and Competitive Dynamics
The competitive landscape of copper foil surface defect detection is shaped by a mix of established instrumentation manufacturers and agile technology startups. Legacy equipment suppliers have leveraged decades of material testing expertise to integrate advanced sensing modalities, while newer entrants challenge the status quo with modular, software-driven platforms.
Leading global metrology providers have broadened their portfolios to include combined laser scanning and machine vision systems, coupling hardware precision with AI-powered analytics to reduce defect classification time and false alarms. Several prominent industrial automation firms have forged strategic partnerships with niche inspection specialists, embedding tailored sensor modules into comprehensive production line solutions. Technology pioneers in eddy current and profilometry are investing heavily in edge-computing capabilities to enable real-time feedback loops and support autonomous process adjustments.
To maintain competitive differentiation, many companies are expanding service offerings, from predictive maintenance programs to cloud-based data management portals that unify inspection data across distributed manufacturing sites. Recent mergers and acquisitions have focused on consolidating software analytics capabilities with high-fidelity hardware vendors, reflecting an industry-wide shift toward end-to-end inspection ecosystems. As collaborative R&D efforts gain momentum, cross-industry alliances between equipment manufacturers and semiconductor or automotive OEMs are emerging to develop customized inspection workflows that address unique application needs. Furthermore, regional equipment specialists are tailoring low-cost, compact inspection units to serve small and medium enterprises in emerging markets, demonstrating the increasing importance of flexible, scalable solutions across diverse operational contexts.
This comprehensive research report delivers an in-depth overview of the principal market players in the Copper Foil Surface Defect Detection System market, evaluating their market share, strategic initiatives, and competitive positioning to illuminate the factors shaping the competitive landscape.
- KLA Corporation
- Camtek Ltd.
- Onto Innovation Inc.
- Keyence Corporation
- Cognex Corporation
- Nordson Corporation
- SAKI Corporation
- MIRTEC Co., Ltd.
- Viscom AG
- Tokyo Seimitsu Co., Ltd.
Strategic Imperatives for Industry Front-Runners
Industry leaders must proactively align their technology roadmaps with anticipated quality demands and supply chain shifts. First, scaling deployment of multi-modal inspection systems that combine laser scanning, eddy current, and machine vision ensures comprehensive defect coverage while optimizing capital utilization. Integrating AI-driven analytics within these platforms will enhance defect classification accuracy and support predictive maintenance models, reducing unplanned downtime and scrap rates.
Second, prioritizing partnerships with domestic equipment suppliers and local service providers can mitigate the impact of tariff escalations and bolster supply chain resilience. Establishing joint ventures or co-development agreements with regional manufacturers will shorten lead times and foster customized inspection protocols that cater to specific regulatory requirements.
Third, industry participants should invest in modular, upgradeable hardware architectures that adapt to evolving production line speeds and material compositions. By adopting scalable deployment modes-ranging from At Line and Inline to Offline and Real Time-manufacturers can achieve flexible inspection workflows and scale capacity in response to shifting demand.
Fourth, unifying inspection data through centralized cloud-based platforms will enhance cross-site visibility, enabling benchmarking of defect trends and process performance. Leveraging secure, interoperable data ecosystems supports continuous improvement initiatives and accelerates root-cause analysis.
Finally, aligning R&D efforts with precise market segmentation insights-targeting high-growth segments such as Lithium Ion battery laminates and smartphone foil substrates-will maximize ROI on development expenditures. These coordinated strategies form the bedrock of sustained competitive advantage in a rapidly evolving market environment.
Robust Methodology Underpinning Research Credibility
This research employs a mixed-methods approach combining extensive secondary data analysis with targeted primary research to ensure both breadth and depth of market insights. The secondary phase involved a comprehensive review of industry publications, patent filings, regulatory documents, and technical white papers to map technological trajectories and identify key defect detection modalities. Market intelligence reports and corporate filings provided clarity on competitive dynamics, recent mergers, and product launch activities.
The primary research phase encompassed in-depth interviews with over fifty stakeholders, including quality assurance managers, production engineers, and procurement directors within copper foil and related industries. These conversations illuminated real-world defect identification challenges, equipment procurement decision criteria, and cost-benefit considerations. Supplementary surveys captured quantitative data on inspection system adoption rates, configuration preferences, and service requirement patterns across different regions and end-use segments.
To validate findings, data triangulation techniques cross-referenced insights from expert interviews with secondary data trends, ensuring consistency and accuracy. Statistical analyses quantified correlations between technology adoption and yield improvement metrics, while scenario modeling assessed the potential impact of tariff changes and regional growth differentials. Throughout the process, a rigorous quality assurance framework guided data collection procedures, coding protocols, and analysis workflows, with peer reviews conducted at key milestones.
The methodology acknowledges inherent limitations, such as potential respondent bias and the dynamic nature of trade policies. Nonetheless, the structured integration of multiple data sources and validation steps enhances the robustness of conclusions and the reliability of strategic recommendations put forth.
Explore AI-driven insights for the Copper Foil Surface Defect Detection System market with ResearchAI on our online platform, providing deeper, data-backed market analysis.
Ask ResearchAI anything
World's First Innovative Al for Market Research
Synthesis of Market Dynamics and Forward Outlook
The copper foil surface defect detection system market is at an inflection point, driven by accelerating demands for precision, throughput, and supply chain resilience. Technological innovations spanning 3D Profilometry, Eddy Current, Laser Scanning, and Machine Vision have collectively elevated inspection capabilities, enabling manufacturers to detect and address microscale anomalies before they escalate into costly failures. These multi-modal solutions, underpinned by AI analytics and flexible deployment models, offer a roadmap for quality improvements and operational efficiencies across diverse end-use sectors.
Tariff developments in the United States slated for 2025 add complexity to procurement decisions, necessitating a balanced approach that factors in local sourcing strategies and financial hedging mechanisms. Meanwhile, regional variations in manufacturing maturity and regulatory frameworks underscore the importance of geographically tailored go-to-market strategies, from the advanced industrial ecosystems of North America and Europe to the high-growth corridors of Asia-Pacific.
Competitive pressures have prompted key players to invest in partnerships, service expansions, and integrated hardware-software ecosystems that deliver end-to-end inspection workflows. These dynamics, when viewed through detailed segmentation lenses such as application type, technology modality, and material thickness, reveal targeted opportunities for innovation and strategic differentiation.
As the market continues to evolve, stakeholders who blend technological agility with data-driven decision making will be best positioned to capitalize on emerging growth areas. This synthesis underscores the imperative for cohesive strategies that align R&D investments, operational excellence, and regional expertise to secure long-term market leadership.
This section provides a structured overview of the report, outlining key chapters and topics covered for easy reference in our Copper Foil Surface Defect Detection System market comprehensive research report.
- Preface
- Research Methodology
- Executive Summary
- Market Overview
- Market Dynamics
- Market Insights
- Cumulative Impact of United States Tariffs 2025
- Copper Foil Surface Defect Detection System Market, by Technology
- Copper Foil Surface Defect Detection System Market, by Application
- Copper Foil Surface Defect Detection System Market, by End Use
- Copper Foil Surface Defect Detection System Market, by Deployment Mode
- Copper Foil Surface Defect Detection System Market, by Coating Process
- Copper Foil Surface Defect Detection System Market, by Thickness Range
- Americas Copper Foil Surface Defect Detection System Market
- Europe, Middle East & Africa Copper Foil Surface Defect Detection System Market
- Asia-Pacific Copper Foil Surface Defect Detection System Market
- Competitive Landscape
- ResearchAI
- ResearchStatistics
- ResearchContacts
- ResearchArticles
- Appendix
- List of Figures [Total: 28]
- List of Tables [Total: 590 ]
Engage with Our Expert for Customized Insights
To gain a competitive edge in the rapidly evolving copper foil surface defect detection market, engage directly with Ketan Rohom, Associate Director of Sales & Marketing, for tailored insights and strategic guidance. Ketan’s extensive experience in quality assurance instrumentation and market advisory services ensures you receive actionable intelligence aligned with your specific operational and commercial objectives. Whether you require a deep dive into tariff mitigation strategies, segmentation-driven product roadmaps, or region-specific deployment frameworks, Ketan can help design a bespoke research package that addresses your most pressing challenges. Contact Ketan today to discuss how our comprehensive market research report will empower your organization to optimize inspection workflows, enhance yield performance, and drive sustainable growth.
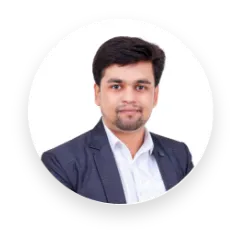
- When do I get the report?
- In what format does this report get delivered to me?
- How long has 360iResearch been around?
- What if I have a question about your reports?
- Can I share this report with my team?
- Can I use your research in my presentation?