Introduction to Copper Polishing Slurry Market Dynamics
Copper polishing slurry stands at the heart of modern surface finishing operations, delivering unparalleled precision in applications ranging from semiconductor fabrication to high-performance metallic components. This specialized abrasive liquid facilitates the removal of minute surface irregularities and oxide layers, ensuring optimal conductivity and durability of copper interconnects, wiring, and plated surfaces. As electronic devices grow ever smaller and more powerful, the demand for slurries that can achieve sub-nanometer flatness and uniformity has surged.
Against a backdrop of rapid technological innovation and heightened performance requirements, manufacturers must navigate a complex matrix of material chemistries, particle size distributions, and process control systems. The evolving nature of end-use industries-from electric vehicles and aerospace components to implantable medical devices-imposes stringent quality standards and scalability challenges. Consequently, suppliers are investing heavily in research to enhance selectivity, reduce defectivity, and minimize environmental impact through green chemistries.
The introduction of advanced control systems, automated mixing solutions, and next-generation abrasive formulations has opened new avenues for cost reduction and process optimization. Yet, achieving a balance between precision, throughput, and sustainability remains a formidable challenge. This executive summary sets the stage for a detailed exploration of market dynamics, emerging catalysts, and strategic imperatives in the copper polishing slurry sector.
Transformative Shifts Redining the Copper Polishing Slurry Landscape
The copper polishing slurry landscape has undergone transformative shifts driven by technological breakthroughs, evolving end-user demands, and regulatory pressures. On the technology front, high-selective slurries engineered for chemical mechanical planarization enable manufacturers to mitigate dishing and erosion while maintaining high removal rates. Advanced pressure control systems and automated slurry mixing platforms have further streamlined process repeatability, fostering tighter tolerances in semiconductor interconnect fabrication.
In parallel, sustainability considerations have accelerated the adoption of eco-friendly formulations. Water-based chemistries and biodegradable surfactants are replacing traditional formulations with high volatile organic compound (VOC) profiles. Manufacturers are also exploring closed-loop recycling and waste-minimization protocols to align with global environmental targets and reduce operating costs.
Moreover, end-user industries are recalibrating their requirements. Electric vehicle manufacturers demand slurries that can uniformly polish copper busbars without compromising thermal management, while aerospace firms seek surface finishes that improve fatigue resistance under extreme operating conditions. As a result, suppliers are forging collaborative partnerships with OEMs to co-develop bespoke solutions. These transformative shifts underscore a dynamic landscape in which innovation, agility, and sustainability converge.
Assessing the Cumulative Impact of United States Tariffs 2025 on Market Flows
The introduction of United States tariffs in 2025 has exerted a cumulative impact on the copper polishing slurry market, reshaping supply chains and pricing structures. Raw material imports, including specialized abrasives and chemical precursors, now face elevated duties, prompting domestic producers to reassess sourcing strategies. Consequently, procurement teams are diversifying vendor portfolios and exploring alternative feedstocks to mitigate cost pressures.
Supply chain recalibrations have also accelerated regional manufacturing integration. North American facilities are expanding capacity for slurry blending and packaging to reduce dependency on cross-border shipments. This reshoring trend not only lowers tariff exposure but also enhances lead-time reliability and inventory control. To support these initiatives, strategic investments in process automation and quality assurance have risen, ensuring consistency despite fluctuating input costs.
Competitively, suppliers that can absorb or offset tariff-driven cost increases through operational efficiencies are gaining market share. At the same time, downstream manufacturers are negotiating longer-term contracts to stabilize pricing and secure supply continuity. In this environment, agility in logistics planning, coupled with forward-looking tariff analysis, has become a cornerstone of commercial success.
Key Segmentation Insights Driving Copper Polishing Slurry Demand
A granular understanding of segmentation reveals differentiated growth trajectories that hinge on material composition, particle dimensions, industrial applications, technology enablers, and product formulations. Market developments in the advanced polishing slurry segment are driven by CMP copper slurry variants optimized for high removal rates and dishing control, whereas high selective slurries cater to applications demanding exceptional planarization uniformity. Conversely, the conventional polishing slurry domain balances cost efficiency with performance, featuring both non-reactive abrasives for general surface preparation and reactive chemistries that enhance oxide removal.
Particle size distribution plays a pivotal role in surface finish outcomes. Micron-sized particles deliver robust material removal for heavier lapping tasks, while nanoparticles facilitate atomic-scale polishing in cutting-edge semiconductor processes. Within end-user industries, aerospace components call for slurries that maintain surface integrity under cyclic stress, and the automotive sector differentiates requirements between conventional vehicles and electric vehicles, where copper interconnect density and thermal management are paramount. Integrated circuit manufacturers rely on CMP variants tailored to microprocessor and IC patterning, and medical device producers select diagnostic tools and implantable devices based on biocompatibility and surface roughness thresholds.
Applications bifurcate into chemical mechanical planarization, primarily focused on copper wiring layers, and surface finish operations that service both metallic surfaces and non-magnetic materials. Underpinning these process segments, technology adoption distinguishes market leaders; advanced pressure control systems provide unparalleled endpoint detection accuracy, whereas automated slurry mixing enhances batch consistency. Finally, product type segmentation illuminates a clear divide between alumina-based slurries favored for their hardness and cost-effectiveness, and colloidal silica-based slurries, including doped variants engineered for improved selectivity and reduced defectivity.
This comprehensive research report categorizes the Copper Polishing Slurry market into clearly defined segments, providing a detailed analysis of emerging trends and precise revenue forecasts to support strategic decision-making.
- Material Type
- Particle Size Distribution
- End User Industry
- Application
- Technology
- Product Type
Regional Market Dynamics and Growth Drivers
Regional market dynamics reflect the interplay of manufacturing infrastructure, end-user concentration, and trade policies. In the Americas, a robust semiconductor fabrication cluster and growing electric vehicle assembly lines are driving local demand for high-precision slurry formulations. Domestic tariff adjustments have spurred investments in regional slurry production facilities to secure reliable supply and maintain cost competitiveness. Downstream industries are also benefiting from proximity to leading chemical suppliers and advanced automation partners.
Europe, Middle East & Africa exhibit a diverse tapestry of demand drivers, with aerospace and automotive OEMs in Western Europe focusing on green chemistry initiatives and lightweight component standards. In the Middle East, emerging electronics and defense sectors present growth opportunities for specialized surface finish applications, while Africa’s rising industrial base is seeking scalable, low-cost polishing solutions. Regulatory alignment with REACH and other eco-design frameworks is accelerating the adoption of low-VOC and biodegradable slurries across these markets.
Asia-Pacific remains a powerhouse for slurry consumption, powered by large-scale semiconductor wafer fabs, electronics manufacturing hubs, and expanding medical device clusters. Nations with strategic investments in advanced manufacturing are prioritizing onshore slurry R&D and pilot facilities. Moreover, supply chain integration across Southeast Asia facilitates efficient raw material sourcing and end-user distribution, reinforcing the region’s role as a global manufacturing nexus.
This comprehensive research report examines key regions that drive the evolution of the Copper Polishing Slurry market, offering deep insights into regional trends, growth factors, and industry developments that are influencing market performance.
- Americas
- Asia-Pacific
- Europe, Middle East & Africa
Competitive Landscape and Leading Industry Players
The competitive landscape for copper polishing slurry is anchored by a mix of global conglomerates and niche specialty chemical firms. Industry frontrunners such as BASF SE and Dow Inc. leverage extensive R&D portfolios to advance slurry chemistries with enhanced selectivity and environmental profiles. Cabot Microelectronics Corporation focuses on high-performance CMP slurries, while DuPont de Nemours distinguishes its offerings through custom formulation services and integrated process support.
Ferro Corporation and Fujimi Corporation invest in collaborative partnerships with semiconductor fabs to co-develop next-generation abrasive systems. Hitachi Chemical Co., Ltd. and Merck KGaA drive innovation through doped colloidal silica and nanotechnology-enabled abrasives. Lone Star Technologies, Inc. and Saint-Gobain Ceramics & Plastics, Inc. capitalize on scalable manufacturing platforms to serve diversified end-use industries, from automotive to medical devices. The Dow Chemical Company, operating as a subsidiary of Dow Inc., integrates advanced pressure control systems into its slurry products, while Versum Materials, Inc. focuses on precision particle engineering for cutting-edge semiconductor applications.
This comprehensive research report delivers an in-depth overview of the principal market players in the Copper Polishing Slurry market, evaluating their market share, strategic initiatives, and competitive positioning to illuminate the factors shaping the competitive landscape.
- BASF SE
- Cabot Microelectronics Corporation (CMC Materials)
- Dow Inc.
- DuPont de Nemours, Inc.
- Ferro Corporation
- Fujimi Corporation
- Hitachi Chemical Co., Ltd.
- Lone Star Technologies, Inc.
- Merck KGaA
- Saint-Gobain Ceramics & Plastics, Inc.
- The Dow Chemical Company (Subsidiary of Dow Inc.)
- Versum Materials, Inc.
Actionable Recommendations for Industry Leadership
To maintain a competitive edge, industry leaders should prioritize strategic initiatives across R&D, operations, and commercial engagement. First, allocating resources to the co-development of high-selective, eco-friendly formulations with key end users will foster long-term partnerships and accelerate time-to-market. Concurrently, expanding automated slurry mixing and pressure control capabilities in regional manufacturing centers can reduce batch variability, lower production costs, and enhance supply chain resilience.
Furthermore, companies must diversify raw material sourcing by qualifying alternative abrasive and chemical feedstocks. Engaging with multiple suppliers across geographies will mitigate tariff exposure and ensure continuity in the event of geopolitical disruptions. To that end, integrating predictive analytics into procurement processes will enable more accurate risk assessments and dynamic contract negotiations.
On the commercial front, tailoring value propositions to distinct end-use segments-highlighting biocompatibility for medical devices, thermal performance for electric vehicles, and ultra-low defectivity for semiconductor fabs-will sharpen competitive differentiation. Establishing joint innovation labs or application centers in strategic regions can deepen customer relationships and provide rapid prototyping capabilities.
Finally, embedding sustainability metrics into product roadmaps and achieving relevant eco-certifications will resonate with increasingly environmentally conscious stakeholders. By aligning technical innovation with green initiatives, industry leaders can unlock premium pricing opportunities and bolster brand reputation.
Explore AI-driven insights for the Copper Polishing Slurry market with ResearchAI on our online platform, providing deeper, data-backed market analysis.
Ask ResearchAI anything
World's First Innovative Al for Market Research
Conclusion and Strategic Imperatives
The copper polishing slurry market continues to evolve under the dual imperatives of precision and sustainability. Technological advancements in selective chemistries, pressure control, and automation are redefining performance benchmarks, while regulatory and tariff landscapes demand agile supply chain strategies. Segmentation analysis highlights the nuanced requirements of diverse end-use industries and process applications, underscoring the importance of targeted product development and regional manufacturing footprints.
Competition among leading chemical suppliers and specialty firms drives continuous innovation, yet success will hinge on the ability to integrate operational excellence with customer-centric collaboration. By embracing eco-friendly formulations and digital process control, companies can not only meet rising performance standards but also support broader environmental goals. The strategic insights, regional trends, and competitive dynamics outlined in this executive summary provide a roadmap for stakeholders seeking to capitalize on emerging opportunities while mitigating risks.
This section provides a structured overview of the report, outlining key chapters and topics covered for easy reference in our Copper Polishing Slurry market comprehensive research report.
- Preface
- Research Methodology
- Executive Summary
- Market Overview
- Market Dynamics
- Market Insights
- Cumulative Impact of United States Tariffs 2025
- Copper Polishing Slurry Market, by Material Type
- Copper Polishing Slurry Market, by Particle Size Distribution
- Copper Polishing Slurry Market, by End User Industry
- Copper Polishing Slurry Market, by Application
- Copper Polishing Slurry Market, by Technology
- Copper Polishing Slurry Market, by Product Type
- Americas Copper Polishing Slurry Market
- Asia-Pacific Copper Polishing Slurry Market
- Europe, Middle East & Africa Copper Polishing Slurry Market
- Competitive Landscape
- ResearchAI
- ResearchStatistics
- ResearchContacts
- ResearchArticles
- Appendix
- List of Figures [Total: 28]
- List of Tables [Total: 627 ]
Next Steps: Secure In-Depth Market Intelligence
To secure comprehensive insights and tactical guidance on navigating the copper polishing slurry landscape, reach out to Ketan Rohom, Associate Director, Sales & Marketing. Ketan can provide access to the full market research report, which delivers in-depth analysis, detailed segmentation data, and actionable foresight critical for strategic decision-making.
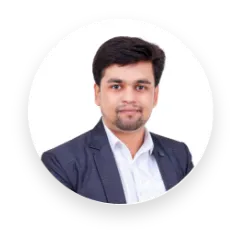
- When do I get the report?
- In what format does this report get delivered to me?
- How long has 360iResearch been around?
- What if I have a question about your reports?
- Can I share this report with my team?
- Can I use your research in my presentation?