Introduction: Unveiling the Core Making Machines Landscape
The core making machines sector stands at the forefront of innovation in metal casting, delivering precision and efficiency across diverse industries. As demand for high-performance engine components, exhaust systems, and transmission parts intensifies, manufacturers increasingly rely on continuous, horizontal, and vertical core making equipment to maintain competitiveness. Continuous core making machines have adapted to varying production demands by offering high-capacity, medium-capacity, and low-capacity solutions, while horizontal systems evolve along advanced and basic lines to balance complexity with cost. Vertical designs, spanning high-performance and standard models, continue to fulfill specialized requirements for both ferrous and non-ferrous foundry operations.
In parallel, end-use industries such as aerospace-both commercial and defense-automotive in original equipment manufacturing and aftermarket segments, and construction across commercial, infrastructure, and residential projects are driving tailored machine configurations. Meanwhile, electrical and electronics applications in consumer products and foundry operations leverage inorganic resin-bonded and silica cores as well as organic carbon and graphite materials. These dynamics set the stage for a transformative period characterized by technological advancements, evolving regulatory landscapes, and shifting supply chains.
Transformative Shifts Reshaping the Core Making Industry
Rapid digitalization and Industry 4.0 integration mark pivotal shifts reshaping the core making industry. Automation-enabled gas hardened and oil hardened core making technologies, including cold box, hot box, lustrous coated, and major bonded processes, have gained traction, driving consistent quality and throughput. Meanwhile, additive techniques and smart sensors facilitate real-time monitoring, enabling predictive maintenance and minimizing downtime.
Sustainability has emerged as another catalyst for change, with manufacturers prioritizing inorganic resin-bonded and silica cores and exploring organic carbon and graphite materials that reduce environmental impact. Advanced materials research also extends to binder formulations, yielding lower emissions and safer working conditions. Moreover, the convergence of artificial intelligence and machine learning is empowering adaptive process controls that dynamically optimize cycle times and resource utilization.
Supply chain resilience continues to influence strategic decision making; firms are diversifying production capacity between mass production lines and custom solutions to address volatility. Throughout this transition, collaboration between equipment suppliers, end-use industries, and technology partners is fostering a new ecosystem of innovation, delivering both performance gains and sustainable outcomes.
Cumulative Impact of United States Tariffs in 2025 on Industry Dynamics
The introduction of targeted tariffs by the United States in 2025 has prompted manufacturers to reassess sourcing and pricing strategies across the core making sector. Increased duties on imported machinery and components have elevated input costs, compelling many suppliers to evaluate nearshoring opportunities and strengthen domestic partnerships. As a result, some high-capacity continuous core making equipment has migrated closer to key automotive and aerospace hubs, where OEMs and defense contractors seek localized support.
Tariff-related price pressures have accelerated investment in advanced horizontal and vertical systems, particularly those offering automated cold box and hot box processes that reduce labor dependency. Firms with established U.S. production footprints have leveraged existing infrastructures to buffer against cost fluctuations, while smaller producers have pursued strategic alliances to maintain supply continuity.
In response, end-use industries are recalibrating budgets, prioritizing core making solutions that offer modular expansion and scalable capacity. This recalibration has spurred demand for medium-capacity machines capable of flexing between foundational production runs and specialized projects. The cumulative impact underscores a strategic pivot toward agility and local resilience, rather than reliance on long-haul imports.
Key Segmentation Insights Driving Market Innovation and Growth
A granular view of market segmentation reveals crucial insights into growth drivers. Continuous core making machines, available in high, medium, and low capacities, are catering to mass production and custom solutions alike. Horizontal core making equipment, offered in advanced and basic configurations, is meeting demand for varying degrees of process automation and complexity. Vertical core making machines, divided between high-performance and standard offerings, continue to satisfy niche requirements for precision casting.
End-use industry segmentation emphasizes aerospace applications-spanning commercial and defense-as key adopters of sophisticated core making solutions. The automotive sector, including OEMs and aftermarket specialists, is driving upgrades to cold box and hot box gas hardened technologies. Construction projects in commercial, infrastructure, and residential domains increasingly rely on core systems that accommodate both inorganic resin-bonded and silica cores and organic carbon and graphite materials. In the electrical and electronics arena, consumer electronics foundries demand process consistency, while ferrous and non-ferrous foundries refine material selection to optimize yield.
Application segments such as engine components, exhaust manifolds, and transmission parts illustrate the importance of dedicated configurations for cylinder heads, manifolds, clutch plates, and gearbox castings. Production capacity stratification between large scale mass production and small scale custom solutions further highlights divergent investment priorities across the value chain.
This comprehensive research report categorizes the Core Making Machines market into clearly defined segments, providing a detailed analysis of emerging trends and precise revenue forecasts to support strategic decision-making.
- Machine Type
- End-Use Industry
- Core Material Type
- Technology
- Application
- Production Capacity
Key Regional Insights Highlighting Geographic Opportunities
Regional dynamics significantly influence competitive positioning and investment strategies. In the Americas, a robust automotive manufacturing base and expanding aerospace sector have spurred adoption of both continuous and horizontal core making machines. Producers in North America are prioritizing domestic capacity expansions to mitigate tariff impacts and ensure timely delivery to OEMs and defense suppliers.
Europe, Middle East & Africa feature a diverse landscape where regulatory frameworks and environmental standards shape equipment preferences. Major foundries in Western Europe are investing heavily in advanced oil hardened systems with lustrous coated and major bonded processes to comply with stringent emission norms, while emerging markets in the Middle East leverage low-capacity solutions to support infrastructure growth.
Asia-Pacific remains a hotbed of growth, fueled by rapid industrialization and escalating demand in consumer electronics, automotive, and construction sectors. Manufacturers across China, India, and Southeast Asia are scaling up both large scale production lines and custom solutions, driving innovations in gas hardened cold box and hot box technologies as they seek to balance cost efficiency with quality consistency.
This comprehensive research report examines key regions that drive the evolution of the Core Making Machines market, offering deep insights into regional trends, growth factors, and industry developments that are influencing market performance.
- Americas
- Asia-Pacific
- Europe, Middle East & Africa
Key Companies Insights Showcasing Competitive Landscape
Market leaders continue to refine their portfolios and global footprints through strategic investments and partnerships. Beatson Clark Ltd has concentrated on specialized glass core applications, while Centracore Inc. emphasizes modular continuous machines that suit both high and low capacity needs. DISA Industries, Inc. maintains a strong presence in horizontal advanced systems, complemented by Harrison Castings Ltd’s focus on bespoke vertical high-performance solutions.
Inductotherm Group and Italpresse Gauss have advanced oil hardened core making technologies, with the former expanding global service networks and the latter integrating digital control platforms. Küttner GmbH & Co. KG has bolstered its modular offerings in both gas hardened and oil hardened segments, while Laempe Mössner Sinto GmbH continues to pioneer automation in cold box and hot box processes.
Loramendi S. Coop and Omega Sinto Foundry Machinery Ltd. leverage cross-regional alliances to streamline spare parts distribution, and Palmer Manufacturing & Supply, Inc. has built a strong aftermarket services division. Savitri Technical Services Pvt. Ltd. focuses on custom solutions in the Asia-Pacific region, while Sinto America, Inc. and Thunderbolt Systems, Inc. reinforce their positions through regional manufacturing hubs and joint ventures.
This comprehensive research report delivers an in-depth overview of the principal market players in the Core Making Machines market, evaluating their market share, strategic initiatives, and competitive positioning to illuminate the factors shaping the competitive landscape.
- Beatson Clark Ltd
- Centracore Inc.
- DISA Industries, Inc.
- Harrison Castings Ltd.
- Inductotherm Group
- Italpresse Gauss
- Küttner GmbH & Co. KG
- Laempe Mössner Sinto GmbH
- Loramendi S. Coop
- Omega Sinto Foundry Machinery Ltd.
- Palmer Manufacturing & Supply, Inc.
- Savitri Technical Services Pvt. Ltd.
- Sinto America, Inc.
- Thunderbolt Systems, Inc.
Actionable Recommendations for Industry Leaders to Capitalize on Emerging Trends
Industry leaders must act decisively to secure long-term advantage. First, investing in advanced sensor integration and predictive analytics will enhance machine uptime and process reliability, driving cost savings and quality improvements. Second, diversifying production capacity between mass production and bespoke custom solutions ensures agility in responding to varied end-use requirements, especially within automotive OEM and aerospace defense segments.
Third, strengthening regional footprints-particularly within the Americas and Asia-Pacific-will mitigate tariff and trade uncertainties, while targeted joint ventures in Europe, Middle East & Africa can unlock new infrastructure and construction projects. Fourth, prioritizing sustainable core materials and binder systems, including resin-bonded silica and low-emission organic formulations, will address tightening environmental regulations and appeal to eco-conscious customers.
Fifth, cultivating strategic partnerships with technology providers and academic institutions can accelerate the adoption of AI-driven process controls, cold box and hot box automation, and digital twin simulations. Finally, establishing robust aftermarket service networks and spare parts distribution channels will enhance customer loyalty and generate recurring revenue, making the overall business model more resilient.
Explore AI-driven insights for the Core Making Machines market with ResearchAI on our online platform, providing deeper, data-backed market analysis.
Ask ResearchAI anything
World's First Innovative Al for Market Research
Conclusion: Charting the Future of Core Making Machines
The core making machines market is entering a decisive era defined by technological innovation, regulatory complexity, and shifting trade policies. Manufacturers that embrace automation, leverage data-driven insights, and diversify their regional operations will be best positioned to thrive amidst evolving end-use demands. By aligning product portfolios with high-growth segments-such as defense aerospace, automotive OEM, and electrical foundries-and investing in sustainable materials, companies can unlock new value and foster long-term partnerships.
Ultimately, success hinges on proactive adaptation: integrating advanced gas hardened and oil hardened processes, expanding both mass production and custom solution capabilities, and forging alliances that bolster supply chain resilience. Through these strategic moves, industry leaders can chart a profitable course, delivering precision, performance, and sustainability across the global casting landscape.
This section provides a structured overview of the report, outlining key chapters and topics covered for easy reference in our Core Making Machines market comprehensive research report.
- Preface
- Research Methodology
- Executive Summary
- Market Overview
- Market Dynamics
- Market Insights
- Cumulative Impact of United States Tariffs 2025
- Core Making Machines Market, by Machine Type
- Core Making Machines Market, by End-Use Industry
- Core Making Machines Market, by Core Material Type
- Core Making Machines Market, by Technology
- Core Making Machines Market, by Application
- Core Making Machines Market, by Production Capacity
- Americas Core Making Machines Market
- Asia-Pacific Core Making Machines Market
- Europe, Middle East & Africa Core Making Machines Market
- Competitive Landscape
- ResearchAI
- ResearchStatistics
- ResearchContacts
- ResearchArticles
- Appendix
- List of Figures [Total: 28]
- List of Tables [Total: 1026 ]
Contact Ketan Rohom to Secure Your Comprehensive Market Insight
To gain comprehensive insight and actionable intelligence on the core making machines market, reach out to Ketan Rohom, Associate Director of Sales & Marketing. Engage today to secure in-depth analysis, competitive benchmarking, and strategic recommendations tailored to your business needs. Take the next step toward transforming your market strategy and driving sustainable growth.
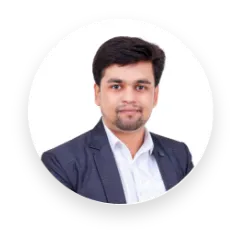
- When do I get the report?
- In what format does this report get delivered to me?
- How long has 360iResearch been around?
- What if I have a question about your reports?
- Can I share this report with my team?
- Can I use your research in my presentation?