Pioneering durability through advanced nickel alloys
Nickel alloys designed to resist corrosion have become indispensable in industries demanding durability under extreme conditions. These materials combine nickel’s inherent resistance to oxidation with strategic alloying elements that fortify performance against acidic, saline, and high-temperature environments. Recent advancements in metallurgical processes and precision manufacturing have enhanced consistency and predictability in alloy behavior, fostering stronger adoption across critical sectors.
As global infrastructure projects, energy transitions, and stringent regulatory frameworks drive demand for robust materials, corrosion resistant nickel alloys stand at the forefront of engineering solutions. Their versatility extends from subsea pipelines to power generation turbines, affirming their role in safeguarding assets, maximizing uptime, and lowering life-cycle costs. The interplay between material science innovation and shifting end-use requirements has set the stage for a dynamic market environment.
This executive summary delivers a comprehensive overview of the forces shaping this sector, highlighting transformative trends, the implications of new trade policies, segmentation drivers, regional variations, leading corporate strategies, and recommendations for industry leadership. It offers a structured foundation for decision-makers seeking to optimize supply chains, refine product portfolios, and steer investments in a market defined by resilience and high performance.
Redefining corrosion protection with innovation and sustainability
Over the past decade, the corrosion resistant nickel alloy market has undergone seismic shifts, driven by evolving regulatory standards, emergent end-use requirements, and materials innovation. Environmental compliance mandates have compelled manufacturers to reformulate alloys that minimize toxic byproducts, while digitalization and additive manufacturing have enabled complex geometries and rapid prototyping. These technological leaps have ushered in a new era of customization, allowing designers to specify alloys by precise performance criteria rather than rely on broad classifications.
Simultaneously, sustainability imperatives have elevated the importance of lifecycle assessments. Stakeholders now evaluate alloys not only for initial corrosion resistance but also for recyclability and environmental footprint. This holistic perspective is fostering partnerships across supply chains, from raw material suppliers to fabricators and end users, to ensure traceability and minimize waste. As a consequence, strategic alliances and collaborative research initiatives are on the rise, reshaping competitive dynamics and accelerating product evolution.
Looking ahead, the convergence of digital twinning, predictive analytics, and advanced coatings will redefine expectations for corrosion protection. Industry players integrating these capabilities early will set new benchmarks for performance and reliability, reinforcing the market’s trajectory toward smarter, more sustainable solutions.
Navigating the new tariff-driven supply chain paradigm
The enactment of the United States tariffs in early 2025 marks a pivotal moment for the corrosion resistant nickel alloy sector. By imposing additional duties on key alloy imports, the policy has pressured domestic supply chains to recalibrate sourcing strategies and renegotiate contracts. Fabricators have responded by intensifying relationships with local mills and exploring nearshore options to mitigate cost escalations triggered by the new levies.
These tariff measures have had a cascading effect. Projects heavily reliant on imported alloys faced initial delays as procurement teams sought tariff-exempt alternative grades and adjusted engineering specifications. In parallel, alloy producers within the United States ramped up capacity expansion efforts to capture growing domestic demand. However, lead times and capital constraints have moderated the speed of this shift, leaving certain segments of the market-particularly those demanding superalloys and specialized forms-vulnerable to intermittent supply fluctuations.
In response, stakeholders are diversifying their risk profiles by pursuing dual-sourcing strategies and establishing framework agreements that can dynamically allocate volumes based on duty structures. This period of adjustment underscores the critical importance of agile supply chain management and robust scenario planning for organizations aiming to sustain uninterrupted production while containing input cost inflation.
Unpacking the nuanced drivers across alloy segments
A nuanced understanding of market segmentation reveals how distinct alloy characteristics and application requirements are shaping demand patterns. Strength grade segmentation indicates that high strength variants are increasingly favored for demanding structural applications, while standard grades retain steady adoption in conventional engineering components and superalloys secure niche positions in extreme temperature environments. Thickness variations likewise influence procurement, with thicker plates and sheets commanding attention in heavy-duty infrastructure projects and thinner gauges utilized in precision components.
Product form intricacies further underscore market complexity. Bar and rod alloys produced via cold drawing find prominence in fastener manufacturing, whereas hot rolled alternatives cater to applications requiring enhanced ductility. Seamless pipe and tube configurations meet the stringent specifications of high-pressure systems, complementing welded variants deployed in lower-stress installations. Plate and sheet assortments, available in both cold rolled and hot rolled formats, address diverse fabrication needs, while powder and castings, achieved through conventional casting or advanced powder metallurgy, enable intricate geometries. Wire products, whether annealed for flexibility or cold drawn for strength, support specialized winding and fastening functions.
End-use industries exhibit differentiated demand profiles: aerospace and defense applications prioritize superalloys and precision forms for critical components; chemical and petrochemical sectors emphasize corrosion resistance under aggressive process streams; marine and offshore projects seek alloys with proven performance in saline environments; oil and gas operations require robust grades for subsea and downhole applications; and power generation relies on a balanced mix of standard and high strength variants for turbines and auxiliaries. Across these industries, core applications such as fasteners, heat exchanger components, and valves and fittings drive volume consumption, each demanding tailored alloy specifications to meet functional and regulatory requirements.
This comprehensive research report categorizes the Corrosion Resistant Nickel Alloy market into clearly defined segments, providing a detailed analysis of emerging trends and precise revenue forecasts to support strategic decision-making.
- Strength Grade
- Thickness
- Product Form
- End Use Industry
- Application
Regional growth fueled by infrastructure and sustainability
Regional dynamics play a decisive role in shaping market trajectories. In the Americas, infrastructure investments and energy sector modernization are fueling demand for corrosion resistant alloys, supported by local production capabilities that have expanded in response to protective trade measures. Capital projects in power and petrochemicals underscore the need for high strength plates and seamless tubes that can endure harsh process conditions.
Moving to Europe, the Middle East and Africa, sustainability mandates and offshore developments are primary growth drivers. Stringent environmental directives in Europe encourage the adoption of alloy grades with low lifecycle emissions, while Middle Eastern desalination and petrochemical projects demand robust materials engineered for extensive saltwater exposure. In African markets, nascent mining and infrastructure initiatives are creating nascent opportunities for standard grades and cost-effective forms.
In Asia-Pacific, industrialization and renewable energy expansion underpin alloy consumption. Rapid growth in wind and solar installations drives heat exchanger component demand, while marine transport and shipbuilding in the region leverage high performance grades. Local mills have scaled up production of powder metallurgy alloys to meet additive manufacturing requirements, positioning the region as a hub for advanced manufacturing of corrosion resistant components.
This comprehensive research report examines key regions that drive the evolution of the Corrosion Resistant Nickel Alloy market, offering deep insights into regional trends, growth factors, and industry developments that are influencing market performance.
- Americas
- Europe, Middle East & Africa
- Asia-Pacific
Corporate strategies driving competitive differentiation
Leading corporations in the corrosion resistant nickel alloy landscape are deploying diversified strategies to consolidate market share. Industry stalwarts are enhancing research and development efforts to formulate new alloy chemistries that deliver performance gains at reduced cost. Concurrently, they are investing in digital process controls and real-time quality verification to improve yield and ensure consistent mechanical properties.
Mid-tier players differentiate through agile manufacturing models, offering rapid turnaround times and tailored service for specialized orders. These firms often cultivate close partnerships with downstream fabricators to co-develop bespoke products, leveraging flexible capacity and deep metallurgical expertise. Some are exploring joint ventures and strategic alliances to access new geographies and feedstock sources, thereby mitigating supply risks and expanding their service portfolios.
Across the competitive spectrum, vertical integration is emerging as a key theme, with both upstream suppliers and downstream fabricators seeking to capture additional value by controlling critical stages of production. This trend promises tighter coordination, improved cost structures, and enhanced innovation throughput for those who execute it effectively.
This comprehensive research report delivers an in-depth overview of the principal market players in the Corrosion Resistant Nickel Alloy market, evaluating their market share, strategic initiatives, and competitive positioning to illuminate the factors shaping the competitive landscape.
- Special Metals Corporation
- Allegheny Technologies Incorporated
- Carpenter Technology Corporation
- Haynes International, Inc.
- VDM Metals GmbH
- Sandvik Materials Technology AB
- Outokumpu Oyj
- Jinchuan Group International Resources Co., Ltd.
- Eramet S.A.
- Sumitomo Metal Mining Co., Ltd.
Enhancing resilience through innovation and collaboration
To maintain leadership in a dynamic market, companies should prioritize investments in advanced characterization and testing protocols that accelerate alloy qualification cycles. Embedding digital twins within manufacturing operations will enable proactive maintenance, yield optimization, and faster adaptation to specification changes. Strengthening collaborative research partnerships with academic institutions and end-use customers can foster co-innovation and secure early access to emerging performance requirements.
Supply chain resilience must be bolstered through diversified sourcing, dual-site manufacturing hubs, and strategic inventory buffers of critical alloy forms. Firms should negotiate flexible contractual frameworks that account for evolving tariff landscapes and currency fluctuations. Additionally, integrating sustainability metrics into product development and disclosure will align offerings with increasingly stringent ESG criteria, unlocking opportunities in public-sector and environmentally focused projects.
Finally, cultivating talent with interdisciplinary expertise-combining materials science, data analytics, and regulatory knowledge-will be essential. Cross-functional teams can better anticipate market disruptions, accelerate product launches, and deliver high-impact solutions that meet both technical demands and business objectives.
Applying a rigorous hybrid research framework
This analysis relies on a blended methodology encompassing primary and secondary research. Primary inputs derive from structured interviews with material suppliers, fabricators, end users, and industry experts, ensuring direct insights into procurement strategies, performance challenges, and emerging requirements. Secondary data sources include trade publications, regulatory filings, technical standards documentation, and publicly available company disclosures to validate market behaviors and historical trends.
Quantitative data extraction follows a rigorous process of cross-referencing trade flow statistics, customs records, and financial reports to map supply-demand dynamics and tariff impacts. Qualitative assessments incorporate scenario planning workshops with sector specialists to explore potential market disruptions, policy shifts, and technology inflections. A multi-tiered validation procedure ensures consistency and accuracy, with discrepancies reconciled through additional expert consultations.
This structured approach provides a robust foundation for actionable insights while maintaining transparency and reproducibility. It balances empirical data with expert judgment to chart a clear perspective on market drivers, segmentation nuances, regional variations, and strategic imperatives.
Explore AI-driven insights for the Corrosion Resistant Nickel Alloy market with ResearchAI on our online platform, providing deeper, data-backed market analysis.
Ask ResearchAI anything
World's First Innovative Al for Market Research
Synthesizing market dynamics for strategic clarity
The corrosion resistant nickel alloy market stands at a crossroads defined by regulatory shifts, technological breakthroughs, and evolving end-use demands. Innovative alloy formulations and manufacturing techniques are elevating performance benchmarks, while sustainability and supply chain resilience have become critical success factors. Trade policies, particularly the 2025 tariff regime, have introduced fresh complexities, prompting stakeholders to recalibrate sourcing strategies and pursue strategic partnerships.
Segmentation analysis highlights the granular drivers of demand across strength grades, thickness categories, product forms, end-use industries, and applications, underscoring the importance of targeted portfolio optimization. Regional insights reveal differentiated growth trajectories in the Americas, Europe, the Middle East and Africa, and Asia-Pacific, each influenced by infrastructure investments, environmental mandates, and industrialization trends.
As competition intensifies, leading companies are leveraging innovation, digitalization, and vertical integration to differentiate their offerings. The path forward requires a balanced focus on agile supply chains, advanced R&D, and sustainability alignment. These imperatives will enable organizations to navigate uncertainties, capitalize on emergent opportunities, and secure long-term value in this essential materials sector.
This section provides a structured overview of the report, outlining key chapters and topics covered for easy reference in our Corrosion Resistant Nickel Alloy market comprehensive research report.
- Preface
- Research Methodology
- Executive Summary
- Market Overview
- Market Dynamics
- Market Insights
- Cumulative Impact of United States Tariffs 2025
- Corrosion Resistant Nickel Alloy Market, by Strength Grade
- Corrosion Resistant Nickel Alloy Market, by Thickness
- Corrosion Resistant Nickel Alloy Market, by Product Form
- Corrosion Resistant Nickel Alloy Market, by End Use Industry
- Corrosion Resistant Nickel Alloy Market, by Application
- Americas Corrosion Resistant Nickel Alloy Market
- Europe, Middle East & Africa Corrosion Resistant Nickel Alloy Market
- Asia-Pacific Corrosion Resistant Nickel Alloy Market
- Competitive Landscape
- ResearchAI
- ResearchStatistics
- ResearchContacts
- ResearchArticles
- Appendix
- List of Figures [Total: 26]
- List of Tables [Total: 460 ]
Engage with Ketan Rohom to unlock tailored insights
To secure a competitive edge in the corrosion resistant nickel alloy market, connect directly with Ketan Rohom, Associate Director, Sales & Marketing at 360iResearch. He will guide you through tailored research options that align with your strategic objectives and deliver the granular intelligence you need to accelerate growth.
By engaging with Ketan, you gain access to comprehensive analytical frameworks, expert interpretation of market dynamics, and bespoke advisory services. Whether you seek in-depth evaluations of tariff impacts, segmentation deep dives, or region-specific tactics, this partnership will equip your organization with validated insights and actionable intelligence.
Reach out now to transform these findings into high-impact strategies, sharpen your competitive positioning, and drive informed decisions. Harness the power of specialized market research to navigate evolving challenges and capitalize on emerging opportunities in corrosion resistant nickel alloys.
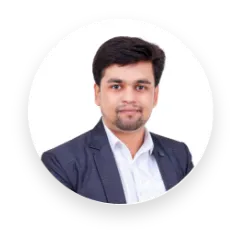
- When do I get the report?
- In what format does this report get delivered to me?
- How long has 360iResearch been around?
- What if I have a question about your reports?
- Can I share this report with my team?
- Can I use your research in my presentation?